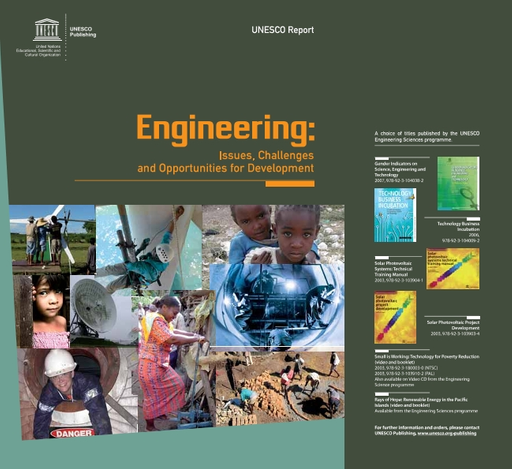
Manufacturing failures have many causes, including bad design, cost saving initiatives, a lack of quality control, etc. There are a number of ways to avoid problems and improve product quality.
Does lean manufacturing really work?
Companies that adopt lean practices often have great success. These companies can eliminate waste, improve cycle time and reap other benefits. These companies do this through trial-and-error and failure.
The main reason for implementation failures, according to almost all lean experts, is due to the senior management. These are the people who are responsible for every aspect of a business, yet they don't always know how to implement lean.
This can make it difficult for employees to join in and achieve the desired results. That's why it is important to begin a skill assessment well before implementing lean techniques. This will eliminate a lot ambiguity, help keep you on track and identify who is able to help you achieve your goals.
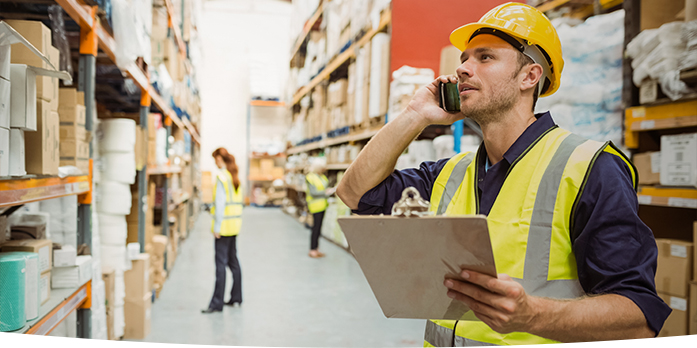
Why do manufacturers fail?
Some manufacturing errors are the result of a manufacturer using the wrong material, or not implementing the right quality control measures. Other defects are caused by manufacturing errors, which are when a product is made in a way that it's not designed to be. These mistakes are costly to correct and may even lead to a company losing revenue.
These problems are costly, both for the producer and for the consumer. Therefore, it is vital that products be manufactured correctly. To prevent these problems, companies need to be able to identify failures early in the manufacturing process and to repair them as soon as possible.
Manufacturers need to know the reasons for machine failures in order to achieve their goal. This will allow them to better understand their business processes and lower their costs.
One of the most common failures is when a manufacturer does not have enough capital. It can be due to a variety of factors. However, it is important to keep in mind that the company must have enough funds to continue its production and sales over time.
The manufacturer and consumer can both be affected by a lack of funds. This can lead to a variety of issues, such as a delay in delivery or lower prices for the product.
