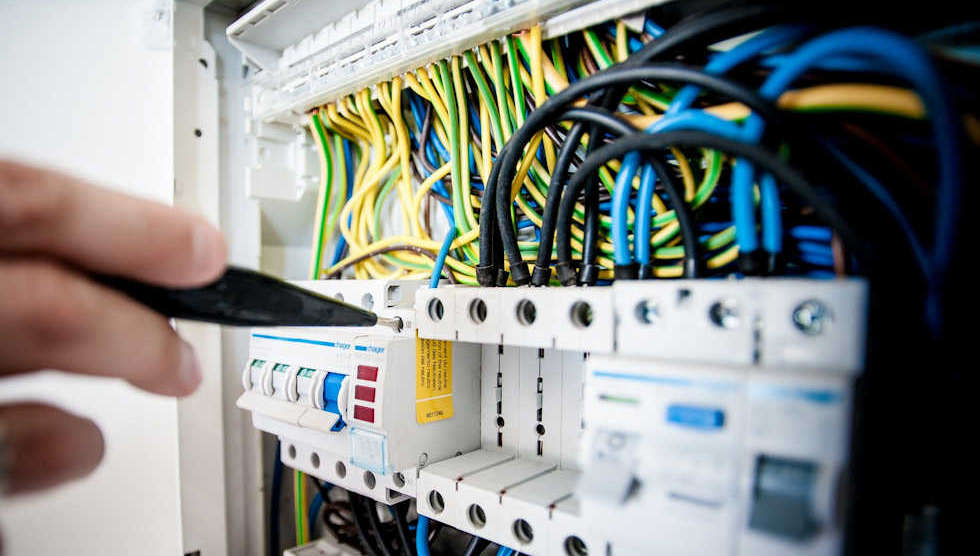
Facilities engineers, also called maintenance engineers, are professionals that provide engineering and construction support for buildings and operations. They are responsible for developing and implementing procedures and recommending repairs and upgrades. They also coordinate routine and emergency maintenance. Their duties can include many engineering disciplines such, as mechanical, electrical and plumbing. They are skilled in technical knowledge, but also have an excellent understanding of the law and safety standards that govern construction.
Facilities engineers start their careers at the entry level and can quickly progress to higher-ranking positions. The best way to stand out in the field is to build a strong portfolio, which may include engineering projects, research, and articles. Facilities engineers must continue to study their specialty. This will make them stand out when they apply for a new job.
Although it is not mandatory for all facilities engineers, a professional engineer certification can be a big advantage when applying for a new position. An engineer must have a good understanding of engineering principles and concepts. They should also be able to make compelling presentations and analyze data. A facility engineer, for example, should have knowledge of asset reliability-centered and predictive maintenance strategies as well as the design of facilities.
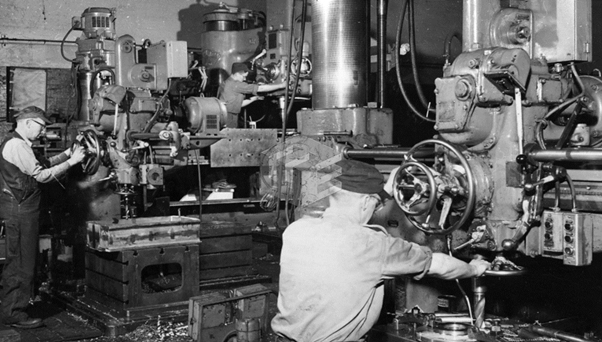
Facility engineers work in offices, construction, and manufacturing environments. They manage and implement processes that ensure safe, efficient, effective, and reliable operation of utility systems. Facilities engineers work closely with managers and other engineers. This helps to make work more efficient and resolves any problems.
A facilities engineer's responsibilities will vary based on the size and type of facility he or she is assigned to work in. The job requires great time management skills, problem solving abilities, and the ability to interact well with others. In a typical day, a facility engineer can perform hundreds of tasks. The facilities engineer can be responsible for plumbing, electrical, and mechanical equipment. He or she must also be able to diagnose and correct malfunctions.
