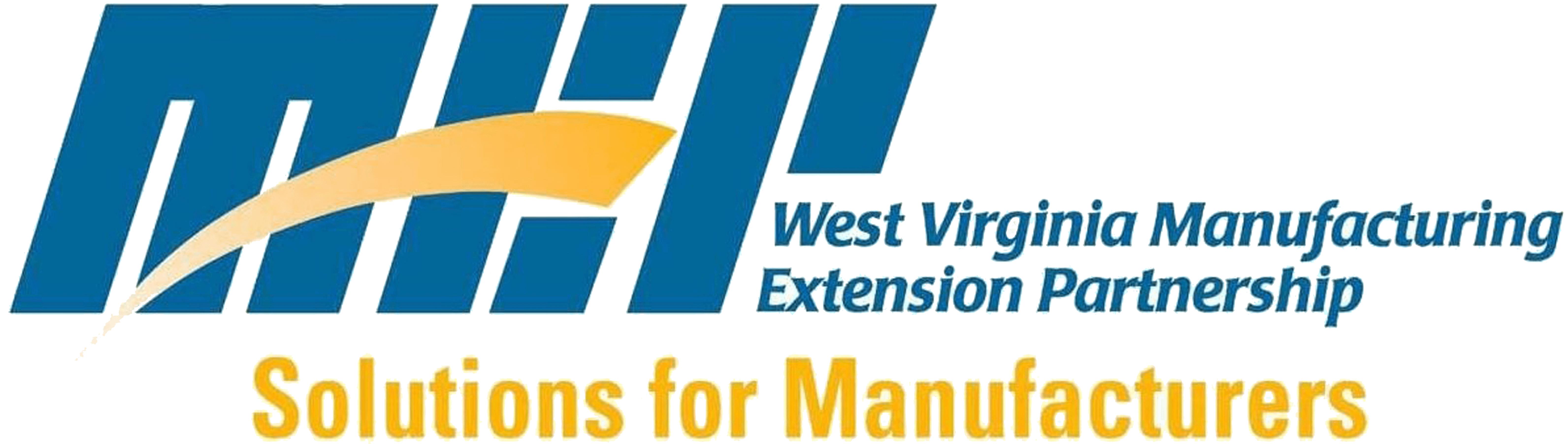
The field of manufacturing engineering is often referred to as production engineering. This type shares many ideas and concepts with other engineering areas. An engineer who is skilled in this field of engineering may find their niche and contribute to a company's success. These engineers are capable of ensuring that a product meets high quality standards.
Your job duties
Production engineers coordinate and analyze the production process from design to completion. This position requires attention to detail, and commitment to safety in the workplace. Production engineers work to ensure high quality standards in the workplace and safety. They evaluate production processes to determine how they can be improved.
A production engineer is a person who helps companies produce products quickly and efficiently. Their job may require them to investigate and analyze current production processes, or they may focus on one area of the production process. They may also assist in the maintenance of plant software and train workers.
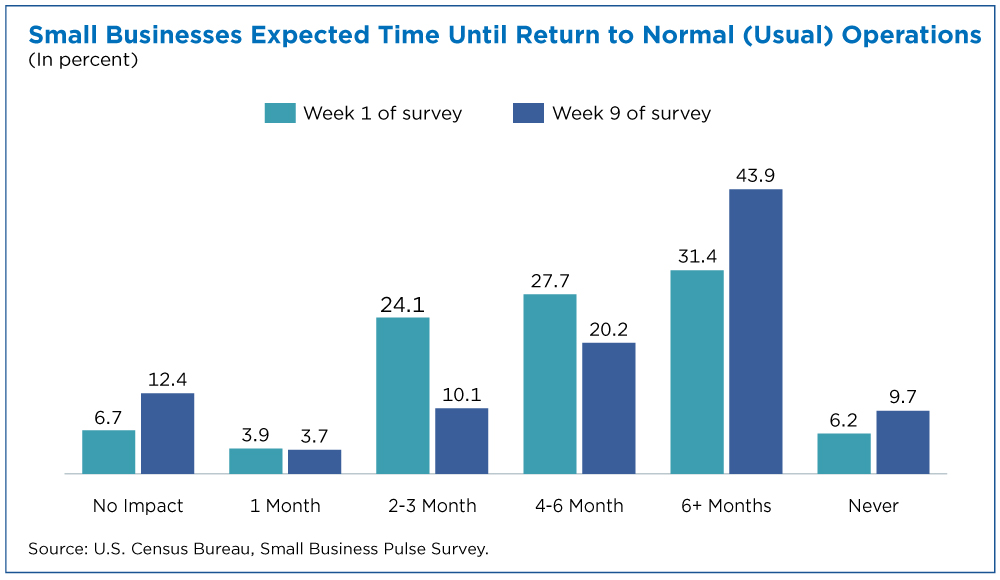
Excellent communication skills are essential for this job. Engineers need to be able communicate complex engineering concepts in a simple and understandable way. Because engineering involves complex math and calculations, this is essential. Production engineers may use equations in order to predict the final product's cost or to solve problems within their manufacturing lines.
