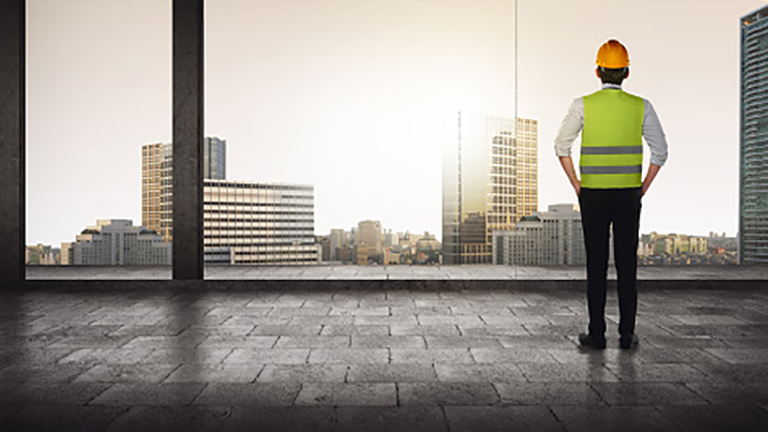
Lean thinking is a method to improve performance in an organization. This is the process of eliminating wasteful activities and undervalued activities from your business processes. It is also an opportunity to create a lean organization culture. A lean culture is a collection of values, principles and practices that increase employee morale and quality and improve productivity. It also creates a more sustainable working environment.
First, identify the value of your customer to implement lean thinking. This means understanding your customers' needs and the whole value chain. Once you know what your customers need, you can identify which steps are involved in your processes. You can identify the steps involved in each process to help you determine whether your current processes are efficient. You can also use the value stream map to see how your company is currently operating. The value streammap shows you the flow of your company, how it works, as well as the value created through each process.
Lean thinking requires flow. It involves the ability to quickly switch from one known activity to another. This is essential when responding quickly to customer demand. It also reduces inventory backlogs. It also makes it possible for workers to quickly switch jobs.
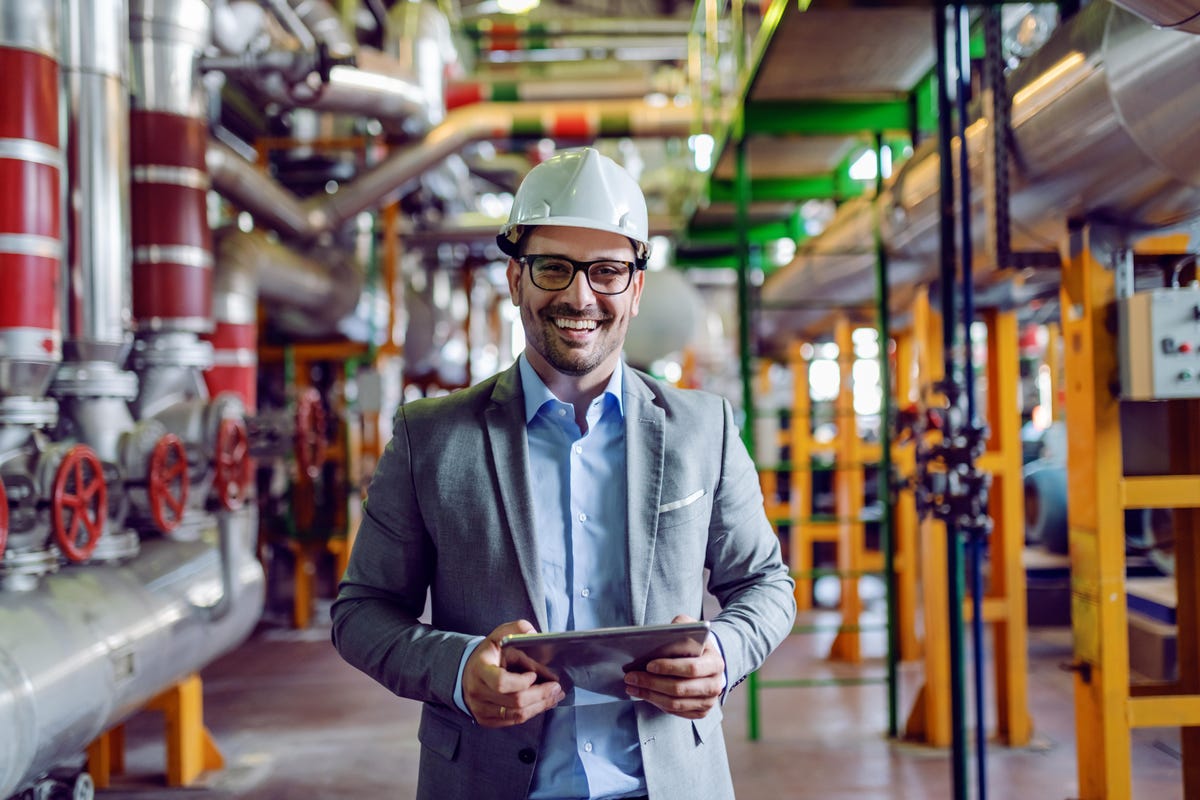
Lean organizations have a similar approach to managing output. They encourage communication and collaboration. They encourage quality assurance, and celebrate the successes. They also minimize unnecessary overcosts to suppliers and customers.
