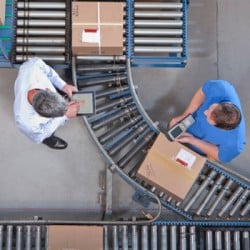
Toyota Motor Manufacturing Indiana Inc. in Gibson County is the first Toyota facility to be fully owned by Toyota in America. It produces Toyota's full-size pickup trucks including the Avalon, Corolla and Corolla as well as the Sienna minivan. The Toyota RAV4 Hybrid is also produced here, making it the most popular hybrid Toyota has ever made.
The original plan was to produce the Toyota Highlander. However, the plant was moved to Gibson County in Indiana. Since 2011, the plant has produced Toyota's RAV4 Hybrid compact SUV, and Lexus ES 350. Toyota spent more that $1.33billion at the plant in 2017.
Toyota Safety Sense 2.5+ features automatic emergency braking and is also produced at this plant. The plant also prepares all of the new 2018 Camry models. This new model has a new transmission and more power. It also features a stylish design. It will cost $25,900
Toyota's Camry production is the largest in America. It is currently the best selling midsize sedan in America, and has been for 15 years. Toyota has manufactured 10 million Camrys in Kentucky. The hybrid model is being manufactured in the plant's first production facility in North America.
Toyota Production System is a collection practices and techniques that increase quality and efficiency. The Toyota Production Engineering and Manufacturing Center is part of this system, and it will house 600 Toyota engineers. The center will be the first to produce hydrogen fuel cell modules suitable for heavy-duty commercial trucks. The facility can produce as many as 100,000 vehicles annually.
Toyota has spent $1.5 billion on the plant in the last five year. The plant has also been home to 700 additional employees. This investment will create 470,100 jobs in the United States by 2020. Toyota has invested more than $147million in Kentucky-based nonprofit partners since 1986.
The Toyota Camry is a reliable vehicle that is also highly stylish. It uses the GA-K platform and a new transmission. It is fun to drive. Consumer Reports highlighted Toyota Camry's popularity as one of America’s top-selling cars in July.
Toyota's production system has many elements. These include continuous improvement, just in-time parts delivery and a sophisticated robotic welding machine. Toyota's Kentucky Investments in Kentucky have been well demonstrated by its Toyota Production Engineering and Manufacturing Center.
Toyota's new production hall design saves on construction and cooling costs. The building also features a Visitor Center, which includes interactive video displays and exhibits on hybrid technology. Toyota will manufacture up to 2 million vehicles in North America over 10 years. This is the largest Toyota facility outside Japan.
Toyota's New Global Architecture is a big step in improving the company's production system. This strategy includes a new engine and production organization, as well as a module that unifies vehicle components. The new design retains Toyota's innovative spirit while reflecting Toyota's traditional values.
FAQ
What's the difference between Production Planning & Scheduling?
Production Planning (PP) is the process of determining what needs to be produced at any given point in time. Forecasting and identifying production capacity are two key elements to this process.
Scheduling refers the process by which tasks are assigned dates so that they can all be completed within the given timeframe.
What is the responsibility for a logistics manager
Logistics managers make sure all goods are delivered on schedule and without damage. This is achieved by using their knowledge and experience with the products of the company. He/she should ensure that sufficient stock is available in order to meet customer demand.
What are the requirements to start a logistics business?
To be a successful businessman in logistics, you will need many skills and knowledge. Good communication skills are essential to effectively communicate with your suppliers and clients. You will need to know how to interpret data and draw conclusions. You will need to be able handle pressure well and work in stressful situations. You need to be innovative and creative to come up with new ways to increase efficiency. You must be a strong leader to motivate others and direct them to achieve organizational goals.
It is important to be organized and efficient in order to meet tight deadlines.
Are there any Manufacturing Processes that we should know before we can learn about Logistics?
No. No. But, being familiar with manufacturing processes will give you a better understanding about how logistics works.
What are the four types in manufacturing?
Manufacturing refers the process of turning raw materials into useful products with machines and processes. It includes many different activities like designing, building and testing, packaging, shipping and selling, as well as servicing.
How can manufacturing excess production be decreased?
It is essential to find better ways to manage inventory to reduce overproduction. This would reduce time spent on activities such as purchasing, stocking, and maintaining excess stock. This could help us free up our time for other productive tasks.
This can be done by using a Kanban system. A Kanban board, a visual display to show the progress of work, is called a Kanban board. In a Kanban system, work items move through a sequence of states until they reach their final destination. Each state represents a different priority level.
