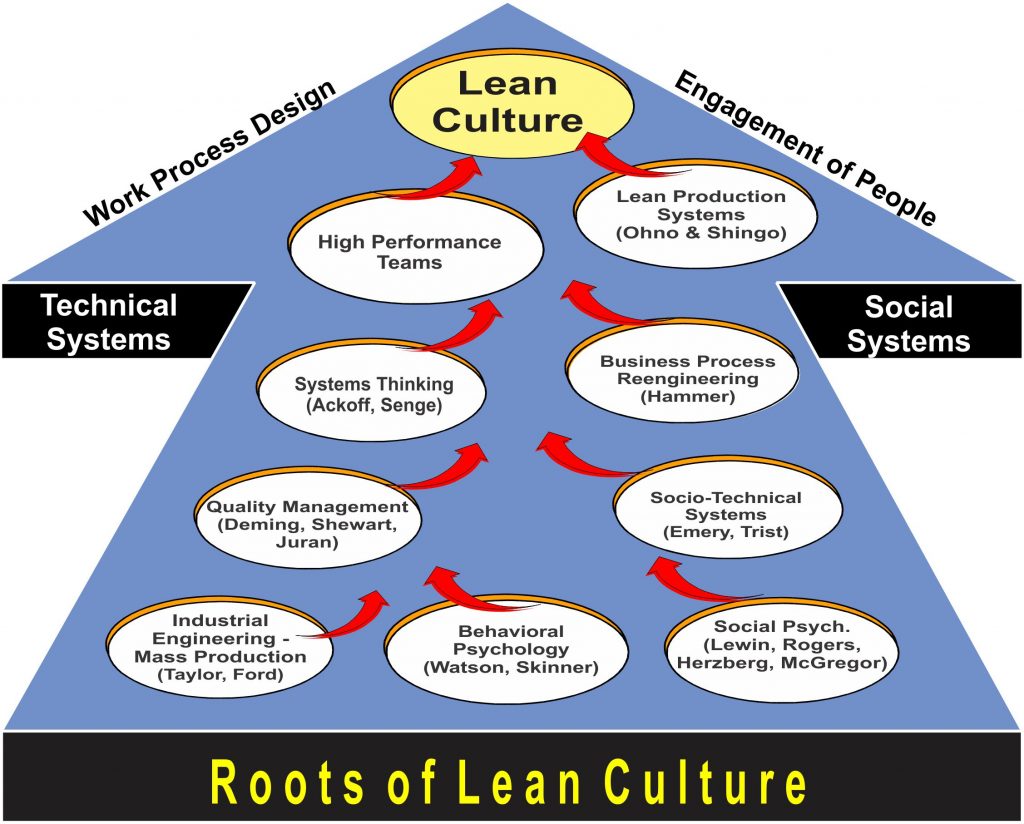
Jobs in wind turbine manufacturing
The manufacturing of wind turbines requires specialized skills and knowledge. These jobs could include blade epoxies or tower assembly. Some wind turbine manufacturing companies also contract with third-party suppliers to manufacture various components. Wind turbine components are huge and must be transported efficiently and quickly. Teams of logisticians or rail freight drivers are needed by companies to complete this task.
For jobs in wind turbine production, a bachelor's is required. However, there are some cases that require masters degrees. Most jobs in the wind turbine industry require engineering or environmental engineering concentrations. Entry-level engineers need to have advanced computer skills and previous experience in addition to a degree. To ensure quality control and accuracy, they usually work with experienced employees. They may also be assigned more complex projects.
Processes involved in wind turbine manufacturing
The main components of a turbine's wind turbine are the blades. Each blade consists of two faces, joined by integral shear webs. The blades are supported with a box spar, shell fairings and a box spar. These structures can withstand edgewise as well as flapwise loads. The spar is resistant to edgewise bending due to wind pressure and gravitational force. These forces are resistant to the blades.
