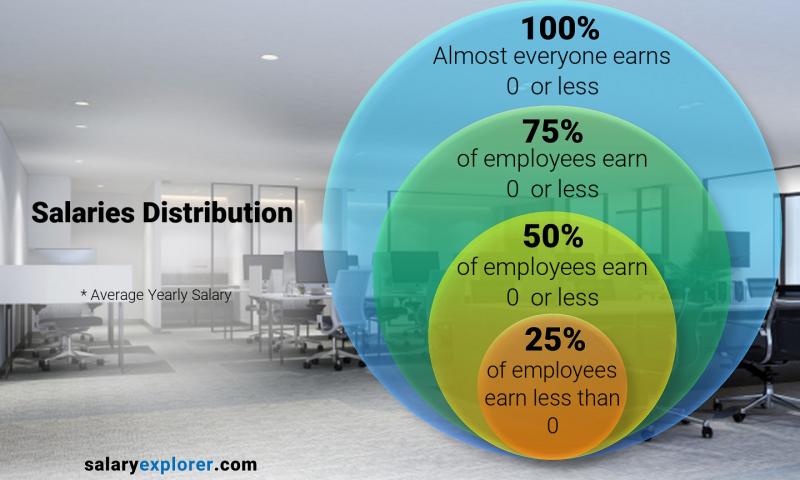
If you are interested in a biochemical salary, you're in the right place. This article will describe biochemical salaries at BOTHELL WA and San Mateo CA. Learn more about the different salary options for biochemical professionals to get you started in your career. Learn more about the job descriptions and salary requirements at Worthington Biochemical and Youtell Biochemical. Both of these companies are located in BOTHELL WA. They offer competitive benefits and excellent compensation.
Youtell Biochemical's hourly salary is $29
The average salary at Youtell Biochemical is $99,854. Salaries can vary from $88,159 to $114,509. Salary ranges from $88,159 up to $114,509, depending on what the position is, how much education they have and the skills required. Here are some examples of salaries and job types at Youtell Biochemical. Remember that education and experience are important factors in determining the range of salaries.
Youtell Biochemical headquarters are located in BOTHELL WA
Youtell Biochemical is a chemical company headquartered in BOTHELL, WA that focuses on enzyme products. They have a stateof-the-art biotechnology center in Bothell, as well two downstream processing plants and fermentation factories located in China. These companies employ patented technologies to make enzyme products. Youtell Biochemical produces over 80,000 tons per year of enzyme products at its main campus in BOTHELL WA.
Worthington Biochemical is based in San Mateo, CA
Worthington Biochemical started in 1947. Charles Worthington, its founder, was a Rockefeller Institute researcher who prepared crystallized enzymes for use with biochemical research. He soon realized that biochemical researchers needed reliable, high-purity proteins and that they would need to be purified by scientists. Worthington started his own company in 1947, in Freehold, New Jersey, to supply these enzymes.
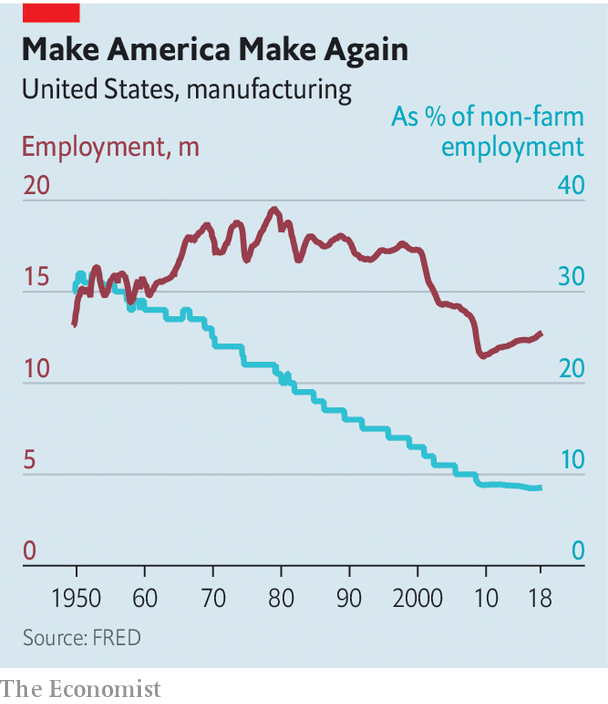
Worthington purchased the New Jersey-based biotech company, Clinical Division of Cooper in 1985. Worthington could expand its operations and focus on the lucrative market for clinical research with this acquisition. However, the company failed to expand into the fields of molecular biology and immunology. Instead, the company developed diagnostic kits for more customers, but devoted less to enzyme production.
FAQ
Why automate your warehouse
Modern warehousing has seen automation take center stage. E-commerce has brought increased demand for more efficient and quicker delivery times.
