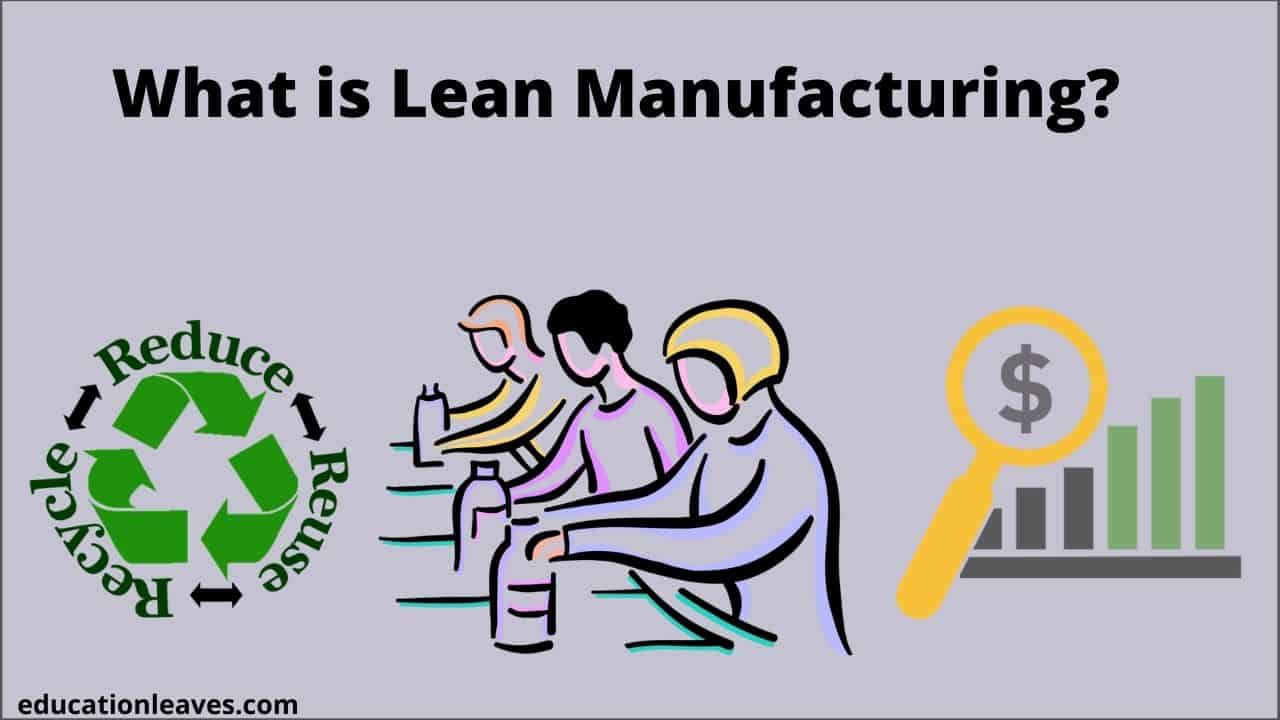
The business world is an ever-evolving process. Organizations must continually improve to stay competitive. From productivity to operations and communication, there are many things that a company can do to improve their operations.
Operational Excellence is a management method that aims to improve every aspect of a company's operation. Reduce waste, improve processes and develop efficient workflows.
The term operational excellence is derived from the management theory of scientific management, which originated in the 18th century and was influenced by the likes of Adam Smith, Frederick Winslow Taylor and Henry Ford. It takes years to implement, and there are many trials and errors. But it's worth the effort.
What is operational excellence?
Operational excellence is defined by the Institute for Operational Excellence as the ability to monitor the flow of product and information within the organization. This means everyone from the senior executives to the workers on the floor should be capable of detecting issues and observing product flow.
