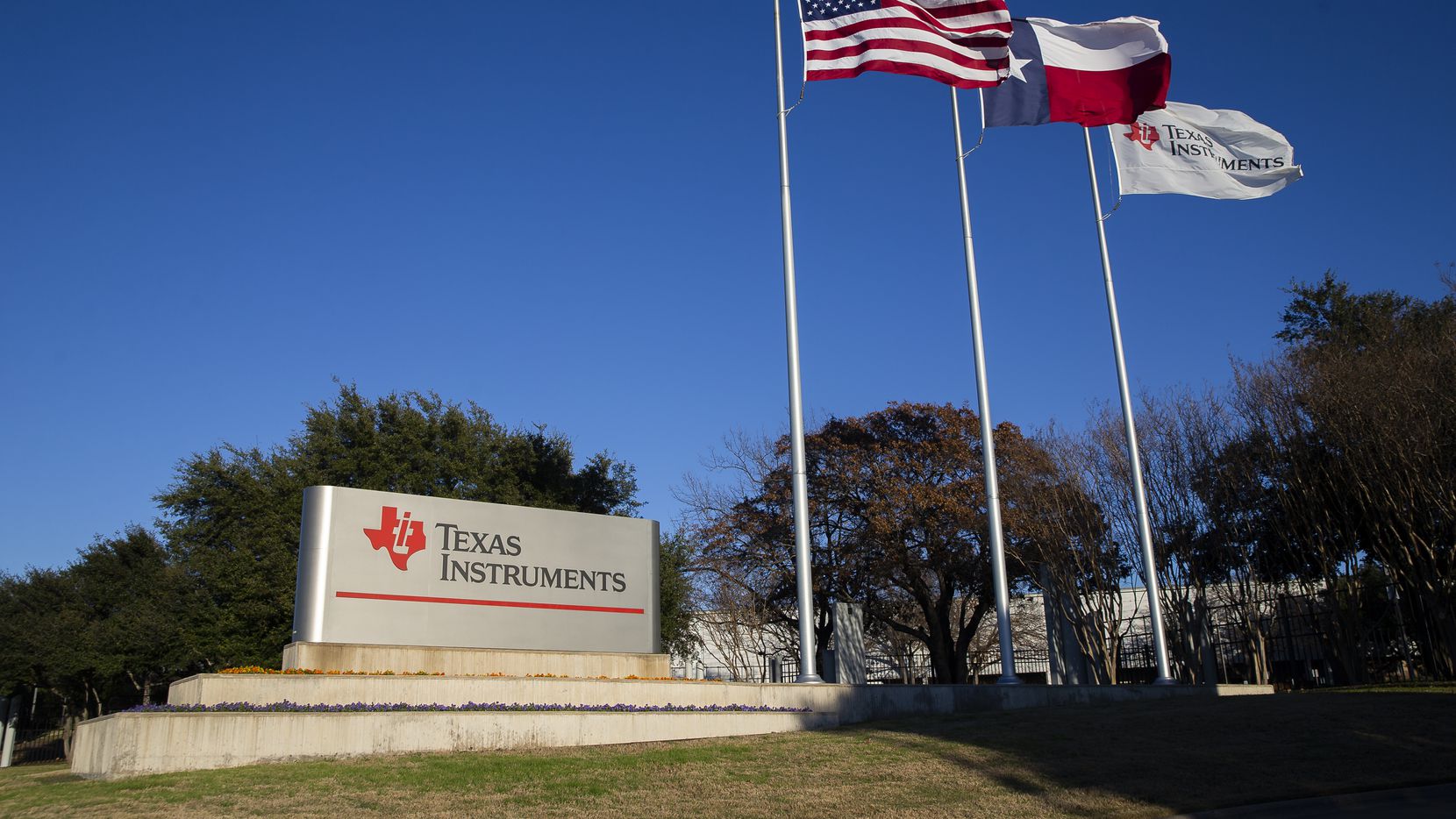
To transform your manufacturing process into an efficient machine, you must understand the five S's of Lean Manufacturing. They are Standardize, Straighten, Shine, and Sustain. These are the steps to follow. To maximize your lean transformation, you must train your frontline operators and team leaders.
Standardize
Clean and organize the workspace. This is the first step to the 5S process. This can be a one-time effort, but by standardizing the process, you can turn it into a routine. To make sure you have a consistent approach when performing 5S tasks, visual cues or checklist templates are all options.
