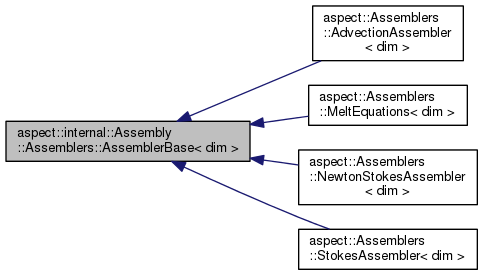
The United States is the third largest manufacturer in the world, and its manufacturing output hit a record high in Q1 2018 at $2.00 trillion, nearly double the amount before the Great Recession. The United States' manufacturing sector is not taking the right approach to its challenges despite a strong economy. This is either due to a lack in investment or a shortage of skilled labor. We must be more aggressive in confronting the challenges that face our industry.
The number of jobs has declined by 5,000,000 since 2000
The US has lost five million manufacturing jobs since 2000. Some believe the increase in trade with China is to blame, but this explains only about a fourth of the decline in manufacturing jobs. Manufacturing jobs were also lost in countries that couldn't compete with Chinese imports. However, there are many reasons that manufacturing jobs have been declining. The following are some of the reasons:
The US manufacturing sector has lost almost a third of its jobs over the past 20 years. It was 17,000,000 in 1965. It dropped to just 12,000,000 in 2010. Trade is not responsible for the decline in manufacturing jobs. However, it has been caused structural problems like a decline of capital investment, output, and productivity. These problems are not sustainable. Although productivity gains played a significant role in the decline of manufacturing jobs, they were not enough to compensate. The problem is automation, not productivity gains.
Strong demand for manufactured goods
Despite the decline in consumer spending, the US still has a strong demand to manufacture goods. In 1945, 58% of personal spending on durable goods was made, while it is now only 28%. The reason is that the price of making and selling these goods has fallen while their content has increased. Therefore, computers, televisions, as well as sound equipment, have experienced a dramatic drop in cost.
The US has experienced a rebound in manufacturing activity which has helped boost the production of manufactured products. According to the Fifth District Manufacturing Activity Survey (Fifth District Manufacturing Activity Survey), demand is strong for manufactured goods, and production is on the rise. However supply chain bottlenecks are hindering output. Increased production has put pressure on supply chains. Many respondents reported experiencing supply chain disruptions that have affected their ability to keep necessary inventories. Backlogs in orders have increased and so has the time it takes for vendors to respond.
Trade deficit in manufactured goods has more than doubled in the past decade
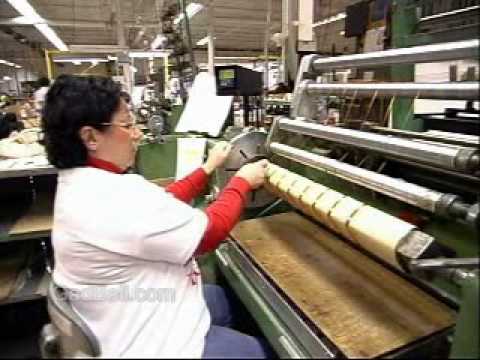
Economists worry that the U.S. will have a lower level of global growth and cause more instability among its trading counterparts. However, high imports from the USA of manufactured goods is not necessarily a problem for the U.S. economy. It is crucial to maintaining economic stability worldwide. Trade deficits may be an inevitable evil since the U.S. is heavily dependent on foreign markets to generate its economy. This may make it more difficult to achieve full employment.
The U.S. trade deficit with China in manufactured goods has almost doubled since 2000. Partly, this is due to an increase in Chinese imports. The problem is even more severe: this imbalance is concentrated at the manufacturing sector, where wages are down and employment is declining since the 1990s. As a result, US manufacturing employment has fallen dramatically from 26 percent in 1970 to 8.5 percent in 2016. Some economists attribute China's increasing competition to the decline, but most blame the decline on automation, productivity increases and the shifting of consumer demand away form goods to services.
