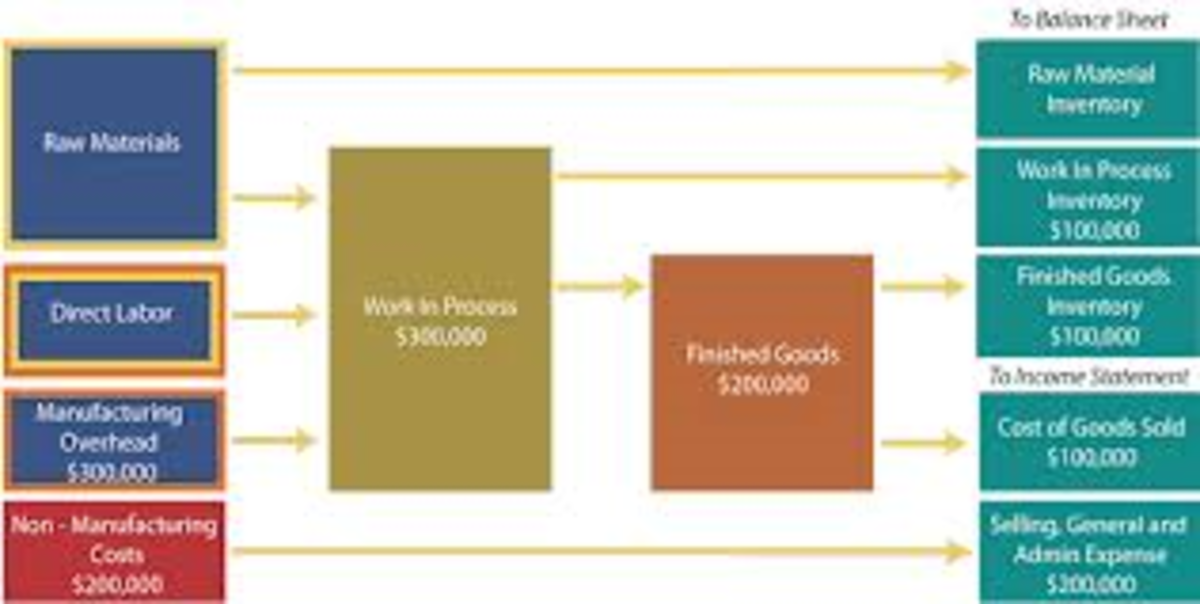
The logistics industry isn't easy, but it can pay off. You are likely searching for the best logistics jobs Miami can offer. There are many reputable companies to choose from, and the best ones aren't hard to find. The most obvious ones include US Logistics Solutions (Medley, FL), Specialized Services Logistics (Miami, FL), and Lineage Logistics (Hialeah, FL). It is not a specialized trucking business as the name suggests, but it is actually a full-service logistics provider. The benefits of a Miami Beach job as a logistics worker include a competitive salary, excellent benefits, and exciting career opportunities. These jobs will not be available all the time. So take this opportunity to get started on your new career. You might also consider hiring a professional resume author or a recruitment agency to help you get in the door.
You should start in the Transportation & Logistics category. Here you will find dozens of jobs and ad samples as well as job fairs. For example, there are two options: an entry-level job at Lineage Logistics in Miami Beach or a full time position at Specialized Services Logistics.
FAQ
How can we increase manufacturing efficiency?
The first step is to determine the key factors that impact production time. Then we need to find ways to improve these factors. You can start by identifying the most important factors that impact production time. Once you have identified them, it is time to identify solutions.
What is the importance of automation in manufacturing?
Automating is not just important for manufacturers, but also for service providers. It allows them provide faster and more efficient services. It reduces human errors and improves productivity, which in turn helps them lower their costs.
What are the four types of manufacturing?
Manufacturing is the process by which raw materials are transformed into useful products through machines and processes. It can involve many activities like designing, manufacturing, testing packaging, shipping, selling and servicing.
What are the 7 R's of logistics?
The acronym "7R's" of Logistics stands for seven principles that underpin logistics management. It was developed by International Association of Business Logisticians (IABL), and published as part of their "Seven Principles of Logistics Management Series" in 2004.
