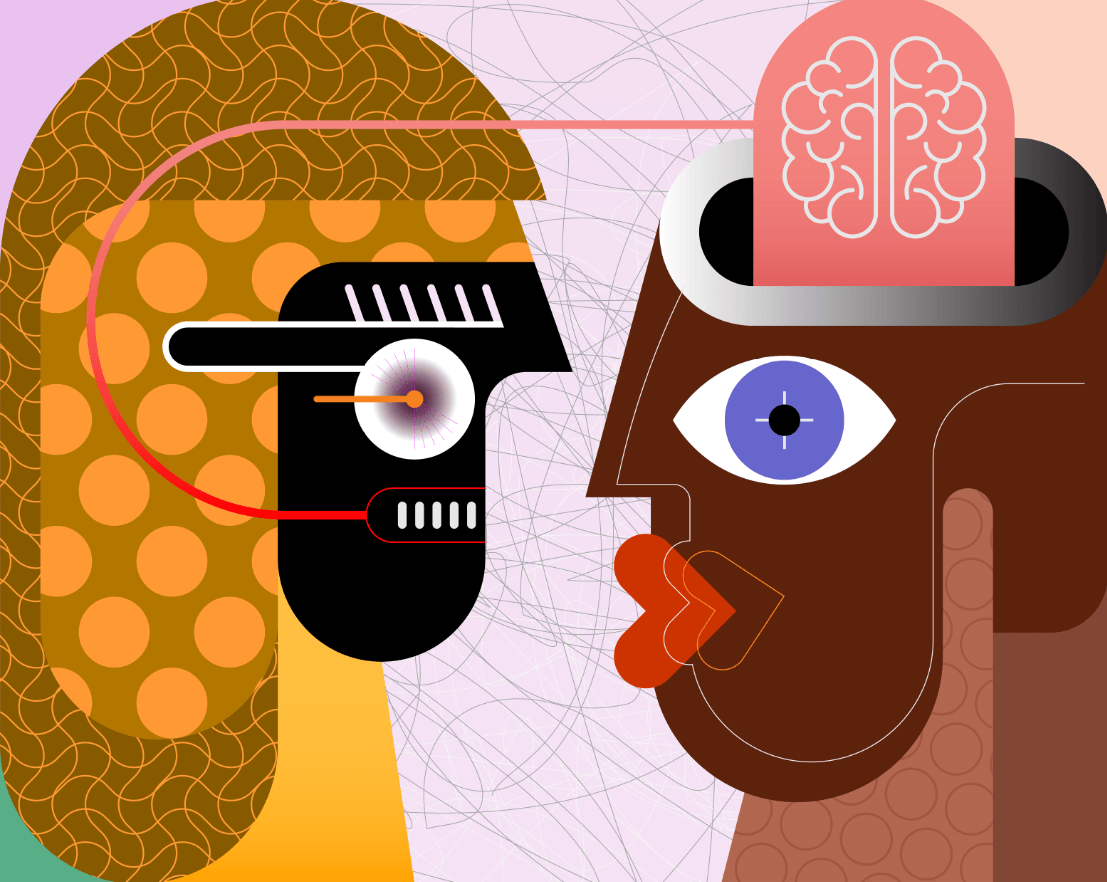
Gemba walk was developed originally by Toyota. This tool takes managers to the shop floor in order to gain insight into the company's process. This is an integral part of any facility renovation. It helps managers understand the processes in their company and make better decisions. The practice also helps to identify problems and potential solutions.
Gemba, a Japanese term meaning "where the work happens", is a Japanese term. Gemba is used to refer to the shop floor or factory floor. However, it can also be used to describe any area where a product is created. Gemba is also the name of a Japanese business philosophy that sets out a series of objectives. Gemba is a Japanese business philosophy that aims to in depth understand the processes of an organization and reduce waste.
Gemba walks are important for companies that are looking to improve their processes and to eliminate waste. Gemba walks also promote cooperation in the workplace. They encourage employees and their families to share ideas. This can increase the quality of any product or service. They can also help managers and executives to better understand the processes in their company.
