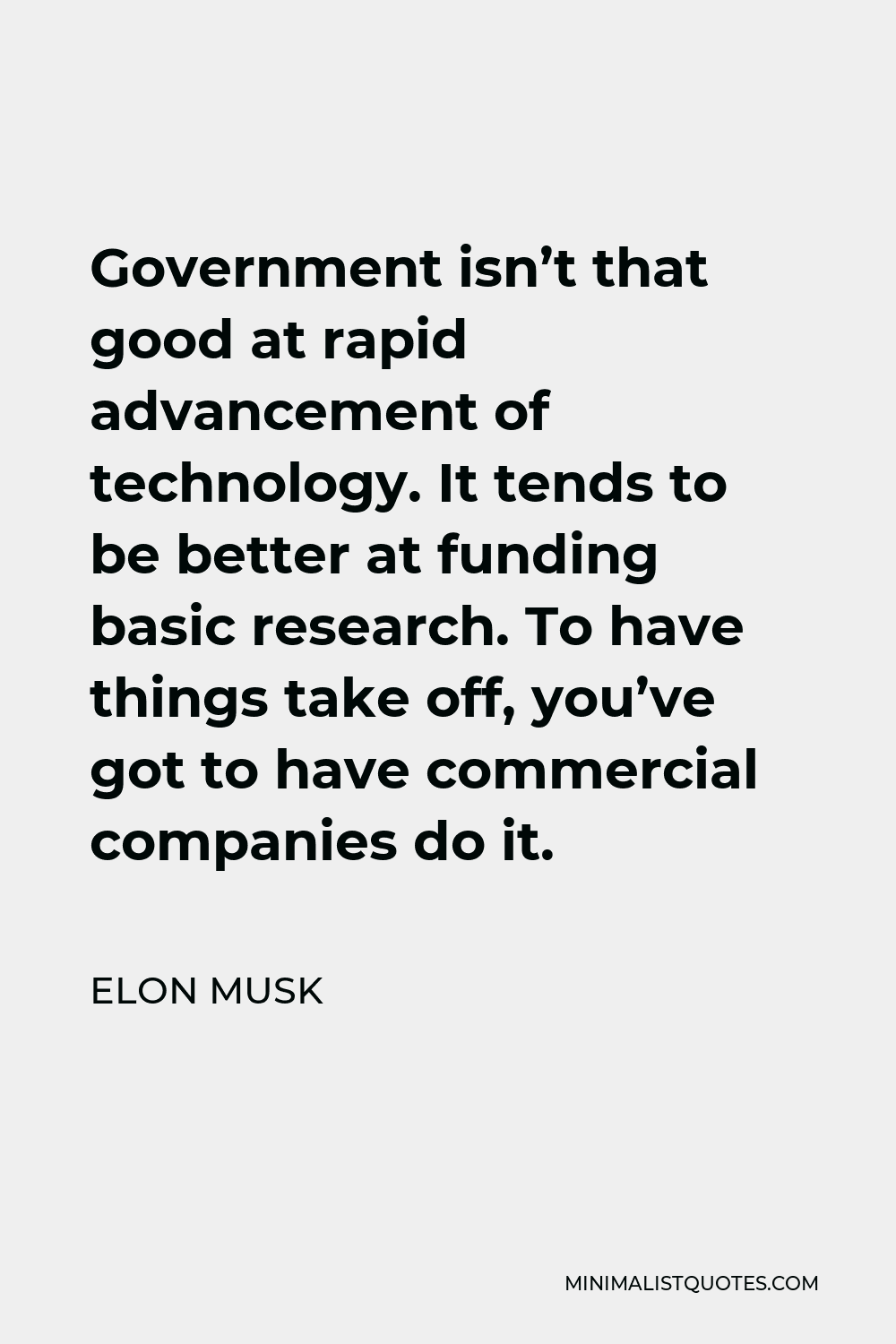
The Bureau Labor Statistics, an agency of the Department of Labor that collects, analyzes, elucidates and disseminates critical economic information, was established in 1884. It conducts research and analyses on a variety of economic issues including labor demand, prices and employment. The agency also publishes statistical reports, and provides training on labor statistics to other countries.
Bureau Labor Statistics surveys the labor force to monitor and adjust wages and employment. It produces detailed industry estimates of nonfarm employment and wage rates. It also produces a Consumer Price Index that measures the prices for common consumer goods. It also measures economic changes such as transport, housing, education, or medical care.
