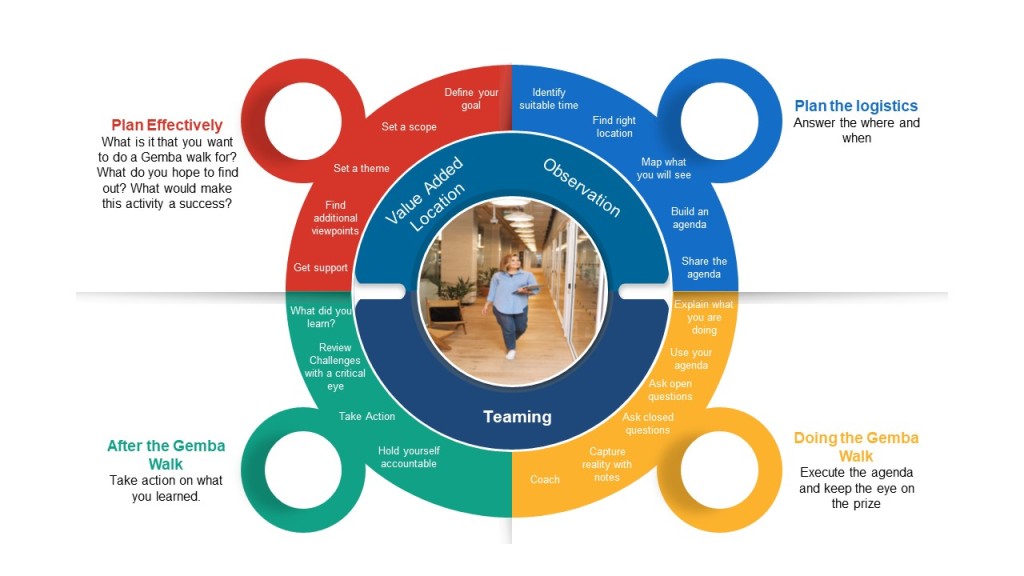
A BLS Mechanical Engineer is a highly sought-after professional with a specialized education and experience in the field of engineering. With years of experience and a strong educational background, they are considered highly selective and can also serve in managerial roles and team leadership roles. There is a good job outlook for this career path over the next 10 years, with a projected 7 percent increase in available positions by 2030, which equates to an additional 20,900 jobs in the job market. Candidates must have some experience with computer-aided simulation and design software.
Duties of the job
A mechanical engineer's job is to plan, design, and develop equipment that uses or produces power. These professionals can also oversee the maintenance, installation, maintenance, and repair machines. These professionals may work for large engineering firms or independently as consultants. They may also design refrigeration systems that freeze foods and air-conditioning system for buildings. Below are data about the wages and employment statistics for mechanical engineers.
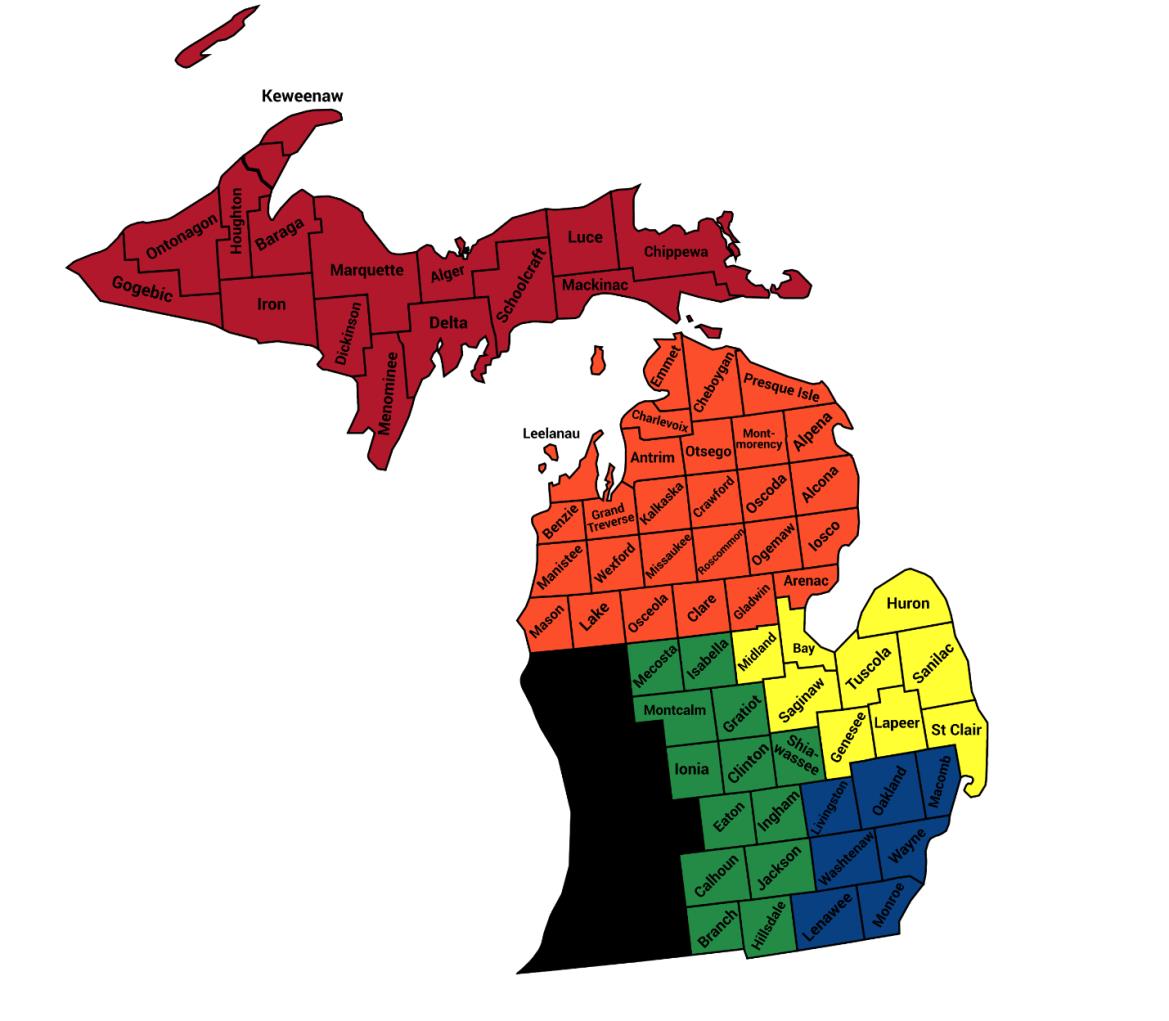
Entry-level mechanical engineers usually work in an administrative environment but may also travel on site to address equipment issues. A strong grasp of basic business principles is essential for this entry-level job. Furthermore, mechanical engineers will frequently use computers so it is important that they have a good understanding of IT and computer science. Strong tech skills are also beneficial for integrating sensors into machinery and analyzing designs.
Education Required
A Bachelor of Science in Mechanical Engineering degree (BSME), may be a great way of getting into mechanical engineering. The degree takes four years and teaches the principles of design and testing as well as manufacturing. Students learn how computer software can be used to create mechanical drawings or other designs. Whether you are interested in the design of airplanes, cars, or other machinery, a BSME will help you find a career in this exciting field.
