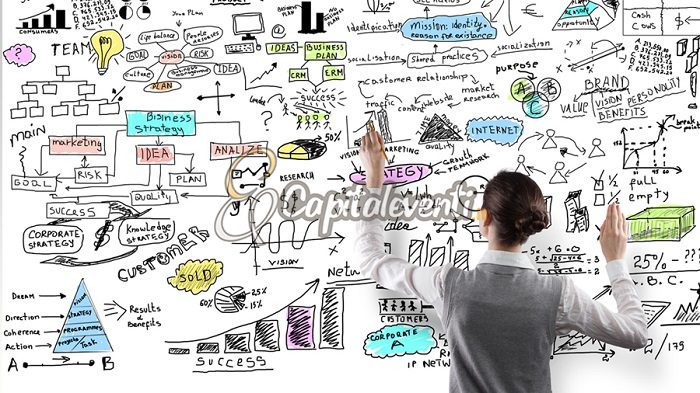
GembaWalk was initially developed by Toyota. The tool allows managers and employees to see the floor so they can gain insight into company processes. This is an integral part of any facility renovation. It allows managers and employees to be more aware of the business processes and make better decision. It helps to identify both potential and existing problems.
Gemba is a Japanese term that means "where the work happens." Gemba is used to refer to the shop floor or factory floor. However, it can also be used to describe any area where a product is created. Gemba is also the Japanese business philosophy. It outlines a set of objectives. In general, the goal of Gemba is to achieve in-depth knowledge of the processes in an organization, while eliminating waste and improving efficiency.
Gemba walks are important for companies that are looking to improve their processes and to eliminate waste. They encourage cooperation within the organization. They encourage employees and their families to share ideas. This can increase the quality of any product or service. They are also a great way to help executives and managers understand the business processes.
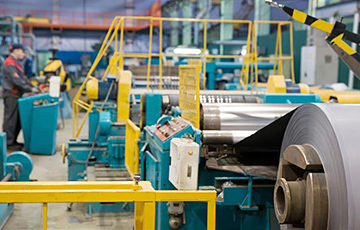
Gemba walks can usually be carried out by supervisors and managers. But, they can also easily be undertaken by executives. Gemba walks should not be performed by managers or supervisors. Gemba walks should last between 45-60 minutes per week. The best time to observe workers' work is during their busiest hours.
Gemba Walks are designed to help executives and managers understand the process and identify improvements. They can also be used to improve safety and security in the workplace. Safety issues represent the greatest waste in manufacturing facilities. Improving safety can make it possible to improve continuously.
Gemba Walks play an important role in Lean. However, they should be applied at all levels within the organization. They are a great way for executives and leaders to get a fresh view on customers. This will lead to better products and services. Gemba Walks are an effective way to help your organization reach its full potential.
Gemba Walks play an important role in Lean process designs. They are often used as part of Kaizen events by key stakeholders. Kaizen events are gatherings of key stakeholders that evaluate activities and assess activities. They are based on the Japanese term "continuous improvement."
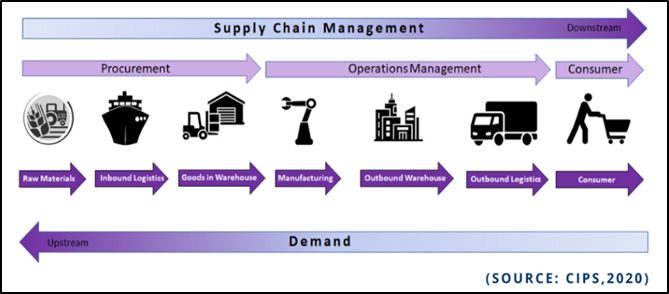
Gemba Walks must be done regularly. If done correctly, they can help to eliminate waste and improve productivity. They are best done during the busiest periods of the day. This will provide executives and project manager with a new outlook on their business. Managers and project managers should take note of any improvements that they find, including new products or services, as well as any suggestions from employees.
FAQ
What makes a production planner different from a project manger?
The primary difference between a producer planner and a manager of a project is that the manager usually plans and organizes the whole project, while a production planner is only involved in the planning stage.
What are the products and services of logistics?
Logistics refers to the movement of goods from one place to another.
They encompass all aspects transport, including packaging and loading, transporting, storage, unloading.
Logisticians ensure that the right product reaches the right place at the right time and under safe conditions. They provide information on demand forecasts as well stock levels, production schedules and availability of raw material.
They can also track shipments in transit and monitor quality standards.
How can we reduce manufacturing overproduction?
Better inventory management is key to reducing excess production. This would reduce the amount of time spent on unnecessary activities such as purchasing, storing, and maintaining excess stock. This will allow us to free up resources for more productive tasks.
