
Industrial management is an engineering field where different engineering processes are integrated in order to create a management system. These engineering processes are integrated into an integrated management system by the industrial manager. These are the basics of your job. Here are the requirements and benefits of becoming an industrial manager. If you are looking for a challenging but rewarding career, this could be the career for your. Continue reading to learn about the career.
Job description
An industrial manager oversees all aspects of the production process. The job can cover every aspect of the production process but will also be responsible for sourcing raw materials and implementing equipment. Industrial production managers should be computer-literate as computers are becoming increasingly important in the coordination of departments, suppliers, vendors, and clients. Industrial production managers must also be familiar with the latest production technologies as well as management practices. Managers are often involved in professional organizations and attend trade shows and industry conferences. They also take courses to become certified in their fields.
In addition to overseeing manufacturing processes, industrial managers coordinate the activities of various departments within a company. They make sure production lines run smoothly and meet customers' time and quality requirements. They also oversee the staffing levels and make changes to production levels if necessary to reduce inventory. They might also coordinate with other departments and oversee quality control programs. A majority of this role involves managing people, which includes identifying, training, and motivating employees.
Education Required
A bachelor's degree is not required to be an industrial manager. Some employers prefer candidates with a background or education in these areas. Industrial managers also need to be computer literate. Computers have become an integral part in manufacturing. They can help coordinate production between departments as well as suppliers and clients. Interested individuals should obtain the proper education and experience to excel in this field.
