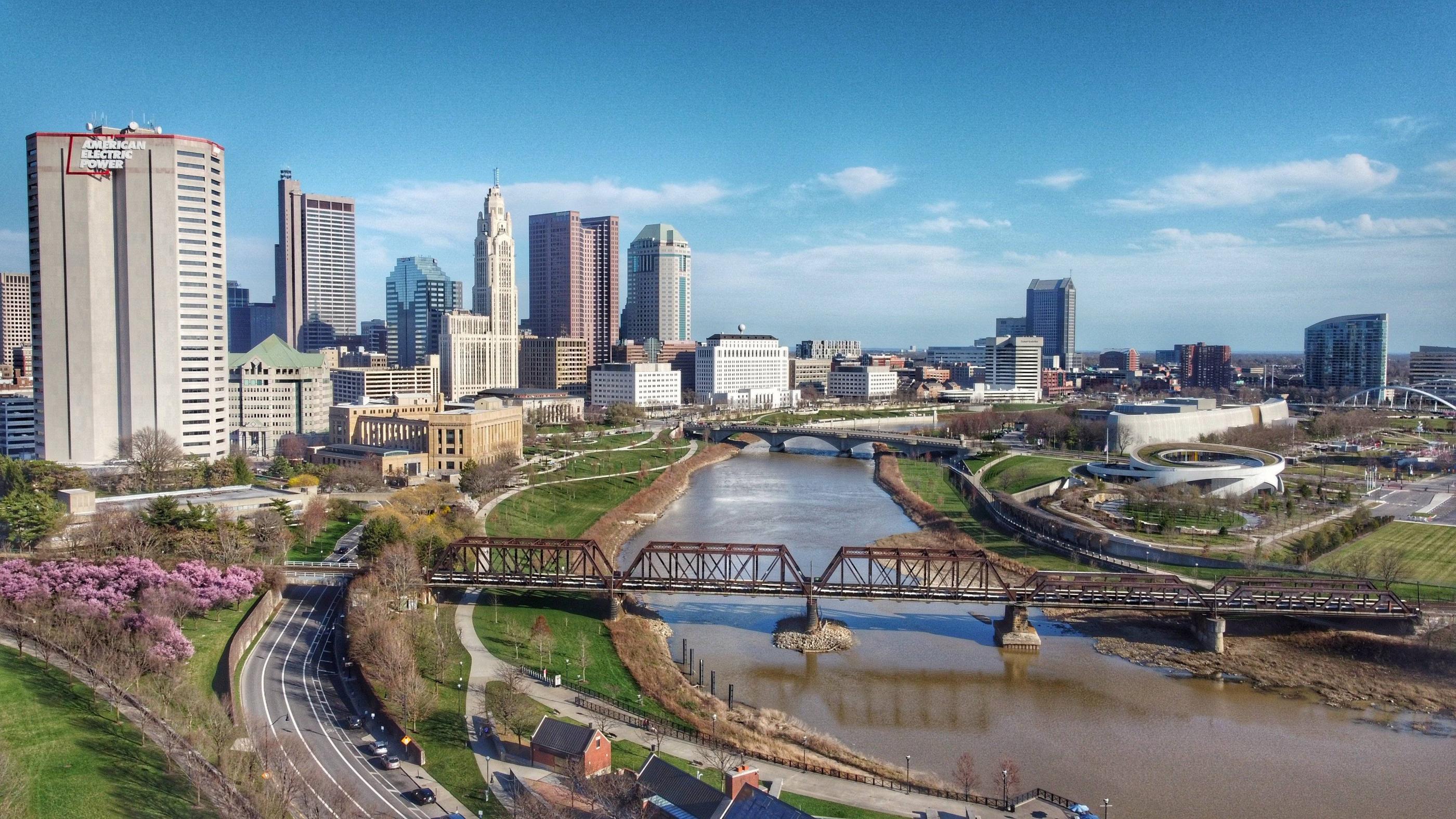
Drawing is a skill that requires a great deal of technical knowledge. They also need to be able to work with other people to help produce the best results. They might also need to be able to read and use specific software programs. They may also need to learn engineering formulas to calculate measurements.
