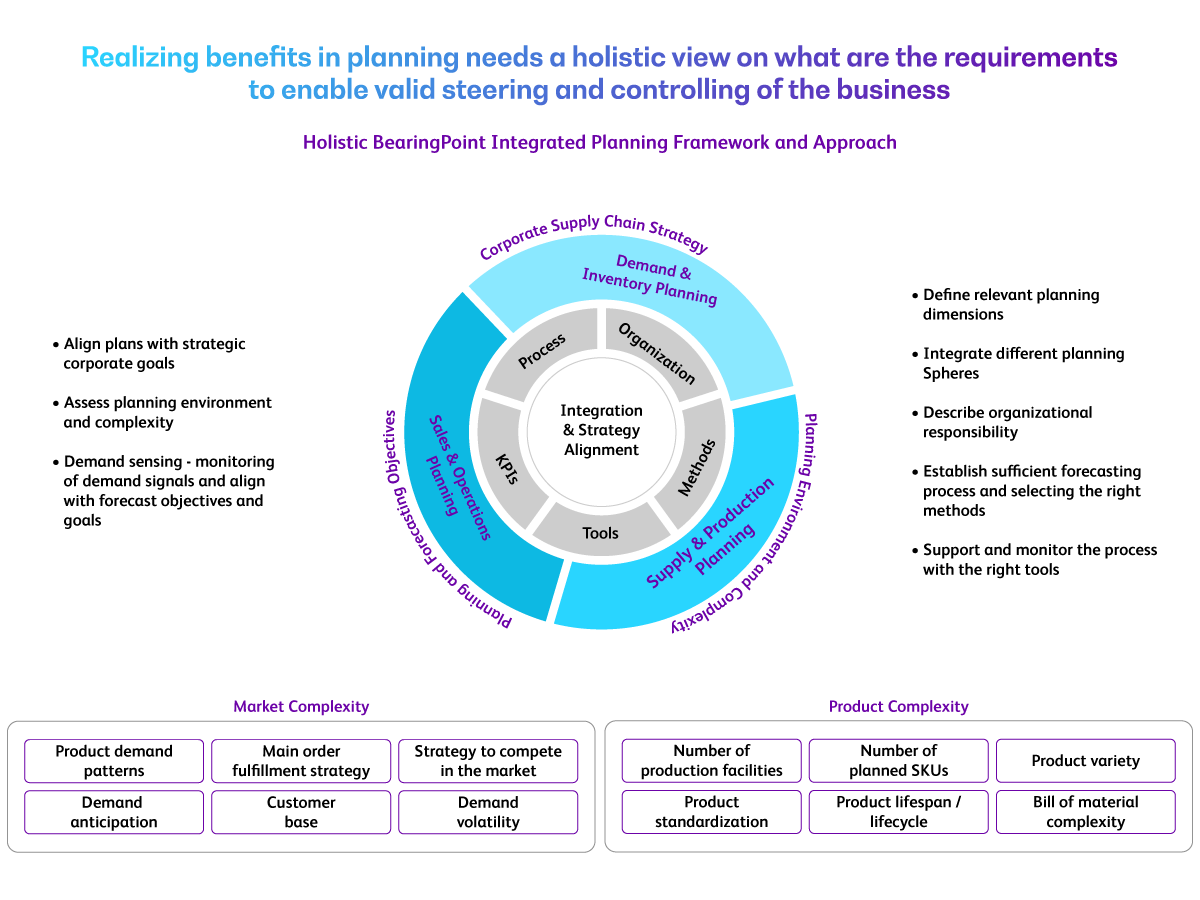
Supply networks are complex adaptive systems, wherein large numbers of firms participate in the process of delivering products and services. A supply network is a collection of interrelated industries that provide raw materials, finished goods and other commodities. A supply network is not only used for traditional functions but can also be used to facilitate digital flows and resource extraction.
As supply networks evolve, they come in all shapes and sizes. It is essential to design a system which is resilient to unanticipated events. Understanding the different supply network types is essential to understand how they respond to disruptions. To address this problem, there are several options.
One way to measure resilience is to look at the flow of information. This is a good place where to begin: the information flow between the customer and the preceding organizations. It can also be used to assess the strength of a relationship. The manufacturer might be able detect missing links if the supplier of the first tier is connected to the supplier of the second tier.
