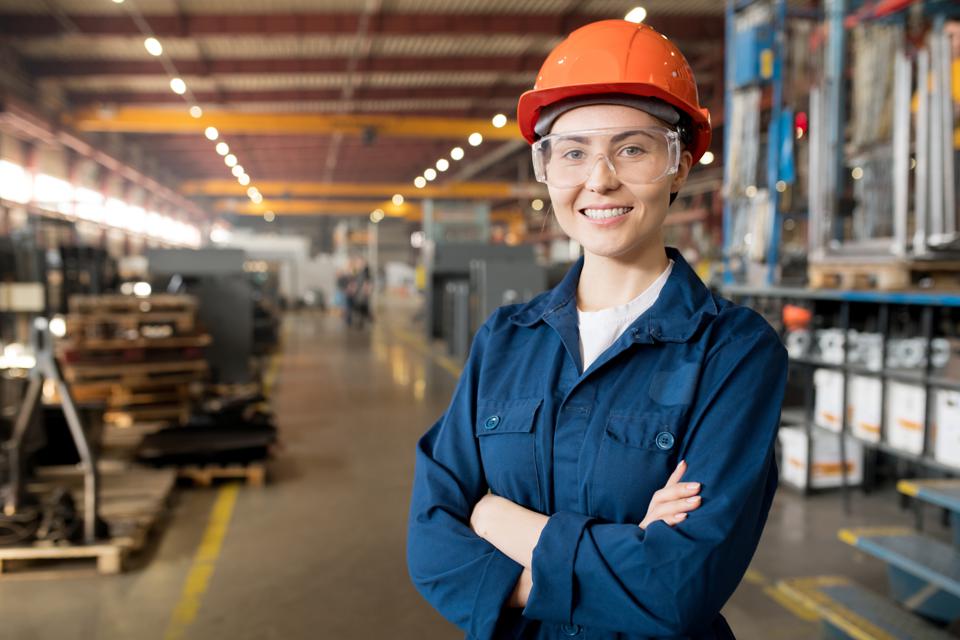
An accurate cost estimate is necessary for nearly every task a company undertakes. They are the cost estimators. They help companies determine the costs of manufacturing and developing new products and services. They also need to assess the cost of building new structures. This includes the analysis of the labor and material costs.
Construction companies employ most cost estimaters. They should have a solid understanding of construction methods and processes. They will also need to be familiarized with computer-aided planning (CAD). This software can improve design and manufacturing efficiency. It is also necessary for cost estimators to be able read data from databases. They can also use Microsoft Excel and other software.
To make accurate cost estimates, cost estimators collaborate with other professionals. To determine the cost of each component, they evaluate the site conditions and project blueprints. They may also work with engineers to determine the gauges and machining operations required.
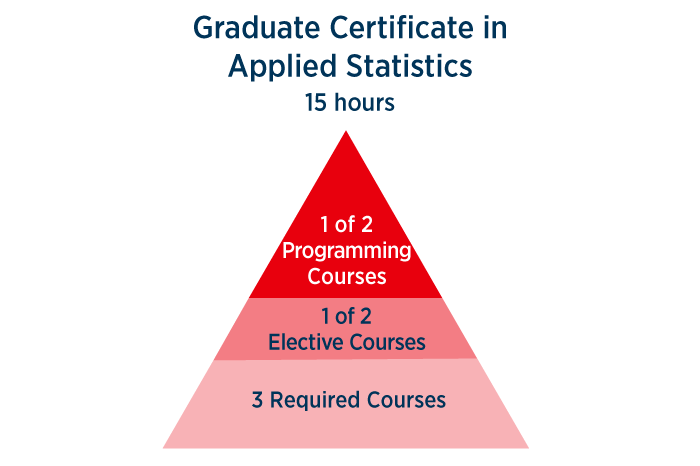
Cost estimators must be meticulous, assertive, and reliable. They must be able and willing to analyse difficult information. They must also be able to present findings accurately and assertively. They must also be able and willing to collaborate with clients and professionals.
Cost estimators are typically assigned to the engineering or cost departments of a company. They should have strong math and science backgrounds. They should be proficient in computer software such as CAD, BIM and commercial. A certification course may be required. Certified Cost Estimator/Analyst(CCEA), Professional cost estimator/Analyst and Certified Professional Estimator are some examples of certifications.
Cost estimators may be skilled in certain services or industries. Some individuals specialize in building or construction costs, while others focus on software development costs. Other areas that cost estimators may be qualified for include automotive repair and maintenance as well as building construction and specialty trade contractors.
The occupation involves communicating with clients, suppliers, and engineers. They are also fluent in industry terminology. They are also able to build a solid knowledge base in order to prepare cost estimates. This occupation is not only responsible for preparing cost estimates but also conducts studies to study the impact of various processes on costs and to find ways to decrease costs.
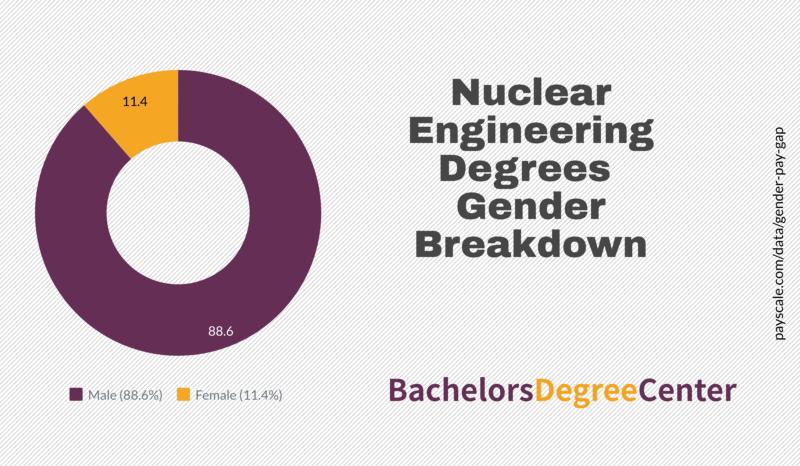
Job applicants might need a bachelor's or master's depending on their industry. They may also require an internship. They can also take advantage of cooperative education programs. Additionally, more construction companies are looking for people with a degree either in building construction or management.