Many websites offer information and news about the field, including the Association of Facility Engineers' (AFE) website. These websites provide information such as a sample resume, salary information and articles about job opportunities.
Besides these websites, facilities engineers can read books and articles, attend training courses, and network with other engineers. In order to be a successful facilities engineer, you should have good organizational skills, a good understanding of various engineering and construction disciplines, and a solid understanding of building and safety codes.
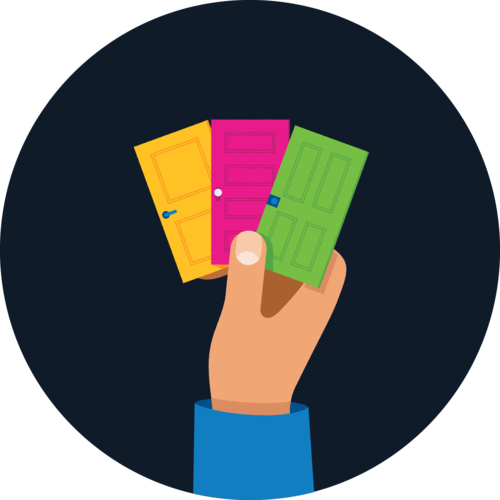
It's important to note that some of the most advanced facilities engineers are able to analyze data and perform a number of tasks at once. For this to happen, they will need to have a working knowledge about AutoCAD as well construction techniques such the CAM. You will also benefit from skills such as project management, critical thinking and problem solving.
The best thing about a job as a facilities engineer is the ability to work alongside a variety of people. These engineers are skilled in working with various materials and are able coordinate the work of other engineers.
FAQ
How can excess manufacturing production be reduced?
Better inventory management is key to reducing excess production. This would reduce the time needed to manage inventory. We could use these resources to do other productive tasks.
Kanban systems are one way to achieve this. A Kanbanboard is a visual tool that allows you to keep track of the work being done. In a Kanban system, work items move through a sequence of states until they reach their final destination. Each state is assigned a different priority.
For instance, when work moves from one stage to another, the current task is complete enough to be moved to the next stage. If a task is still in its beginning stages, it will continue to be so until it reaches the end.
This allows for work to continue moving forward, while also ensuring that there is no work left behind. A Kanban board allows managers to monitor how much work is being completed at any given moment. This information allows managers to adjust their workflow based off real-time data.
Lean manufacturing can also be used to reduce inventory levels. Lean manufacturing works to eliminate waste throughout every stage of the production chain. Anything that doesn't add value to the product is considered waste. These are some of the most common types.
-
Overproduction
-
Inventory
-
Packaging not required
-
Exceed materials
These ideas will help manufacturers increase efficiency and lower costs.
What are the responsibilities of a manufacturing manager
The manufacturing manager should ensure that every manufacturing process is efficient and effective. They should also be aware of any problems within the company and act accordingly.
They should also be able and comfortable communicating with other departments like sales and marketing.
They should also be aware of the latest trends in their industry and be able to use this information to help improve productivity and efficiency.
What do we need to know about Manufacturing Processes in order to learn more about Logistics?
No. You don't have to know about manufacturing processes before learning about logistics. Knowing about manufacturing processes will help you understand how logistics works.
What skills are required to be a production manager?
You must be flexible and organized to become a productive production planner. You must also be able to communicate effectively with clients and colleagues.
What kind of jobs are there in logistics?
There are many types of jobs in logistics. Here are some:
-
Warehouse workers - They load trucks and pallets.
-
Transportation drivers: They drive trucks and trailers and deliver goods and make pick-ups.
-
Freight handlers: They sort and package freight in warehouses.
-
Inventory managers: They are responsible for the inventory and management of warehouses.
-
Sales representatives - They sell products to customers.
-
Logistics coordinators are responsible for organizing and planning logistics operations.
-
Purchasing agents - They purchase goods and services needed for company operations.