BLS publishes data regarding employment and wages for the United States as well as several other areas. These data are often cited by economists, businessmen, and market participants. The Bureau also produces statistical charts that provide more detail on economic conditions. The Consumer Price Index (the most important) is the main report. Other economic data produced by the Bureau include the Producers Price Index as well as the Employment Situation Report.
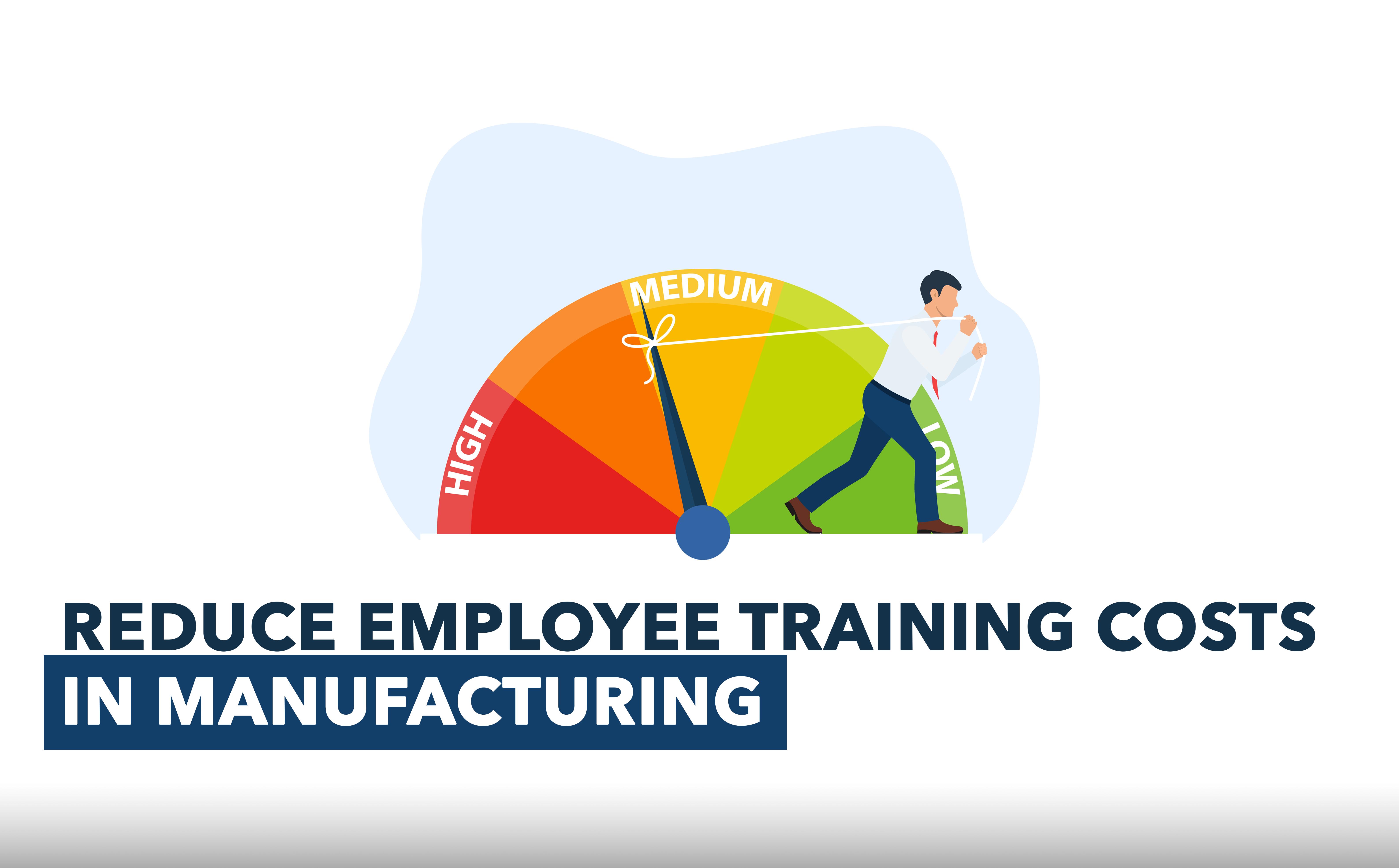
The Bureau of Labor Statistics does research on the employment of older Americans, teens, and women. It also compiles data about worker fatalities as well as non-fatal workplace injury. It also provides data files about low-wage labor. The Bureau also researches foreign-owned enterprises that have at minimum 10% of their stock owned abroad.
