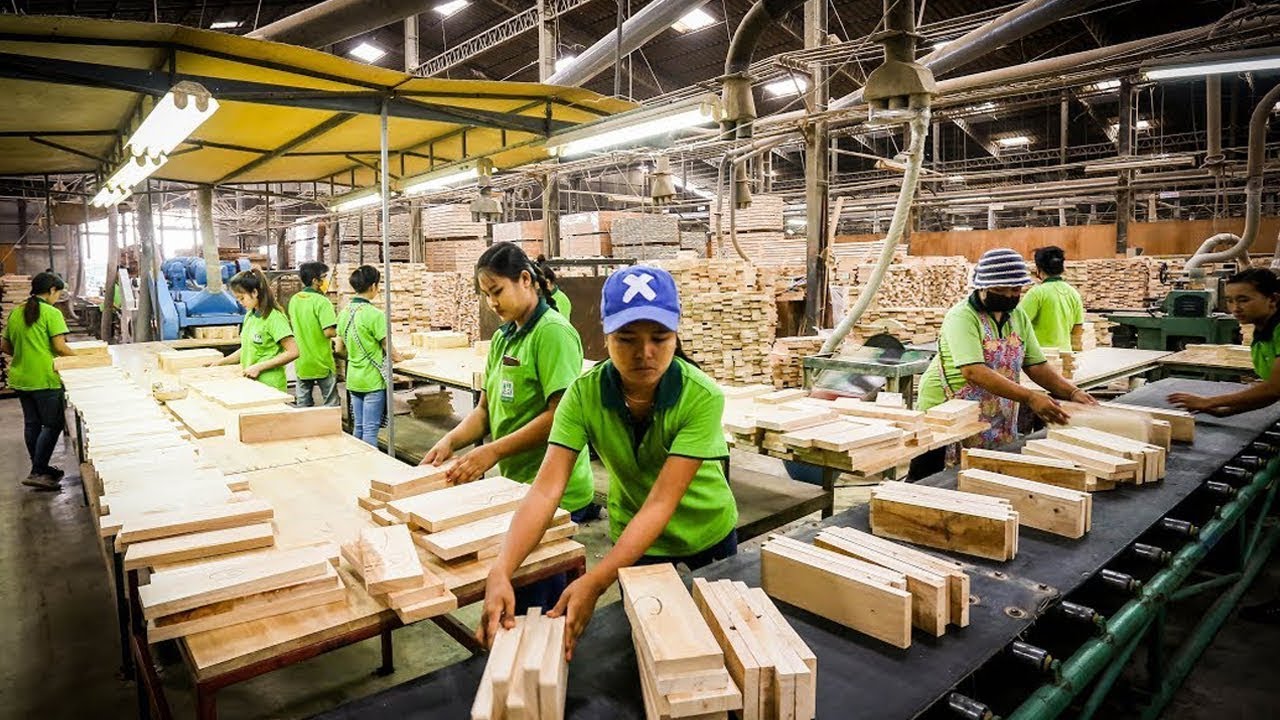
A drafter is someone who has a good understanding of technical details and can translate designs into drawings. They must also be able work well with others to achieve the best results. They may also need to learn how to read engineering plans and how to work with specific software programs. They might also need an understanding of engineering formulas that can be used to calculate measurement.
Most drafters work in engineering and architectural firms. They create plans for buildings, structures, and other products using computer-aided design (CAD) software. While they often work alone on projects, these professionals also work in teams to create new designs. Although they are often full-time workers, they can also take on other jobs. They may need to work overtime depending upon the company they work for.
Most drafters get an associate's or technical degree from a community college. They can then continue their education with a 4-year program at a university. The course they choose may allow them to transfer their degree to a bachelor’s degree.
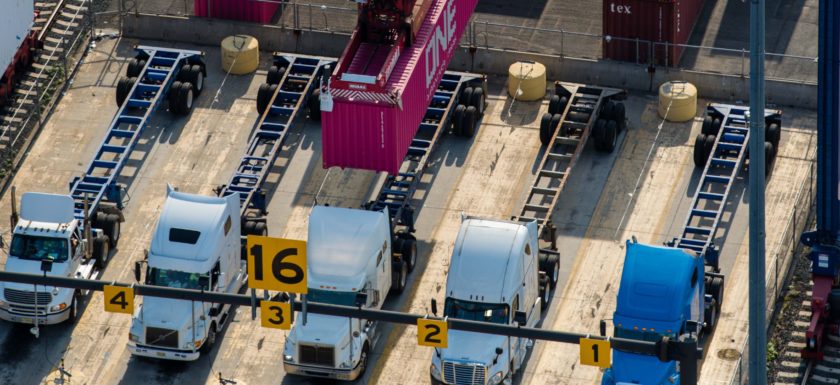
Drafters might need to have more than a degree in drafting. For practical experience, they might be asked to work as interns at a company. This experience can help drafters land a job. A portfolio may be requested to show their drafting skills.
