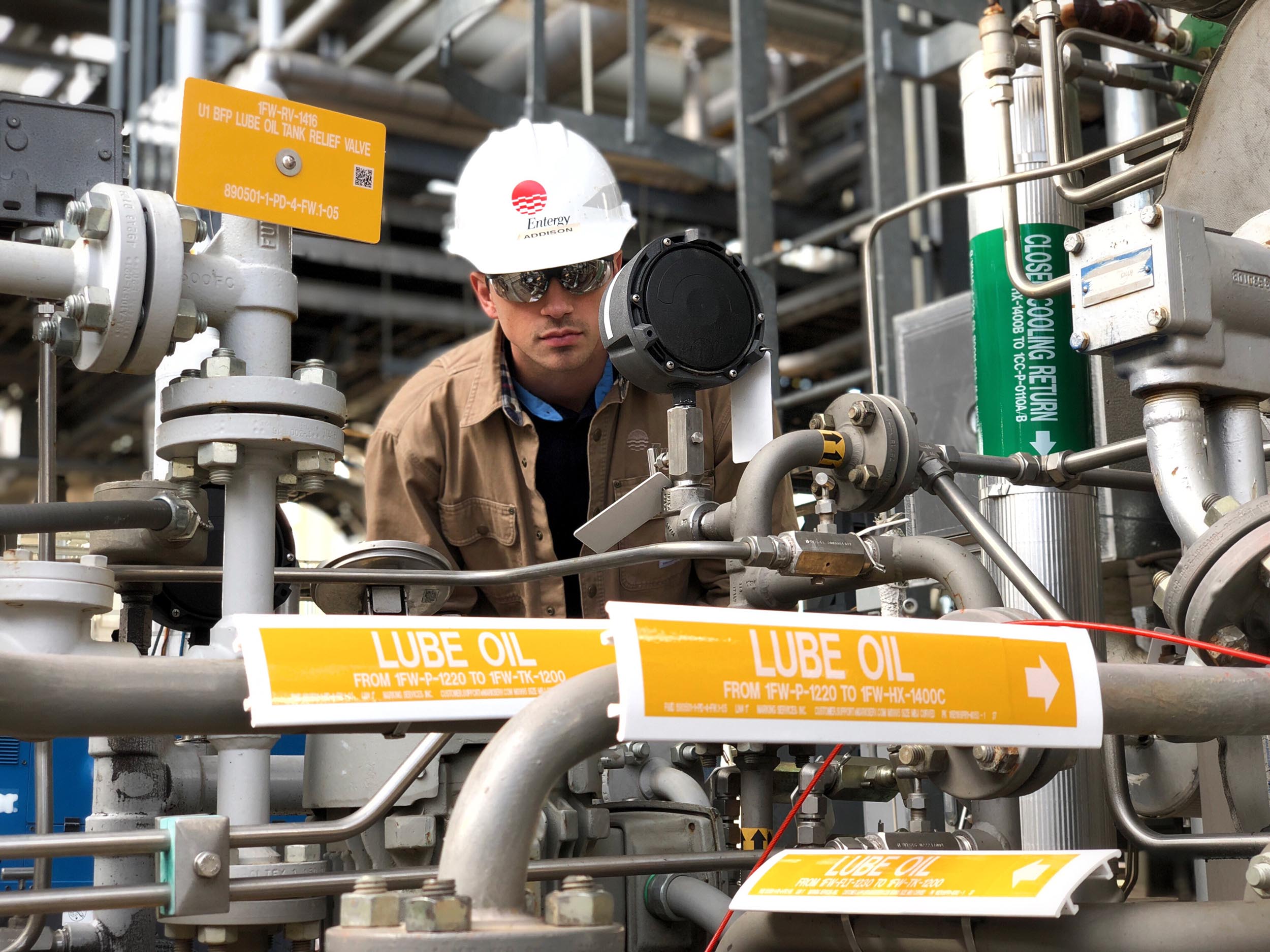
Kaizen isn't always easy to integrate into manufacturing processes. It is slow and takes time to get inventory and make sure everyone is on the same page. The length of this improvement project depends on the type of company and participation level. To ensure that your manufacturing process improvement initiative will be successful, follow the proper implementation methodologies and get the necessary resources. You must create a company culture that encourages continual improvement in order to make this strategy a success.
