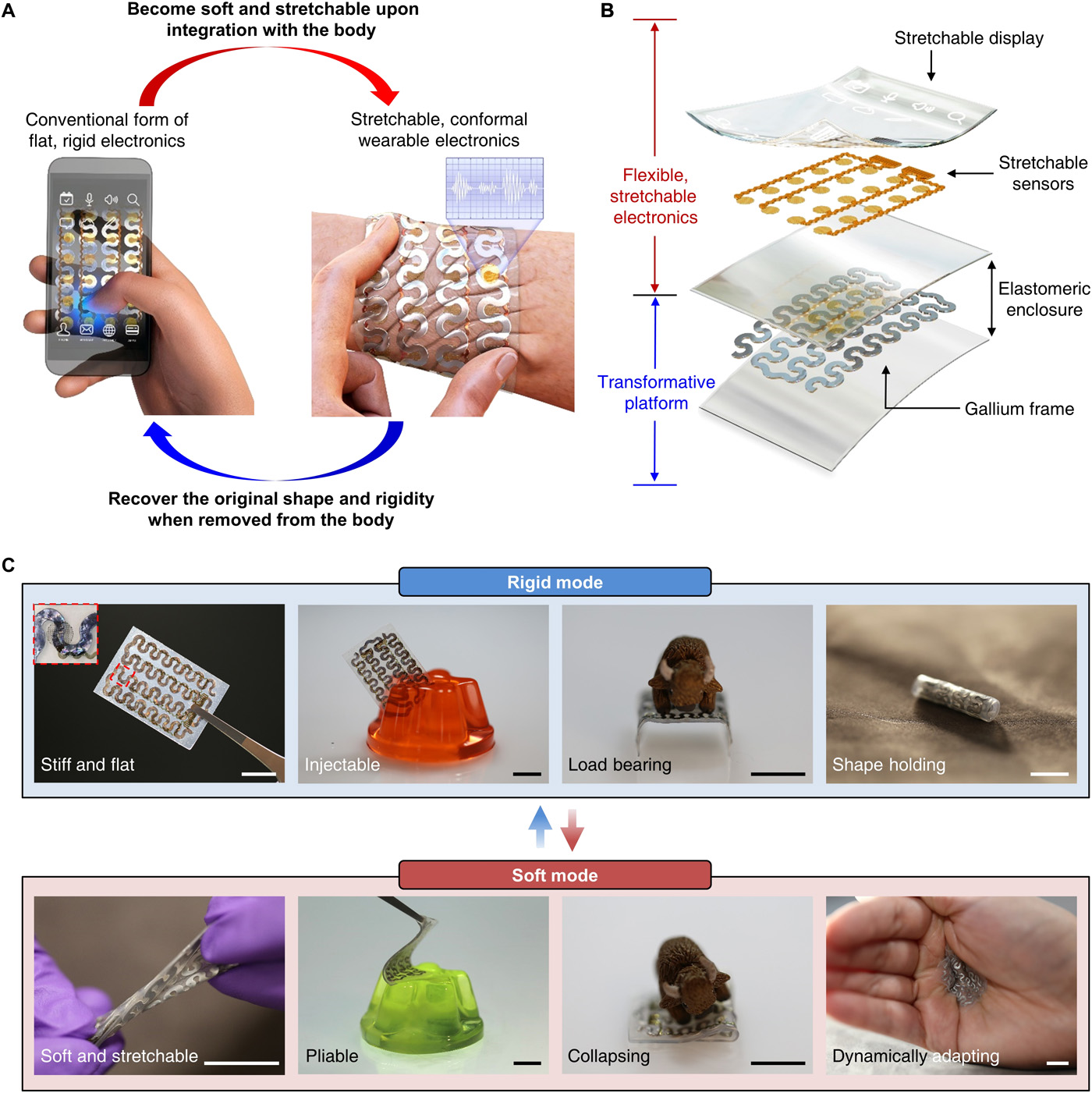
The highest salaries for biochemists are $84,365. These professionals do research on drugs and how they effect organisms. They also develop new chemical compounds and formulations. They could work in a company, or be a professor at a college.
Biochemists have different education requirements depending on their job. Most employers require candidates to have an advanced degree. Some companies only require a bachelor's degree. For positions in biophysics (the study of biological phenomena and physical laws), a master's degree is sometimes required.
Biochemists are responsible for developing new chemical compounds and formulas. They also establish quality control procedures. Biochemists often collaborate with biophysicists. They study the relationship between physical laws, biological phenomena, and how they relate to each other. They may also be partnered with chemical biologists. These scientists are responsible for developing medicinal chemistry strategies and preparing samples.