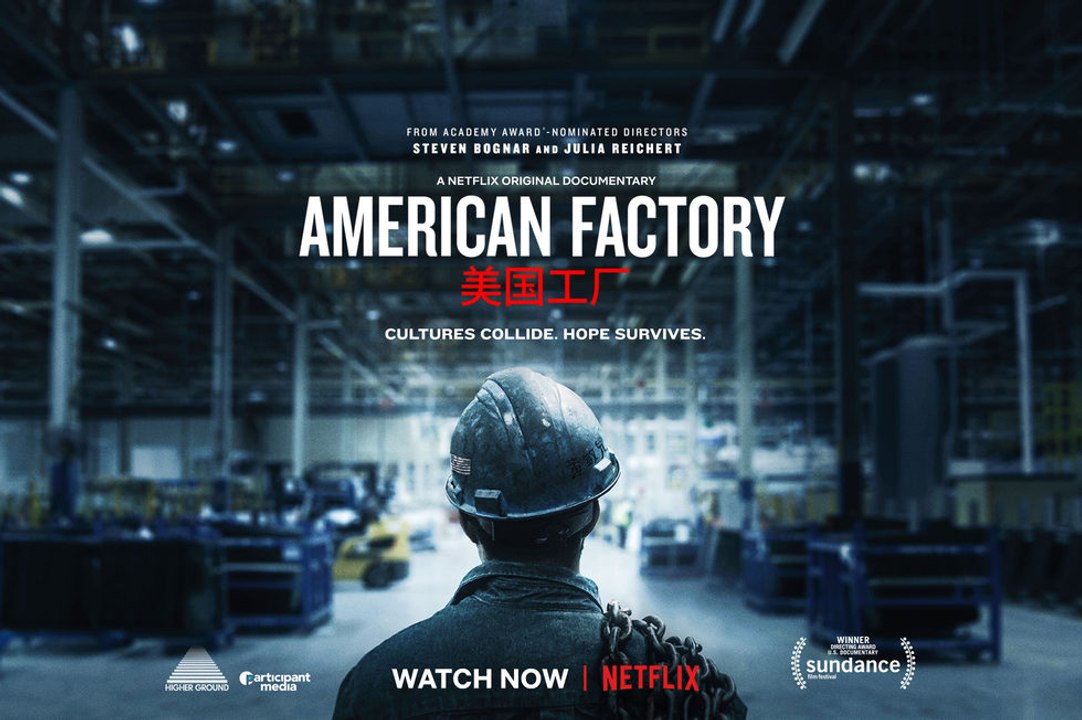
Gemba walks can usually be carried out by supervisors and managers. But, they can also easily be undertaken by executives. Gemba walks should always be conducted by senior executives. Gemba walks should be completed with a Lean teacher, Sensei, for approximately 45-60 minutes each week. Because it is easy to observe how workers do their jobs, these walks should not be done during peak hours.
Gemba Walks assist executives and managers in understanding the working of processes and identifying improvement opportunities. They also help to improve the overall safety of an organization. Safety is the largest waste stream from manufacturing plants. Increasing safety can lead to continuous improvement.
Gemba Walks can be a vital part of Lean but they should also be implemented by all levels of an organization. Gemba Walks can be used to help executives and leaders gain a new perspective on their customers' needs, which can result in better products, services and processes. Gemba Walks can help an organization achieve its full potential.
Gemba Walks, which are an integral part Lean process designs and used frequently by key stakeholders in Kaizen meetings, are also a crucial part. A Kaizen event is a gathering of key stakeholders to evaluate activities and evaluate activities, based on the Japanese term, "continuous improvement."