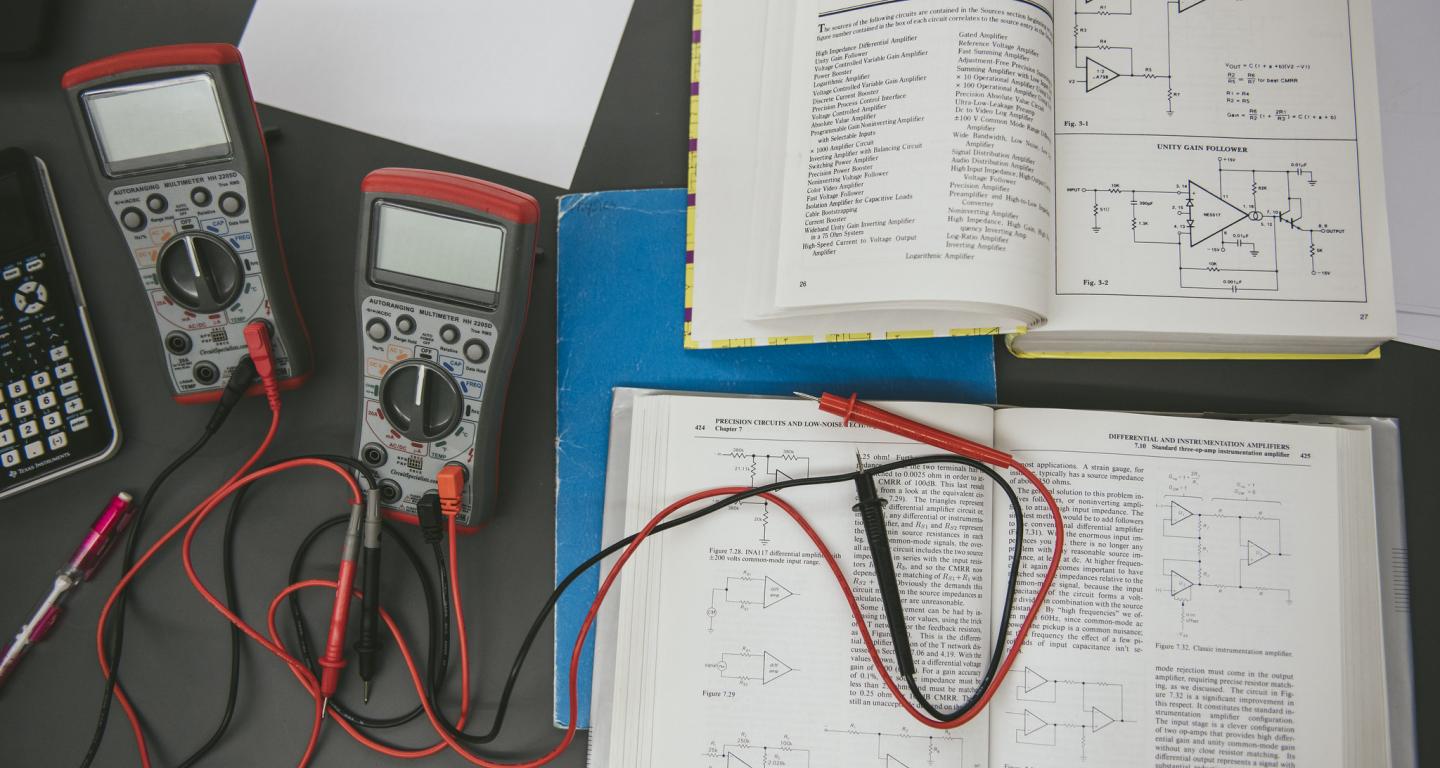
A consumer may also be injured if they use the product in a dangerous way. If a person breaks their bone after playing with a lit match, the manufacturer could be held responsible for failing to warn the victim about the fire-starting risk.
This is a dangerous situation for children, who may not be familiar with handling hazardous substances. This can be an expensive problem for the manufacturer, but is vital to any business that wants to remain in business.
FAQ
Is there anything we should know about Manufacturing Processes prior to learning about Logistics.
No. No. Knowing about manufacturing processes will help you understand how logistics works.
How can manufacturing reduce production bottlenecks?
Avoiding production bottlenecks is as simple as keeping all processes running smoothly, from the time an order is received until the product ships.
This includes planning to meet capacity requirements and quality control.
The best way to do this is to use continuous improvement techniques such as Six Sigma.
Six Sigma is a management system used to improve quality and reduce waste in every aspect of your organization.
It emphasizes consistency and eliminating variance in your work.
How does a Production Planner differ from a Project Manager?
The difference between a product planner and project manager is that a planer is typically the one who organizes and plans the entire project. A production planner, however, is mostly involved in the planning stages.
Can certain manufacturing steps be automated?
Yes! Automation has been around since ancient times. The Egyptians invent the wheel thousands of year ago. Robots are now used to assist us in assembly lines.
Robotics is used in many manufacturing processes today. These include:
-
Automation line robots
-
Robot welding
-
Robot painting
-
Robotics inspection
-
Robots that create products
Manufacturing can also be automated in many other ways. For instance, 3D printing allows us make custom products and not have to wait for months or even weeks to get them made.