Establishing a culture of improvement in your company
Gallup polls show that only 32% percent of American employees are actively engaged in their jobs. 17.2% of those surveyed were disengaged. Implementing a Kaizen culture will encourage employee engagement, which will ultimately improve processes, reduce turnover, and encourage innovation. Engagement will increase employee productivity and satisfaction. Kaizen culture provides many other benefits than reducing waste and improving productivity.
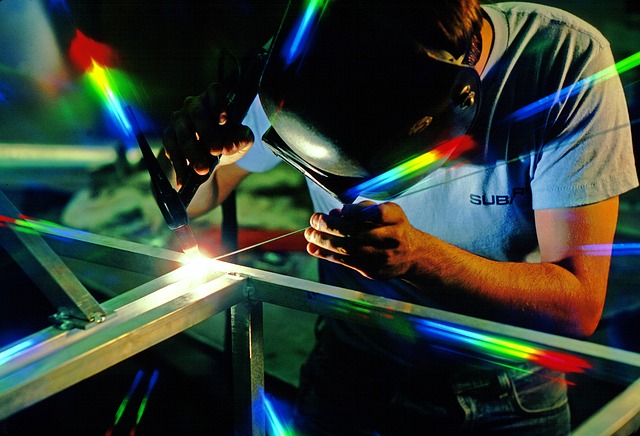
Kaizen is a philosophy that encourages continuous improvement in every area of a business. Rather than making big, sweeping changes that have little to no benefit, Kaizen is a method of incremental improvement. Kaizen is a process that can improve customer satisfaction, productivity, quality, and costs. It can also improve communication and morale among employees.
Implementing kaizen in manufacturing is difficult
Although there are many benefits to implementing kaizen, there are also some drawbacks. First, the implementation of kaizen can require major changes to a business's managerial system. It can be hard to reverse these changes after the changes have been made. Second, many businesses find it difficult or impossible to modify their existing work practices. This could hinder the implementation of kaizen.
Another common obstacle is that many manufacturers operate on a "feast or famine" cycle. A machine shop could run into difficulties if there isn't enough demand for the products they produce or enough qualified people to fill their positions. In such a scenario, they will have to layoff employees and close their doors. The solution is to implement kaizen or continuous improvement. This will prevent these machine shops from becoming "feast" or "famine." Kaizen can increase shop efficiency and allow shops to produce more.
Kaizen implementation in manufacturing: Success rate
Statistics show that Kaizen implementation in manufacturing is not a success. Only 10% manufacturing firms reported positive Kaizen results. However, this doesn't mean that implementation is futile. Implementing Kaizen is an integral part of lean manufacturing. Here are some tips for increasing the success rate of your manufacturing enterprise:
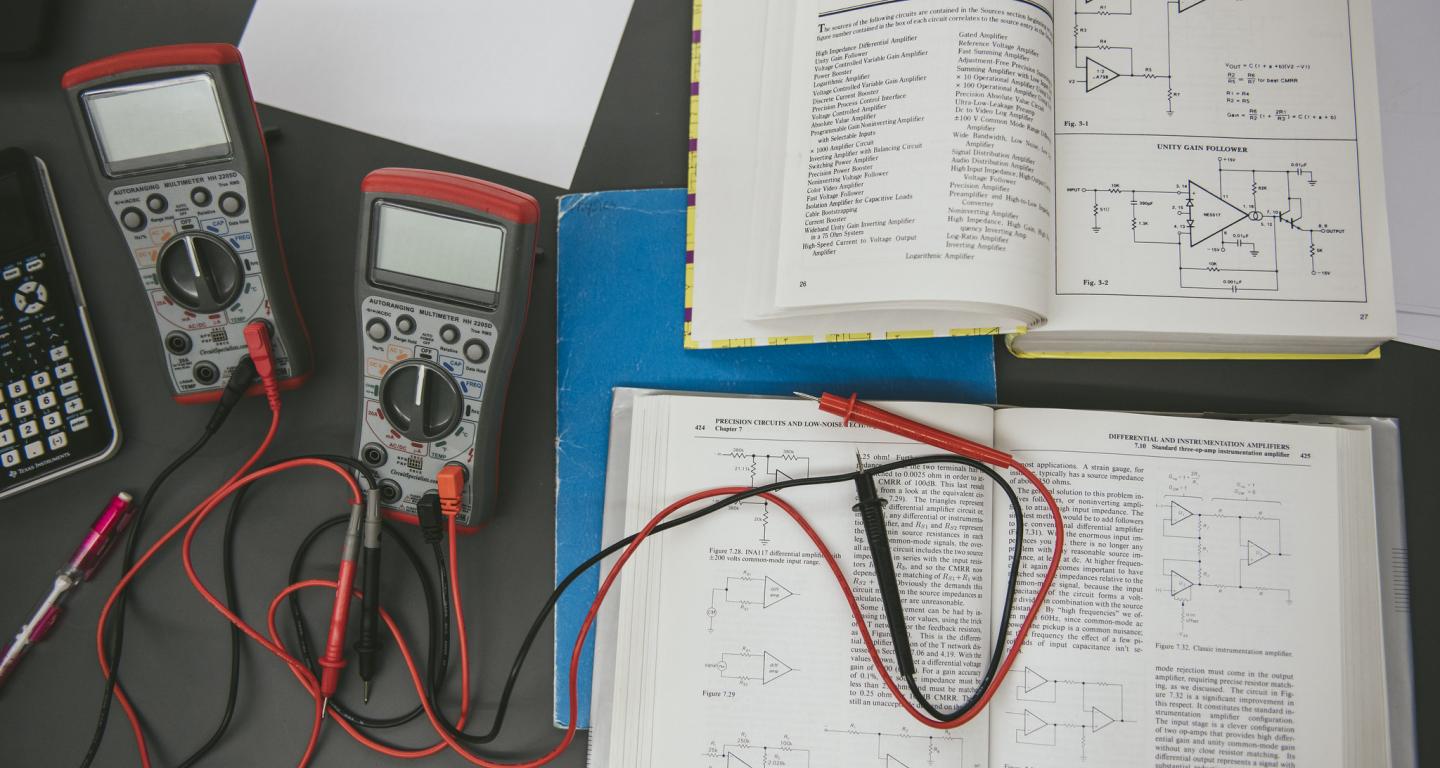
First, the process of kaizen must start with an understanding of current state processes. Data is collected and analyzed in order to identify top priorities. After that, improvements can be tested and verified through a before-and after comparison. The benefit-to–cost analysis can be used to evaluate the effect of any improvement or the entire process. It is vital to track the results from kaizen cycles over 60-90 days in order to assess its effectiveness.
FAQ
What are the responsibilities of a manufacturing manager
A manufacturing manager has to ensure that all manufacturing processes work efficiently and effectively. They should also be aware of any problems within the company and act accordingly.
They should also know how to communicate with other departments such as sales and marketing.
