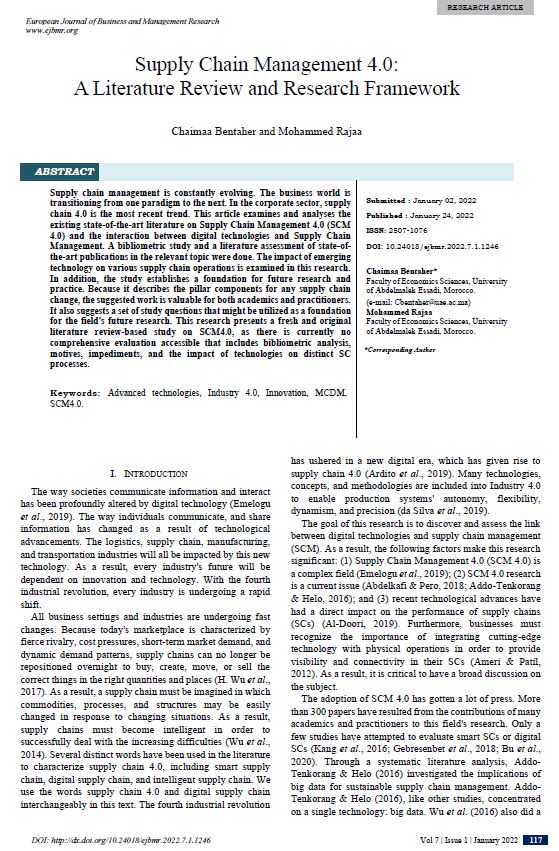
Japanese factories produce highquality products at low cost. They are the backbone and 5% of the GDP of Japan. However, they have struggled to cope with tighter standards as well growing competition and the rising cost pressures caused by the recent recession.
Last year, for example, a white paper by the government found that Japanese companies weren't prepared to cope with a reduction in parts procurement. The recession took a toll on Japan's auto industry. Traditionally, the car manufacturing industry relies on 30,000 different parts, so a disruption to the supply chain can stop production. Some parts don't have substitutes.
In order to keep the quality of their products high, Japanese manufacturers are working closely with suppliers to solve problems and improve efficiency. They welcome input from workers, salesmen, as well as quality inspectors.
Japanese manufacturers are concerned about the high number of accidents on the factory floor. There have been numerous safety scandals in the country's industrial sector. This has led to greater scrutiny of the standard of work in factories.
Another issue that has been negatively affecting production of Japanese goods has been the influx non-regular workforce. Non-regular workers allow companies to reduce labor costs, but they increase the risk of accidents and de-skill the production floor. Companies have begun to focus on training their regular workers to become better, safer workers.
Japan's shrinking birthrate is responsible for the growing labor force shortage. Companies complaining about a shortage of labor are at an all-time high of 25 years. Japanese companies will face further challenges if their labor force shrinks.
A large number of factories are cutting costs despite the lack of skilled workers. A growing number "factries" have fewer than 10 employees. Many of these small workshops create the finest equipment in the entire world.
The Japanese manufacturing sector is facing increasing competition from countries such as China and South Korea. Many factories are trying reduce costs and increase productivity. The Japanese government has warned, however, that the industry may lose its competitive edge overseas.
Japan faces increasing competition from Asia, as well as overseas. This raises questions about its ability to adjust its processes and adapt quickly enough. The demand for skilled workers will rise even if Japan can adapt its processes to meet the increased competition from Asia and abroad.
Japanese factories are a significant source of components to the global market. They also provide advanced materials such as silicon chips that are used in smart phones and computers. Although Chinese factories are skilled in low-cost assembly, the Japanese supply essential components.
The Japanese are now facing increased competition from foreigners, despite their efforts to improve their productivity. They have had to reduce their costs due to the fact that their products are less valuable in the domestic market. Despite these challenges the Japanese have managed to maintain a high level production standard.
FAQ
Why automate your factory?
Automation has become increasingly important in modern warehousing. The rise of e-commerce has led to increased demand for faster delivery times and more efficient processes.
Warehouses must adapt quickly to meet changing customer needs. Technology is essential for warehouses to be able to adapt quickly to changing needs. Automating warehouses is a great way to save money. Here are some benefits of investing in automation
-
Increases throughput/productivity
-
Reduces errors
-
Increases accuracy
-
Safety increases
-
Eliminates bottlenecks
-
Companies can scale up more easily
-
Makes workers more efficient
-
It gives visibility to everything that happens inside the warehouse
-
Enhances customer experience
-
Improves employee satisfaction
-
Reduces downtime and improves uptime
-
Ensures quality products are delivered on time
-
Eliminates human error
-
Assure compliance with regulations
What do you mean by warehouse?
Warehouses and storage facilities are where goods are kept before being sold. It can be indoors or out. In some cases, it may be a combination of both.
Are there any Manufacturing Processes that we should know before we can learn about Logistics?
No. No. Knowing about manufacturing processes will help you understand how logistics works.
Statistics
- According to a Statista study, U.S. businesses spent $1.63 trillion on logistics in 2019, moving goods from origin to end user through various supply chain network segments. (netsuite.com)
- In 2021, an estimated 12.1 million Americans work in the manufacturing sector.6 (investopedia.com)
- [54][55] These are the top 50 countries by the total value of manufacturing output in US dollars for its noted year according to World Bank.[56] (en.wikipedia.org)
- It's estimated that 10.8% of the U.S. GDP in 2020 was contributed to manufacturing. (investopedia.com)
- (2:04) MTO is a production technique wherein products are customized according to customer specifications, and production only starts after an order is received. (oracle.com)
External Links
How To
Six Sigma and Manufacturing
Six Sigma refers to "the application and control of statistical processes (SPC) techniques in order to achieve continuous improvement." Motorola's Quality Improvement Department, Tokyo, Japan, developed it in 1986. Six Sigma's main goal is to improve process quality by standardizing processes and eliminating defects. Since there are no perfect products, or services, this approach has been adopted by many companies over the years. The main goal of Six Sigma is to reduce variation from the mean value of production. If you take a sample and compare it with the average, you will be able to determine how much of the production process is different from the norm. If this deviation is too big, you know something needs fixing.
Understanding the dynamics of variability within your business is the first step in Six Sigma. Once you have this understanding, you will need to identify sources and causes of variation. These variations can also be classified as random or systematic. Random variations occur when people do mistakes. Symmetrical variations are caused due to factors beyond the process. Random variations would include, for example, the failure of some widgets to fall from the assembly line. If however, you notice that each time you assemble a widget it falls apart in exactly the same spot, that is a problem.
After identifying the problem areas, you will need to devise solutions. You might need to change the way you work or completely redesign the process. To verify that the changes have worked, you need to test them again. If they don’t work, you’ll need to go back and rework the plan.