Industry follows a shotgun approach
While the US manufacturing sector has a number of advanced manufacturing projects and is well-established, other countries are using a single-shot approach for bringing the internet to manufacturing. The US, on the other hand, focuses on diverse technologies and combines Internet advertising with traditional mass media. The result is a shotgun approach. Companies focus on many technologies and target a broad client base.
FAQ
What are the 4 types manufacturing?
Manufacturing is the process of transforming raw materials into useful products using machines and processes. Manufacturing involves many activities, including designing, building, testing and packaging, shipping, selling, service, and so on.
How can manufacturing excess production be decreased?
It is essential to find better ways to manage inventory to reduce overproduction. This would reduce the time spent on unproductive activities like purchasing, storing and maintaining excess stock. This could help us free up our time for other productive tasks.
You can do this by adopting a Kanban method. A Kanban Board is a visual display that tracks work progress. A Kanban system allows work items to move through several states before reaching their final destination. Each state has a different priority level.
For instance, when work moves from one stage to another, the current task is complete enough to be moved to the next stage. However, if a task is still at the beginning stages, it will remain so until it reaches the end of the process.
This allows work to move forward and ensures that no work is missed. Managers can view the Kanban board to see how much work they have done. This data allows them adjust their workflow based upon real-time data.
Another way to control inventory levels is to implement lean manufacturing. Lean manufacturing is about eliminating waste from all stages of the production process. Anything that doesn't add value to the product is considered waste. Here are some examples of common types.
-
Overproduction
-
Inventory
-
Packaging not required
-
Exceed materials
Manufacturers can increase efficiency and decrease costs by implementing these ideas.
Why automate your warehouse?
Modern warehousing is becoming more automated. The rise of e-commerce has led to increased demand for faster delivery times and more efficient processes.
Warehouses have to be flexible to meet changing requirements. Technology is essential for warehouses to be able to adapt quickly to changing needs. The benefits of automating warehouses are numerous. Here are some benefits of investing in automation
-
Increases throughput/productivity
-
Reduces errors
-
Increases accuracy
-
Safety is boosted
-
Eliminates bottlenecks
-
Allows companies scale more easily
-
It makes workers more efficient
-
The warehouse can be viewed from all angles.
-
Enhances customer experience
-
Improves employee satisfaction
-
It reduces downtime, and increases uptime
-
You can be sure that high-quality products will arrive on time
-
Removes human error
-
This helps to ensure compliance with regulations
Statistics
- (2:04) MTO is a production technique wherein products are customized according to customer specifications, and production only starts after an order is received. (oracle.com)
- You can multiply the result by 100 to get the total percent of monthly overhead. (investopedia.com)
- Job #1 is delivering the ordered product according to specifications: color, size, brand, and quantity. (netsuite.com)
- [54][55] These are the top 50 countries by the total value of manufacturing output in US dollars for its noted year according to World Bank.[56] (en.wikipedia.org)
- According to a Statista study, U.S. businesses spent $1.63 trillion on logistics in 2019, moving goods from origin to end user through various supply chain network segments. (netsuite.com)
External Links
How To
How to use 5S to increase Productivity in Manufacturing
5S stands as "Sort", Set In Order", Standardize", Separate" and "Store". Toyota Motor Corporation created the 5S methodology in 1954. It allows companies to improve their work environment, thereby achieving greater efficiency.
This approach aims to standardize production procedures, making them predictable, repeatable, and easily measurable. This means that every day tasks such cleaning, sorting/storing, packing, and labeling can be performed. This knowledge allows workers to be more efficient in their work because they are aware of what to expect.
Implementing 5S involves five steps: Sort, Set in Order, Standardize Separate, Store, and Each step requires a different action, which increases efficiency. If you sort items, it makes them easier to find later. When you set items in an order, you put items together. Then, after you separate your inventory into groups, you store those groups in containers that are easy to access. Finally, label all containers correctly.
This process requires employees to think critically about how they do their job. Employees should understand why they do the tasks they do, and then decide if there are better ways to accomplish them. They will need to develop new skills and techniques in order for the 5S system to be implemented.
The 5S method increases efficiency and morale among employees. They will feel motivated to strive for higher levels of efficiency once they start to see results.