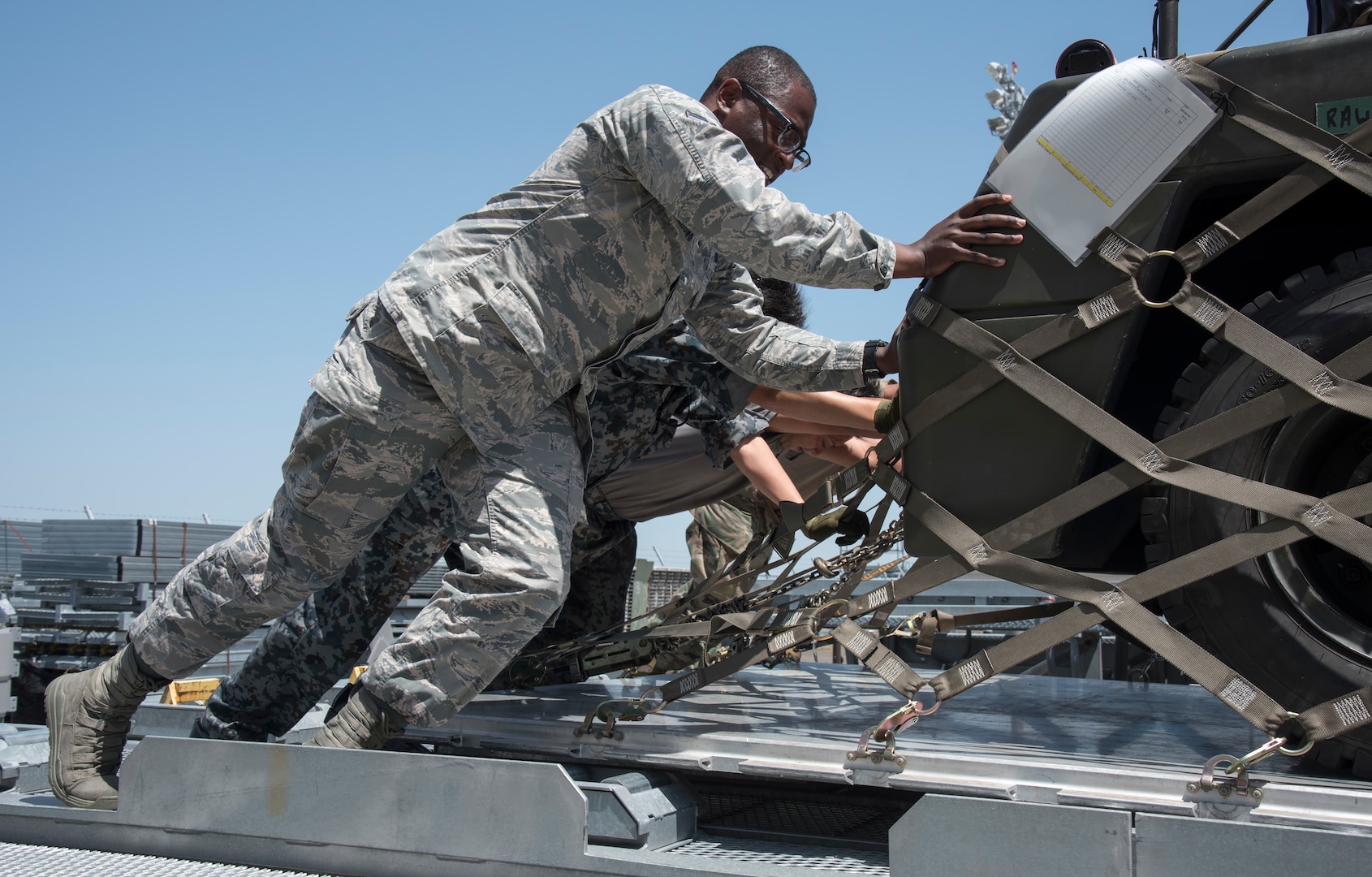
The blades can be made of a variety materials. The most common material for commercial wind turbine blades is fiberglass, but aluminum and lightweight woods can also be used. The blades will then be wrapped in foil, and connected to tubes with resin pumps.
