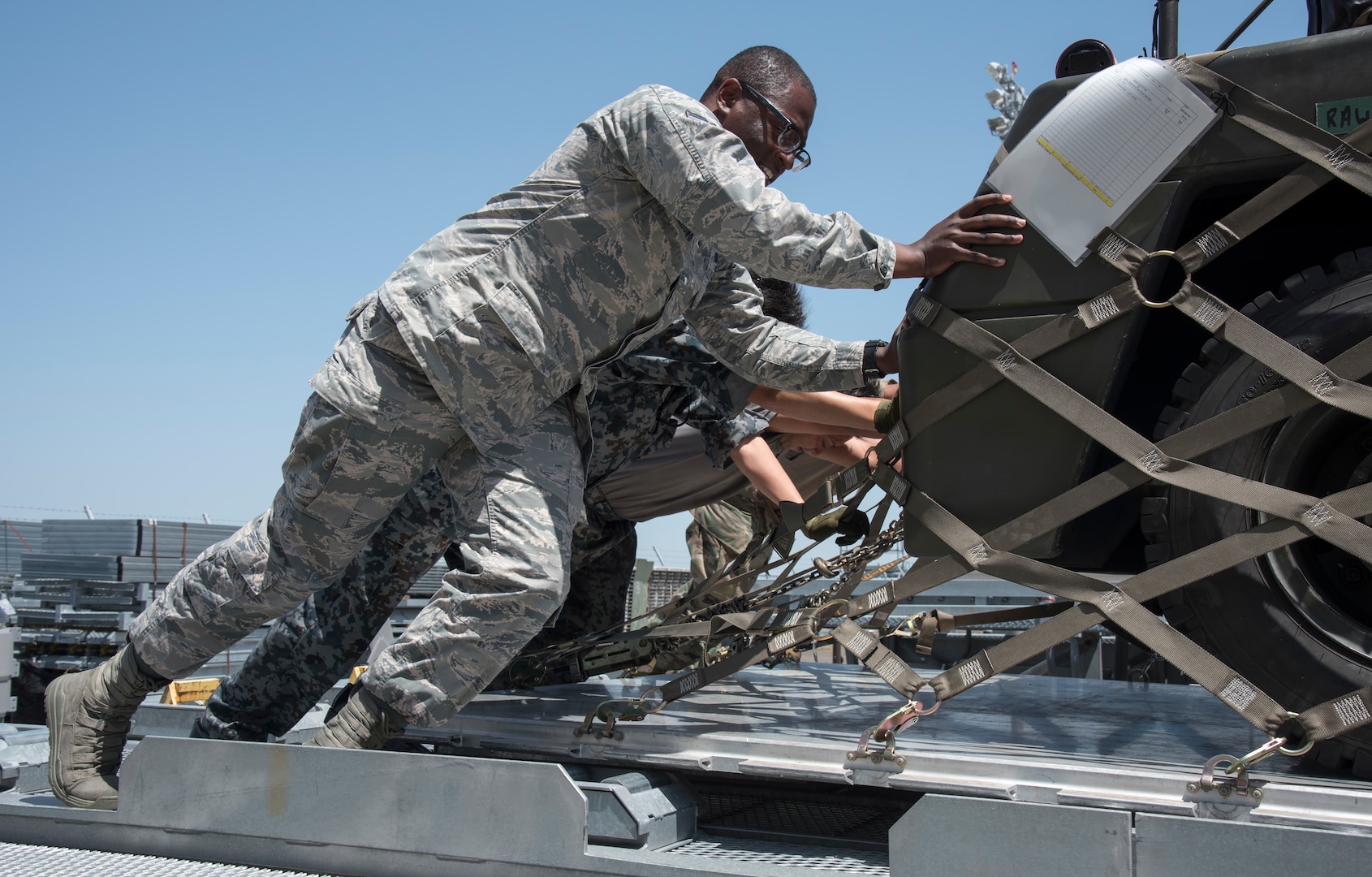
To stay competitive, organizations need to constantly improve. There are many ways that a business can improve its operations, from productivity to communication and operations.
Operational efficiency is a type of management technique which seeks to improve a business in all areas. It involves reducing waste, improving workflows and processes to increase efficiency and profitability.
The term operational excellence derives from the management theory known as scientific management. This theory was created in the 18th century, and was heavily influenced Adam Smith and Frederick Winslow Taylor. The process takes years and involves a lot trial and error.
What is Operational excellence?
According to the Institute for Operational Excellence, operational excellence is the ability to monitor product and information flow within an organization. This means everyone from the senior executives to the workers on the floor should be capable of detecting issues and observing product flow.