What does it take for a logistics enterprise to succeed?
To be a successful businessman in logistics, you will need many skills and knowledge. Good communication skills are essential to effectively communicate with your suppliers and clients. You should be able analyse data and draw inferences. You must be able manage stress and pressure under pressure. You need to be innovative and creative to come up with new ways to increase efficiency. To motivate and guide your team towards reaching organizational goals, you must have strong leadership skills.
To meet tight deadlines, you must also be efficient and organized.
Statistics
- According to a Statista study, U.S. businesses spent $1.63 trillion on logistics in 2019, moving goods from origin to end user through various supply chain network segments. (netsuite.com)
- [54][55] These are the top 50 countries by the total value of manufacturing output in US dollars for its noted year according to World Bank.[56] (en.wikipedia.org)
- You can multiply the result by 100 to get the total percent of monthly overhead. (investopedia.com)
- In the United States, for example, manufacturing makes up 15% of the economic output. (twi-global.com)
- Job #1 is delivering the ordered product according to specifications: color, size, brand, and quantity. (netsuite.com)
External Links
How To
How to Use lean manufacturing in the Production of Goods
Lean manufacturing (or lean manufacturing) is a style of management that aims to increase efficiency, reduce waste and improve performance through continuous improvement. It was developed in Japan between 1970 and 1980 by Taiichi Ohno. TPS founder Kanji Tyoda gave him the Toyota Production System, or TPS award. Michael L. Watkins published the book "The Machine That Changed the World", which was the first to be published about lean manufacturing.
Lean manufacturing can be described as a set or principles that are used to improve quality, speed and cost of products or services. It emphasizes eliminating waste and defects throughout the value stream. Just-in-time (JIT), zero defect (TPM), and 5S are all examples of lean manufacturing. Lean manufacturing emphasizes reducing non-value-added activities like inspection, rework and waiting.
Lean manufacturing not only improves product quality but also reduces costs. Companies can also achieve their goals faster by reducing employee turnover. Lean manufacturing can be used to manage all aspects of the value chain. Customers, suppliers, distributors, retailers and employees are all included. Lean manufacturing practices are widespread in many industries. Toyota's philosophy, for example, is what has enabled it to be successful in electronics, automobiles, medical devices, healthcare and chemical engineering as well as paper and food.
Lean manufacturing is based on five principles:
-
Define Value: Identify the social value of your business and what sets you apart.
-
Reduce Waste – Eliminate all activities that don't add value throughout the supply chain.
-
Create Flow - Make sure work runs smoothly without interruptions.
-
Standardize & simplify - Make processes consistent and repeatable.
-
Build Relationships - Establish personal relationships with both internal and external stakeholders.
Lean manufacturing is not a new concept, but it has been gaining popularity over the last few years due to a renewed interest in the economy following the global financial crisis of 2008. To increase their competitiveness, many businesses have turned to lean manufacturing. In fact, some economists believe that lean manufacturing will be an important factor in economic recovery.
With many benefits, lean manufacturing is becoming more common in the automotive industry. These include higher customer satisfaction, lower inventory levels, lower operating expenses, greater productivity, and improved overall safety.
Lean manufacturing can be applied to almost every aspect of an organization. This is because it ensures efficiency and effectiveness in all stages of the value chain.
There are three main types of lean manufacturing:
-
Just-in Time Manufacturing, (JIT): This kind of lean manufacturing is also commonly known as "pull-systems." JIT refers to a system in which components are assembled at the point of use instead of being produced ahead of time. This approach reduces lead time, increases availability and reduces inventory.
-
Zero Defects Manufacturing (ZDM): ZDM focuses on ensuring that no defective units leave the manufacturing facility. If a part needs to be fixed during the assembly line, it should be repaired rather than scrapped. This applies to finished goods that may require minor repairs before shipment.
-
Continuous Improvement (CI), also known as Continuous Improvement, aims at improving the efficiency of operations through continuous identification and improvement to minimize or eliminate waste. Continuous Improvement (CI) involves continuous improvement in processes, people, tools, and infrastructure.