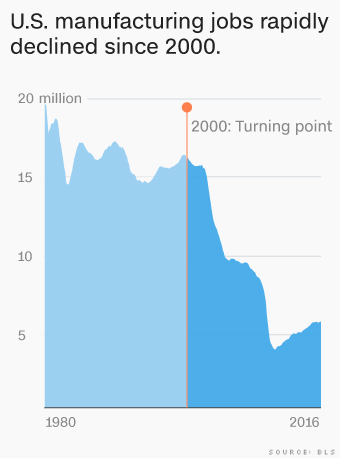
Biochemists might work in the manufacturing or pharmaceutical industries. Pfizer, GlaxoSmithkline and Amgen are some of the most prominent employers. These companies are known for their high-paying jobs, but it is not easy to find a job. Genentech is another company that can be difficult to get a job, even though their salaries are similar. Eurofins has 10 open biochemist positions. Siemens Healthineers has 10.
A biochemist might also work as an instructor at a college. These professionals can teach students about the biology and evolution of other organisms. They may also play a role in environmental restoration. They might be able to develop new chemical substances or formulations that address environmental problems. Biochemists can also examine the effects of drugs and hormones on organisms.
Many biochemists promote the study biochemistry. Advocates could be awarded degrees from Western Illinois University or Kean University. They may also have internships at research labs. These internships can help students build contacts in the field and gain hands-on experience. They can later apply for roles as a research associate or lecturer.
Biochemists typically earn a bachelor's degree and a doctorate. These degrees are necessary for entry-level biochemistry positions. A license may be required for biochemists who have not attended college. Some jobs require you to have contact with patients. A license is also required for some medical assistant positions. These positions may be on a small team, but may have room for advancement.
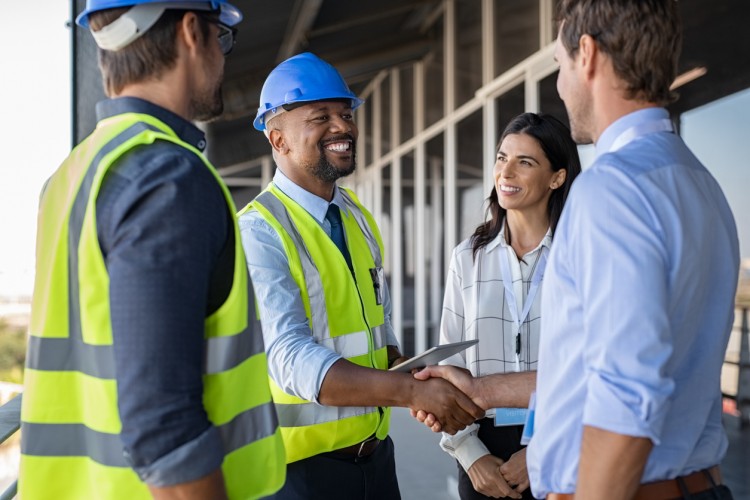
There are many salaries for biochemists. The median annual salary of biochemists is $76,806 while the average salary is $95,998 Biochemists have a salary that is expected rise by 2020. Pfizer is one of the biggest employers in the health-care industry. Eurofins, Amgen and Amgen all pay their employees high salaries. GlaxoSmithkline and Siemens Healthineers also offer salaries for biochemists that are comparable to other professionals.
In pharma companies, biochemists can work as chemical biologists. These professionals analyze samples and create reports. They also supervise lab operations. They must have strong experimental skills to be able prepare samples and present findings for stakeholders.
FAQ
How important is automation in manufacturing?
Not only are service providers and manufacturers important, but so is automation. It allows them to offer services faster and more efficiently. It reduces human errors and improves productivity, which in turn helps them lower their costs.
What is production planning?
Production Planning is the creation of a plan to cover all aspects, such as scheduling, budgeting. Location, crew, equipment, props and other details. This document will ensure everything is in order and ready to go when you need it. It should also contain information on achieving the best results on set. This includes location information, crew details, equipment specifications, and casting lists.
First, you need to plan what you want to film. You may have decided where to shoot or even specific locations you want to use. Once you've identified the locations and scenes you want to use, you can begin to plan what elements you need for each scene. For example, you might decide that you need a car but don't know exactly what model you want. In this case, you could start looking up cars online to find out what models are available and then narrow your choices by choosing between different makes and models.
After you have selected the car you want, you can begin to think about additional features. Do you need people sitting in the front seats? Or perhaps you need someone walking around the back of the car? Maybe you want to change the interior color from black to white? These questions will help guide you in determining the ideal look and feel for your car. Also, think about what kind of shots you would like to capture. Will you be filming close-ups or wide angles? Maybe you want the engine or the steering wheels to be shown. These factors will help you determine which car style you want to film.
Once you have made all the necessary decisions, you can start to create a schedule. You can use a schedule to determine when and where you need it to be shot. The schedule will show you when to get there, what time to leave, and when to return home. Everyone knows exactly what they should do and when. Hire extra staff by booking them ahead of time. You should not hire anyone who doesn't show up because of your inaction.
It is important to calculate the amount of filming days when you are creating your schedule. Some projects only take one or two days, while others may last weeks. When creating your schedule, be aware of whether you need more shots per day. Multiple takes of the same location will lead to higher costs and take more time. It is better to be cautious and take fewer shots than you risk losing money if you are not sure if multiple takes are necessary.