The Bureau also provides information on the national unemployment rate, which is derived from the Current Population Survey. It also publishes additional surveys. Current Employment Statistics (CES), which surveys 670,000 work sites, is available. BLS also does research on the number businesses and labor organisations in the country.
The Bureau also publishes the Employment and Earnings report, which provides a national outlook of the labor market. This report includes information about the national unemployment rate and total employment. It also provides information about wages and employment growth. The Bureau also publishes a list highlighting the most rapidly-growing jobs. The Bureau also offers listings of high-wage jobs.
The Bureau has a large staff and six regional offices. The Bureau also maintains several smaller local offices.
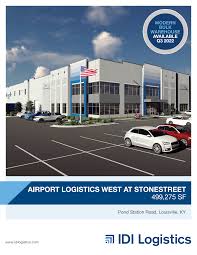
The Bureau also publishes many reports, including a National Compensation Survey. The National Compensation Survey is one of the largest data gathering programs in the United States. This program compiles data on the average earnings and hours worked by employees across all industries. These data are then compiled into an industry specific average. For many industries, it is also published quarterly. You can also find the Occupational Perspective Quarterly which gives analysis of the labor markets for specific occupations.
The Bureau also operates an Office of Prices and Living Conditions. This office measures the economic impact of price changes. The Producer Price Index and Consumer Price Index is produced by the Office of Prices and Living Conditions. It also provides information on import and exported prices.
FAQ
What does it mean to be a manufacturer?
Manufacturing Industries is a group of businesses that produce goods for sale. Consumers are the people who purchase these products. These companies use various processes such as production, distribution, retailing, management, etc., to fulfill this purpose. These companies produce goods using raw materials and other equipment. This includes all types of manufactured goods, including food items, clothing, building supplies, furniture, toys, electronics, tools, machinery, vehicles, pharmaceuticals, medical devices, chemicals, and many others.
Why is logistics important in manufacturing
Logistics is an integral part of every business. They enable you to achieve outstanding results by helping manage product flow from raw materials through to finished goods.
Logistics play an important role in reducing costs as well as increasing efficiency.
What is the responsibility for a logistics manager
Logistics managers are responsible for ensuring that all goods arrive in perfect condition and on time. This is achieved by using their knowledge and experience with the products of the company. He/she also needs to ensure adequate stock to meet demand.
What skills does a production planner need?
Being a production planner is not easy. You need to be organized and flexible. It is also important to be able communicate with colleagues and clients.
Statistics
- You can multiply the result by 100 to get the total percent of monthly overhead. (investopedia.com)
- Many factories witnessed a 30% increase in output due to the shift to electric motors. (en.wikipedia.org)
- [54][55] These are the top 50 countries by the total value of manufacturing output in US dollars for its noted year according to World Bank.[56] (en.wikipedia.org)
- (2:04) MTO is a production technique wherein products are customized according to customer specifications, and production only starts after an order is received. (oracle.com)
- Job #1 is delivering the ordered product according to specifications: color, size, brand, and quantity. (netsuite.com)
External Links
How To
Six Sigma and Manufacturing
Six Sigma can be described as "the use of statistical process control (SPC), techniques to achieve continuous improvement." It was developed by Motorola's Quality Improvement Department at their plant in Tokyo, Japan, in 1986. The basic idea behind Six Sigma is to improve quality by improving processes through standardization and eliminating defects. In recent years, many companies have adopted this method because they believe there is no such thing as perfect products or services. Six Sigma's main objective is to reduce variations from the production average. This means that if you take a sample of your product, then measure its performance against the average, you can find out what percentage of the time the process deviates from the norm. If there is a significant deviation from the norm, you will know that something needs to change.
The first step toward implementing Six Sigma is understanding how variability works in your business. Once you understand that, it is time to identify the sources of variation. Also, you will need to identify the sources of variation. Random variations occur when people do mistakes. Symmetrical variations are caused due to factors beyond the process. You could consider random variations if some widgets fall off the assembly lines. If however, you notice that each time you assemble a widget it falls apart in exactly the same spot, that is a problem.
Once you identify the problem areas, it is time to create solutions. That solution might involve changing the way you do things or redesigning the process altogether. Test them again once you've implemented the changes. If they don’t work, you’ll need to go back and rework the plan.