Many industrial production managers start their career as production workers and advance to first-line supervisory positions. Most professionals need to have a college degree or equivalent in business management to be able to move up to the position of industrial manager. Some entry-level workers might be able to get this education while on the job or through classes sponsored by their employers. Managers are expected to have at least two to five years' experience in the relevant field before they can become managers.
Earning potential
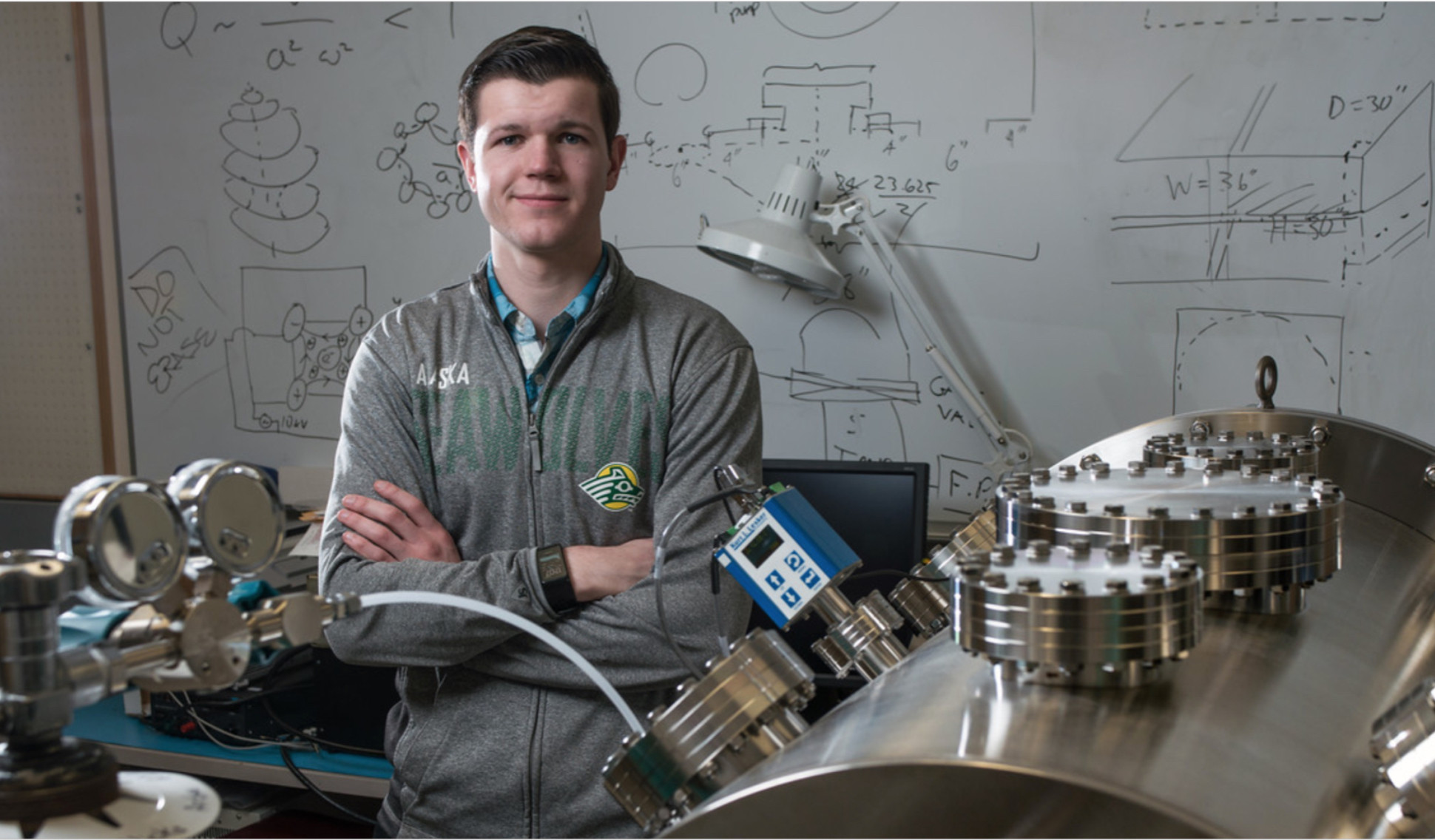
The industrial managers are responsible for overseeing the smooth running of manufacturing plants. They decide how to best utilize employees and equipment, meet production standards, and make strategic decisions. Their responsibilities include hiring, evaluating, and setting production times, and making sure safety procedures are adhered to. They oversee the day to day activities of a group of workers and analyze the production process continuously to ensure that it runs efficiently and at its peak efficiency.
The employer's experience and the earnings potential of industrial production managers will affect their earning potential. While it's difficult to predict the future earnings of industrial managers, the average salary in May 2016 was $103,380, with the highest paid industrial production managers earning $172,150 annually. Also, higher earnings are possible for industrial production managers who have had advanced training and certification. According to the U.S. Bureau of Labor Statistics industrial production managers who have earned a bachelor’s degree or higher could earn more.
Work environment
A manager of industrial production divides their time between the production floor or an office. Sometimes, they live in the same building. When they work in a production zone, industrial production managers need to adhere to safety and health guidelines and use appropriate protective equipment. They often spend significant time in meetings and analysis of production data. They may also be responsible for writing reports. A manager of industrial production often works in a dynamic environment.