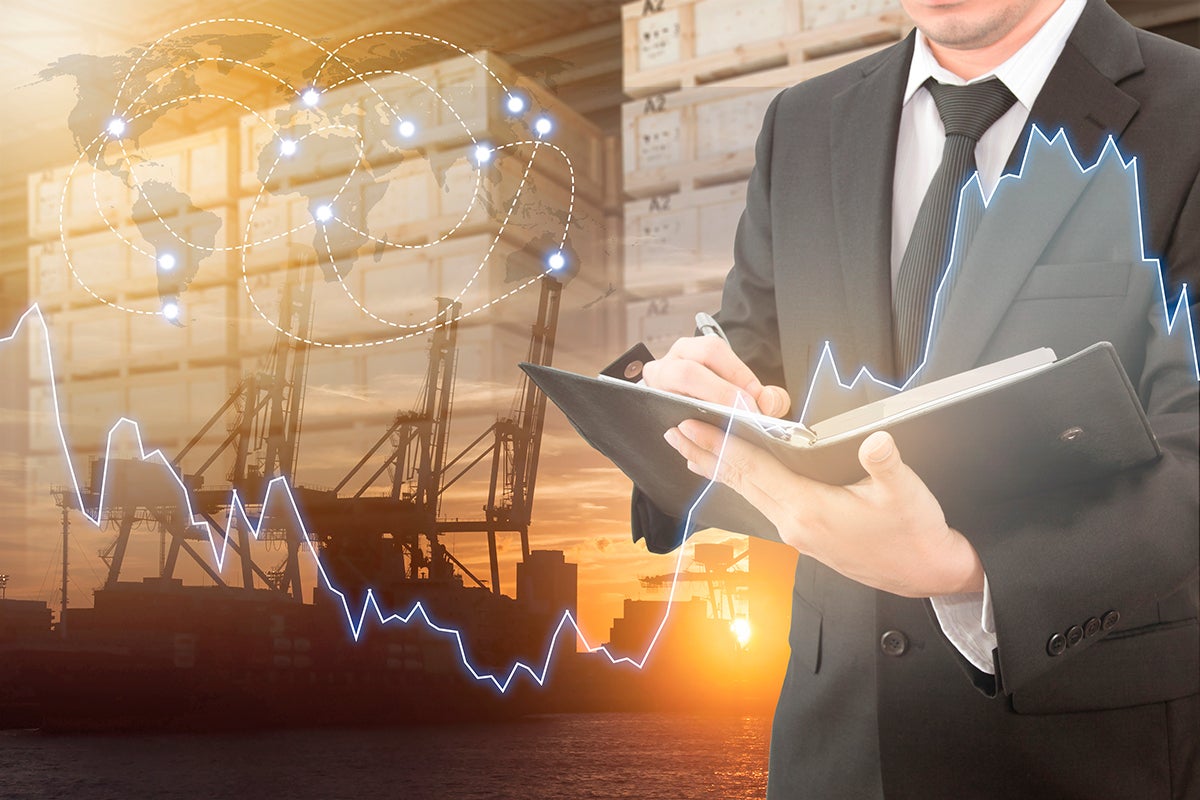
A culture change is required to create a culture of excellence in operations. Building trust with employees is a long-term process that takes time. It also involves a change in leadership styles and behavior, but it's an important step that can lead to long-term results.
What is the role for Operational Excellence Staffs?
Staff responsible for operational excellence are those who implement the organization's strategy. Their responsibilities involve overseeing improvement processes, participating in cross functional project teams, defining metrics and monitoring them, cultivating culture and mentoring operational excellence leaders.
Also, they may lead projects using improvement methodologies like Six Sigma and Kaizen. These methods can transform operations and improve efficiency. However they require skilled staff with expertise in areas such project management and Business Intelligence.
How to Create a Plan of Operational Excellence
A plan of operational excellence must include a set of methodologies that will enable you to achieve your goals in the shortest time possible. It is important to consider this if you're looking to improve customer satisfaction, reduce waste and streamline your processes.
You can use various KPIs for tracking your progress. They should be relevant to the goals you have set and realistic to encourage employees to strive towards excellence.
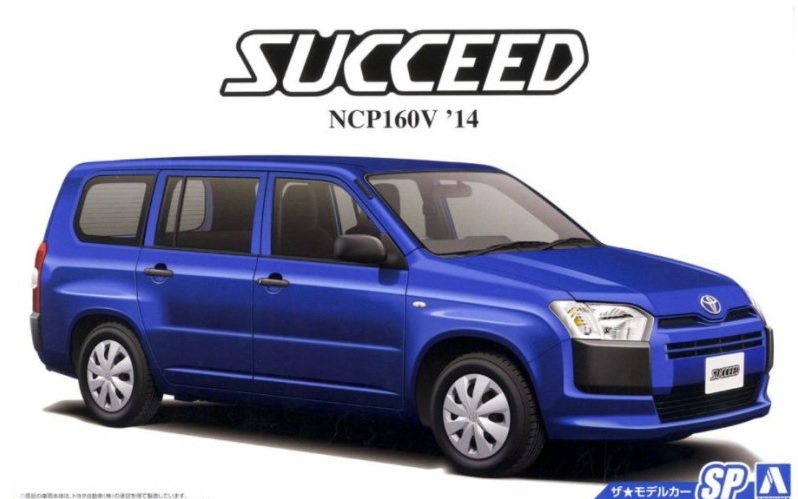
Using these tools ensures that your operations will be as efficient and cost effective as possible. The tools also allow you to collect feedback from your staff on the front lines so that you may continue to improve.
How to measure your operational excellence goals
Most directors of operations will use a combination of financial and operational data at a high level, along with qualitative information from employee and customer surveys. This will help them to get a better idea of how well they're doing and how near they are to their objectives.
This is because operational excellence works at every level of the company, so it's vital to make sure that all of the individual team members have their own targets. For example, a Director of Operations needs to have a profit target around what they spend on people, while a project manager should have their own targets around billable and non-billable work. The operational excellence of an organization can then be measured on all levels. This will ensure that revenue and costs are equal.
FAQ
What is meant by manufacturing industries?
Manufacturing Industries are businesses that produce products for sale. The people who buy these products are called consumers. These companies use a variety processes such as distribution, retailing and management to accomplish their purpose. They create goods from raw materials, using machines and various other equipment. This includes all types and varieties of manufactured goods, such as food items, clothings, building supplies, furnitures, toys, electronics tools, machinery vehicles, pharmaceuticals medical devices, chemicals, among others.