The acronym consists of the following letters:
-
Responsible - ensure that all actions taken are within legal requirements and are not harmful to others.
-
Reliable - have confidence in the ability to deliver on commitments made.
-
Be responsible - Use resources efficiently and avoid wasting them.
-
Realistic – Consider all aspects, including cost-effectiveness as well as environmental impact.
-
Respectful: Treat others with fairness and equity
-
Resourceful - look for opportunities to save money and increase productivity.
-
Recognizable - provide customers with value-added services.
Statistics
- According to a Statista study, U.S. businesses spent $1.63 trillion on logistics in 2019, moving goods from origin to end user through various supply chain network segments. (netsuite.com)
- [54][55] These are the top 50 countries by the total value of manufacturing output in US dollars for its noted year according to World Bank.[56] (en.wikipedia.org)
- (2:04) MTO is a production technique wherein products are customized according to customer specifications, and production only starts after an order is received. (oracle.com)
- In the United States, for example, manufacturing makes up 15% of the economic output. (twi-global.com)
- Many factories witnessed a 30% increase in output due to the shift to electric motors. (en.wikipedia.org)
External Links
How To
How to Use lean manufacturing in the Production of Goods
Lean manufacturing is a management system that aims at increasing efficiency and reducing waste. It was created in Japan by Taiichi Ohno during the 1970s and 80s. He received the Toyota Production System award (TPS), from Kanji Toyoda, founder of TPS. Michael L. Watkins published the "The Machine That Changed the World", the first book about lean manufacturing. It was published in 1990.
Lean manufacturing is often defined as a set of principles used to improve the quality, speed, and cost of products and services. It emphasizes the elimination and minimization of waste in the value stream. The five-steps of Lean Manufacturing are just-in time (JIT), zero defect and total productive maintenance (TPM), as well as 5S. Lean manufacturing seeks to eliminate non-value added activities, such as inspection, work, waiting, and rework.
Lean manufacturing can help companies improve their product quality and reduce costs. Additionally, it helps them achieve their goals more quickly and reduces employee turnover. Lean manufacturing is a great way to manage the entire value chain including customers, suppliers, distributors and retailers as well as employees. Lean manufacturing is widely used in many industries. Toyota's philosophy is a great example of this. It has helped to create success in automobiles as well electronics, appliances and healthcare.
Five fundamental principles underlie lean manufacturing.
-
Define Value - Determine the value that your business brings to society. Also, identify what sets you apart from your competitors.
-
Reduce Waste - Remove any activity which doesn't add value to your supply chain.
-
Create Flow - Ensure work moves smoothly through the process without interruption.
-
Standardize & Simplify - Make processes as consistent and repeatable as possible.
-
Building Relationships – Establish personal relationships with both external and internal stakeholders.
Lean manufacturing isn’t new, but it has seen a renewed interest since 2008 due to the global financial crisis. To increase their competitiveness, many businesses have turned to lean manufacturing. According to some economists, lean manufacturing could be a significant factor in the economic recovery.
Lean manufacturing, which has many benefits, is now a standard practice in the automotive industry. These include better customer satisfaction and lower inventory levels. They also result in lower operating costs.
Lean manufacturing can be applied to almost every aspect of an organization. This is because it ensures efficiency and effectiveness in all stages of the value chain.
There are three main types in lean manufacturing
-
Just-in Time Manufacturing, (JIT): This kind of lean manufacturing is also commonly known as "pull-systems." JIT means that components are assembled at the time of use and not manufactured in advance. This approach aims to reduce lead times, increase the availability of parts, and reduce inventory.
-
Zero Defects Manufacturing: ZDM ensures that no defective units leave the manufacturing plant. Repairing a part that is damaged during assembly should be done, not scrapping. This also applies to finished products that need minor repairs before being shipped.
-
Continuous Improvement (CI),: Continuous improvement aims improve the efficiency and effectiveness of operations by continuously identifying issues and making changes to reduce waste. Continuous improvement refers to continuous improvement of processes as well people and tools.