This field is in good shape according to the BLS. BLS expects that there will be a 4 per cent increase in jobs for mechanical engineering workers between 2019-2029. Some engineers may have the chance to become managers or faculty members in higher education institutions, research and development programs, or both. This profession earns an average of $84,190. The U.S. employment outlook for mechanical engineers is expected to rise faster than the average over the next ten years.
Salary
According to U.S. Bureau of Labor Statistics in 2012, the number of engineers will rise by 5 per cent between 2012 and 2022. While this growth is slower than the average for all occupations, it is still impressive. In a competitive job marketplace, those who stay current on technological advances will have a better chance of succeeding. There are many factors which can impact the salary of an engineer in mechanical engineering.
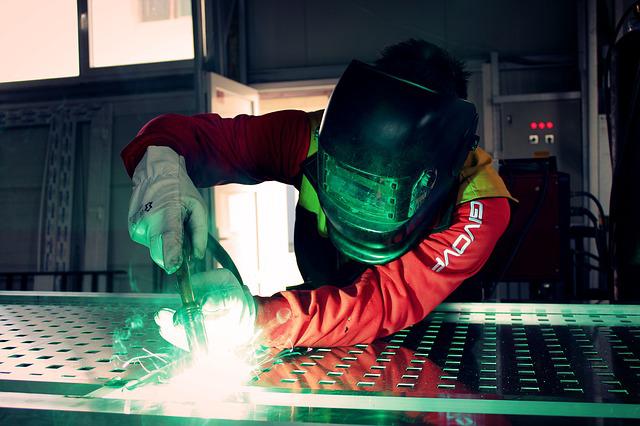
Mechanical engineers make more than the rest of the engineering profession, although there are many factors that can influence salary. In fact, the top 10 percent earned more than $126,430 per year. The highest salaries for mechanical engineers are not only possible but so is a career as a computer and electronic product manufacturer. California, New Mexico, and Alaska have the highest salaries currently for mechanical engineers. These states are ranked by their wage levels, which varies widely depending on experience and education.
FAQ
How can manufacturing excess production be decreased?
Better inventory management is key to reducing excess production. This would reduce time spent on activities such as purchasing, stocking, and maintaining excess stock. This would allow us to use our resources for more productive tasks.
This can be done by using a Kanban system. A Kanbanboard is a visual tool that allows you to keep track of the work being done. Kanban systems are where work items travel through a series of states until reaching their final destination. Each state represents a different priority.