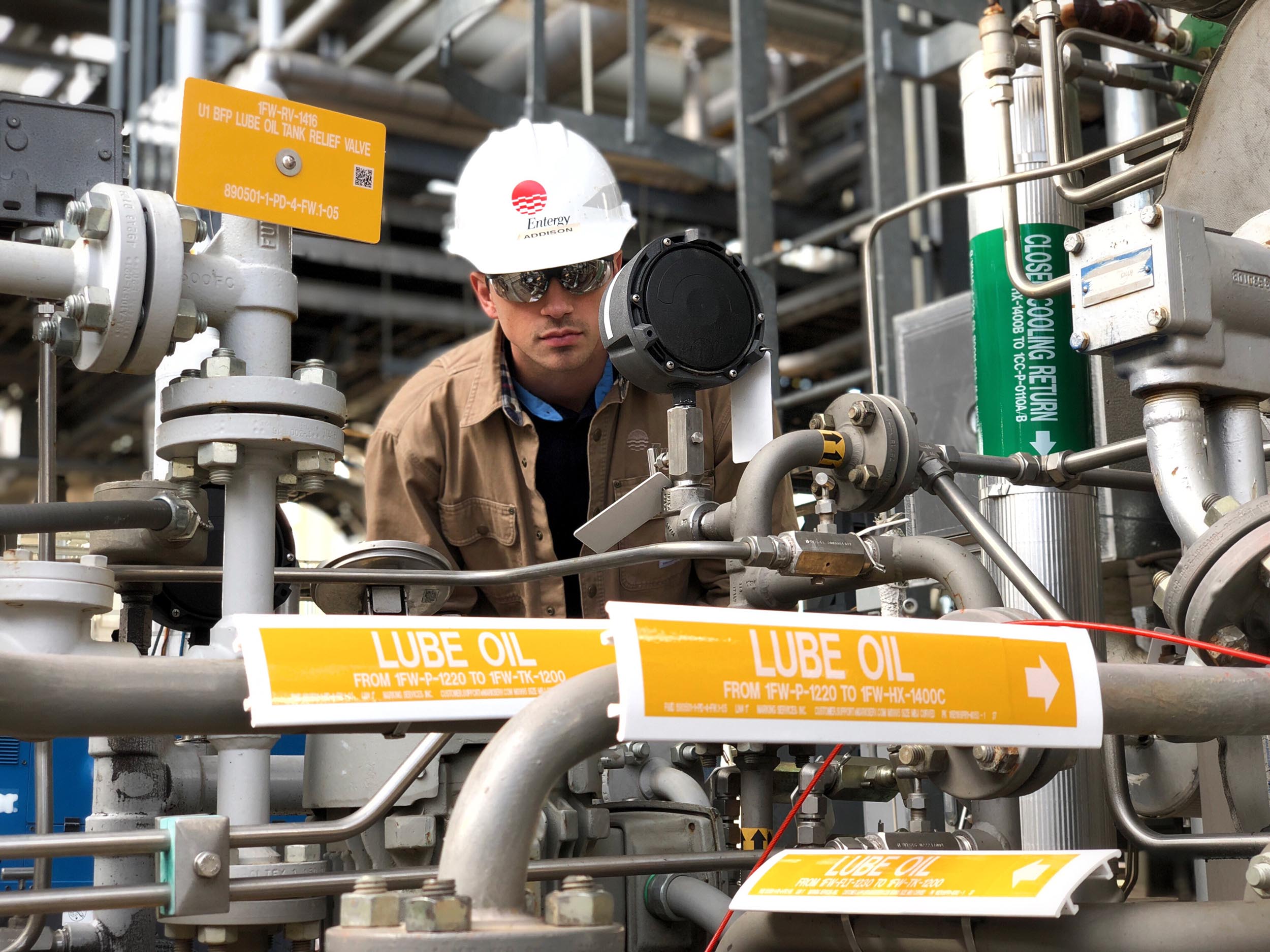
Gemba Walks should be conducted on a regular basis. If they are done correctly, they can reduce waste and improve productivity. Because these are the busiest hours of the day, it is best to do them during shift changes. This will provide executives and project manager with a new outlook on their business. It is important to note any potential improvements, such as new products and services, or any ideas from employees.
FAQ
What skills are required to be a production manager?
Being a production planner is not easy. You need to be organized and flexible. You must also be able to communicate effectively with clients and colleagues.
What can I do to learn more about manufacturing?
Experience is the best way for you to learn about manufacturing. You can read books, or watch instructional videos if you don't have the opportunity to do so.
Is automation important for manufacturing?
Not only are service providers and manufacturers important, but so is automation. It allows them to offer services faster and more efficiently. In addition, it helps them reduce costs by reducing human errors and improving productivity.
What is the difference between Production Planning, Scheduling and Production Planning?
