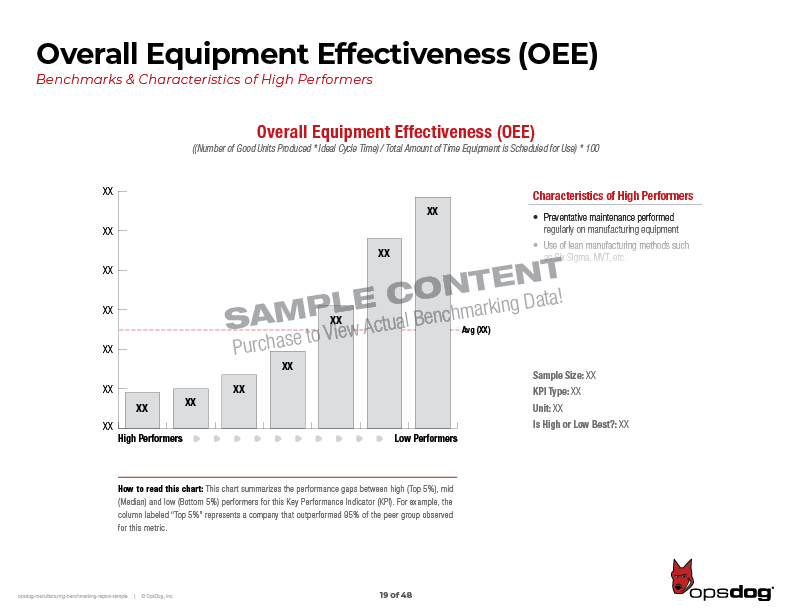
Chemical manufacturing is an important industry in America that transforms organic raw materials into useful products. It supplies consumer goods and materials for industries ranging from plastics to explosives. The chemical industry faces many challenges. Numerous workers are at high risk for health and safety.
The two main areas of chemical manufacturing are commodity chemicals and specialty chemicals. These two groups share the same infrastructure, utilities, production processes, and other resources. However, the types of products are different. Specialty chemical are often designed to be used by customers. Specialty producers produce some of most expensive chemicals. Many of these chemicals are protected under patents.
Although some chemicals are produced in a single location, most petrochemicals and commodity chemicals are produced in large-scale facilities. For example, large-scale chemical plants are located in Texas, Louisiana, and Rotterdam in the Netherlands. Large-scale chemical plants often share utilities, infrastructures, and create economies of scale.
The United States is the second-largest chemical manufacturer in the world behind China. Statista says that the industry generates more than $4 trillion annually. About half the industry's revenues are generated by the top 50 US businesses.
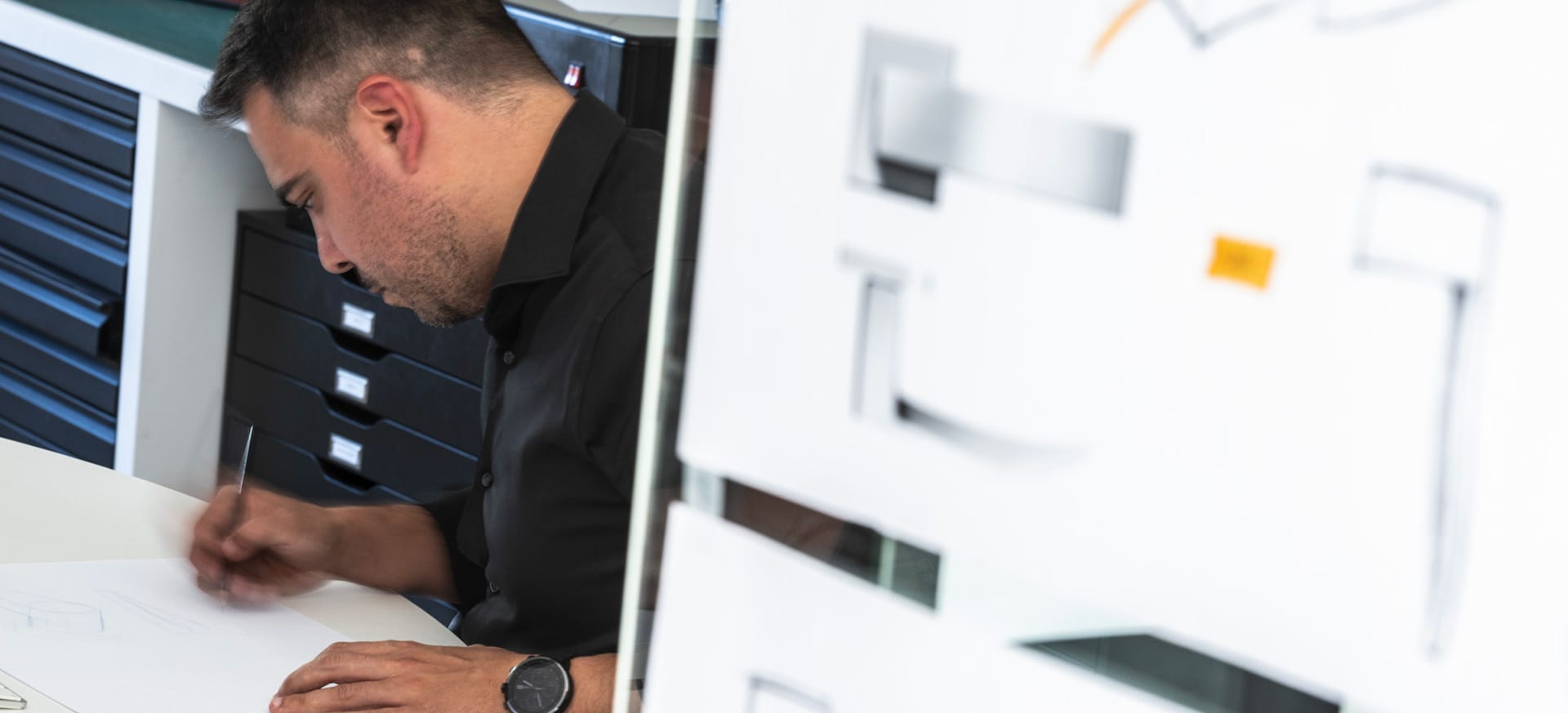
Around 20 million people work in the chemical manufacturing sector worldwide. These workers are mostly employed in large-scale manufacturing plants. However, there are a few contract and part-time workers. The sector's employment is being affected by technological advances and increased competition.
The U.S. economy is driving the demand for chemicals. Moreover, the chemical industry is a highly regulated sector. The manufacturing process is regulated by the government. Companies should implement environmentally sustainable operations. Some raw materials used in chemical manufacturing are also dangerous to extract.
The procurement process is challenging for the industry. It is also very expensive to obtain raw materials. To keep costs down, some companies are shifting their operations to locations that have lower overhead. Companies are also merging with others or shifting production activities to emerging countries. This will lead eventually to the elimination or merging of companies.
In 2008, 80 percent of jobs were in the basic chemical manufacturing section. This segment includes manufacturers of pesticides and dyes as well as other materials. Pfizer and Dow are two of the largest manufacturers in this area. DuPont, Formosa Plastics and Sinopec Group are other major players in this sector.
Large-scale production plants are often clean. Workers are required to wear safety goggles and work in a temperature-controlled environment. Some workers are however replaced by advanced machines that have computerized controls. These workers often work night shifts.