These five ss's of Lean can help make your workplace more productive. This will encourage staff to be more organized and streamline their work. It will also help you improve the efficiency of your processes by ensuring a clean and organized work space. The five s's of lean are also helpful to improve the workplace's safety. An organized workspace can prevent accidents and reduce the chances of making mistakes. It will also increase productivity.
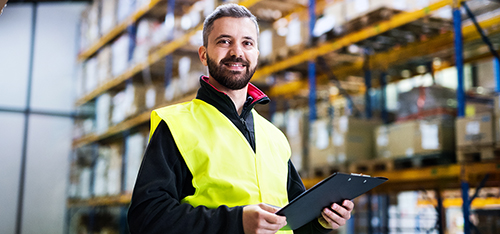
Straighten
Not having to do it all is necessary to achieve your 5 S's of Lean. Businesses can improve their business processes if they follow lean principles. For example, by organizing the components of an assembly line, workers will be able to find the components they need more easily. This can help to reduce time spent searching misplaced parts and improve company safety.
This will allow you to reduce the number items in each area. It will also help you save money on consumables. This means you can cut your office supply bill significantly. Straightening work cells can not only help you save money, but it will also improve your production processes and increase quality, safety, standard work, and efficiency.
Shine
Shine focuses on the inspection of the workspace and identifying any potential problems. Shine examines equipment and tools in order to improve flow. Shine helps workers identify potential problems before they hamper production. Shine can also be used to standardize a workspace to improve output.
Shine is one of the 5S tools used in lean manufacturing. This technique is designed to automate and streamline work processes, reduce waste, and increase efficiency. It can be applied to any industry, including manufacturing. It applies the 5S principles to all business. It allows companies to reduce inventory, work-in process, and supply stock.
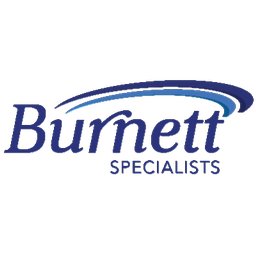
Sustain
The 5 s's are about introducing a standardized system to a facility in order to maintain the 5S. This is a process that is meant to be continuous and should be repeated often to ensure the facility works at its best. Employees should learn how to perform 5S audits.
The 5S approach emphasizes reducing waste, optimizing productivity, and keeping a clean, orderly workplace. Basically, it is a system for organizing workplaces that applies the five principles of the Toyota Production System. It was developed by Hiroyuki Hirano in post-war Japan as a means to improve efficiency in manufacturing facilities.
FAQ
What are the goods of logistics?
Logistics refers to all activities that involve moving goods from A to B.
They include all aspects associated with transport including packaging, loading transporting, unloading storage, warehousing inventory management customer service, distribution returns and recycling.
Logisticians ensure the product reaches its destination in the most efficient manner. Logisticians help companies improve their supply chain efficiency by providing information about demand forecasts and stock levels, production schedules, as well as availability of raw materials.
They coordinate with vendors and suppliers, keep track of shipments, monitor quality standards and perform inventory and order replenishment.
How can overproduction in manufacturing be reduced?
Better inventory management is key to reducing excess production. This would reduce time spent on activities such as purchasing, stocking, and maintaining excess stock. This would allow us to use our resources for more productive tasks.
This can be done by using a Kanban system. A Kanbanboard is a visual tool that allows you to keep track of the work being done. Kanban systems are where work items travel through a series of states until reaching their final destination. Each state is assigned a different priority.
When work is completed, it can be transferred to the next stage. But if a task remains in the beginning stages it will stay that way until it reaches its end.
This keeps work moving and ensures no work is lost. With a Kanban board, managers can see exactly how much work is being done at any given moment. This allows them the ability to adjust their workflow using real-time data.
Lean manufacturing is another way to manage inventory levels. Lean manufacturing seeks to eliminate waste from every step of the production cycle. Anything that doesn't add value to the product is considered waste. Some common types of waste include:
-
Overproduction
-
Inventory
-
Unnecessary packaging
-
Exceed materials
Manufacturers can increase efficiency and decrease costs by implementing these ideas.
How does a production planner differ from a project manager?
The major difference between a Production Planner and a Project Manager is that a Project Manager is often the person responsible for organizing and planning the entire project. While a Production Planner is involved mainly in the planning stage,
What are the 4 types manufacturing?
