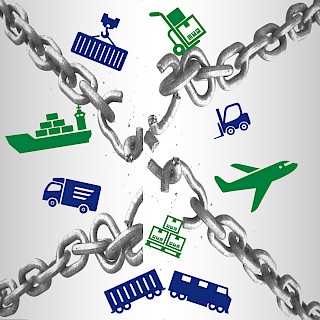
Murata Manufacturing Co. Ltd., located in Kyoto, Japan, is an excellent option if you're searching for electronics component manufacturers. From the name alone, you'll know that the company has been around for more than 100 years. There are other companies you should know about. Here are their products and services. This company produces electronic parts that can be used in many different kinds of electronics.
Murata Manufacturing Co., Ltd.
Murata Manufacturing Co., Ltd., Japan's leading electronic component manufacturer, is based out of Kyoto, Japan. It manufactures electronic components like circuit boards, transistors and LEDs. Learn more about the company and its products. Also read on to learn how Murata manufactures its products. In addition, you can view some of Murata's most popular products. Visit Murata’s site for more information.
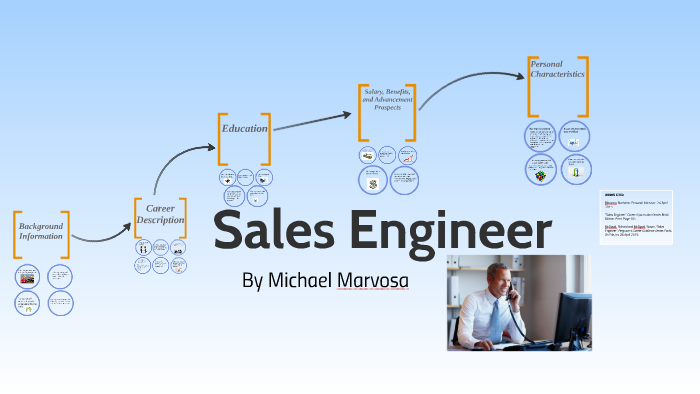
Murata Energy Device Singapore Pte Ltd
The company's acronym stands for "Making Primary Charge Batteries." This company is a subsidiary to the Japanese Murata Manufacturing Co. Ltd. which is located in Nagaokakyo. Murata Singapore was established in 1972 and is the first Murata factory to be opened outside of Japan. Its mission, is to fulfill the South East Asia electronics market demand. Murata acquired Sony Energy Devices Corporation, in 2017. The headquarters are located at 1 Tuas Road Singapore.
Murata Electronics Trading (Tianjin) Co. Ltd
Since 2007, Murata Elektrons Trading Company has been operating in Tianjin (China) as MEC. MEC is originally from Japan. It focuses its efforts on supplying high quality electronic parts to global markets. The company has been expanding its business to include the sale of components that reduce EMI over the last few years. It also has technical support services that help solve customers' EMC problems.
Murata Vios
Murata Vios, an innovative medical technology is being introduced to hospital floors. Japanese company is developing a system to detect signs of early clinical decline. It is wireless and can be used in conjunction with Hicuity Health. This company provides clinical oversight and engages specialists to respond to patient deterioration. Murata Vios combines these two technologies to offer a new service for care providers and clinicians.