A certification is also available to drafters. American Design Drafting Association (ADDA), offers certification exams that assess drafting knowledge. These tests are designed to test geometric designs and tolerating. Many certifications are valid three years. Candidates will need to take new exams. The ADDA provides certification in many areas of drafting.
Most drafters work in engineering, construction, or manufacturing. They can also work in factories and with electricals. Some drafters work more hours than 40 hours per work week. They should also know how to manage their time and use computer-aided design (CAD).
Drafters can profit from the growing use of technology in order to increase their efficiency. For a company to stay competitive, drafters will need to have a good understanding of CAD and other software programs. A master's degree may be an option for anyone who is interested in drafting. Those with a master's degree will have an edge over other candidates when it comes to getting hired. They will be better qualified to give technical information to clients.
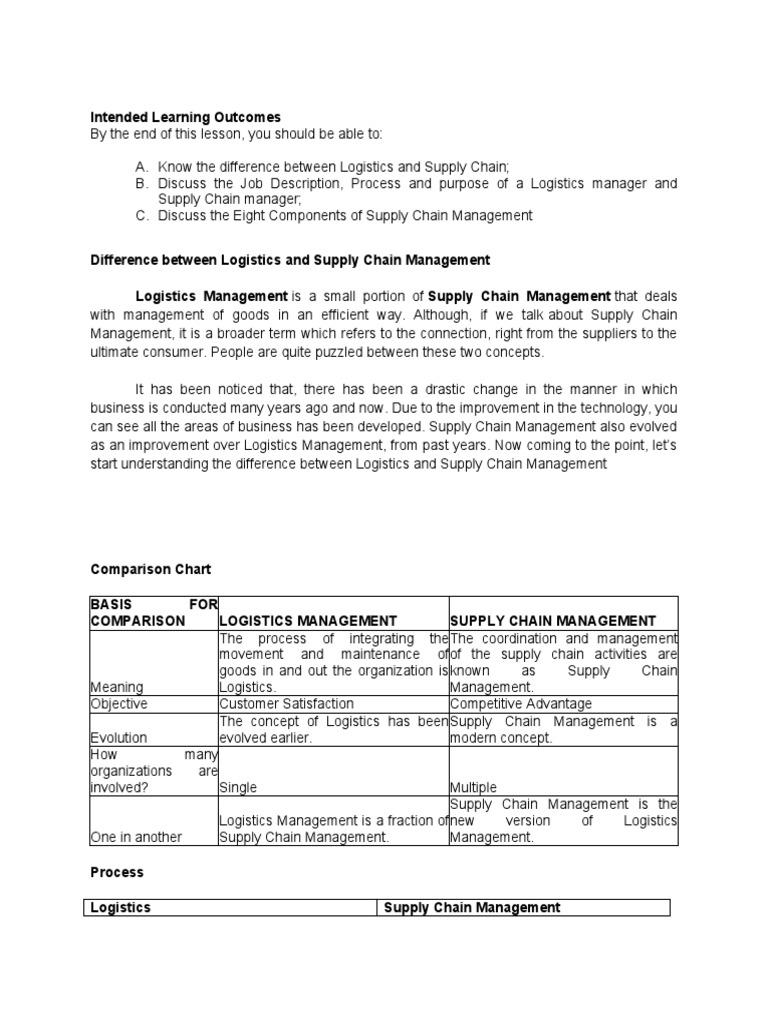
Drafters could also serve as assistants to professional drafting professionals. Volunteers may be available to help out with community projects. Before you sign up for courses, make sure you know what kind of projects you are interested. Some clients prefer pencil sketches while others prefer computer-generated designs.
Draft technicians can gain practical experience after graduating high school. They can enroll in drafting classes at technical institutes to get professional experience. They should also be aware of computer and math classes.