Manufacturing refers the process of turning raw materials into useful products with machines and processes. It can involve many activities like designing, manufacturing, testing packaging, shipping, selling and servicing.
Are there ways to automate parts of manufacturing?
Yes! Since ancient times, automation has been in existence. The wheel was invented by the Egyptians thousands of years ago. We now use robots to help us with assembly lines.
There are many applications for robotics in manufacturing today. These include:
-
Automated assembly line robots
-
Robot welding
-
Robot painting
-
Robotics inspection
-
Robots create products
Automation can be applied to manufacturing in many other ways. For example, 3D printing allows us to make custom products without having to wait for weeks or months to get them manufactured.
Statistics
- It's estimated that 10.8% of the U.S. GDP in 2020 was contributed to manufacturing. (investopedia.com)
- In the United States, for example, manufacturing makes up 15% of the economic output. (twi-global.com)
- You can multiply the result by 100 to get the total percent of monthly overhead. (investopedia.com)
- According to the United Nations Industrial Development Organization (UNIDO), China is the top manufacturer worldwide by 2019 output, producing 28.7% of the total global manufacturing output, followed by the United States, Japan, Germany, and India.[52][53] (en.wikipedia.org)
- In 2021, an estimated 12.1 million Americans work in the manufacturing sector.6 (investopedia.com)
External Links
How To
How to use Lean Manufacturing in the production of goods
Lean manufacturing is a management style that aims to increase efficiency and reduce waste through continuous improvement. It was developed by Taiichi Okono in Japan, during the 1970s & 1980s. TPS founder Kanji Takoda awarded him the Toyota Production System Award (TPS). Michael L. Watkins published the "The Machine That Changed the World", the first book about lean manufacturing. It was published in 1990.
Lean manufacturing is often defined as a set of principles used to improve the quality, speed, and cost of products and services. It emphasizes eliminating waste and defects throughout the value stream. Just-in-time (JIT), zero defect (TPM), and 5S are all examples of lean manufacturing. Lean manufacturing seeks to eliminate non-value added activities, such as inspection, work, waiting, and rework.
Lean manufacturing is a way for companies to achieve their goals faster, improve product quality, and lower costs. Lean manufacturing has been deemed one of the best ways to manage the entire value-chain, including customers, distributors as well retailers and employees. Lean manufacturing practices are widespread in many industries. Toyota's philosophy, for example, is what has enabled it to be successful in electronics, automobiles, medical devices, healthcare and chemical engineering as well as paper and food.
Lean manufacturing includes five basic principles:
-
Define Value: Identify the social value of your business and what sets you apart.
-
Reduce waste - Stop any activity that isn't adding value to the supply chains.
-
Create Flow – Ensure that work flows smoothly throughout the process.
-
Standardize and Simplify – Make processes as consistent, repeatable, and as simple as possible.
-
Build Relationships - Establish personal relationships with both internal and external stakeholders.
Although lean manufacturing has always been around, it is gaining popularity in recent years because of a renewed interest for the economy after 2008's global financial crisis. Many companies have adopted lean manufacturing methods to increase their marketability. In fact, some economists believe that lean manufacturing will be an important factor in economic recovery.
Lean manufacturing has many benefits in the automotive sector. These include improved customer satisfaction, reduced inventory levels, lower operating costs, increased productivity, and better overall safety.
Lean manufacturing can be applied to almost every aspect of an organization. Because it makes sure that all value chains are efficient and effectively managed, Lean Manufacturing is particularly helpful for organizations.
There are three types principally of lean manufacturing:
-
Just-in-Time Manufacturing: Also known as "pull systems", this type of lean manufacturing uses just-in-time manufacturing (JIT). JIT means that components are assembled at the time of use and not manufactured in advance. This approach is designed to reduce lead times and increase the availability of components. It also reduces inventory.
-
Zero Defects Manufacturing (ZDM),: ZDM is a system that ensures no defective units are left the manufacturing facility. If a part is required to be repaired on the assembly line, it should not be scrapped. This also applies to finished products that need minor repairs before being shipped.
-
Continuous Improvement: Continuous Improvement aims to improve efficiency by continually identifying problems and making adjustments to eliminate or minimize waste. Continuous Improvement (CI) involves continuous improvement in processes, people, tools, and infrastructure.