You can do this by adopting a Kanban method. A Kanban board can be used to monitor work progress. Work items are moved through various states to reach their destination in a Kanban system. Each state has a different priority level.
When work is completed, it can be transferred to the next stage. If a task is still in its beginning stages, it will continue to be so until it reaches the end.
This keeps work moving and ensures no work is lost. With a Kanban board, managers can see exactly how much work is being done at any given moment. This information allows managers to adjust their workflow based off real-time data.
Lean manufacturing, another method to control inventory levels, is also an option. Lean manufacturing focuses on eliminating waste throughout the entire production chain. Anything that does nothing to add value to a product is waste. These are some of the most common types.
-
Overproduction
-
Inventory
-
Packaging that is not necessary
-
Material surplus
By implementing these ideas, manufacturers can improve efficiency and cut costs.
Why automate your warehouse
Modern warehousing has seen automation take center stage. E-commerce has increased the demand for quicker delivery times and more efficient processes.
Warehouses have to be flexible to meet changing requirements. Technology is essential for warehouses to be able to adapt quickly to changing needs. Automation of warehouses offers many benefits. These are some of the benefits that automation can bring to warehouses:
-
Increases throughput/productivity
-
Reduces errors
-
Accuracy is improved
-
Safety is boosted
-
Eliminates bottlenecks
-
Allows companies scale more easily
-
Increases efficiency of workers
-
It gives visibility to everything that happens inside the warehouse
-
Enhances customer experience
-
Improves employee satisfaction
-
This reduces downtime while increasing uptime
-
Quality products delivered on time
-
Eliminates human error
-
Helps ensure compliance with regulations
Statistics
- Many factories witnessed a 30% increase in output due to the shift to electric motors. (en.wikipedia.org)
- In 2021, an estimated 12.1 million Americans work in the manufacturing sector.6 (investopedia.com)
- [54][55] These are the top 50 countries by the total value of manufacturing output in US dollars for its noted year according to World Bank.[56] (en.wikipedia.org)
- You can multiply the result by 100 to get the total percent of monthly overhead. (investopedia.com)
- According to the United Nations Industrial Development Organization (UNIDO), China is the top manufacturer worldwide by 2019 output, producing 28.7% of the total global manufacturing output, followed by the United States, Japan, Germany, and India.[52][53] (en.wikipedia.org)
External Links
How To
How to use the Just-In Time Method in Production
Just-in time (JIT), is a process that reduces costs and increases efficiency in business operations. It allows you to get the right amount resources at the right time. This means that only what you use is charged to your account. The term was first coined by Frederick Taylor, who developed his theory while working as a foreman in the early 1900s. Taylor observed that overtime was paid to workers if they were late in working. He realized that workers should have enough time to complete their jobs before they begin work. This would help increase productivity.
JIT is an acronym that means you need to plan ahead so you don’t waste your money. It is important to look at your entire project from beginning to end and ensure that you have enough resources to handle any issues that may arise. You can anticipate problems and have enough equipment and people available to fix them. This way you won't be spending more on things that aren’t really needed.
There are many JIT methods.
-
Demand-driven: This JIT is where you place regular orders for the parts/materials that are needed for your project. This will allow to track how much material has been used up. You'll also be able to estimate how long it will take to produce more.
-
Inventory-based : You can stock the materials you need in advance. This allows for you to anticipate how much you can sell.
-
Project-driven: This is an approach where you set aside enough funds to cover the cost of your project. Once you have an idea of how much material you will need, you can purchase the necessary materials.
-
Resource-based JIT: This is the most popular form of JIT. You assign certain resources based off demand. You might assign more people to help with orders if there are many. If you don't have many orders, you'll assign fewer people to handle the workload.
-
Cost-based: This approach is very similar to resource-based. However, you don't just care about the number of people you have; you also need to consider how much each person will cost.
-
Price-based: This is similar to cost-based but instead of looking at individual workers' salaries, you look at the total company price.
-
Material-based: This approach is similar to cost-based. However, instead of looking at the total cost for the company, you look at how much you spend on average on raw materials.
-
Time-based: This is another variation of resource-based JIT. Instead of focusing only on how much each employee is costing, you should focus on how long it takes to complete your project.
-
Quality-based JIT is another variant of resource-based JIT. Instead of focusing on the cost of each worker or how long it takes, think about how high quality your product is.
-
Value-based JIT: This is the latest form of JIT. This is where you don't care about how the products perform or whether they meet customers' expectations. Instead, you focus on the added value that you provide to your market.
-
Stock-based. This method is inventory-based and focuses only on the actual production at any given point. It is used when production goals are met while inventory is kept to a minimum.
-
Just-intime (JIT), planning is a combination JIT management and supply chain management. It is the process that schedules the delivery of components within a short time of their order. It reduces lead times and improves throughput.