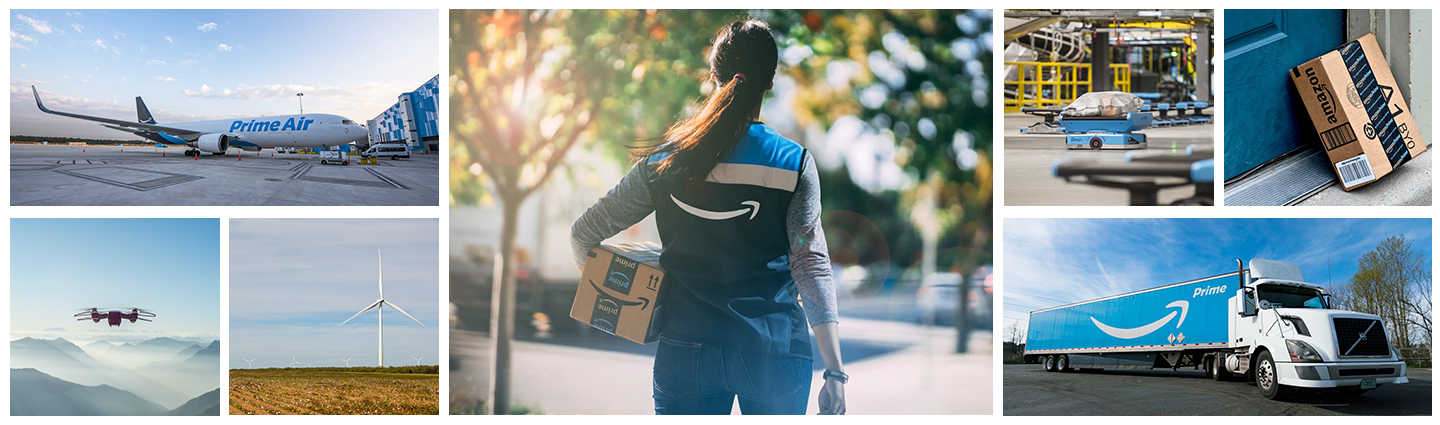
Are you looking for New Jersey logistics jobs? Whether you want to be a manager or just run your own business, these jobs are available in all types of settings and require various skills. A bachelor's degree is preferable. You will need the following qualifications to work as a logistic manager. These skills include the ability solve problems and work independently. Positive attitude and natural problem solver are essential.
a bachelor's degree is required
To be eligible for jobs in logistics, you need a Bachelor’s degree from an accredited college, plus 4+ years relevant experience. You also need proven time-management and organizational skills. Additionally, you will need to have excellent communication skills and fluency in English. In addition, you should have an aptitude for data analysis, proven leadership abilities, and excellent interpersonal skills.
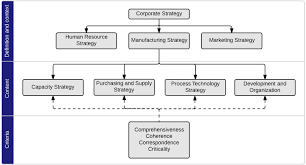
Many of these positions require a Bachelor's Degree in Logistics in New Jersey. Although most jobs in this industry are low-skilled, you can still make a lot by applying your skills to other industries. New Jersey has many middle skill jobs that require workers with specialized training. One of these middle-skill programs is available at NJCU's Center for Workforce and Community Development.
Employers will often consider work experience in logistics over a college degree. Prior experience can make you more marketable and increase your chances of getting hired. If you have a bachelor’s degree in logistics, it is possible to work as a courier or customer service representative. You can get promoted to management positions in logistics if you have experience and other qualifications. Moreover, you can also pursue higher education in logistics, such as postsecondary teaching or research.
It is preferable to have a bachelor’s degree
Several logistics positions require a bachelor's degree, and a bachelor's degree in a related field is often preferred. Employers prefer applicants who have a bachelor's degree to be able to manage complex supply chains and transport laws. Additionally, students who have completed a bachelor’s degree in logistics are able to gain a broad perspective on the field, which will help them expand their professional networks. A customer service representative or freight agent could be an entry-level position in logistics. Management positions might become available if you have the right qualifications and training. Other options for higher-level logistics positions include research, postsecondary teaching, and consulting.
Employers prefer to have a bachelor's level in logistics. But, associates can also be accepted. Relevant work experience could be used in some cases to replace education. Job seekers can also get certifications in specific industry fields, such as data analysis or warehouse management. A bachelor's degree in logistics is preferred in New Jersey. A bachelor's level in logistics will enable you to fully understand the supply chain. Many companies require a bachelor's degree, particularly if they handle large-scale transactions.

An Industrial Engineer career requires a bachelor's Degree and some experience in manufacturing or in industrial facilities. Moreover, you must have knowledge of municipal coding rules and must be able to effectively communicate with employees. An Industrial Engineer should have at least six years of relevant work experience and be familiar with the working conditions in industries that are similar to the ones you are applying for.
FAQ
How can we improve manufacturing efficiency?
The first step is to identify the most important factors affecting production time. We then need to figure out how to improve these variables. You can start by identifying the most important factors that impact production time. Once you've identified them, try to find solutions for each of those factors.
What jobs are available in logistics?
There are many kinds of jobs available within logistics. Some examples are:
-
Warehouse workers – They load and unload pallets and trucks.