FAQ
What is the role and responsibility of a Production Planner?
A production planner ensures all aspects of the project are delivered on time, within budget, and within scope. They ensure that the product or service is of high quality and meets client requirements.
How can manufacturing overproduction be reduced?
It is essential to find better ways to manage inventory to reduce overproduction. This would reduce the time needed to manage inventory. This will allow us to free up resources for more productive tasks.
This can be done by using a Kanban system. A Kanban board is a visual display used to track work in progress. Kanban systems are where work items travel through a series of states until reaching their final destination. Each state has a different priority level.
If work is moving from one stage to the other, then the current task can be completed and moved on to the next. It is possible to keep a task in the beginning stages until it gets to the end.
This allows for work to continue moving forward, while also ensuring that there is no work left behind. Managers can view the Kanban board to see how much work they have done. This information allows managers to adjust their workflow based off real-time data.
Lean manufacturing is another option to control inventory levels. Lean manufacturing focuses on eliminating waste throughout the entire production chain. Anything that doesn't add value to the product is considered waste. Some common types of waste include:
-
Overproduction
-
Inventory
-
Unnecessary packaging
-
Exceed materials
These ideas can help manufacturers improve efficiency and reduce costs.
What is it like to manage a logistics company?
It takes a lot of skills and knowledge to run a successful logistics business. Good communication skills are essential to effectively communicate with your suppliers and clients. You must be able analyze data and draw out conclusions. You need to be able work under pressure and manage stressful situations. In order to innovate and create new ways to improve efficiency, creativity is essential. You need to have strong leadership qualities to motivate team members and direct them towards achieving organizational goals.
It is also important to be efficient and well organized in order meet deadlines.
What are the responsibilities of a logistic manager?
Logistics managers ensure that goods arrive on time and are unharmed. This is accomplished by using the experience and knowledge gained from working with company products. He/she must also ensure sufficient stock to meet the demand.
How can manufacturing reduce production bottlenecks?
You can avoid bottlenecks in production by making sure that everything runs smoothly throughout the production cycle, from the moment you receive an order to the moment the product is shipped.
This includes planning for both capacity requirements and quality control measures.
Continuous improvement techniques such Six Sigma can help you achieve this.
Six Sigma management is a system that improves quality and reduces waste within your organization.
It seeks to eliminate variation and create consistency in your work.
Statistics
- Many factories witnessed a 30% increase in output due to the shift to electric motors. (en.wikipedia.org)
- According to the United Nations Industrial Development Organization (UNIDO), China is the top manufacturer worldwide by 2019 output, producing 28.7% of the total global manufacturing output, followed by the United States, Japan, Germany, and India.[52][53] (en.wikipedia.org)
- According to a Statista study, U.S. businesses spent $1.63 trillion on logistics in 2019, moving goods from origin to end user through various supply chain network segments. (netsuite.com)
- [54][55] These are the top 50 countries by the total value of manufacturing output in US dollars for its noted year according to World Bank.[56] (en.wikipedia.org)
- Job #1 is delivering the ordered product according to specifications: color, size, brand, and quantity. (netsuite.com)
External Links
How To
Six Sigma in Manufacturing
Six Sigma is defined as "the application of statistical process control (SPC) techniques to achieve continuous improvement." It was developed by Motorola's Quality Improvement Department at their plant in Tokyo, Japan, in 1986. Six Sigma's main goal is to improve process quality by standardizing processes and eliminating defects. In recent years, many companies have adopted this method because they believe there is no such thing as perfect products or services. Six Sigma seeks to reduce variation between the mean production value. This means that if you take a sample of your product, then measure its performance against the average, you can find out what percentage of the time the process deviates from the norm. If there is a significant deviation from the norm, you will know that something needs to change.
Understanding the nature of variability in your business is the first step to Six Sigma. Once you've understood that, you'll want to identify sources of variation. This will allow you to decide if these variations are random and systematic. Random variations occur when people do mistakes. Symmetrical variations are caused due to factors beyond the process. These are, for instance, random variations that occur when widgets are made and some fall off the production line. If however, you notice that each time you assemble a widget it falls apart in exactly the same spot, that is a problem.
Once you've identified the problem areas you need to find solutions. You might need to change the way you work or completely redesign the process. After implementing the new changes, you should test them again to see if they worked. If they don't work you need to rework them and come up a better plan.