In construction companies and other manufacturing firms, cost estimators are employed. They help companies make accurate estimates that allow them to place profitable bids. In addition, they analyze data related to the supply chain and other factors that affect costs. For government programs, cost estimators are also available. They may also be required to redesign existing products.
Cost estimators should have a good understanding of computer-aided planning (CAD) software. They can also learn how to use automated cost estimation software.
FAQ
Why automate your warehouse
Modern warehouses are increasingly dependent on automation. With the rise of ecommerce, there is a greater demand for faster delivery times as well as more efficient processes.
Warehouses have to be flexible to meet changing requirements. In order to do this, they need to invest in technology. Automating warehouses has many benefits. These are some of the benefits that automation can bring to warehouses:
-
Increases throughput/productivity
-
Reduces errors
-
Improves accuracy
-
Safety enhancements
-
Eliminates bottlenecks
-
Companies can scale more easily
-
Increases efficiency of workers
-
Gives you visibility into all that is happening in your warehouse
-
Enhances customer experience
-
Improves employee satisfaction
-
Reducing downtime and increasing uptime
-
Ensures quality products are delivered on time
-
Eliminates human error
-
It ensures compliance with regulations
How can manufacturing efficiency be improved?
First, determine which factors have the greatest impact on production time. We must then find ways that we can improve these factors. If you don't know where to start, then think about which factor(s) have the biggest impact on production time. Once you have identified the factors, then try to find solutions.
What is meant by manufacturing industries?
Manufacturing Industries are those businesses that make products for sale. The people who buy these products are called consumers. This is accomplished by using a variety of processes, including production, distribution and retailing. They make goods from raw materials with machines and other equipment. This includes all types manufactured goods such as clothing, building materials, furniture, electronics, tools and machinery.
What is the importance of logistics in manufacturing?
Logistics are an essential part of any business. They are essential to any business's success.
Logistics play an important role in reducing costs as well as increasing efficiency.
Statistics
- [54][55] These are the top 50 countries by the total value of manufacturing output in US dollars for its noted year according to World Bank.[56] (en.wikipedia.org)
- In the United States, for example, manufacturing makes up 15% of the economic output. (twi-global.com)
- Job #1 is delivering the ordered product according to specifications: color, size, brand, and quantity. (netsuite.com)
- According to the United Nations Industrial Development Organization (UNIDO), China is the top manufacturer worldwide by 2019 output, producing 28.7% of the total global manufacturing output, followed by the United States, Japan, Germany, and India.[52][53] (en.wikipedia.org)
- In 2021, an estimated 12.1 million Americans work in the manufacturing sector.6 (investopedia.com)
External Links
How To
How to Use the Just In Time Method in Production
Just-in-time is a way to cut costs and increase efficiency in business processes. It is a process where you get the right amount of resources at the right moment when they are needed. This means that only what you use is charged to your account. Frederick Taylor was the first to coin this term. He developed it while working as a foreman during the early 1900s. He saw how overtime was paid to workers for work that was delayed. He realized that workers should have enough time to complete their jobs before they begin work. This would help increase productivity.
JIT teaches you to plan ahead and prepare everything so you don’t waste time. You should also look at the entire project from start to finish and make sure that you have sufficient resources available to deal with any problems that arise during the course of your project. You'll be prepared to handle any potential problems if you know in advance. You won't have to pay more for unnecessary items.
There are many JIT methods.
-
Demand-driven JIT: You order the parts and materials you need for your project every other day. This will allow for you to track the material that you have left after using it. This will allow to you estimate the time it will take for more to be produced.
-
Inventory-based: This type allows you to stock the materials needed for your projects ahead of time. This allows you to predict how much you can expect to sell.
-
Project-driven : This is a method where you make sure that enough money is set aside to pay the project's cost. Knowing how much money you have available will help you purchase the correct amount of materials.
-
Resource-based JIT: This type of JIT is most commonly used. This is where you assign resources based upon demand. If you have many orders, you will assign more people to manage them. If you don’t have many orders you will assign less people to the work.
-
Cost-based: This is a similar approach to resource-based but you are not only concerned with how many people you have, but also how much each one costs.
-
Price-based: This is a variant of cost-based. However, instead of focusing on the individual workers' costs, this looks at the total price of the company.
-
Material-based - This is a variant of cost-based. But instead of looking at the total company cost, you focus on how much raw material you spend per year.
-
Time-based: Another variation of resource-based JIT. Instead of focusing only on how much each employee is costing, you should focus on how long it takes to complete your project.
-
Quality-based JIT: This is another variation of resource based JIT. Instead of focusing on the cost of each worker or how long it takes, think about how high quality your product is.
-
Value-based JIT: This is the latest form of JIT. In this instance, you are not concerned about the product's performance or meeting customer expectations. Instead, your focus is on the value you bring to the market.
-
Stock-based. This method is inventory-based and focuses only on the actual production at any given point. It is used when production goals are met while inventory is kept to a minimum.
-
Just-in time (JIT), planning: This is a combination JIT/supply chain management. It is the process that schedules the delivery of components within a short time of their order. This is important as it reduces lead time and increases throughput.