Competitors in wind turbine manufacturing
While Chinese manufacturers are growing in the global industry of wind, they are not yet the predominant player. Chinese turbine manufacturers have struggled to dethrone incumbents in developed markets. They might be able eventually to increase their overseas activity if the invest in local manufacturing capabilities.
Many are opting to build their components themselves, even though large turbine companies are outsourcing increasingly many parts. This has both advantages and disadvantages. Vestas in Pueblo (Colorado) has adopted this strategy and now manufactures wind turbine towers to support third-party US projects. This agreement allows the tower factory to use up 25 percent of its manufacturing capacity and supports 100 jobs in the local area. Quality control is a problem with this approach. In the past, some components outsourced have failed. This includes gearbox failures or blade cracking. Some foundations offshore are made from low quality steel.
Manufacturing wind turbines poses health and safety risks
Safety and health are two of the most critical issues in manufacturing wind turbines. The hazards faced by workers can result in long-term injuries or even fatalities. There are many things you can do to reduce the risk. These are some tips for keeping employees safe when working in a manufacturing wind turbine facility.
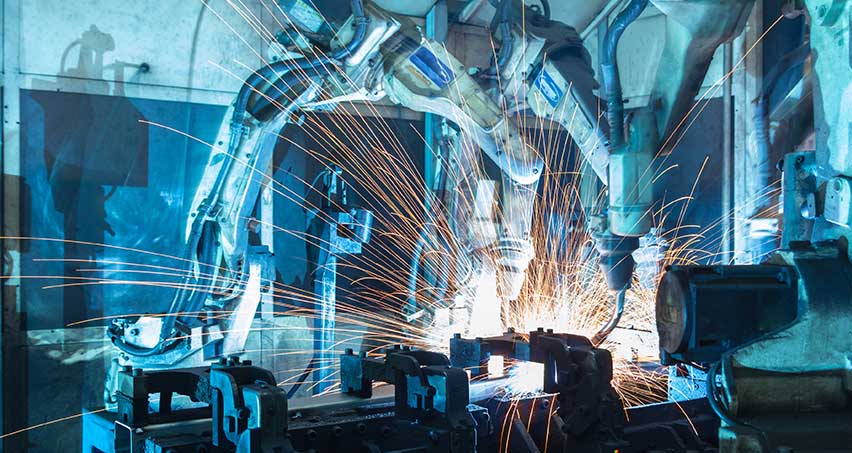
One of the most common hazards in wind turbine blade manufacturing is the exposure to harmful gases, vapors, and dust. Workers must use respirators to reduce their exposure and are trained to use them. It is important to have ear protection and good training.
FAQ
What does it take to run a logistics business?
It takes a lot of skills and knowledge to run a successful logistics business. You must have good communication skills to interact effectively with your clients and suppliers. You must be able analyze data and draw out conclusions. You must be able manage stress and pressure under pressure. You need to be innovative and creative to come up with new ways to increase efficiency. You need to have strong leadership qualities to motivate team members and direct them towards achieving organizational goals.
To meet tight deadlines, you must also be efficient and organized.
What are the 7 Rs of logistics?
The acronym 7R's of Logistic is an acronym that stands for seven fundamental principles of logistics management. It was created by the International Association of Business Logisticians and published in 2004 under its "Seven Principles of Logistics Management".
The following letters form the acronym:
-
Responsive - ensure all actions are legal and not harmful to others.
-
Reliable – have faith in your ability and capability to keep promises.
-
Reasonable - make sure you use your resources well and don't waste them.
-
Realistic – Consider all aspects, including cost-effectiveness as well as environmental impact.
-
Respectful - treat people fairly and equitably.
-
You are resourceful and look for ways to save money while increasing productivity.