If work is moving from one stage to the other, then the current task can be completed and moved on to the next. If a task is still in its beginning stages, it will continue to be so until it reaches the end.
This allows for work to continue moving forward, while also ensuring that there is no work left behind. Managers can see how much work has been done and the status of each task at any time with a Kanban Board. This information allows them to adjust their workflow based on real-time data.
Lean manufacturing, another method to control inventory levels, is also an option. Lean manufacturing focuses on eliminating waste throughout the entire production chain. Anything that does nothing to add value to a product is waste. The following are examples of common waste types:
-
Overproduction
-
Inventory
-
Unnecessary packaging
-
Material surplus
These ideas can help manufacturers improve efficiency and reduce costs.
What are manufacturing & logistics?
Manufacturing is the act of producing goods from raw materials using machines and processes. Logistics encompasses the management of all aspects associated with supply chain activities such as procurement, production planning, distribution and inventory control. It also includes customer service. Manufacturing and logistics can often be grouped together to describe a larger term that covers both the creation of products, and the delivery of them to customers.
How can manufacturing avoid production bottlenecks
The key to avoiding bottlenecks in production is to keep all processes running smoothly throughout the entire production cycle, from the time you receive an order until the time when the product ships.
This includes planning to meet capacity requirements and quality control.
This can be done by using continuous improvement techniques, such as Six Sigma.
Six Sigma Management System is a method to increase quality and reduce waste throughout your organization.
It is focused on creating consistency and eliminating variation in your work.
What are the four types of manufacturing?
Manufacturing refers the process of turning raw materials into useful products with machines and processes. Manufacturing involves many activities, including designing, building, testing and packaging, shipping, selling, service, and so on.
Statistics
- In 2021, an estimated 12.1 million Americans work in the manufacturing sector.6 (investopedia.com)
- It's estimated that 10.8% of the U.S. GDP in 2020 was contributed to manufacturing. (investopedia.com)
- (2:04) MTO is a production technique wherein products are customized according to customer specifications, and production only starts after an order is received. (oracle.com)
- Many factories witnessed a 30% increase in output due to the shift to electric motors. (en.wikipedia.org)
- According to a Statista study, U.S. businesses spent $1.63 trillion on logistics in 2019, moving goods from origin to end user through various supply chain network segments. (netsuite.com)
External Links
How To
How to Use Just-In-Time Production
Just-in-time is a way to cut costs and increase efficiency in business processes. It's a way to ensure that you get the right resources at just the right time. This means that you only pay the amount you actually use. The term was first coined by Frederick Taylor, who developed his theory while working as a foreman in the early 1900s. Taylor observed that overtime was paid to workers if they were late in working. He concluded that if workers were given enough time before they start work, productivity would increase.
The idea behind JIT is that you should plan ahead and have everything ready so you don't waste money. Look at your entire project, from start to end. Make sure you have enough resources in place to deal with any unexpected problems. You can anticipate problems and have enough equipment and people available to fix them. You won't have to pay more for unnecessary items.
There are several types of JIT techniques:
-
Demand-driven JIT: This is a JIT that allows you to regularly order the parts/materials necessary for your project. This will enable you to keep track of how much material is left after you use it. You'll also be able to estimate how long it will take to produce more.
-
Inventory-based: This type allows you to stock the materials needed for your projects ahead of time. This allows for you to anticipate how much you can sell.
-
Project-driven: This is an approach where you set aside enough funds to cover the cost of your project. When you know how much you need, you'll purchase the appropriate amount of materials.
-
Resource-based JIT: This type of JIT is most commonly used. You assign certain resources based off demand. You will, for example, assign more staff to deal with large orders. If there aren't many orders, you will assign fewer people.
-
Cost-based: This is similar to resource-based, except that here you're not just concerned about how many people you have but how much each person costs.
-
Price-based: This is a variant of cost-based. However, instead of focusing on the individual workers' costs, this looks at the total price of the company.
-
Material-based - This is a variant of cost-based. But instead of looking at the total company cost, you focus on how much raw material you spend per year.
-
Time-based JIT: A variation on resource-based JIT. Instead of focusing on the cost of each employee, you will focus on the time it takes to complete a project.
-
Quality-based: This is yet another variation of resource-based JIT. Instead of thinking about the cost of each employee or the time it takes to produce something, you focus on how good your product quality.
-
Value-based JIT: One of the most recent forms of JIT. In this instance, you are not concerned about the product's performance or meeting customer expectations. Instead, your goal is to add value to the market.
-
Stock-based. This method is inventory-based and focuses only on the actual production at any given point. This method is useful when you want to increase production while decreasing inventory.
-
Just-intime planning (JIT), is a combination JIT/sales chain management. It refers to the process of scheduling the delivery of components as soon as they are ordered. It's important as it reduces leadtimes and increases throughput.