Lean thinking can be applied to any type of work. It can be applied in any kind of work. It can reduce environmental damage and waste, as well as improve employee morale. Lean thinking can be applied to any business area.
Creating a culture that fosters lean thinking is a key factor in implementing lean production practices. Culture should have a clear definition and encourage employee motivation. It also must be willing to take small steps forward on a regular basis. This is called kaizen.
Lean thinking requires continuous improvement. To improve the quality of your product you have to be open to small improvements each day. This can be achieved by either implementing organizational changes or using standardized tasks. Standardized work is a visual representation of the flow of work. Everything is clearly located. It helps people see how to overcome obstacles and make work easier.
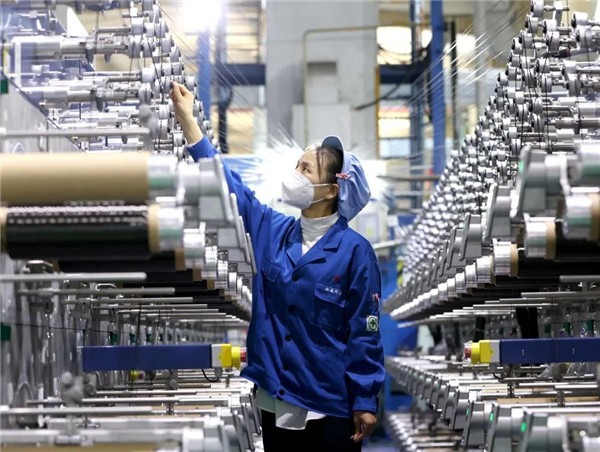
Other production metrics should also be considered when you implement lean production techniques. The ratio of running time to downtime shows how frequently an asset is available for production. It also displays how often planned maintenance is necessary. The quality ratio is an indication of the quality of a supplier's products.
Importantly, you should be aware of potential dangers associated with the "Just In Time." principle. This principle ensures that supplies can be delivered promptly. It also focuses the mind and concentrates on the task at hand. It can also lead to problems within the industry.
FAQ
What are the 7 Rs of logistics?
The acronym 7R's of Logistic is an acronym that stands for seven fundamental principles of logistics management. It was published in 2004 by the International Association of Business Logisticians as part of their "Seven Principles of Logistics Management" series.
The following letters form the acronym:
-
Responsible - to ensure that all actions are within the legal requirements and are not detrimental to others.
-
Reliable: Have faith in your ability or the ability to honor any promises made.
-
Reasonable - make sure you use your resources well and don't waste them.
-
Realistic - consider all aspects of operations, including cost-effectiveness and environmental impact.
-
Respectful - show respect and treat others fairly and fairly
-
Be resourceful: Look for opportunities to save money or increase productivity.
-
Recognizable is a company that provides customers with value-added solutions.
What are the jobs in logistics?
Logistics can offer many different jobs. Here are some examples:
-
Warehouse workers – They load, unload and transport pallets and trucks.
-
Transportation drivers: They drive trucks and trailers and deliver goods and make pick-ups.
-
Freight handlers – They sort and package freight at warehouses.
-
Inventory managers - These are responsible for overseeing the stock of goods in warehouses.
