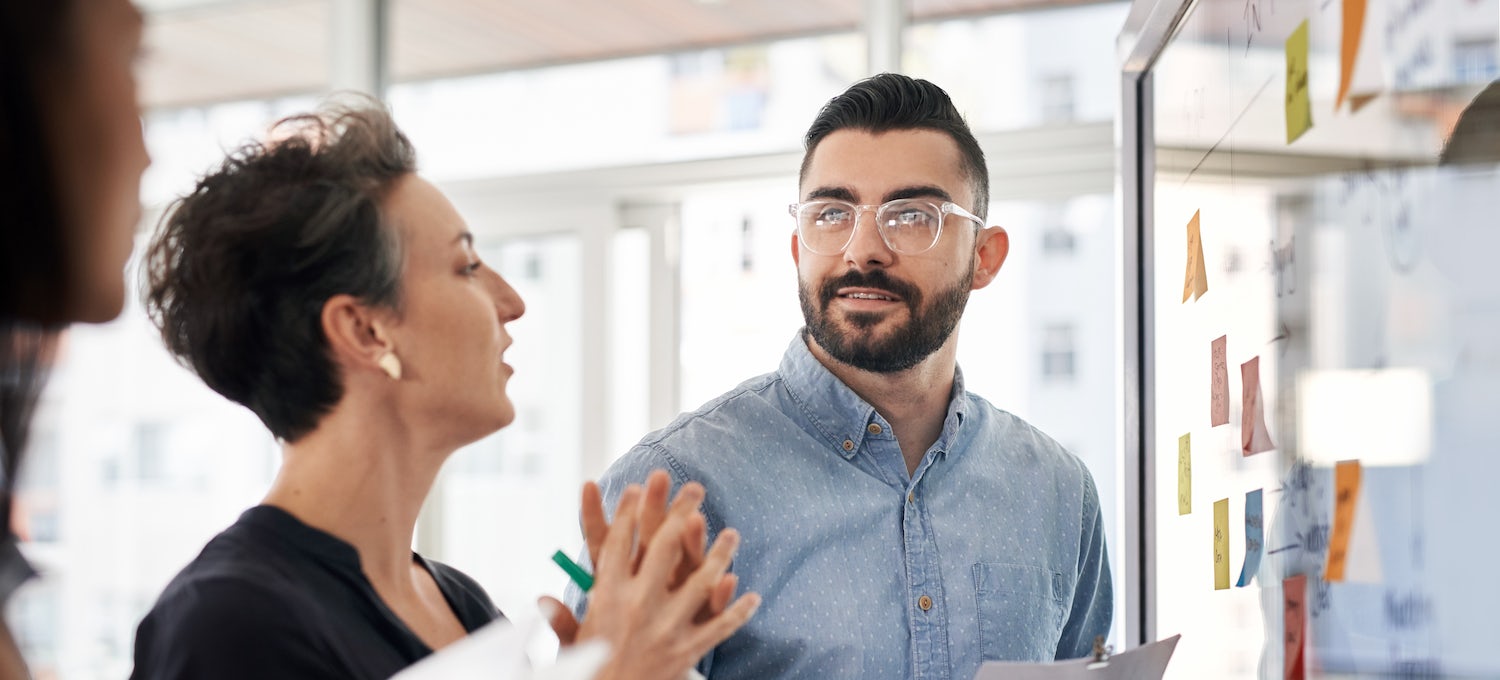
Global supply chains have seen many changes over the years. They have evolved from an industrial problem to a serious economic threat. It is a good idea to keep an eye on the latest developments. Global supply chains can be complex and interconnected in many ways.
Global value chain are made up of capital, flows, and intangibles. They are the result of economies, specialization, long-standing relationships, scale, and relationships. While some value chains are highly capital-intensive, other value chains are more regionalized.
Global supply chains are dynamic, multi-dimensional, and increasingly complex. They are an integral part of global trade as well as the functioning of countries. They are also vulnerable to disruptions. These disruptions can be short-term or permanent. It is essential to have a diverse, flexible, and resilient supply network in order to avoid these disruptions. This requires a comprehensive approach which includes structural reforms and prudent risk management. Identifying the biggest challenges and assessing the solutions is the first step towards building a supply chain that can withstand the next storm.
Along with assessing the risk of disruptions in supply chains, companies must also take into account the risks associated to manufacturing, labor and materials. In order to assess their impact, they should also simulate extreme supply and demand disruptions. They must also examine their inventory of critical materials to ensure they are able to meet foreseeable demand. A strategic strategy is required to develop a resilient supply network. This may involve reprioritizing production and shifting manufacturing to more flexible places, improving supply chain technology, and implementing guaranteed sources.
The COVID-19 pandemic caused significant disruptions to global supply chains. Several countries imposed tariffs on each other, while others imposed sanctions against each other. These tariffs or sanctions have created trade frictions that made it harder for the United States, China, and other countries to export certain products. These disruptions have caused price inflation. However, they have made companies more aware that their supply networks are fragile and have caused them to rethink how they design and implement their supply systems.
The COVID-19 epidemic caused severe disruption in global supply chain operations, but the effects of the pandemic are still being felt. For example, disruptions to supply chains caused by the Suez Canal's blockage have been lasting up to six month. The freight costs have also increased dramatically as a result. The UK's annual inflation is now at 9%.