-
Transport drivers - These are people who drive trucks and trailers to transport goods or perform pick-ups.
-
Freight handlers are people who sort and pack freight into warehouses.
-
Inventory managers - They oversee the inventory of goods in warehouses.
-
Sales representatives: They sell products to customers.
-
Logistics coordinators: They plan and manage logistics operations.
-
Purchasing agents: They are responsible for purchasing goods and services to support company operations.
-
Customer service agents - They answer phone calls and respond to emails.
-
Shipping clerks – They process shipping orders, and issue bills.
-
Order fillers: They fill orders based off what has been ordered and shipped.
-
Quality control inspectors – They inspect incoming and outgoing products to ensure that there are no defects.
-
Others - There are many other types of jobs available in logistics, such as transportation supervisors, cargo specialists, etc.
What are the 7 Rs of logistics management?
The acronym 7Rs of Logistics refers to the seven core principles of logistics management. It was published in 2004 by the International Association of Business Logisticians as part of their "Seven Principles of Logistics Management" series.
The acronym consists of the following letters:
-
Responsible - ensure that all actions taken are within legal requirements and are not harmful to others.
-
Reliable - have confidence in the ability to deliver on commitments made.
-
Be responsible - Use resources efficiently and avoid wasting them.
-
Realistic – Consider all aspects, including cost-effectiveness as well as environmental impact.
-
Respectful - Treat people fairly and equitably
-
Be resourceful: Look for opportunities to save money or increase productivity.
-
Recognizable: Provide customers with value-added service
Statistics
- According to a Statista study, U.S. businesses spent $1.63 trillion on logistics in 2019, moving goods from origin to end user through various supply chain network segments. (netsuite.com)
- Many factories witnessed a 30% increase in output due to the shift to electric motors. (en.wikipedia.org)
- Job #1 is delivering the ordered product according to specifications: color, size, brand, and quantity. (netsuite.com)
- In 2021, an estimated 12.1 million Americans work in the manufacturing sector.6 (investopedia.com)
- [54][55] These are the top 50 countries by the total value of manufacturing output in US dollars for its noted year according to World Bank.[56] (en.wikipedia.org)
External Links
How To
How to Use Lean Manufacturing in the Production of Goods
Lean manufacturing refers to a method of managing that seeks to improve efficiency and decrease waste. It was first developed in Japan in the 1970s/80s by Taiichi Ahno, who was awarded the Toyota Production System (TPS), award from KanjiToyoda, the founder of TPS. Michael L. Watkins published the "The Machine That Changed the World", the first book about lean manufacturing. It was published in 1990.
Lean manufacturing is often described as a set if principles that help improve the quality and speed of products and services. It emphasizes reducing defects and eliminating waste throughout the value chain. Lean manufacturing is called just-in-time (JIT), zero defect, total productive maintenance (TPM), or 5S. Lean manufacturing seeks to eliminate non-value added activities, such as inspection, work, waiting, and rework.
Lean manufacturing not only improves product quality but also reduces costs. Companies can also achieve their goals faster by reducing employee turnover. Lean manufacturing has been deemed one of the best ways to manage the entire value-chain, including customers, distributors as well retailers and employees. Lean manufacturing is widely used in many industries. Toyota's philosophy, for example, is what has enabled it to be successful in electronics, automobiles, medical devices, healthcare and chemical engineering as well as paper and food.
Five principles are the basis of lean manufacturing:
-
Define Value: Identify the social value of your business and what sets you apart.
-
Reduce waste - Stop any activity that isn't adding value to the supply chains.
-
Create Flow - Ensure work moves smoothly through the process without interruption.
-
Standardize and simplify – Make processes as repeatable and consistent as possible.
-
Build Relationships - Establish personal relationships with both internal and external stakeholders.
Lean manufacturing is not a new concept, but it has been gaining popularity over the last few years due to a renewed interest in the economy following the global financial crisis of 2008. Many companies have adopted lean manufacturing methods to increase their marketability. Some economists even believe that lean manufacturing can be a key factor in economic recovery.
Lean manufacturing, which has many benefits, is now a standard practice in the automotive industry. These include higher customer satisfaction, lower inventory levels, lower operating expenses, greater productivity, and improved overall safety.
Lean manufacturing can be applied to almost every aspect of an organization. However, it is particularly useful when applied to the production side of an organization because it ensures that all steps in the value chain are efficient and effective.
There are three types of lean manufacturing.
-
Just-in Time Manufacturing (JIT), also known as "pull system": This form of lean manufacturing is often referred to simply as "pull". JIT stands for a system where components are assembled on the spot rather than being made in advance. This approach is designed to reduce lead times and increase the availability of components. It also reduces inventory.
-
Zero Defects Manufacturing, (ZDM): ZDM is focused on ensuring that no defective products leave the manufacturing facility. If a part is required to be repaired on the assembly line, it should not be scrapped. This also applies to finished products that need minor repairs before being shipped.
-
Continuous Improvement (CI), also known as Continuous Improvement, aims at improving the efficiency of operations through continuous identification and improvement to minimize or eliminate waste. Continuous Improvement (CI) involves continuous improvement in processes, people, tools, and infrastructure.