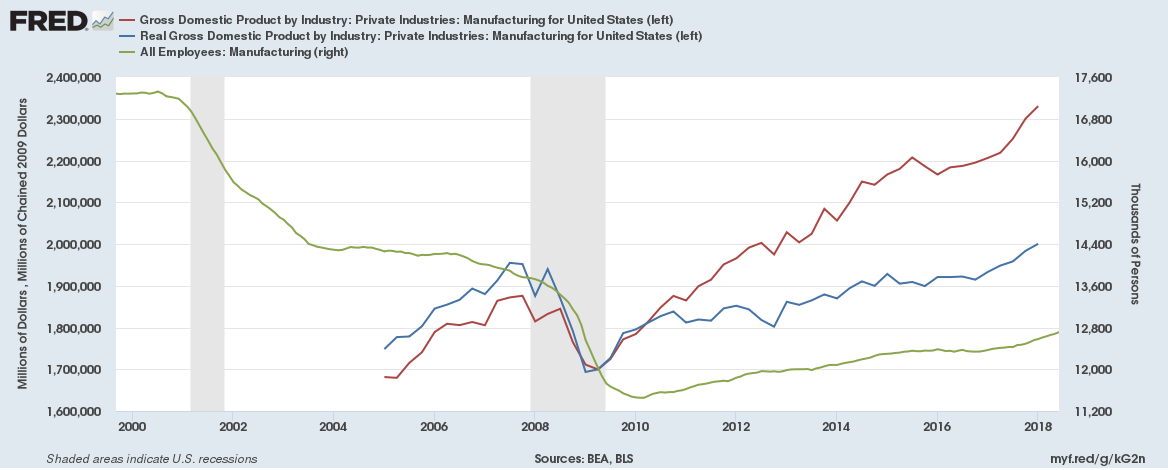
Industrial production managers are an integral part of the business's management structure. They have many responsibilities. They must coordinate the activities of various workers and increase productivity. A manager of industrial production is responsible for increasing productivity and safety. Corporate restructuring has seen many levels of management eliminated and support staff cut, which means that production managers have more to do. This is a serious challenge for any manager and can make the job of a production manager difficult.
FAQ
How does manufacturing avoid bottlenecks in production?
You can avoid bottlenecks in production by making sure that everything runs smoothly throughout the production cycle, from the moment you receive an order to the moment the product is shipped.
This includes both planning for capacity and quality control.
Continuous improvement techniques like Six Sigma are the best way to achieve this.
Six Sigma can be used to improve the quality and decrease waste in all areas of your company.
It emphasizes consistency and eliminating variance in your work.
What is the responsibility of a production planner?
A production planner makes sure all project elements are delivered on schedule, within budget, as well as within the agreed scope. They also ensure the quality of the product and service meets the client's requirements.
What does it take to run a logistics business?
It takes a lot of skills and knowledge to run a successful logistics business. For clients and suppliers to be successful, you need to have excellent communication skills. You will need to know how to interpret data and draw conclusions. You must be able to work well under pressure and handle stressful situations. To increase efficiency and creativity, you need to be creative. Strong leadership qualities are essential to motivate your team and help them achieve their organizational goals.
To meet tight deadlines, you must also be efficient and organized.
Statistics
- Many factories witnessed a 30% increase in output due to the shift to electric motors. (en.wikipedia.org)
- You can multiply the result by 100 to get the total percent of monthly overhead. (investopedia.com)
- It's estimated that 10.8% of the U.S. GDP in 2020 was contributed to manufacturing. (investopedia.com)
- According to the United Nations Industrial Development Organization (UNIDO), China is the top manufacturer worldwide by 2019 output, producing 28.7% of the total global manufacturing output, followed by the United States, Japan, Germany, and India.[52][53] (en.wikipedia.org)
- Job #1 is delivering the ordered product according to specifications: color, size, brand, and quantity. (netsuite.com)
External Links
How To
How to use 5S to increase Productivity in Manufacturing
5S stands to stand for "Sort", “Set In Order", “Standardize", and "Store". Toyota Motor Corporation was the first to develop the 5S approach in 1954. It assists companies in improving their work environments and achieving higher efficiency.
The basic idea behind this method is to standardize production processes, so they become repeatable, measurable, and predictable. Cleaning, sorting and packing are all done daily. These actions allow workers to perform their job more efficiently, knowing what to expect.
There are five steps to implementing 5S, including Sort, Set In Order, Standardize, Separate and Store. Each step involves a different action which leads to increased efficiency. Sorting things makes it easier to find them later. You arrange items by placing them in an order. After you have divided your inventory into groups you can store them in easy-to-reach containers. Finally, when you label your containers, you ensure everything is labeled correctly.
Employees need to reflect on how they do their jobs. Employees need to be able understand their motivations and discover alternative ways to do them. To implement the 5S system, employees must acquire new skills and techniques.
The 5S method increases efficiency and morale among employees. They will feel motivated to strive for higher levels of efficiency once they start to see results.