They should be informed about industry trends and be able make use of this information to improve their productivity and efficiency.
What is the responsibility for a logistics manager
Logistics managers make sure all goods are delivered on schedule and without damage. This is done using his/her knowledge of the company's products. He/she should also ensure enough stock is available to meet demand.
What jobs are available in logistics?
There are different kinds of jobs available in logistics. Here are some examples:
-
Warehouse workers – They load, unload and transport pallets and trucks.
-
Transport drivers - These are people who drive trucks and trailers to transport goods or perform pick-ups.
-
Freight handlers: They sort and package freight in warehouses.
-
Inventory managers: They are responsible for the inventory and management of warehouses.
-
Sales reps are people who sell products to customers.
-
Logistics coordinators are responsible for organizing and planning logistics operations.
-
Purchasing agents: They are responsible for purchasing goods and services to support company operations.
-
Customer service representatives – They answer emails and phone calls from customers.
-
Shipping clerks: They process shipping requests and issue bills.
-
Order fillers - They fill orders based on what is ordered and shipped.
-
Quality control inspectors are responsible for inspecting incoming and outgoing products looking for defects.
-
Others - There are many other types of jobs available in logistics, such as transportation supervisors, cargo specialists, etc.
What does warehouse refer to?
A warehouse is a place where goods are stored until they are sold. It can be either an indoor or outdoor space. Sometimes, it can be both an indoor and outdoor space.
How can we improve manufacturing efficiency?
First, we need to identify which factors are most critical in affecting production times. Next, we must find ways to improve those factors. You can start by identifying the most important factors that impact production time. Once you've identified them, try to find solutions for each of those factors.
Why automate your warehouse?
Modern warehousing has seen automation take center stage. With the rise of ecommerce, there is a greater demand for faster delivery times as well as more efficient processes.
Warehouses have to be flexible to meet changing requirements. To do so, they must invest heavily in technology. Automating warehouses has many benefits. Here are some benefits of investing in automation
-
Increases throughput/productivity
-
Reduces errors
-
Increases accuracy
-
Safety is boosted
-
Eliminates bottlenecks
-
Companies can scale up more easily
-
This makes workers more productive
-
Gives you visibility into all that is happening in your warehouse
-
Enhances customer experience
-
Improves employee satisfaction
-
Minimizes downtime and increases uptime
-
Quality products delivered on time
-
Eliminates human error
-
It helps ensure compliance with regulations
How can we reduce manufacturing overproduction?