It's difficult to ignore the fact the United States and China are engaged in a trade conflict. Supply chain executives need to question how they can rely so heavily in outsourced networks. They must also be aware of the potential risks from labor shortages that can result in economic shocks. Leaders in supply chains should also be aware of the potential benefits of cross-border finance as well as regulation that can help expand global integration.
Despite all the turmoil, we are still connected to the rest of the world. Companies that are more holistic in their supply chain management will reap the benefits from global integration.
FAQ
Can some manufacturing processes be automated?
Yes! Yes. Automation has been around since ancient time. The wheel was invented by the Egyptians thousands of years ago. Today, robots assist in the assembly of lines.
Actually, robotics can be used in manufacturing for many purposes. These include:
-
Assembly line robots
-
Robot welding
-
Robot painting
-
Robotics inspection
-
Robots that create products
Manufacturing can also be automated in many other ways. For instance, 3D printing allows us make custom products and not have to wait for months or even weeks to get them made.
Why is logistics important in manufacturing
Logistics are an essential component of any business. They are essential to any business's success.
Logistics are also important in reducing costs and improving efficiency.
What are the 7 Rs of logistics.
The 7R's of Logistics is an acronym for the seven basic principles of logistics management. It was developed by the International Association of Business Logisticians (IABL) and published in 2004 as part of its "Seven Principles of Logistics Management" series.
The acronym is composed of the following letters.
-
Responsible – ensure that all actions are legal and don't cause harm to anyone else.
-
Reliable – have faith in your ability and capability to keep promises.
-
Be responsible - Use resources efficiently and avoid wasting them.
-
Realistic – Consider all aspects, including cost-effectiveness as well as environmental impact.
-
Respectful: Treat others with fairness and equity
-
Be resourceful: Look for opportunities to save money or increase productivity.
-
Recognizable: Provide customers with value-added service
What skills should a production planner have?
Being a production planner is not easy. You need to be organized and flexible. Also, you must be able and willing to communicate with clients and coworkers.
How can we reduce manufacturing overproduction?
The key to reducing overproduction lies in developing better ways to manage inventory. This would reduce the amount of time spent on unnecessary activities such as purchasing, storing, and maintaining excess stock. We could use these resources to do other productive tasks.
You can do this by adopting a Kanban method. A Kanban board, a visual display to show the progress of work, is called a Kanban board. Kanban systems are where work items travel through a series of states until reaching their final destination. Each state represents a different priority level.
If work is moving from one stage to the other, then the current task can be completed and moved on to the next. However, if a task is still at the beginning stages, it will remain so until it reaches the end of the process.
This keeps work moving and ensures no work is lost. Managers can see how much work has been done and the status of each task at any time with a Kanban Board. This information allows managers to adjust their workflow based off real-time data.
Another way to control inventory levels is to implement lean manufacturing. Lean manufacturing focuses on eliminating waste throughout the entire production chain. Anything that does nothing to add value to a product is waste. The following are examples of common waste types:
-
Overproduction
-
Inventory
-
Unnecessary packaging
-
Materials in excess
These ideas can help manufacturers improve efficiency and reduce costs.
How does manufacturing avoid bottlenecks in production?
To avoid production bottlenecks, ensure that all processes run smoothly from the moment you receive your order to the time the product ships.
This includes both planning for capacity and quality control.
This can be done by using continuous improvement techniques, such as Six Sigma.
Six Sigma is a management system used to improve quality and reduce waste in every aspect of your organization.
It focuses on eliminating variation and creating consistency in your work.
Statistics
- In the United States, for example, manufacturing makes up 15% of the economic output. (twi-global.com)
- In 2021, an estimated 12.1 million Americans work in the manufacturing sector.6 (investopedia.com)
- (2:04) MTO is a production technique wherein products are customized according to customer specifications, and production only starts after an order is received. (oracle.com)
- Job #1 is delivering the ordered product according to specifications: color, size, brand, and quantity. (netsuite.com)
- Many factories witnessed a 30% increase in output due to the shift to electric motors. (en.wikipedia.org)
External Links
How To
Six Sigma in Manufacturing
Six Sigma refers to "the application and control of statistical processes (SPC) techniques in order to achieve continuous improvement." Motorola's Quality Improvement Department in Tokyo, Japan developed Six Sigma in 1986. Six Sigma's basic concept is to improve quality and eliminate defects through standardization. In recent years, many companies have adopted this method because they believe there is no such thing as perfect products or services. The main goal of Six Sigma is to reduce variation from the mean value of production. If you take a sample and compare it with the average, you will be able to determine how much of the production process is different from the norm. If it is too large, it means that there are problems.
Understanding the nature of variability in your business is the first step to Six Sigma. Once you've understood that, you'll want to identify sources of variation. You'll also want to determine whether these variations are random or systematic. Random variations occur when people do mistakes. Symmetrical variations are caused due to factors beyond the process. These are, for instance, random variations that occur when widgets are made and some fall off the production line. It would be considered a systematic problem if every widget that you build falls apart at the same location each time.
Once you've identified where the problems lie, you'll want to design solutions to eliminate those problems. This could mean changing your approach or redesigning the entire process. After implementing the new changes, you should test them again to see if they worked. If they don’t work, you’ll need to go back and rework the plan.