Drawing professionals are often employed by engineering or architectural firms. They create plans for buildings, structures, and other products using computer-aided design (CAD) software. They often work on their own projects but also collaborate with others to create innovative designs. They often work full-time, but they also can take on a variety of jobs. They may have to work overtime depending on their company.
An associate's degree is typically earned by drafting professionals from a community or technical college. Then, they can continue their education by enrolling in a 4-year university program. Depending on the course they take, they may be able to transfer their degree to a bachelor's degree.
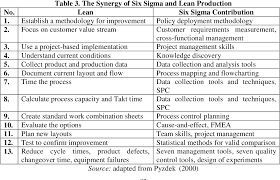
In addition to a drafting degree, drafters may also need to have professional experience. A firm may ask them to do an internship to gain practical experience. This can be a great way to land a job as a drafter. A portfolio may be requested to show their drafting skills.
You can also become a certified drafter. American Design Drafting Association has certification exams that measure drafting skills. These exams test the ability to understand and use geometric designs. Many certifications can be renewed every three years. The ADDA allows you to be certified in many areas of drafting.
Drafters typically work for construction, engineering, and manufacturing companies. They might also be employed in factories or with electricity. Although they might work on a schedule, some drafters may work for more than 40 hours per week. They should also know how to manage their time and use computer-aided design (CAD).
Drafters can benefit from a growing trend in which more businesses use technology to increase efficiency. To stay competitive, they may need to learn CAD and other programming languages. Those who are interested in becoming a drafter may want to consider earning a master's degree. A master's degree will give you an advantage over other applicants when it comes time to get hired. They are also more qualified to provide technical information to clients.
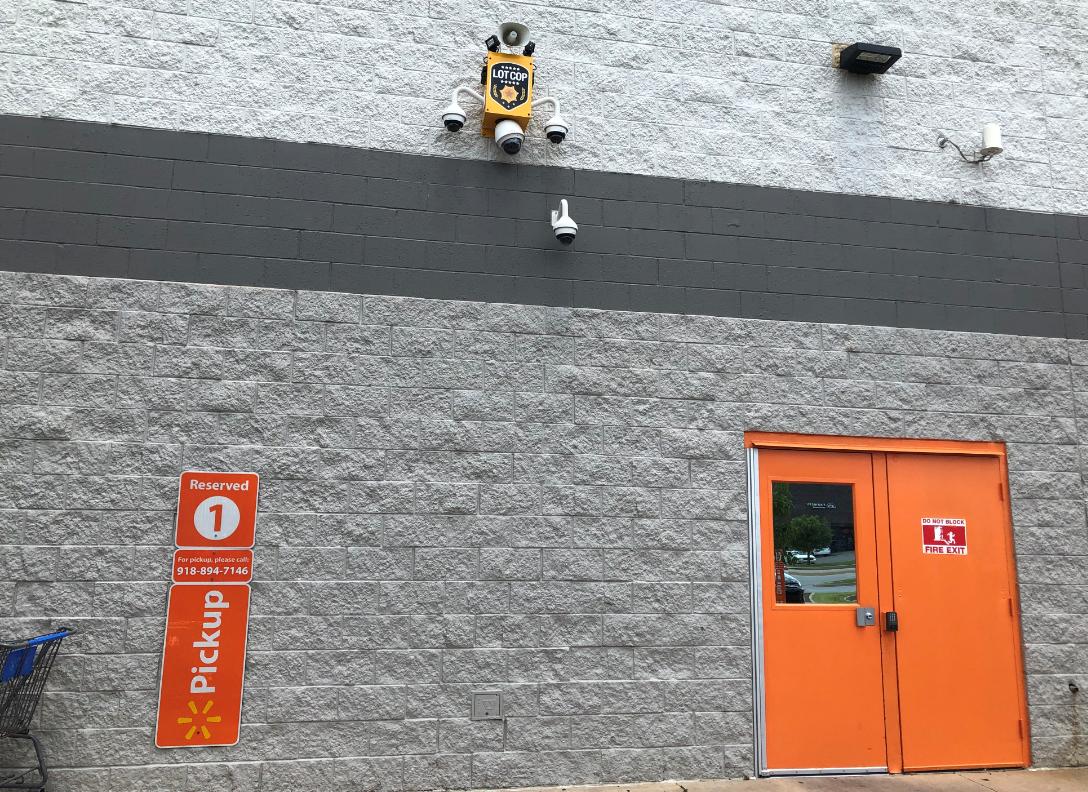
Drafters can also work as assistants to professional drafters. Volunteers may be available to help out with community projects. If you are interested in becoming a drafter, you should determine what type of project you are interested in before enrolling in classes. Some clients prefer drawing in pencil while others prefer drawings that are computer-generated.