Improved inventory management is the key to reducing overproduction. This would reduce the amount of time spent on unnecessary activities such as purchasing, storing, and maintaining excess stock. This would allow us to use our resources for more productive tasks.
A Kanban system is one way to achieve this. A Kanban board is a visual display used to track work in progress. Work items are moved through various states to reach their destination in a Kanban system. Each state represents a different priority level.
When work is completed, it can be transferred to the next stage. But if a task remains in the beginning stages it will stay that way until it reaches its end.
This allows for work to continue moving forward, while also ensuring that there is no work left behind. With a Kanban board, managers can see exactly how much work is being done at any given moment. This data allows them adjust their workflow based upon real-time data.
Lean manufacturing, another method to control inventory levels, is also an option. Lean manufacturing focuses on eliminating waste throughout the entire production chain. Anything that doesn't add value to the product is considered waste. These are some of the most common types.
-
Overproduction
-
Inventory
-
Unnecessary packaging
-
Material surplus
Manufacturers can increase efficiency and decrease costs by implementing these ideas.
Statistics
- According to a Statista study, U.S. businesses spent $1.63 trillion on logistics in 2019, moving goods from origin to end user through various supply chain network segments. (netsuite.com)
- In the United States, for example, manufacturing makes up 15% of the economic output. (twi-global.com)
- [54][55] These are the top 50 countries by the total value of manufacturing output in US dollars for its noted year according to World Bank.[56] (en.wikipedia.org)
- In 2021, an estimated 12.1 million Americans work in the manufacturing sector.6 (investopedia.com)
- Many factories witnessed a 30% increase in output due to the shift to electric motors. (en.wikipedia.org)
External Links
How To
How to Use the Just In Time Method in Production
Just-intime (JIT), which is a method to minimize costs and maximize efficiency in business process, is one way. It is a process where you get the right amount of resources at the right moment when they are needed. This means you only pay what you use. Frederick Taylor developed the concept while working as foreman in early 1900s. Taylor observed that overtime was paid to workers if they were late in working. He concluded that if workers were given enough time before they start work, productivity would increase.
JIT teaches you to plan ahead and prepare everything so you don’t waste time. The entire project should be looked at from start to finish. You need to ensure you have enough resources to tackle any issues that might arise. You can anticipate problems and have enough equipment and people available to fix them. This way you won't be spending more on things that aren’t really needed.
There are many JIT methods.
-
Demand-driven: This JIT is where you place regular orders for the parts/materials that are needed for your project. This will let you track the amount of material left over after you've used it. You'll also be able to estimate how long it will take to produce more.
-
Inventory-based: You stock materials in advance to make your projects easier. This allows you to forecast how much you will sell.
-
Project-driven: This means that you have enough money to pay for your project. Knowing how much money you have available will help you purchase the correct amount of materials.
-
Resource-based JIT : This is probably the most popular type of JIT. Here, you allocate certain resources based on demand. For example, if there is a lot of work coming in, you will have more people assigned to them. If you don’t have many orders you will assign less people to the work.
-
Cost-based: This approach is very similar to resource-based. However, you don't just care about the number of people you have; you also need to consider how much each person will cost.
-
Price-based: This is a variant of cost-based. However, instead of focusing on the individual workers' costs, this looks at the total price of the company.
-
Material-based: This is quite similar to cost-based, but instead of looking at the total cost of the company, you're concerned with how much raw materials you spend on average.
-
Time-based: Another variation of resource-based JIT. Instead of worrying about how much each worker costs, you can focus on how long the project takes.
-
Quality-based JIT: Another variation on resource-based JIT. Instead of thinking about how much each employee costs or how long it takes to manufacture something, you think about how good the quality of your product is.
-
Value-based: This is one of the newest forms of JIT. In this instance, you are not concerned about the product's performance or meeting customer expectations. Instead, your focus is on the value you bring to the market.
-
Stock-based: This is an inventory-based method that focuses on the actual number of items being produced at any given time. It's useful when you want maximum production and minimal inventory.
-
Just-in-time planning (JIT): This is a combination JIT and supply-chain management. It is the process that schedules the delivery of components within a short time of their order. It's important as it reduces leadtimes and increases throughput.