Warehouses must adapt quickly to meet changing customer needs. Technology is essential for warehouses to be able to adapt quickly to changing needs. Automating warehouses has many benefits. Here are some benefits of investing in automation
-
Increases throughput/productivity
-
Reduces errors
-
Increases accuracy
-
Boosts safety
-
Eliminates bottlenecks
-
This allows companies to scale easily
-
Workers are more productive
-
It gives visibility to everything that happens inside the warehouse
-
Enhances customer experience
-
Improves employee satisfaction
-
Reduces downtime and improves uptime
-
This ensures that quality products are delivered promptly
-
Removes human error
-
It ensures compliance with regulations
What types of jobs can you find in logistics
There are many types of jobs in logistics. Here are some examples:
-
Warehouse workers – They load, unload and transport pallets and trucks.
-
Transport drivers - These are people who drive trucks and trailers to transport goods or perform pick-ups.
-
Freight handlers - They sort and pack freight in warehouses.
-
Inventory managers – These people oversee inventory at warehouses.
-
Sales representatives: They sell products to customers.
-
Logistics coordinators: They plan and manage logistics operations.
-
Purchasing agents - They purchase goods and services needed for company operations.
-
Customer service representatives are available to answer customer calls and emails.
-
Shipping clerks – They process shipping orders, and issue bills.
-
Order fillers – They fill orders based upon what was ordered and shipped.
-
Quality control inspectors - They check incoming and outgoing products for defects.
-
Others - There is a variety of other jobs in logistics. These include transportation supervisors and cargo specialists.
What is the role of a logistics manager
Logistics managers ensure that goods arrive on time and are unharmed. This is done by using his/her experience and knowledge of the company's products. He/she also needs to ensure adequate stock to meet demand.
How can we improve manufacturing efficiency?
First, we need to identify which factors are most critical in affecting production times. Next, we must find ways to improve those factors. If you aren't sure where to begin, think about the factors that have the greatest impact on production time. Once you've identified them all, find solutions to each one.
Statistics
- It's estimated that 10.8% of the U.S. GDP in 2020 was contributed to manufacturing. (investopedia.com)
- According to the United Nations Industrial Development Organization (UNIDO), China is the top manufacturer worldwide by 2019 output, producing 28.7% of the total global manufacturing output, followed by the United States, Japan, Germany, and India.[52][53] (en.wikipedia.org)
- You can multiply the result by 100 to get the total percent of monthly overhead. (investopedia.com)
- In 2021, an estimated 12.1 million Americans work in the manufacturing sector.6 (investopedia.com)
- (2:04) MTO is a production technique wherein products are customized according to customer specifications, and production only starts after an order is received. (oracle.com)
External Links
How To
How to Use the Just-In-Time Method in Production
Just-intime (JIT), which is a method to minimize costs and maximize efficiency in business process, is one way. It is a process where you get the right amount of resources at the right moment when they are needed. This means that only what you use is charged to your account. Frederick Taylor, a 1900s foreman, first coined the term. Taylor observed that overtime was paid to workers if they were late in working. He decided to ensure workers have enough time to do their jobs before starting work to improve productivity.
The idea behind JIT is that you should plan ahead and have everything ready so you don't waste money. Also, you should look at the whole project from start-to-finish and make sure you have the resources necessary to address any issues. You can anticipate problems and have enough equipment and people available to fix them. This will prevent you from spending extra money on unnecessary things.
There are different types of JIT methods:
-
Demand-driven: This JIT is where you place regular orders for the parts/materials that are needed for your project. This will enable you to keep track of how much material is left after you use it. This will allow you to calculate how long it will take to make more.
-
Inventory-based: You stock materials in advance to make your projects easier. This allows for you to anticipate how much you can sell.
-
Project-driven: This is an approach where you set aside enough funds to cover the cost of your project. You will be able to purchase the right amount of materials if you know what you need.
-
Resource-based JIT: This is the most popular form of JIT. Here you can allocate certain resources based purely on demand. For instance, if you have a lot of orders coming in, you'll assign more people to handle them. If you don't have many orders, you'll assign fewer people to handle the workload.
-
Cost-based: This approach is very similar to resource-based. However, you don't just care about the number of people you have; you also need to consider how much each person will cost.
-
Price-based: This is a variant of cost-based. However, instead of focusing on the individual workers' costs, this looks at the total price of the company.
-
Material-based: This is quite similar to cost-based, but instead of looking at the total cost of the company, you're concerned with how much raw materials you spend on average.
-
Time-based: Another variation of resource-based JIT. Instead of focusing only on how much each employee is costing, you should focus on how long it takes to complete your project.
-
Quality-based JIT: Another variation on resource-based JIT. Instead of focusing on the cost of each worker or how long it takes, think about how high quality your product is.
-
Value-based: This is one of the newest forms of JIT. In this scenario, you're not concerned about how products perform or whether customers expect them to meet their expectations. Instead, you focus on the added value that you provide to your market.
-
Stock-based is an inventory-based system that measures the number of items produced at any given moment. It's used when you want to maximize production while minimizing inventory.
-
Just-intime (JIT), planning is a combination JIT management and supply chain management. It's the process of scheduling delivery of components immediately after they are ordered. This is important as it reduces lead time and increases throughput.