Why automate your warehouse?
Automation has become increasingly important in modern warehousing. Increased demand for efficient and faster delivery has resulted in a rise in e-commerce.
Warehouses have to be flexible to meet changing requirements. Technology is essential for warehouses to be able to adapt quickly to changing needs. Automating warehouses has many benefits. Here are some benefits of investing in automation
-
Increases throughput/productivity
-
Reduces errors
-
Increases accuracy
-
Safety enhancements
-
Eliminates bottlenecks
-
Companies can scale more easily
-
Workers are more productive
-
It gives visibility to everything that happens inside the warehouse
-
Enhances customer experience
-
Improves employee satisfaction
-
Reduces downtime and improves uptime
-
High quality products delivered on-time
-
Eliminates human error
-
It ensures compliance with regulations
Can certain manufacturing steps be automated?
Yes! Automation has been around since ancient times. The Egyptians created the wheel thousands years ago. We now use robots to help us with assembly lines.
Actually, robotics can be used in manufacturing for many purposes. They include:
-
Line robots
-
Robot welding
-
Robot painting
-
Robotics inspection
-
Robots that make products
Manufacturing can also be automated in many other ways. 3D printing makes it possible to produce custom products in a matter of days or weeks.
What are the differences between these four types?
Manufacturing is the process that transforms raw materials into useful products. Manufacturing involves many activities, including designing, building, testing and packaging, shipping, selling, service, and so on.
What is the difference between Production Planning, Scheduling and Production Planning?
Production Planning (PP), or production planning, is the process by which you determine what products are needed at any given time. Forecasting and identifying production capacity are two key elements to this process.
Scheduling is the process that assigns dates to tasks so they can get completed within a given timeframe.
Why is logistics important in manufacturing
Logistics are an integral part any business. They enable you to achieve outstanding results by helping manage product flow from raw materials through to finished goods.
Logistics play an important role in reducing costs as well as increasing efficiency.
Statistics
- You can multiply the result by 100 to get the total percent of monthly overhead. (investopedia.com)
- In the United States, for example, manufacturing makes up 15% of the economic output. (twi-global.com)
- It's estimated that 10.8% of the U.S. GDP in 2020 was contributed to manufacturing. (investopedia.com)
- In 2021, an estimated 12.1 million Americans work in the manufacturing sector.6 (investopedia.com)
- According to the United Nations Industrial Development Organization (UNIDO), China is the top manufacturer worldwide by 2019 output, producing 28.7% of the total global manufacturing output, followed by the United States, Japan, Germany, and India.[52][53] (en.wikipedia.org)
External Links
How To
How to use the Just-In Time Method in Production
Just-in time (JIT), is a process that reduces costs and increases efficiency in business operations. It's a way to ensure that you get the right resources at just the right time. This means that your only pay for the resources you actually use. Frederick Taylor, a 1900s foreman, first coined the term. He noticed that workers were often paid overtime when they had to work late. He decided to ensure workers have enough time to do their jobs before starting work to improve productivity.
JIT is a way to plan ahead and make sure you don't waste any money. You should also look at the entire project from start to finish and make sure that you have sufficient resources available to deal with any problems that arise during the course of your project. If you expect problems to arise, you will be able to provide the necessary equipment and personnel to address them. You won't have to pay more for unnecessary items.
There are several types of JIT techniques:
-
Demand-driven: This JIT is where you place regular orders for the parts/materials that are needed for your project. This will allow for you to track the material that you have left after using it. This will allow to you estimate the time it will take for more to be produced.
-
Inventory-based: This type allows you to stock the materials needed for your projects ahead of time. This allows you to forecast how much you will sell.
-
Project-driven: This is an approach where you set aside enough funds to cover the cost of your project. Knowing how much money you have available will help you purchase the correct amount of materials.
-
Resource-based JIT: This type of JIT is most commonly used. This is where you assign resources based upon demand. You might assign more people to help with orders if there are many. If you don’t have many orders you will assign less people to the work.
-
Cost-based: This is similar to resource-based, except that here you're not just concerned about how many people you have but how much each person costs.
-
Price-based: This approach is very similar to the cost-based method except that you don't look at individual workers costs but the total cost of the company.
-
Material-based: This is quite similar to cost-based, but instead of looking at the total cost of the company, you're concerned with how much raw materials you spend on average.
-
Time-based JIT: A variation on resource-based JIT. Instead of focusing on the cost of each employee, you will focus on the time it takes to complete a project.
-
Quality-based: This is yet another variation of resource-based JIT. Instead of focusing on the cost of each worker or how long it takes, think about how high quality your product is.
-
Value-based JIT : This is the newest type of JIT. In this scenario, you're not concerned about how products perform or whether customers expect them to meet their expectations. Instead, your focus is on the value you bring to the market.
-
Stock-based is an inventory-based system that measures the number of items produced at any given moment. This method is useful when you want to increase production while decreasing inventory.
-
Just-in-time planning (JIT): This is a combination JIT and supply-chain management. This refers to the scheduling of the delivery of components as soon after they are ordered. This is important as it reduces lead time and increases throughput.