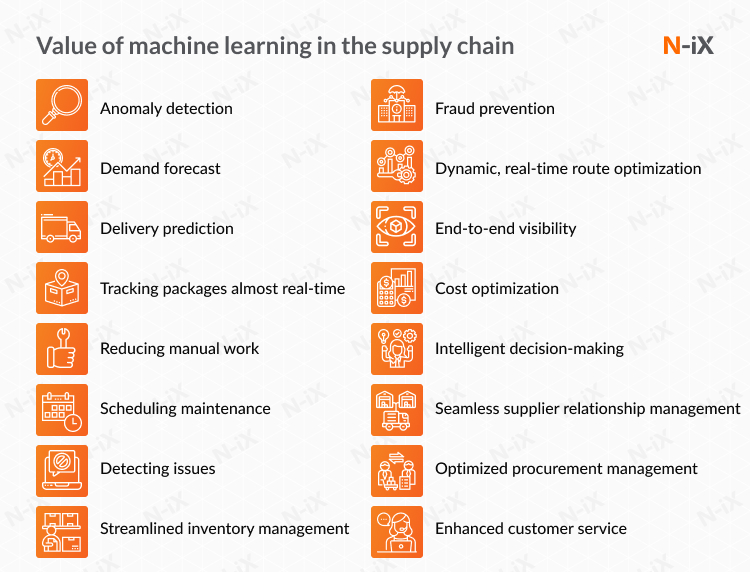
If you are able to locate the right job opportunities, it is easy to get a job as a logistics professional in Dallas. You will find work in many different industries including shipping, trucking and logistics. All levels of employment are available, including executive and entry-level roles. Also, you can get free advice and guidance from human resources professionals.
Dallas' growing logistics industry is an industry that is rapidly developing. You can expect a good pay and benefits package from the get go. Some of the most lucrative jobs include free health insurance and gym memberships. A courier job is a great option for a new graduate looking for their first job. You can also opt for a position as a driver. Expect to work five shifts a week.
If you have a driver’s licence, excellent credit and a strong work history, you can get a job as a Dallas logistics manager. A local community college may offer a driver's education program that is free to you. You might also be eligible to join a military preferred hire program.
There are many interesting jobs available in the logistics sector that require a wide range skills. A job as a driver, transport service specialist or courier can be found. An executive assistant, supply chain analyst, warehouse manager or warehouse manager are all possible options. You will have many responsibilities as a job holder. However, your most important task will be to coordinate key activities in your organization. You will be able to execute the best strategies possible to ensure smooth goods flow. There are many jobs available in the logistics industry, which is growing rapidly in Dallas. There are many positions available at local companies, including those for truck drivers, couriers, and executive assistants. It's a great way for you to get in the door. Apply online if there is a position that interests you. There are a number of job portals that allow you to browse and apply for jobs in Dallas. Online job listings are also available for free to view what companies are seeking.
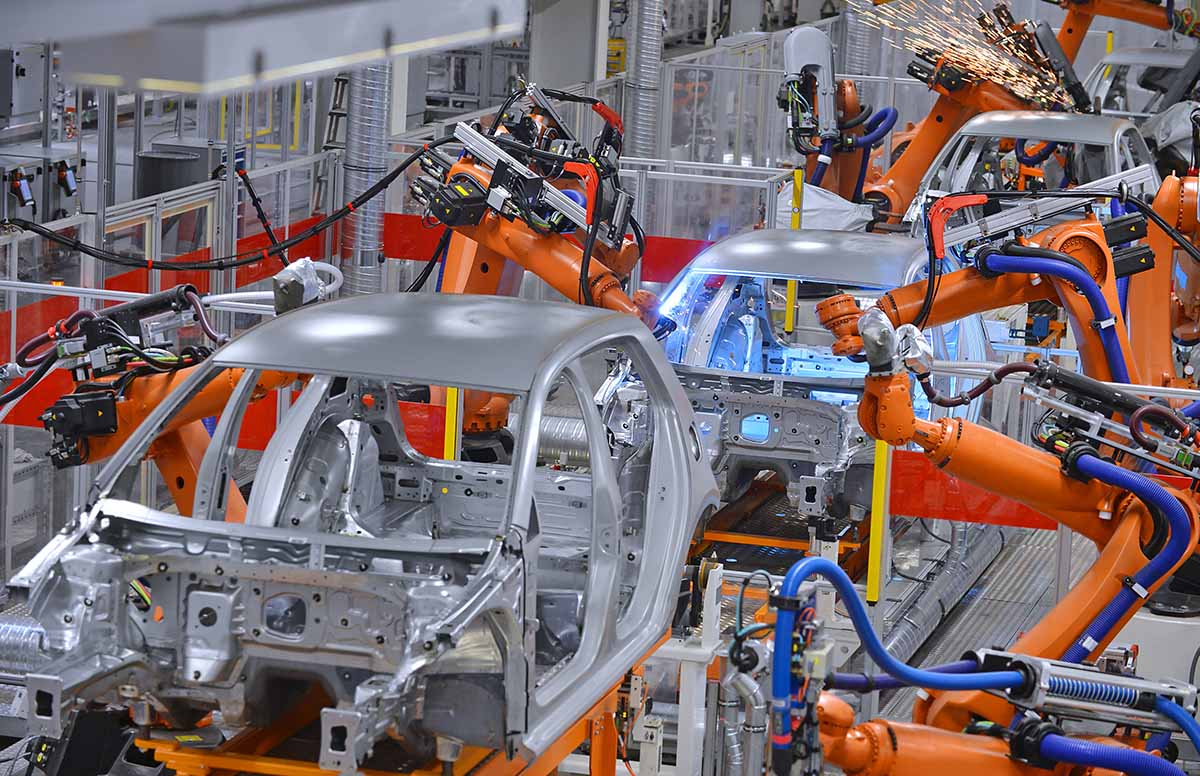
The logistics industry is filled with exciting opportunities, from truck driver to logistics manager to executive assistant. You can find the best jobs in Dallas by browsing through a number of job sites. CareerOneStop has a free online job portal that will allow you to view the jobs available in your local area. The best thing is that you get free advice and guidance from human resources professionals.