When work is completed, it can be transferred to the next stage. However, if a task is still at the beginning stages, it will remain so until it reaches the end of the process.
This allows for work to continue moving forward, while also ensuring that there is no work left behind. Managers can see how much work has been done and the status of each task at any time with a Kanban Board. This allows them the ability to adjust their workflow using real-time data.
Lean manufacturing is another option to control inventory levels. Lean manufacturing emphasizes eliminating waste in all phases of production. Anything that doesn't add value to the product is considered waste. The following are examples of common waste types:
-
Overproduction
-
Inventory
-
Unnecessary packaging
-
Materials in excess
These ideas can help manufacturers improve efficiency and reduce costs.
What is the responsibility of a manufacturing manager?
The manufacturing manager should ensure that every manufacturing process is efficient and effective. They should be aware of any issues within the company and respond accordingly.
They should also learn how to communicate effectively with other departments, including sales and marketing.
They should be up to date on the latest trends and be able apply this knowledge to increase productivity and efficiency.
Statistics
- In 2021, an estimated 12.1 million Americans work in the manufacturing sector.6 (investopedia.com)
- According to a Statista study, U.S. businesses spent $1.63 trillion on logistics in 2019, moving goods from origin to end user through various supply chain network segments. (netsuite.com)
- Many factories witnessed a 30% increase in output due to the shift to electric motors. (en.wikipedia.org)
- (2:04) MTO is a production technique wherein products are customized according to customer specifications, and production only starts after an order is received. (oracle.com)
- Job #1 is delivering the ordered product according to specifications: color, size, brand, and quantity. (netsuite.com)
External Links
How To
How to Use lean manufacturing in the Production of Goods
Lean manufacturing is a management style that aims to increase efficiency and reduce waste through continuous improvement. It was developed by Taiichi Okono in Japan, during the 1970s & 1980s. TPS founder Kanji Takoda awarded him the Toyota Production System Award (TPS). The first book published on lean manufacturing was titled "The Machine That Changed the World" written by Michael L. Watkins and published in 1990.
Lean manufacturing is often described as a set if principles that help improve the quality and speed of products and services. It emphasizes the elimination of defects and waste throughout the value stream. Lean manufacturing is called just-in-time (JIT), zero defect, total productive maintenance (TPM), or 5S. Lean manufacturing seeks to eliminate non-value added activities, such as inspection, work, waiting, and rework.
Lean manufacturing is a way for companies to achieve their goals faster, improve product quality, and lower costs. Lean manufacturing can be used to manage all aspects of the value chain. Customers, suppliers, distributors, retailers and employees are all included. Lean manufacturing can be found in many industries. Toyota's philosophy has been a key driver of success in many industries, including automobiles and electronics.
Lean manufacturing is based on five principles:
-
Define Value: Identify the social value of your business and what sets you apart.
-
Reduce Waste – Eliminate all activities that don't add value throughout the supply chain.
-
Create Flow - Make sure work runs smoothly without interruptions.
-
Standardize & simplify - Make processes consistent and repeatable.
-
Build Relationships - Establish personal relationships with both internal and external stakeholders.
Although lean manufacturing has always been around, it is gaining popularity in recent years because of a renewed interest for the economy after 2008's global financial crisis. Many companies have adopted lean manufacturing methods to increase their marketability. Economists think that lean manufacturing is a crucial factor in economic recovery.
Lean manufacturing is now becoming a common practice in the automotive industry, with many benefits. These include improved customer satisfaction, reduced inventory levels, lower operating costs, increased productivity, and better overall safety.
Lean manufacturing can be applied to almost every aspect of an organization. This is because it ensures efficiency and effectiveness in all stages of the value chain.
There are three main types of lean manufacturing:
-
Just-in-Time Manufacturing (JIT): This type of lean manufacturing is commonly referred to as "pull systems." JIT stands for a system where components are assembled on the spot rather than being made in advance. This method reduces lead times, increases availability, and decreases inventory.
-
Zero Defects Manufacturing: ZDM ensures that no defective units leave the manufacturing plant. If a part is required to be repaired on the assembly line, it should not be scrapped. This is true even for finished products that only require minor repairs prior to shipping.
-
Continuous Improvement (CI), also known as Continuous Improvement, aims at improving the efficiency of operations through continuous identification and improvement to minimize or eliminate waste. Continuous improvement involves continuous improvement of processes and people as well as tools.