Education required
To be a successful production engineer, you must first earn a bachelor's in manufacturing or industrial engineering. In order to be considered for research-oriented jobs in manufacturing, employers might prefer a master's level. A master's degree is also beneficial if you are proficient in one or more specialized fields.
Industrial engineers use their creativity and analytical skills to improve the efficiency of production processes. They strive to eliminate waste and create new ways to use equipment, materials, or employees more efficiently. Because they must communicate complex processes to non-technical audience, they should also possess excellent communication skills. Being able listen to and understand others' opinions and points of view is a key component of good communication skills.
During the degree program, manufacturing engineers receive hands-on training. They will also be taught safety regulations and procedures. In addition, they will be required to obtain a Professional Engineer license, issued by the National Society of Professional Engineers. This license proves to employers and clients you have the right credentials. It's important to renew your licence according to state requirements.
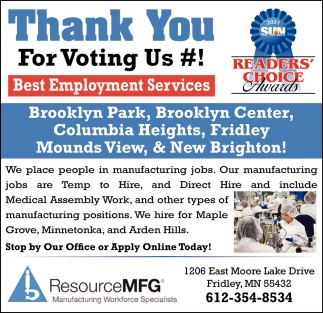
Salary
The salary of production engineers varies depending on their location and company. Production engineers usually work in an office environment. However they may occasionally travel to production sites to inspect machinery, improve processes and perform other tasks. Some production engineers are self-employed, while others work for larger companies. Production engineers are expected not only to earn a good salary but also to finish their work promptly.
Production engineers work in collaboration with other professionals to ensure the safety and quality of the final product. To ensure the highest quality production, they work closely together with designers. They are responsible for maintaining safety standards at the factory floor, as well as training workers on safety procedures. While this job description doesn't cover all the duties and responsibilities that a production engineering has, it does give an idea of what they are responsible for.
Production engineers' salaries depend on their level of experience. The salary for entry-level production engineers is around Rs2.5 Lakhs per annum. The salary for mid-level engineers can reach Rs3.8 lakhs. Experienced production engineers can make as much as Rs6.1 lakhs per year.
FAQ
What are the essential elements of running a logistics firm?
A successful logistics business requires a lot more than just knowledge. You must have good communication skills to interact effectively with your clients and suppliers. You must be able analyze data and draw out conclusions. You will need to be able handle pressure well and work in stressful situations. To improve efficiency, you must be innovative and creative. You must be a strong leader to motivate others and direct them to achieve organizational goals.
To meet tight deadlines, you must also be efficient and organized.
What are manufacturing and logistics?
Manufacturing is the production of goods using raw materials. Logistics manages all aspects of the supply chain, including procurement, production planning and distribution, inventory control, transportation, customer service, and transport. Sometimes manufacturing and logistics are combined to refer to a wider term that includes both the process of creating products as well as their delivery to customers.
What is production management?
Production Planning refers to the development of a plan for every aspect of production. This document ensures that everything is prepared and available when you are ready for shooting. It should also contain information on achieving the best results on set. It should include information about shooting locations, casting lists, crew details, equipment requirements, and shooting schedules.
The first step is to outline what you want to film. You may have decided where to shoot or even specific locations you want to use. Once you have determined your scenes and locations, it is time to start figuring out the elements that you will need for each scene. For example, you might decide that you need a car but don't know exactly what model you want. To narrow your options, you can search online for available models.
Once you have found the right car, you can start thinking about extras. Are you looking for people to sit in the front seats? Perhaps you have someone who needs to be able to walk around the back of your car. You may want to change the interior's color from black or white. These questions will help you determine the exact look and feel of your car. It is also worth considering the types of shots that you wish to take. Will you be filming close-ups or wide angles? Maybe you want to show the engine and the steering wheel. These factors will help you determine which car style you want to film.
Once you have determined all of the above, you can move on to creating a schedule. You can create a schedule that will outline when you must start and finish your shoots. A schedule for each day will detail when you should arrive at the location and when you need leave. It will help everyone know exactly what they have to do and when. If you need to hire extra staff, you can make sure you book them in advance. It's not worth paying someone to show up if you haven't told him.
It is important to calculate the amount of filming days when you are creating your schedule. Some projects are quick and easy, while others take weeks. While creating your schedule, it is important to remember whether you will require more than one shot per day. Multiple takes of the same location will lead to higher costs and take more time. It's better to be safe than sorry and shoot less takes if you're not certain whether you need more takes.
Budget setting is another important aspect in production planning. It is important to set a realistic budget so you can work within your budget. It is possible to reduce the budget at any time if you experience unexpected problems. But, don't underestimate how much money you'll spend. You'll end up with less money after paying for other things if the cost is underestimated.
Planning production is a tedious process. Once you have a good understanding of how everything works together, planning future projects becomes easy.
What does it mean to be a manufacturer?