-
Customer service representatives – They answer emails and phone calls from customers.
-
Shippers clerks - They process shipping order and issue bills.
-
Order fillers - These people fill orders based on what has been ordered.
-
Quality control inspectors – They inspect incoming and outgoing products to ensure that there are no defects.
-
Others - There is a variety of other jobs in logistics. These include transportation supervisors and cargo specialists.
What is the role and responsibility of a Production Planner?
Production planners ensure all aspects of the project are delivered within time and budget. They also ensure that the product/service meets the client’s needs.
Statistics
- You can multiply the result by 100 to get the total percent of monthly overhead. (investopedia.com)
- It's estimated that 10.8% of the U.S. GDP in 2020 was contributed to manufacturing. (investopedia.com)
- In 2021, an estimated 12.1 million Americans work in the manufacturing sector.6 (investopedia.com)
- Many factories witnessed a 30% increase in output due to the shift to electric motors. (en.wikipedia.org)
- (2:04) MTO is a production technique wherein products are customized according to customer specifications, and production only starts after an order is received. (oracle.com)
External Links
How To
How to Use lean manufacturing in the Production of Goods
Lean manufacturing is a management style that aims to increase efficiency and reduce waste through continuous improvement. It was developed in Japan between 1970 and 1980 by Taiichi Ohno. TPS founder Kanji Tyoda gave him the Toyota Production System, or TPS award. Michael L. Watkins published the "The Machine That Changed the World", the first book about lean manufacturing. It was published in 1990.
Lean manufacturing is often described as a set if principles that help improve the quality and speed of products and services. It emphasizes the elimination and minimization of waste in the value stream. Lean manufacturing is called just-in-time (JIT), zero defect, total productive maintenance (TPM), or 5S. Lean manufacturing seeks to eliminate non-value added activities, such as inspection, work, waiting, and rework.
In addition to improving product quality and reducing costs, lean manufacturing helps companies achieve their goals faster and reduces employee turnover. Lean manufacturing is a great way to manage the entire value chain including customers, suppliers, distributors and retailers as well as employees. Lean manufacturing practices are widespread in many industries. Toyota's philosophy, for example, is what has enabled it to be successful in electronics, automobiles, medical devices, healthcare and chemical engineering as well as paper and food.
Five fundamental principles underlie lean manufacturing.
-
Define Value - Determine the value that your business brings to society. Also, identify what sets you apart from your competitors.
-
Reduce Waste – Eliminate all activities that don't add value throughout the supply chain.
-
Create Flow - Make sure work runs smoothly without interruptions.
-
Standardize & simplify - Make processes consistent and repeatable.
-
Build Relationships- Develop personal relationships with both internal as well as external stakeholders.
Although lean manufacturing has always been around, it is gaining popularity in recent years because of a renewed interest for the economy after 2008's global financial crisis. Many companies have adopted lean manufacturing methods to increase their marketability. Many economists believe lean manufacturing will play a major role in economic recovery.
Lean manufacturing, which has many benefits, is now a standard practice in the automotive industry. These include better customer satisfaction and lower inventory levels. They also result in lower operating costs.
You can apply Lean Manufacturing to virtually any aspect of your organization. However, it is particularly useful when applied to the production side of an organization because it ensures that all steps in the value chain are efficient and effective.
There are three main types:
-
Just-in Time Manufacturing, (JIT): This kind of lean manufacturing is also commonly known as "pull-systems." JIT stands for a system where components are assembled on the spot rather than being made in advance. This approach reduces lead time, increases availability and reduces inventory.
-
Zero Defects Manufacturing (ZDM),: ZDM is a system that ensures no defective units are left the manufacturing facility. If a part is required to be repaired on the assembly line, it should not be scrapped. This is also true for finished products that require minor repairs before shipping.
-
Continuous Improvement (CI),: Continuous improvement aims improve the efficiency and effectiveness of operations by continuously identifying issues and making changes to reduce waste. It involves continuous improvement of processes, people, and tools.