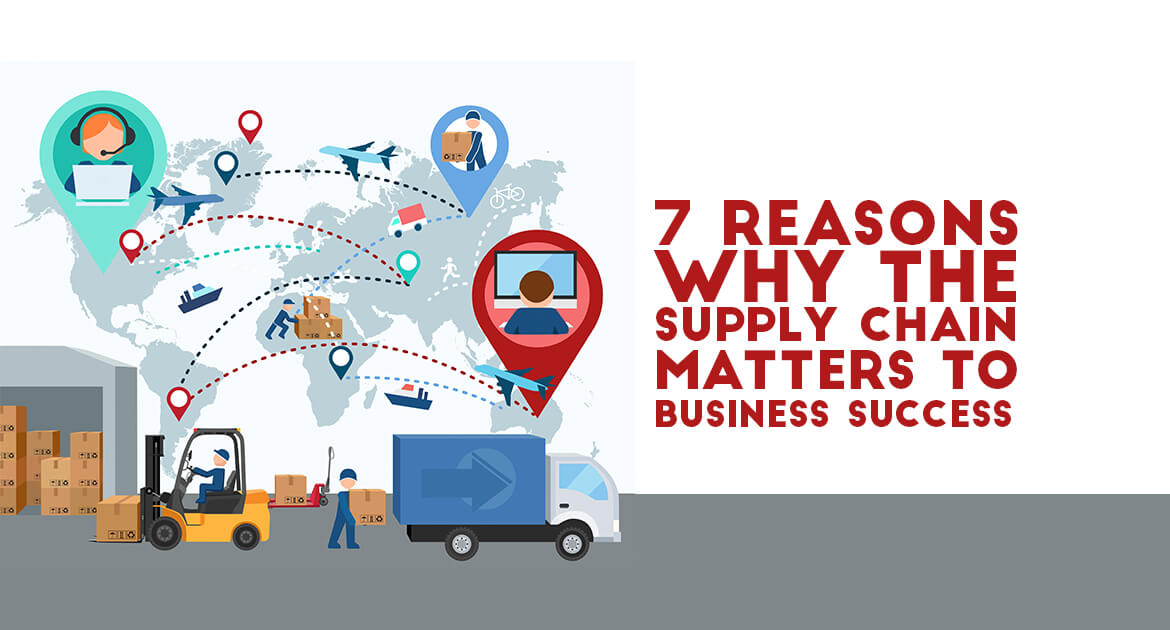
The supply network that allows for this flow can be beneficial to the customer in that it delivers the desired product/service. Implementing such a smart approach to supply chain management isn't as easy as it sounds. First, companies must find a way to overcome the constraints of existing networks. The second is to ensure that the way they manage information flows can withstand disruptions.
Intermediaries play an important role in the supply system. These entities are often not well-understood. For example, a semiconductor manufacturer moves work-in-process material from fabrication to assembly. These materials can be moved in a way that maximizes their productivity and speeds up production. Likewise, a manufacturing firm that has a strong reliance on procuring subcomponents from other firms can scale up or down depending on its production needs.
Unexpected results may result from incorporating intermediaries into the supply chain model. Among other things, better communication can lead to increased productivity and efficiency. Additionally, strong partnerships can help organisations improve their service to customers.
Supply networks are often characterized by high to medium levels of complexity upstream and downstream. This is due to the fact that suppliers must make decisions about which to buy and which to re-sell, while ensuring that the overall network is functional. As a result, power imbalances are quite common. These are easily managed by a few key strategies.
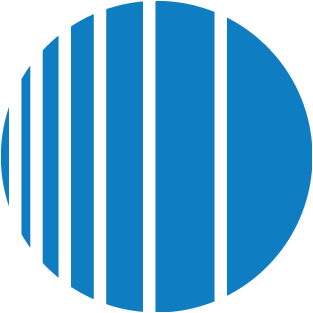
Some of the most common solutions to this problem are establishing a control center to monitor and manage suppliers, an information hub to collect and analyse data, as well as an automated decision making engine. A rebalancing exercise can be used to correct imbalances, and a buffer is designed to protect the network from disruptions. Suppliers who are able predict and meet the clients' requirements may be better able than others to prevent a meltdown in their supply networks.
FAQ
What does warehouse mean?
A warehouse or storage facility is where goods are stored before they are sold. You can have it indoors or outdoors. In some cases, it may be a combination of both.
What is the job of a manufacturer manager?
Manufacturing managers must ensure that manufacturing processes are efficient, effective, and cost-effective. They should also be aware and responsive to any company problems.
They should also know how to communicate with other departments such as sales and marketing.
They should be up to date on the latest trends and be able apply this knowledge to increase productivity and efficiency.
What does the term manufacturing industries mean?
Manufacturing Industries refers to businesses that manufacture products. The people who buy these products are called consumers. This is accomplished by using a variety of processes, including production, distribution and retailing. They make goods from raw materials with machines and other equipment. This includes all types if manufactured goods.
What is the job of a logistics manger?
A logistics manager ensures that all goods are delivered on time and without damage. This is done by using his/her experience and knowledge of the company's products. He/she also needs to ensure adequate stock to meet demand.
Statistics
- You can multiply the result by 100 to get the total percent of monthly overhead. (investopedia.com)
- Job #1 is delivering the ordered product according to specifications: color, size, brand, and quantity. (netsuite.com)
- In the United States, for example, manufacturing makes up 15% of the economic output. (twi-global.com)
- In 2021, an estimated 12.1 million Americans work in the manufacturing sector.6 (investopedia.com)
- (2:04) MTO is a production technique wherein products are customized according to customer specifications, and production only starts after an order is received. (oracle.com)
External Links
How To
Six Sigma in Manufacturing
Six Sigma is "the application statistical process control (SPC), techniques for continuous improvement." Motorola's Quality Improvement Department created Six Sigma at their Tokyo plant, Japan in 1986. Six Sigma's main goal is to improve process quality by standardizing processes and eliminating defects. Since there are no perfect products, or services, this approach has been adopted by many companies over the years. Six Sigma aims to reduce variation in the production's mean value. This means that if you take a sample of your product, then measure its performance against the average, you can find out what percentage of the time the process deviates from the norm. If there is a significant deviation from the norm, you will know that something needs to change.
The first step toward implementing Six Sigma is understanding how variability works in your business. Once you understand this, you can then identify the causes of variation. It is important to identify whether the variations are random or systemic. Random variations occur when people make mistakes; systematic ones are caused by factors outside the process itself. If you make widgets and some of them end up on the assembly line, then those are considered random variations. If however, you notice that each time you assemble a widget it falls apart in exactly the same spot, that is a problem.
Once you've identified where the problems lie, you'll want to design solutions to eliminate those problems. It might mean changing the way you do business or redesigning it entirely. You should then test the changes again after they have been implemented. If they don't work you need to rework them and come up a better plan.