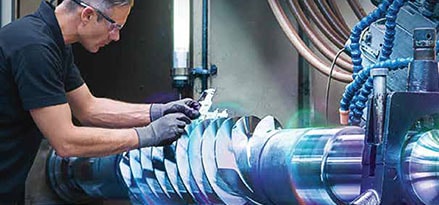
Industrial engineering technicians use their knowledge of mathematics and engineering to determine and improve the way a business runs. This includes the development of blueprints for machinery and the analysis of statistical data. A skilled industrial engineer can assist management in making decisions that will improve the company's efficiency.
Typical tasks of an industrial engineering technician include: performing time and motion studies to enhance productivity, evaluating performance and implementing changes. They may also be called on to analyze data from an industrial health and safety program.
Other technical tasks include preparing graphs and diagrams to illustrate the flow of a process. They also conduct a variety quality control tests on products in order to ensure they meet standards.
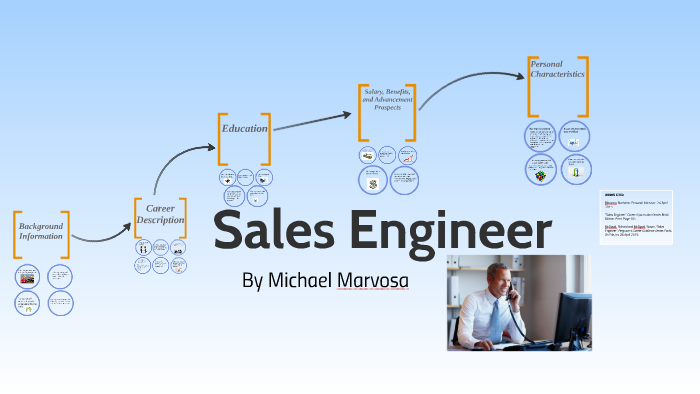
A popular job function for industrial engineers is to plan workflows, analyze production costs, gauge prototypes, assess equipment capacities, and create efficient operating procedures. They can be found in a variety of industries, including aerospace, pharmaceuticals, electronics, food, and automotive. Most work full-time. Their average salary is $53,000 per annum, but they may earn more if they have more education or experience.
You don't need a degree to be an industrial engineer. An industrial engineer must have strong math skills, good critical thinking, and attention to detail. They must also be able to speak with and work with employees, and be able to accurately observe the processes that take place in a workplace.
An industrial engineer technician should be able recognize key elements and create the best workflow possible. For instance, they must be able to see the importance of reducing wasted materials and wasteful practices. This allows them to see the value of implementing improvements at work and can save money for the company.
They are more likely to be the first in an organization to explore new ideas. This is possible by using a strategic outline. It's similar to putting together pieces of a huge puzzle.
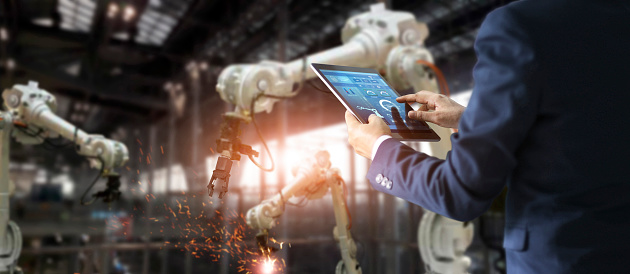
A second important job function for an industrial engineer is to improve the quality and quantity of the product. Although the automation of manufacturing will decrease the number of jobs available, increasing cost control will increase the importance of industrial engineering technicians.
When it comes to the best way to measure the performance of a system, an engineer might choose to conduct a time and motion study to determine how long it takes to complete a task. An engineer might use the results to calculate a production rate based on the information they have gathered. These data will be used to improve the operations.
A variety of courses are offered in the industrial engineering technology program at universities like Liberty University. These courses range from basic machinist skills, motor controls, hydraulics and self-management. This program teaches problem-solving skills as well as how to work with others to achieve their goals.
FAQ
What are the responsibilities for a manufacturing manager
A manufacturing manager must make sure that all manufacturing processes run smoothly and effectively. They must also be alert to any potential problems and take appropriate action.