Production Planning (PP), also known as forecasting and identifying production capacities, is the process that determines what product needs to be produced at any particular time. This is done through forecasting demand and identifying production capacities.
Scheduling refers to the process of allocating specific dates to tasks in order that they can be completed within a specified timeframe.
What are the four types of manufacturing?
Manufacturing is the process by which raw materials are transformed into useful products through machines and processes. Manufacturing involves many activities, including designing, building, testing and packaging, shipping, selling, service, and so on.
How can manufacturing avoid production bottlenecks
The key to avoiding bottlenecks in production is to keep all processes running smoothly throughout the entire production cycle, from the time you receive an order until the time when the product ships.
This includes both planning for capacity and quality control.
The best way to do this is to use continuous improvement techniques such as Six Sigma.
Six Sigma is a management system used to improve quality and reduce waste in every aspect of your organization.
It is focused on creating consistency and eliminating variation in your work.
Statistics
- Many factories witnessed a 30% increase in output due to the shift to electric motors. (en.wikipedia.org)
- [54][55] These are the top 50 countries by the total value of manufacturing output in US dollars for its noted year according to World Bank.[56] (en.wikipedia.org)
- In 2021, an estimated 12.1 million Americans work in the manufacturing sector.6 (investopedia.com)
- In the United States, for example, manufacturing makes up 15% of the economic output. (twi-global.com)
- According to the United Nations Industrial Development Organization (UNIDO), China is the top manufacturer worldwide by 2019 output, producing 28.7% of the total global manufacturing output, followed by the United States, Japan, Germany, and India.[52][53] (en.wikipedia.org)
External Links
How To
How to Use the Just In Time Method in Production
Just-in time (JIT), is a process that reduces costs and increases efficiency in business operations. It's the process of obtaining the right amount and timing of resources when you need them. This means you only pay what you use. Frederick Taylor was the first to coin this term. He developed it while working as a foreman during the early 1900s. He noticed that workers were often paid overtime when they had to work late. He decided that workers would be more productive if they had enough time to complete their work before they started to work.
JIT is a way to plan ahead and make sure you don't waste any money. The entire project should be looked at from start to finish. You need to ensure you have enough resources to tackle any issues that might arise. If you expect problems to arise, you will be able to provide the necessary equipment and personnel to address them. You won't have to pay more for unnecessary items.
There are different types of JIT methods:
-
Demand-driven JIT: This is a JIT that allows you to regularly order the parts/materials necessary for your project. This will enable you to keep track of how much material is left after you use it. This will allow to you estimate the time it will take for more to be produced.
-
Inventory-based: This is a type where you stock the materials required for your projects in advance. This allows you to predict how much you can expect to sell.
-
Project-driven: This is an approach where you set aside enough funds to cover the cost of your project. When you know how much you need, you'll purchase the appropriate amount of materials.
-
Resource-based JIT : This is probably the most popular type of JIT. Here you can allocate certain resources based purely on demand. You will, for example, assign more staff to deal with large orders. You'll have fewer orders if you have fewer.
-
Cost-based: This is a similar approach to resource-based but you are not only concerned with how many people you have, but also how much each one costs.
-
Price-based pricing: This is similar in concept to cost-based but instead you look at how much each worker costs, it looks at the overall company's price.
-
Material-based: This is very similar to cost-based but instead of looking at total costs of the company you are concerned with how many raw materials you use on an average.
-
Time-based JIT: This is another variant of resource-based JIT. Instead of focusing only on how much each employee is costing, you should focus on how long it takes to complete your project.
-
Quality-based JIT: This is another variation of resource based JIT. Instead of focusing on the cost of each worker or how long it takes, think about how high quality your product is.
-
Value-based JIT: This is the latest form of JIT. In this scenario, you're not concerned about how products perform or whether customers expect them to meet their expectations. Instead, your focus is on the value you bring to the market.
-
Stock-based: This inventory-based approach focuses on how many items are being produced at any one time. It's useful when you want maximum production and minimal inventory.
-
Just-in-time (JIT) planning: This is a combination of JIT and supply chain management. It's the process of scheduling delivery of components immediately after they are ordered. It reduces lead times and improves throughput.