Manufacturing Industries are businesses that produce products for sale. Consumers are those who purchase these products. These companies employ many processes to achieve this purpose, such as production and distribution, retailing, management and so on. They create goods from raw materials, using machines and various other equipment. This includes all types and varieties of manufactured goods, such as food items, clothings, building supplies, furnitures, toys, electronics tools, machinery vehicles, pharmaceuticals medical devices, chemicals, among others.
How can we increase manufacturing efficiency?
The first step is to determine the key factors that impact production time. We must then find ways that we can improve these factors. You can start by identifying the most important factors that impact production time. Once you've identified them, try to find solutions for each of those factors.
What is the difference between Production Planning, Scheduling and Production Planning?
Production Planning (PP), is the process of deciding what production needs to take place at any given time. This is done through forecasting demand and identifying production capacities.
Scheduling refers to the process of allocating specific dates to tasks in order that they can be completed within a specified timeframe.
What type of jobs is there in logistics
There are many types of jobs in logistics. These are some of the jobs available in logistics:
-
Warehouse workers – They load, unload and transport pallets and trucks.
-
Transportation drivers - They drive trucks and trailers to deliver goods and carry out pick-ups.
-
Freight handlers, - They sort out and pack freight in warehouses.
-
Inventory managers: They are responsible for the inventory and management of warehouses.
-
Sales reps - They sell products and services to customers.
-
Logistics coordinators - They organize and plan logistics operations.
-
Purchasing agents - They purchase goods and services needed for company operations.
-
Customer service agents - They answer phone calls and respond to emails.
-
Shipping clerks: They process shipping requests and issue bills.
-
Order fillers - They fill orders based on what is ordered and shipped.
-
Quality control inspectors - They check incoming and outgoing products for defects.
-
Other - Logistics has many other job opportunities, including transportation supervisors, logistics specialists, and cargo specialists.
Statistics
- (2:04) MTO is a production technique wherein products are customized according to customer specifications, and production only starts after an order is received. (oracle.com)
- According to the United Nations Industrial Development Organization (UNIDO), China is the top manufacturer worldwide by 2019 output, producing 28.7% of the total global manufacturing output, followed by the United States, Japan, Germany, and India.[52][53] (en.wikipedia.org)
- Many factories witnessed a 30% increase in output due to the shift to electric motors. (en.wikipedia.org)
- In 2021, an estimated 12.1 million Americans work in the manufacturing sector.6 (investopedia.com)
- Job #1 is delivering the ordered product according to specifications: color, size, brand, and quantity. (netsuite.com)
External Links
How To
How to Use the Just-In-Time Method in Production
Just-in time (JIT), is a process that reduces costs and increases efficiency in business operations. It is a process where you get the right amount of resources at the right moment when they are needed. This means that your only pay for the resources you actually use. Frederick Taylor, a 1900s foreman, first coined the term. Taylor observed that overtime was paid to workers if they were late in working. He concluded that if workers were given enough time before they start work, productivity would increase.
The idea behind JIT is that you should plan ahead and have everything ready so you don't waste money. It is important to look at your entire project from beginning to end and ensure that you have enough resources to handle any issues that may arise. If you anticipate that there might be problems, you'll have enough people and equipment to fix them. This will prevent you from spending extra money on unnecessary things.
There are different types of JIT methods:
-
Demand-driven: This type of JIT allows you to order the parts/materials required for your project on a regular basis. This will allow you to track how much material you have left over after using it. It will also allow you to predict how long it takes to produce more.
-
Inventory-based : You can stock the materials you need in advance. This allows for you to anticipate how much you can sell.
-
Project-driven : This is a method where you make sure that enough money is set aside to pay the project's cost. If you know the amount you require, you can buy the materials you need.
-
Resource-based JIT: This type of JIT is most commonly used. You assign certain resources based off demand. You will, for example, assign more staff to deal with large orders. If there aren't many orders, you will assign fewer people.
-
Cost-based: This is the same as resource-based except that you don't care how many people there are but how much each one of them costs.
-
Price-based: This approach is very similar to the cost-based method except that you don't look at individual workers costs but the total cost of the company.
-
Material-based is an alternative to cost-based. Instead of looking at the total cost in the company, this method focuses on the average amount of raw materials that you consume.
-
Time-based JIT: This is another variant of resource-based JIT. Instead of worrying about how much each worker costs, you can focus on how long the project takes.
-
Quality-based JIT - This is another form of resource-based JIT. Instead of worrying about the costs of each employee or how long it takes for something to be made, you should think about how quality your product is.
-
Value-based JIT: One of the most recent forms of JIT. You don't worry about whether the products work or if they meet customer expectations. Instead, your goal is to add value to the market.
-
Stock-based: This inventory-based approach focuses on how many items are being produced at any one time. This method is useful when you want to increase production while decreasing inventory.
-
Just-intime planning (JIT), is a combination JIT/sales chain management. It refers to the process of scheduling the delivery of components as soon as they are ordered. It is essential because it reduces lead-times and increases throughput.