They should also be able communicate with other departments, such as sales or marketing.
They should also be knowledgeable about the latest trends in the industry so they can use this information for productivity and efficiency improvements.
Why should you automate your warehouse?
Modern warehouses are increasingly dependent on automation. Increased demand for efficient and faster delivery has resulted in a rise in e-commerce.
Warehouses must be able to quickly adapt to changing demands. They must invest heavily in technology to do this. The benefits of automating warehouses are numerous. Here are some benefits of investing in automation
-
Increases throughput/productivity
-
Reduces errors
-
Increases accuracy
-
Boosts safety
-
Eliminates bottlenecks
-
Allows companies scale more easily
-
Makes workers more efficient
-
The warehouse can be viewed from all angles.
-
Enhances customer experience
-
Improves employee satisfaction
-
Reducing downtime and increasing uptime
-
Quality products delivered on time
-
Removes human error
-
This helps to ensure compliance with regulations
What is the difference between Production Planning and Scheduling?
Production Planning (PP), or production planning, is the process by which you determine what products are needed at any given time. This is done through forecasting demand and identifying production capacities.
Scheduling is the process that assigns dates to tasks so they can get completed within a given timeframe.
What makes a production planner different from a project manger?
The major difference between a Production Planner and a Project Manager is that a Project Manager is often the person responsible for organizing and planning the entire project. While a Production Planner is involved mainly in the planning stage,
What are the 7 Rs of logistics management?
The 7R's of Logistics is an acronym for the seven basic principles of logistics management. It was developed by the International Association of Business Logisticians (IABL) and published in 2004 as part of its "Seven Principles of Logistics Management" series.
The acronym is made up of the following letters:
-
Responsible - ensure that all actions taken are within legal requirements and are not harmful to others.
-
Reliable - You can have confidence that you will fulfill your promises.
-
It is reasonable to use resources efficiently and not waste them.
-
Realistic - Take into consideration all aspects of operations including cost-effectiveness, environmental impact, and other factors.
-
Respectful - treat people fairly and equitably.
-
You are resourceful and look for ways to save money while increasing productivity.
-
Recognizable - Provide value-added services to customers
Statistics
- (2:04) MTO is a production technique wherein products are customized according to customer specifications, and production only starts after an order is received. (oracle.com)
- [54][55] These are the top 50 countries by the total value of manufacturing output in US dollars for its noted year according to World Bank.[56] (en.wikipedia.org)
- In 2021, an estimated 12.1 million Americans work in the manufacturing sector.6 (investopedia.com)
- According to a Statista study, U.S. businesses spent $1.63 trillion on logistics in 2019, moving goods from origin to end user through various supply chain network segments. (netsuite.com)
- Job #1 is delivering the ordered product according to specifications: color, size, brand, and quantity. (netsuite.com)
External Links
How To
How to use 5S to increase Productivity in Manufacturing
5S stands for "Sort", 'Set In Order", 'Standardize', & Separate>. Toyota Motor Corporation was the first to develop the 5S approach in 1954. It allows companies to improve their work environment, thereby achieving greater efficiency.
This approach aims to standardize production procedures, making them predictable, repeatable, and easily measurable. This means that daily tasks such as cleaning and sorting, storage, packing, labeling, and packaging are possible. These actions allow workers to perform their job more efficiently, knowing what to expect.
Five steps are required to implement 5S: Sort, Set In Order, Standardize. Separate. Each step has a different action and leads to higher efficiency. By sorting, for example, you make it easy to find the items later. When you set items in an order, you put items together. Once you have separated your inventory into groups and organized them, you will store these groups in easily accessible containers. Make sure everything is correctly labeled when you label your containers.
Employees will need to be more critical about their work. Employees must be able to see why they do what they do and find a way to achieve them without having to rely on their old methods. To be successful in the 5S system, employees will need to acquire new skills and techniques.
The 5S method not only increases efficiency but also boosts morale and teamwork. They are more motivated to achieve higher efficiency levels as they start to see improvement.