-
Sales representatives: They sell products to customers.
-
Logistics coordinators – They plan and coordinate logistics operations.
-
Purchasing agents are those who purchase goods and services for the company.
-
Customer service representatives - Answer calls and email from customers.
-
Shipping clerks - They process shipping orders and issue bills.
-
Order fillers - These people fill orders based on what has been ordered.
-
Quality control inspectors (QCI) - They inspect all incoming and departing products for potential defects.
-
Others – There are many other types available in logistics. They include transport supervisors, cargo specialists and others.
How can overproduction in manufacturing be reduced?
Improved inventory management is the key to reducing overproduction. This would reduce the amount of time spent on unnecessary activities such as purchasing, storing, and maintaining excess stock. This would allow us to use our resources for more productive tasks.
You can do this by adopting a Kanban method. A Kanban Board is a visual display that tracks work progress. Kanban systems allow work items to move through different states until they reach their final destination. Each state represents a different priority level.
To illustrate, work can move from one stage or another when it is complete enough for it to be moved to a new stage. It is possible to keep a task in the beginning stages until it gets to the end.
This helps to keep work moving forward while ensuring that no work is left behind. With a Kanban board, managers can see exactly how much work is being done at any given moment. This allows them the ability to adjust their workflow using real-time data.
Lean manufacturing is another option to control inventory levels. Lean manufacturing emphasizes eliminating waste in all phases of production. Anything that doesn't add value to the product is considered waste. The following are examples of common waste types:
-
Overproduction
-
Inventory
-
Unnecessary packaging
-
Overstock materials
Manufacturers can reduce their costs and improve their efficiency by using these ideas.
What is the responsibility of a manufacturing manager?
The manufacturing manager should ensure that every manufacturing process is efficient and effective. They must also be alert to any potential problems and take appropriate action.
They should also be able communicate with other departments, such as sales or marketing.
They should be up to date on the latest trends and be able apply this knowledge to increase productivity and efficiency.
How can manufacturing avoid production bottlenecks
Avoiding production bottlenecks is as simple as keeping all processes running smoothly, from the time an order is received until the product ships.
This includes both planning for capacity and quality control.
Continuous improvement techniques such Six Sigma can help you achieve this.
Six Sigma is a management system used to improve quality and reduce waste in every aspect of your organization.
It focuses on eliminating variation and creating consistency in your work.
Statistics
- Job #1 is delivering the ordered product according to specifications: color, size, brand, and quantity. (netsuite.com)
- (2:04) MTO is a production technique wherein products are customized according to customer specifications, and production only starts after an order is received. (oracle.com)
- Many factories witnessed a 30% increase in output due to the shift to electric motors. (en.wikipedia.org)
- You can multiply the result by 100 to get the total percent of monthly overhead. (investopedia.com)
- According to the United Nations Industrial Development Organization (UNIDO), China is the top manufacturer worldwide by 2019 output, producing 28.7% of the total global manufacturing output, followed by the United States, Japan, Germany, and India.[52][53] (en.wikipedia.org)
External Links
How To
Six Sigma: How to Use it in Manufacturing
Six Sigma can be described as "the use of statistical process control (SPC), techniques to achieve continuous improvement." Motorola's Quality Improvement Department in Tokyo, Japan developed Six Sigma in 1986. Six Sigma's basic concept is to improve quality and eliminate defects through standardization. Many companies have adopted Six Sigma in recent years because they believe that there are no perfect products and services. Six Sigma's primary goal is to reduce variation from the average value of production. This means that you can take a sample from your product and then compare its performance to the average to find out how often the process differs from the norm. If you notice a large deviation, then it is time to fix it.
Understanding the nature of variability in your business is the first step to Six Sigma. Once you have this understanding, you will need to identify sources and causes of variation. This will allow you to decide if these variations are random and systematic. Random variations occur when people do mistakes. Symmetrical variations are caused due to factors beyond the process. For example, if you're making widgets, and some of them fall off the assembly line, those would be considered random variations. It would be considered a systematic problem if every widget that you build falls apart at the same location each time.
Once you've identified the problem areas you need to find solutions. That solution might involve changing the way you do things or redesigning the process altogether. After implementing the new changes, you should test them again to see if they worked. If they don’t work, you’ll need to go back and rework the plan.