After graduating from high school, draft technicians can gain professional experience by enrolling in drafting classes at a technical institute. They should also pay special attention to math and computer classes.
FAQ
What is the distinction between Production Planning or Scheduling?
Production Planning (PP) is the process of determining what needs to be produced at any given point in time. Forecasting and identifying production capacity are two key elements to this process.
Scheduling is the process that assigns dates to tasks so they can get completed within a given timeframe.
How is a production manager different from a producer planner?
The primary difference between a producer planner and a manager of a project is that the manager usually plans and organizes the whole project, while a production planner is only involved in the planning stage.
What type of jobs is there in logistics
There are many kinds of jobs available within logistics. Some examples are:
-
Warehouse workers – They load and unload pallets and trucks.
-
Transport drivers - These are people who drive trucks and trailers to transport goods or perform pick-ups.
-
Freight handlers: They sort and package freight in warehouses.
-
Inventory managers – They manage the inventory in warehouses.
-
Sales reps are people who sell products to customers.
-
Logistics coordinators: They plan and manage logistics operations.
-
Purchasing agents: They are responsible for purchasing goods and services to support company operations.
-
Customer service representatives - Answer calls and email from customers.
-
Shippers clerks - They process shipping order and issue bills.
-
Order fillers: They fill orders based off what has been ordered and shipped.
-
Quality control inspectors – They inspect incoming and outgoing products to ensure that there are no defects.
-
Others - There are many types of jobs in logistics such as transport supervisors and cargo specialists.
What are manufacturing & logistics?
Manufacturing is the process of creating goods from raw materials by using machines and processes. Logistics encompasses the management of all aspects associated with supply chain activities such as procurement, production planning, distribution and inventory control. It also includes customer service. Manufacturing and logistics can often be grouped together to describe a larger term that covers both the creation of products, and the delivery of them to customers.
How does manufacturing avoid bottlenecks in production?
Avoiding production bottlenecks is as simple as keeping all processes running smoothly, from the time an order is received until the product ships.
This includes planning to meet capacity requirements and quality control.
The best way to do this is to use continuous improvement techniques such as Six Sigma.
Six Sigma can be used to improve the quality and decrease waste in all areas of your company.
It's all about eliminating variation and creating consistency in work.
Statistics
- According to a Statista study, U.S. businesses spent $1.63 trillion on logistics in 2019, moving goods from origin to end user through various supply chain network segments. (netsuite.com)
- It's estimated that 10.8% of the U.S. GDP in 2020 was contributed to manufacturing. (investopedia.com)
- Many factories witnessed a 30% increase in output due to the shift to electric motors. (en.wikipedia.org)
- [54][55] These are the top 50 countries by the total value of manufacturing output in US dollars for its noted year according to World Bank.[56] (en.wikipedia.org)
- Job #1 is delivering the ordered product according to specifications: color, size, brand, and quantity. (netsuite.com)
External Links
How To
How to use 5S to increase Productivity in Manufacturing
5S stands to stand for "Sort", “Set In Order", “Standardize", and "Store". Toyota Motor Corporation invented the 5S strategy in 1954. This methodology helps companies improve their work environment to increase efficiency.
This method has the basic goal of standardizing production processes to make them repeatable. It means tasks like cleaning, sorting or packing, labeling, and storing are done every day. Workers can be more productive by knowing what to expect.
Five steps are required to implement 5S: Sort, Set In Order, Standardize. Separate. Each step is a different action that leads to greater efficiency. Sorting things makes it easier to find them later. When items are ordered, they are put together. Then, after you separate your inventory into groups, you store those groups in containers that are easy to access. Finally, label all containers correctly.
Employees must be able to critically examine their work practices. Employees need to be able understand their motivations and discover alternative ways to do them. They must learn new skills and techniques in order to implement the 5S system.
In addition to improving efficiency, the 5S system also increases morale and teamwork among employees. They will feel motivated to strive for higher levels of efficiency once they start to see results.