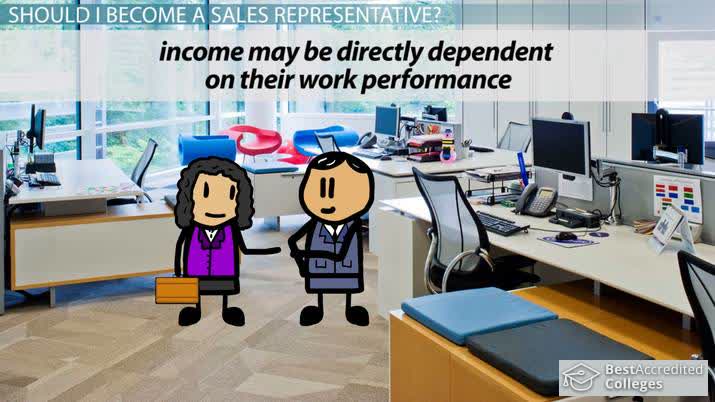
Chemical manufacturing plants may need to be modified to accommodate new production methods. New processes can increase accuracy and lower labor costs. Also, the use of nanotechnology will make chemical manufacturing more efficient. Nanotechnology can also be used to reduce waste and energy consumption.
The employment prospects for the chemical manufacturing industry will be affected by increased foreign competition, technological developments, as well as safety and environmental concerns. In general, the industry's employment will decrease by 13 percent over four years.
FAQ
What is the responsibility of a logistics manager?
A logistics manager ensures that all goods are delivered on time and without damage. This is done through his/her expertise and knowledge about the company's product range. He/she should ensure that sufficient stock is available in order to meet customer demand.
How can excess manufacturing production be reduced?
The key to reducing overproduction lies in developing better ways to manage inventory. This would reduce the amount of time spent on unnecessary activities such as purchasing, storing, and maintaining excess stock. This would allow us to use our resources for more productive tasks.
This can be done by using a Kanban system. A Kanbanboard is a visual tool that allows you to keep track of the work being done. Kanban systems allow work items to move through different states until they reach their final destination. Each state represents a different priority.
If work is moving from one stage to the other, then the current task can be completed and moved on to the next. It is possible to keep a task in the beginning stages until it gets to the end.
This allows for work to continue moving forward, while also ensuring that there is no work left behind. With a Kanban board, managers can see exactly how much work is being done at any given moment. This information allows them to adjust their workflow based on real-time data.
Another way to control inventory levels is to implement lean manufacturing. Lean manufacturing emphasizes eliminating waste in all phases of production. Any product that isn't adding value can be considered waste. Some common types of waste include:
-
Overproduction
-
Inventory
-
Unnecessary packaging
-
Excess materials
These ideas can help manufacturers improve efficiency and reduce costs.
What types of jobs can you find in logistics
There are many types of jobs in logistics. Some examples are:
-
Warehouse workers - They load and unload trucks and pallets.
-
Transport drivers - These are people who drive trucks and trailers to transport goods or perform pick-ups.
-
Freight handlers are people who sort and pack freight into warehouses.
-
Inventory managers – These people oversee inventory at warehouses.
-
Sales representatives - They sell products.
-
Logistics coordinators – They plan and coordinate logistics operations.
-
Purchasing agents: They are responsible for purchasing goods and services to support company operations.
-
Customer service agents - They answer phone calls and respond to emails.
-
Shipping clerks – They process shipping orders, and issue bills.
-
Order fillers - They fill orders based on what is ordered and shipped.
-
Quality control inspectors are responsible for inspecting incoming and outgoing products looking for defects.
-
Others - There are many types of jobs in logistics such as transport supervisors and cargo specialists.
What does the term manufacturing industries mean?
Manufacturing Industries are companies that manufacture products. The people who buy these products are called consumers. This is accomplished by using a variety of processes, including production, distribution and retailing. They make goods from raw materials with machines and other equipment. This includes all types of manufactured goods, including food items, clothing, building supplies, furniture, toys, electronics, tools, machinery, vehicles, pharmaceuticals, medical devices, chemicals, and many others.
What is the best way to learn about manufacturing?
The best way to learn about manufacturing is through hands-on experience. But if that is not possible you can always read books and watch educational videos.