FAQ
What are the responsibilities of a production planner
Production planners make sure that every aspect of the project is delivered on-time, within budget, and within schedule. They also ensure the quality of the product and service meets the client's requirements.
What are the 7 Rs of logistics?
The acronym 7R's for Logistics stands to represent the seven basic principles in logistics management. It was published in 2004 by the International Association of Business Logisticians as part of their "Seven Principles of Logistics Management" series.
The acronym is made up of the following letters:
-
Responsible - ensure that all actions taken are within legal requirements and are not harmful to others.
-
Reliable: Have faith in your ability or the ability to honor any promises made.
-
It is reasonable to use resources efficiently and not waste them.
-
Realistic - Consider all aspects of operations, including environmental impact and cost effectiveness.
-
Respectful – Treat others fairly and equitably.
-
Reliable - Find ways to save money and increase your productivity.
-
Recognizable is a company that provides customers with value-added solutions.
What does "warehouse" mean?
A warehouse, or storage facility, is where goods are stored prior to being sold. It can be indoors or out. It may also be an indoor space or an outdoor area.
How can manufacturing excess production be decreased?
It is essential to find better ways to manage inventory to reduce overproduction. This would reduce the time spent on unproductive activities like purchasing, storing and maintaining excess stock. This will allow us to free up resources for more productive tasks.
You can do this by adopting a Kanban method. A Kanban board, a visual display to show the progress of work, is called a Kanban board. Kanban systems allow work items to move through different states until they reach their final destination. Each state is assigned a different priority.
If work is moving from one stage to the other, then the current task can be completed and moved on to the next. A task that is still in the initial stages of a process will be considered complete until it moves on to the next stage.
This keeps work moving and ensures no work is lost. Managers can monitor the work being done by Kanban boards to see what is happening at any given time. This information allows managers to adjust their workflow based off real-time data.
Lean manufacturing is another option to control inventory levels. Lean manufacturing emphasizes eliminating waste in all phases of production. Waste includes anything that does not add value to the product. These are some of the most common types.
-
Overproduction
-
Inventory
-
Packaging not required
-
Materials in excess
By implementing these ideas, manufacturers can improve efficiency and cut costs.
What is manufacturing and logistics?
Manufacturing refers the process of producing goods from raw materials through machines and processes. Logistics is the management of all aspects of supply chain activities, including procurement, production planning, distribution, warehousing, inventory control, transportation, and customer service. Sometimes manufacturing and logistics are combined to refer to a wider term that includes both the process of creating products as well as their delivery to customers.
What jobs are available in logistics?
There are different kinds of jobs available in logistics. Here are some:
-
Warehouse workers - They load trucks and pallets.
-
Transportation drivers – These drivers drive trucks and wagons to transport goods and pick up the goods.
-
Freight handlers are people who sort and pack freight into warehouses.
-
Inventory managers: They are responsible for the inventory and management of warehouses.
-
Sales representatives - They sell products to customers.
-
Logistics coordinators - They plan and organize logistics operations.
-
Purchasing agents - They buy goods and services that are necessary for company operations.
-
Customer service agents - They answer phone calls and respond to emails.
-
Shipping clerks - They process shipping orders and issue bills.
-
Order fillers - They fill orders based on what is ordered and shipped.
-
Quality control inspectors - They check incoming and outgoing products for defects.
-
Others - There are many types of jobs in logistics such as transport supervisors and cargo specialists.
Is it necessary to be familiar with Manufacturing Processes before we learn about Logistics.
No. No. But, being familiar with manufacturing processes will give you a better understanding about how logistics works.
Statistics
- Job #1 is delivering the ordered product according to specifications: color, size, brand, and quantity. (netsuite.com)
- In 2021, an estimated 12.1 million Americans work in the manufacturing sector.6 (investopedia.com)
- You can multiply the result by 100 to get the total percent of monthly overhead. (investopedia.com)
- According to a Statista study, U.S. businesses spent $1.63 trillion on logistics in 2019, moving goods from origin to end user through various supply chain network segments. (netsuite.com)
- Many factories witnessed a 30% increase in output due to the shift to electric motors. (en.wikipedia.org)
External Links
How To
Six Sigma and Manufacturing
Six Sigma can be described as "the use of statistical process control (SPC), techniques to achieve continuous improvement." Motorola's Quality Improvement Department created Six Sigma at their Tokyo plant, Japan in 1986. Six Sigma's main goal is to improve process quality by standardizing processes and eliminating defects. This method has been adopted by many companies in recent years as they believe there are no perfect products or services. Six Sigma's primary goal is to reduce variation from the average value of production. This means that if you take a sample of your product, then measure its performance against the average, you can find out what percentage of the time the process deviates from the norm. If the deviation is excessive, it's likely that something needs to be fixed.
The first step toward implementing Six Sigma is understanding how variability works in your business. Once you understand that, it is time to identify the sources of variation. This will allow you to decide if these variations are random and systematic. Random variations occur when people do mistakes. Symmetrical variations are caused due to factors beyond the process. These are, for instance, random variations that occur when widgets are made and some fall off the production line. You might notice that your widgets always fall apart at the same place every time you put them together.
Once you identify the problem areas, it is time to create solutions. That solution might involve changing the way you do things or redesigning the process altogether. You should then test the changes again after they have been implemented. If they don’t work, you’ll need to go back and rework the plan.