Budgeting is another important aspect of production planning. Setting a realistic budget is essential as it will allow you to work within your means. It is possible to reduce the budget at any time if you experience unexpected problems. However, you shouldn't overestimate the amount of money you will spend. You'll end up with less money after paying for other things if the cost is underestimated.
Production planning can be a complex process. However, once you know how everything works together it will become easier to plan future projects.
How can overproduction in manufacturing be reduced?
Better inventory management is key to reducing excess production. This would reduce the time needed to manage inventory. This will allow us to free up resources for more productive tasks.
You can do this by adopting a Kanban method. A Kanbanboard is a visual tool that allows you to keep track of the work being done. Kanban systems are where work items travel through a series of states until reaching their final destination. Each state has a different priority level.
To illustrate, work can move from one stage or another when it is complete enough for it to be moved to a new stage. But if a task remains in the beginning stages it will stay that way until it reaches its end.
This helps to keep work moving forward while ensuring that no work is left behind. With a Kanban board, managers can see exactly how much work is being done at any given moment. This data allows them adjust their workflow based upon real-time data.
Another way to control inventory levels is to implement lean manufacturing. Lean manufacturing is about eliminating waste from all stages of the production process. Anything that does nothing to add value to a product is waste. Here are some examples of common types.
-
Overproduction
-
Inventory
-
Unnecessary packaging
-
Overstock materials
Manufacturers can increase efficiency and decrease costs by implementing these ideas.
What does "warehouse" mean?
Warehouses and storage facilities are where goods are kept before being sold. You can have it indoors or outdoors. It may also be an indoor space or an outdoor area.
What is the distinction between Production Planning or Scheduling?
Production Planning (PP), is the process of deciding what production needs to take place at any given time. This is accomplished by forecasting the demand and identifying production resources.
Scheduling is the process that assigns dates to tasks so they can get completed within a given timeframe.
Statistics
- In 2021, an estimated 12.1 million Americans work in the manufacturing sector.6 (investopedia.com)
- In the United States, for example, manufacturing makes up 15% of the economic output. (twi-global.com)
- You can multiply the result by 100 to get the total percent of monthly overhead. (investopedia.com)
- Job #1 is delivering the ordered product according to specifications: color, size, brand, and quantity. (netsuite.com)
- [54][55] These are the top 50 countries by the total value of manufacturing output in US dollars for its noted year according to World Bank.[56] (en.wikipedia.org)
External Links
How To
How to use the Just-In Time Method in Production
Just-in time (JIT), is a process that reduces costs and increases efficiency in business operations. It allows you to get the right amount resources at the right time. This means that your only pay for the resources you actually use. Frederick Taylor first coined this term while working in the early 1900s as a foreman. After observing how workers were paid overtime for late work, he realized that overtime was a common practice. He then concluded that if he could ensure that workers had enough time to do their job before starting to work, this would improve productivity.
JIT teaches you to plan ahead and prepare everything so you don’t waste time. Also, you should look at the whole project from start-to-finish and make sure you have the resources necessary to address any issues. You can anticipate problems and have enough equipment and people available to fix them. This way, you won't end up paying extra money for things that weren't really necessary.
There are many types of JIT methods.
-
Demand-driven: This type of JIT allows you to order the parts/materials required for your project on a regular basis. This will allow you to track how much material you have left over after using it. This will allow you to calculate how long it will take to make more.
-
Inventory-based : You can stock the materials you need in advance. This allows one to predict how much they will sell.
-
Project-driven: This approach involves setting aside sufficient funds to cover your project's costs. You will be able to purchase the right amount of materials if you know what you need.
-
Resource-based JIT: This type of JIT is most commonly used. You assign certain resources based off demand. For example, if there is a lot of work coming in, you will have more people assigned to them. If you don't receive many orders, then you'll assign fewer employees to handle the load.
-
Cost-based: This is similar to resource-based, except that here you're not just concerned about how many people you have but how much each person costs.
-
Price-based: This approach is very similar to the cost-based method except that you don't look at individual workers costs but the total cost of the company.
-
Material-based: This is very similar to cost-based but instead of looking at total costs of the company you are concerned with how many raw materials you use on an average.
-
Time-based: This is another variation of resource-based JIT. Instead of focusing solely on the amount each employee costs, focus on how long it takes for the project to be completed.
-
Quality-based JIT is another variant of resource-based JIT. Instead of thinking about how much each employee costs or how long it takes to manufacture something, you think about how good the quality of your product is.
-
Value-based JIT is the newest form of JIT. In this instance, you are not concerned about the product's performance or meeting customer expectations. Instead, your focus is on the value you bring to the market.
-
Stock-based: This is an inventory-based method that focuses on the actual number of items being produced at any given time. This method is useful when you want to increase production while decreasing inventory.
-
Just-in-time (JIT) planning: This is a combination of JIT and supply chain management. It is the process of scheduling components' delivery as soon as they have been ordered. It is essential because it reduces lead-times and increases throughput.