What is the responsibility of a manufacturing manager?
A manufacturing manager has to ensure that all manufacturing processes work efficiently and effectively. They should also be aware of any problems within the company and act accordingly.
They should also learn how to communicate effectively with other departments, including sales and marketing.
They should be informed about industry trends and be able make use of this information to improve their productivity and efficiency.
Statistics
- Many factories witnessed a 30% increase in output due to the shift to electric motors. (en.wikipedia.org)
- It's estimated that 10.8% of the U.S. GDP in 2020 was contributed to manufacturing. (investopedia.com)
- (2:04) MTO is a production technique wherein products are customized according to customer specifications, and production only starts after an order is received. (oracle.com)
- Job #1 is delivering the ordered product according to specifications: color, size, brand, and quantity. (netsuite.com)
- You can multiply the result by 100 to get the total percent of monthly overhead. (investopedia.com)
External Links
How To
How to use Lean Manufacturing in the production of goods
Lean manufacturing is a management system that aims at increasing efficiency and reducing waste. It was first developed in Japan in the 1970s/80s by Taiichi Ahno, who was awarded the Toyota Production System (TPS), award from KanjiToyoda, the founder of TPS. The first book published on lean manufacturing was titled "The Machine That Changed the World" written by Michael L. Watkins and published in 1990.
Lean manufacturing refers to a set of principles that improve the quality, speed and costs of products and services. It is about eliminating defects and waste from all stages of the value stream. The five-steps of Lean Manufacturing are just-in time (JIT), zero defect and total productive maintenance (TPM), as well as 5S. Lean manufacturing focuses on eliminating non-value-added activities such as rework, inspection, and waiting.
In addition to improving product quality and reducing costs, lean manufacturing helps companies achieve their goals faster and reduces employee turnover. Lean manufacturing is considered one of the most effective ways to manage the entire value chain, including suppliers, customers, distributors, retailers, and employees. Lean manufacturing is widely practiced in many industries around the world. Toyota's philosophy is a great example of this. It has helped to create success in automobiles as well electronics, appliances and healthcare.
Five fundamental principles underlie lean manufacturing.
-
Define Value: Identify the social value of your business and what sets you apart.
-
Reduce waste - Get rid of any activity that does not add value to the supply chain.
-
Create Flow - Ensure work moves smoothly through the process without interruption.
-
Standardize and simplify – Make processes as repeatable and consistent as possible.
-
Build Relationships- Develop personal relationships with both internal as well as external stakeholders.
Although lean manufacturing has always been around, it is gaining popularity in recent years because of a renewed interest for the economy after 2008's global financial crisis. Many businesses have adopted lean production techniques to make them more competitive. Some economists even believe that lean manufacturing can be a key factor in economic recovery.
Lean manufacturing is now becoming a common practice in the automotive industry, with many benefits. These include higher customer satisfaction, lower inventory levels, lower operating expenses, greater productivity, and improved overall safety.
It can be applied to any aspect of an organisation. However, it is particularly useful when applied to the production side of an organization because it ensures that all steps in the value chain are efficient and effective.
There are three main types of lean manufacturing:
-
Just-in Time Manufacturing (JIT), also known as "pull system": This form of lean manufacturing is often referred to simply as "pull". JIT is a method in which components are assembled right at the moment of use, rather than being manufactured ahead of time. This approach is designed to reduce lead times and increase the availability of components. It also reduces inventory.
-
Zero Defects Manufacturing - ZDM: ZDM focuses its efforts on making sure that no defective units leave a manufacturing facility. You should repair any part that needs to be repaired during an assembly line. This is also true for finished products that require minor repairs before shipping.
-
Continuous Improvement: Continuous Improvement aims to improve efficiency by continually identifying problems and making adjustments to eliminate or minimize waste. Continuous improvement refers to continuous improvement of processes as well people and tools.