-
Recognizable is a company that provides customers with value-added solutions.
How can manufacturing efficiency be improved?
First, we need to identify which factors are most critical in affecting production times. We must then find ways that we can improve these factors. If you don’t know where to begin, consider which factors have the largest impact on production times. Once you have identified the factors, then try to find solutions.
Statistics
- [54][55] These are the top 50 countries by the total value of manufacturing output in US dollars for its noted year according to World Bank.[56] (en.wikipedia.org)
- In 2021, an estimated 12.1 million Americans work in the manufacturing sector.6 (investopedia.com)
- It's estimated that 10.8% of the U.S. GDP in 2020 was contributed to manufacturing. (investopedia.com)
- (2:04) MTO is a production technique wherein products are customized according to customer specifications, and production only starts after an order is received. (oracle.com)
- According to a Statista study, U.S. businesses spent $1.63 trillion on logistics in 2019, moving goods from origin to end user through various supply chain network segments. (netsuite.com)
External Links
How To
How to use Lean Manufacturing in the production of goods
Lean manufacturing is a management style that aims to increase efficiency and reduce waste through continuous improvement. It was developed by Taiichi Okono in Japan, during the 1970s & 1980s. TPS founder Kanji Takoda awarded him the Toyota Production System Award (TPS). Michael L. Watkins published the "The Machine That Changed the World", the first book about lean manufacturing. It was published in 1990.
Lean manufacturing, often described as a set and practice of principles, is aimed at improving the quality, speed, cost, and efficiency of products, services, and other activities. It is about eliminating defects and waste from all stages of the value stream. Lean manufacturing can be described as just-in–time (JIT), total productive maintenance, zero defect (TPM), or even 5S. Lean manufacturing focuses on eliminating non-value-added activities such as rework, inspection, and waiting.
Lean manufacturing improves product quality and costs. It also helps companies reach their goals quicker and decreases employee turnover. Lean manufacturing has been deemed one of the best ways to manage the entire value-chain, including customers, distributors as well retailers and employees. Many industries worldwide use lean manufacturing. For example, Toyota's philosophy underpins its success in automobiles, electronics, appliances, healthcare, chemical engineering, aerospace, paper, food, etc.
Five basic principles of Lean Manufacturing are included in lean manufacturing
-
Define Value - Identify the value your business adds to society and what makes you different from competitors.
-
Reduce waste - Get rid of any activity that does not add value to the supply chain.
-
Create Flow - Make sure work runs smoothly without interruptions.
-
Standardize and simplify – Make processes as repeatable and consistent as possible.
-
Build relationships - Develop and maintain personal relationships with both your internal and external stakeholders.
Lean manufacturing, although not new, has seen renewed interest in the economic sector since 2008. To increase their competitiveness, many businesses have turned to lean manufacturing. In fact, some economists believe that lean manufacturing will be an important factor in economic recovery.
Lean manufacturing is now becoming a common practice in the automotive industry, with many benefits. These benefits include increased customer satisfaction, reduced inventory levels and lower operating costs.
Lean manufacturing can be applied to almost every aspect of an organization. However, it is particularly useful when applied to the production side of an organization because it ensures that all steps in the value chain are efficient and effective.
There are three types principally of lean manufacturing:
-
Just-in-Time Manufacturing: Also known as "pull systems", this type of lean manufacturing uses just-in-time manufacturing (JIT). JIT is a process in which components can be assembled at the point they are needed, instead of being made ahead of time. This approach reduces lead time, increases availability and reduces inventory.
-
Zero Defects Manufacturing, (ZDM): ZDM is focused on ensuring that no defective products leave the manufacturing facility. Repairing a part that is damaged during assembly should be done, not scrapping. This is true even for finished products that only require minor repairs prior to shipping.
-
Continuous Improvement: Continuous Improvement aims to improve efficiency by continually identifying problems and making adjustments to eliminate or minimize waste. Continuous improvement involves continuous improvement of processes and people as well as tools.