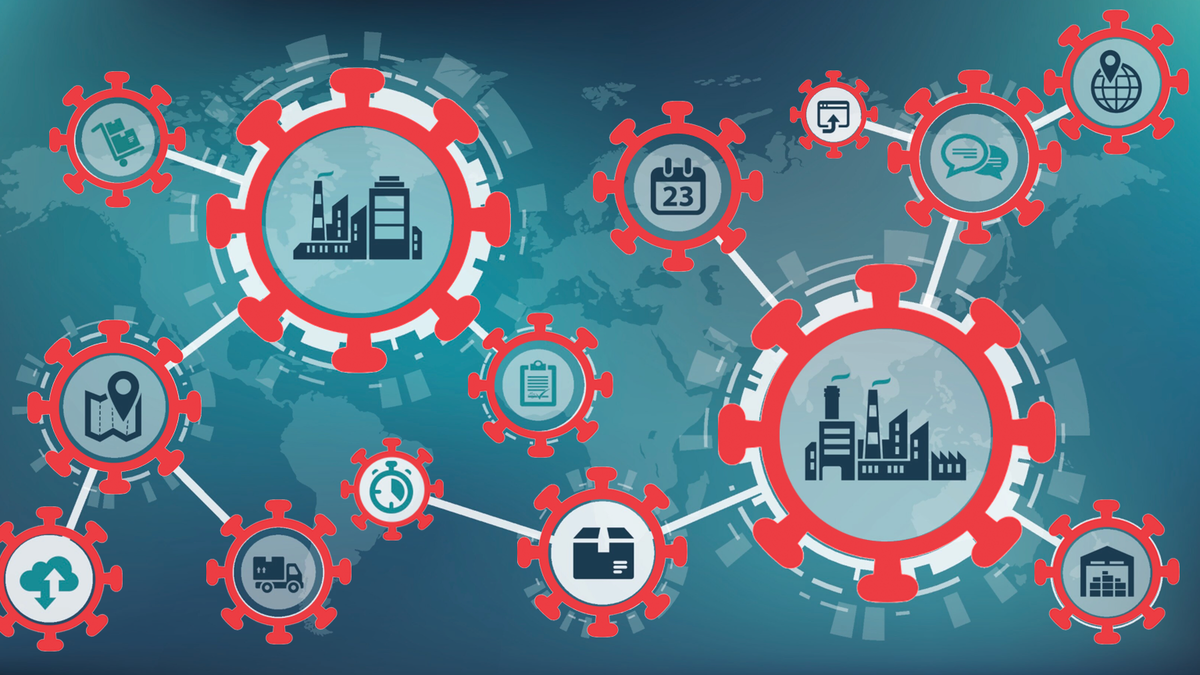
Integration of Murata Vios with PointClickCare
The Vios Monitoring System from Murata, Inc. has recently integrated with PointClickCare, a cloud-based senior care software vendor. This integration reduces transcription errors and data entry delays and improves clinician efficiency. Vios Monitoring System gathers information such as heart beat, oxygen levels, pulse rate, respiratory rate, and posture data. These data are important in order to implement a patient-centric healthcare plan.
FAQ
What are the four types of manufacturing?
Manufacturing is the process of transforming raw materials into useful products using machines and processes. It includes many different activities like designing, building and testing, packaging, shipping and selling, as well as servicing.
Why automate your warehouse?
Modern warehousing has seen automation take center stage. E-commerce has brought increased demand for more efficient and quicker delivery times.
Warehouses should be able adapt quickly to new needs. Technology investment is necessary to enable warehouses to respond quickly to changing demands. Automating warehouses is a great way to save money. Here are some reasons why it's worth investing in automation:
-
Increases throughput/productivity
-
Reduces errors
-
Improves accuracy
-
Boosts safety
-
Eliminates bottlenecks
-
Companies can scale more easily
-
It makes workers more efficient
-
It gives visibility to everything that happens inside the warehouse
-
Enhances customer experience
-
Improves employee satisfaction
-
Reduces downtime and improves uptime
-
You can be sure that high-quality products will arrive on time
-
Eliminates human error
-
Helps ensure compliance with regulations
How can we reduce manufacturing overproduction?
Improved inventory management is the key to reducing overproduction. This would decrease the time that is spent on inefficient activities like purchasing, storing, or maintaining excess stock. This could help us free up our time for other productive tasks.
A Kanban system is one way to achieve this. A Kanban board, a visual display to show the progress of work, is called a Kanban board. In a Kanban system, work items move through a sequence of states until they reach their final destination. Each state represents a different priority level.
To illustrate, work can move from one stage or another when it is complete enough for it to be moved to a new stage. It is possible to keep a task in the beginning stages until it gets to the end.
This allows for work to continue moving forward, while also ensuring that there is no work left behind. Managers can monitor the work being done by Kanban boards to see what is happening at any given time. This allows them the ability to adjust their workflow using real-time data.
Lean manufacturing can also be used to reduce inventory levels. Lean manufacturing is about eliminating waste from all stages of the production process. Anything that doesn't add value to the product is considered waste. The following are examples of common waste types:
-
Overproduction
-
Inventory
-
Unnecessary packaging
-
Material surplus
These ideas can help manufacturers improve efficiency and reduce costs.
What are the 7 Rs of logistics.
The acronym 7Rs of Logistics refers to the seven core principles of logistics management. It was created by the International Association of Business Logisticians and published in 2004 under its "Seven Principles of Logistics Management".
The acronym is made up of the following letters:
-
Responsible - to ensure that all actions are within the legal requirements and are not detrimental to others.
-
Reliable - Have confidence in your ability to fulfill all of your commitments.
-
Be responsible - Use resources efficiently and avoid wasting them.
-
Realistic – Consider all aspects, including cost-effectiveness as well as environmental impact.
-
Respectful – Treat others fairly and equitably.
-
Reliable - Find ways to save money and increase your productivity.
-
Recognizable - Provide value-added services to customers
Can some manufacturing processes be automated?
Yes! Since ancient times, automation has been in existence. The Egyptians discovered the wheel thousands and years ago. To help us build assembly lines, we now have robots.
There are many uses of robotics today in manufacturing. These include:
-
Assembly line robots
-
Robot welding
-
Robot painting
-
Robotics inspection
-
Robots that produce products
There are many other examples of how manufacturing could benefit from automation. For example, 3D printing allows us to make custom products without having to wait for weeks or months to get them manufactured.
Statistics
- According to a Statista study, U.S. businesses spent $1.63 trillion on logistics in 2019, moving goods from origin to end user through various supply chain network segments. (netsuite.com)
- In 2021, an estimated 12.1 million Americans work in the manufacturing sector.6 (investopedia.com)
- (2:04) MTO is a production technique wherein products are customized according to customer specifications, and production only starts after an order is received. (oracle.com)
- [54][55] These are the top 50 countries by the total value of manufacturing output in US dollars for its noted year according to World Bank.[56] (en.wikipedia.org)
- In the United States, for example, manufacturing makes up 15% of the economic output. (twi-global.com)
External Links
How To
How to Use Just-In-Time Production
Just-in time (JIT), is a process that reduces costs and increases efficiency in business operations. It allows you to get the right amount resources at the right time. This means you only pay what you use. Frederick Taylor was the first to coin this term. He developed it while working as a foreman during the early 1900s. He noticed that workers were often paid overtime when they had to work late. He concluded that if workers were given enough time before they start work, productivity would increase.
JIT is a way to plan ahead and make sure you don't waste any money. It is important to look at your entire project from beginning to end and ensure that you have enough resources to handle any issues that may arise. If you expect problems to arise, you will be able to provide the necessary equipment and personnel to address them. This will ensure that you don't spend more money on things that aren't necessary.
There are many JIT methods.
-
Demand-driven JIT: This is a JIT that allows you to regularly order the parts/materials necessary for your project. This will enable you to keep track of how much material is left after you use it. This will allow to you estimate the time it will take for more to be produced.
-
Inventory-based: You stock materials in advance to make your projects easier. This allows you to forecast how much you will sell.
-
Project-driven: This approach involves setting aside sufficient funds to cover your project's costs. Once you have an idea of how much material you will need, you can purchase the necessary materials.
-
Resource-based JIT : This is probably the most popular type of JIT. This is where you assign resources based upon demand. You might assign more people to help with orders if there are many. If you don't receive many orders, then you'll assign fewer employees to handle the load.
-
Cost-based: This approach is very similar to resource-based. However, you don't just care about the number of people you have; you also need to consider how much each person will cost.
-
Price-based: This is similar to cost-based but instead of looking at individual workers' salaries, you look at the total company price.
-
Material-based: This approach is similar to cost-based. However, instead of looking at the total cost for the company, you look at how much you spend on average on raw materials.
-
Time-based JIT: A variation on resource-based JIT. Instead of worrying about how much each worker costs, you can focus on how long the project takes.
-
Quality-based JIT: Another variation on resource-based JIT. Instead of looking at the labor costs and time it takes to make a product, think about its quality.
-
Value-based JIT is the newest form of JIT. In this scenario, you're not concerned about how products perform or whether customers expect them to meet their expectations. Instead, you are focused on adding value to the marketplace.
-
Stock-based: This stock-based method focuses on the actual quantity of products being made at any given time. This method is useful when you want to increase production while decreasing inventory.
-
Just-in-time (JIT) planning: This is a combination of JIT and supply chain management. It is the process that schedules the delivery of components within a short time of their order. It's important because it reduces lead times and increases throughput.