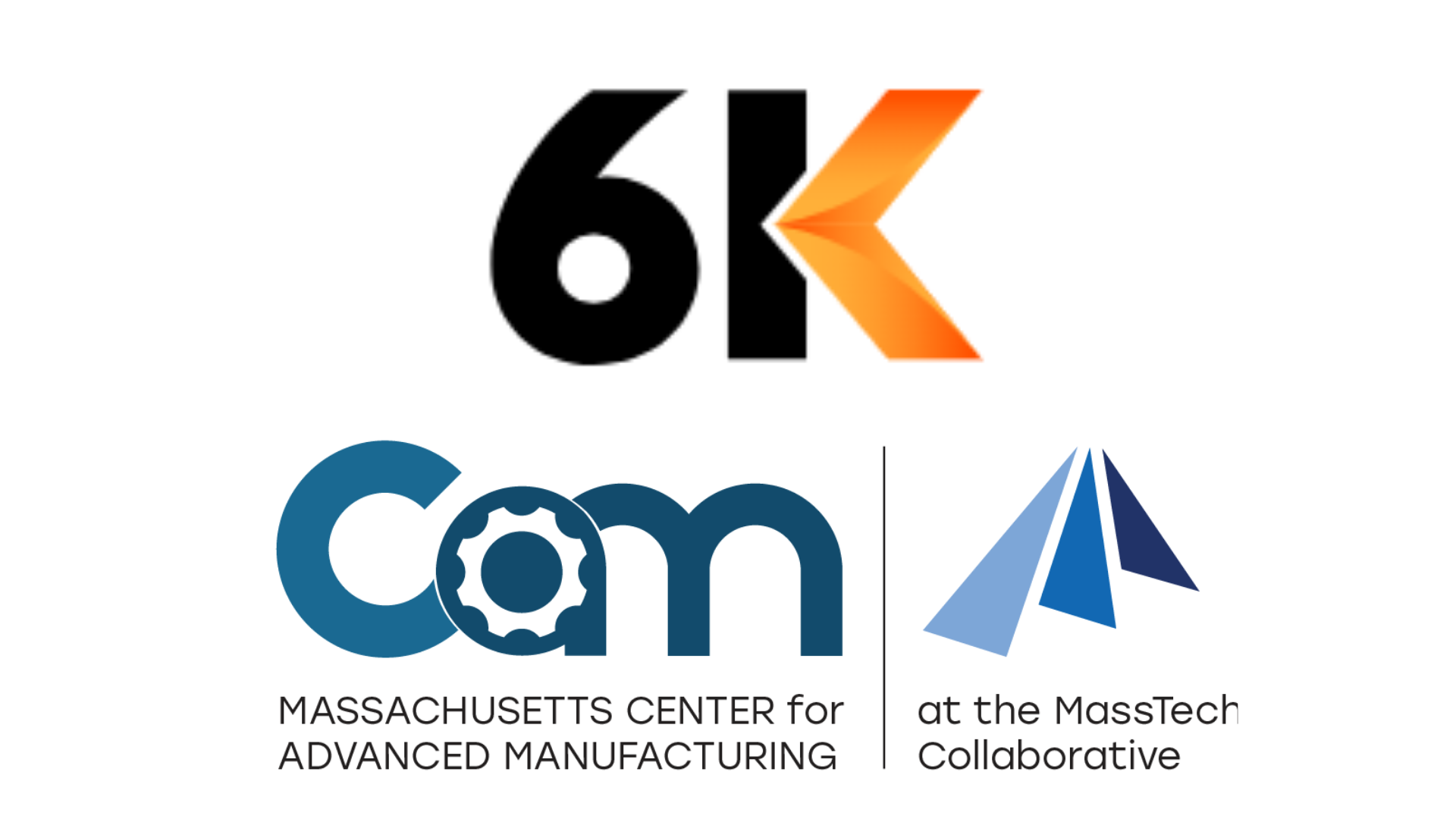
To create a culture that is based on operational excellence, a cultural change is needed. This is a continuous process, and it takes some time to build employee trust. It involves changing leadership styles and behaviors, but this is an important first step.
What Is The Role Of Operational Excellence Staffs
Operational excellence staff are responsible for implementing the strategy of the organization. Their responsibilities include overseeing process improvement events, participating in cross-functional project teams, defining and monitoring performance metrics, fostering culture and mentoring frontline operational excellence leaders.
They may also oversee projects that are based on methodologies of improvement, such as Six Sigma. These methods are highly effective at improving efficiency and transforming operations, but they need trained staff who have expertise in areas such as project management or business intelligence.
How to Create Operational Excellence Plan
A plan for operational excellence should include a methodology to help you reach your goals quickly and efficiently. This is particularly true if you want to reduce waste, enhance your workflows, or improve the customer experience.
To track your progress, you can use different KPIs. They should be relevant to the goals you have set and realistic to encourage employees to strive towards excellence.
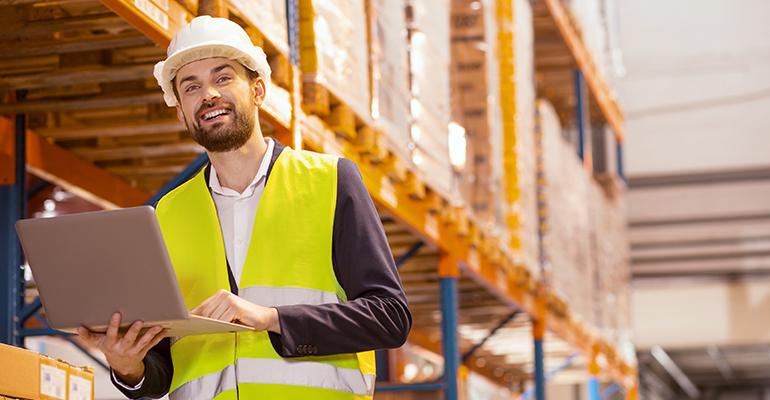
Using these tools will ensure that your operations are as efficient and cost-effective as possible. These tools will allow you to receive feedback from frontline staff, so you can continue improving.
How to Measure Operational Excellence Goals
The majority of Directors of Operations measure a combination of operational and financial numbers at the highest level along with common sense qualitative data from employee surveys and client feedback. This will help them to get a better idea of how well they're doing and how near they are to their objectives.
This is because operational excellence works at every level of the company, so it's vital to make sure that all of the individual team members have their own targets. As an example, the Director of Operation should set their profit targets according to how much they spend on staff. Meanwhile, project managers need to set their own goals based on billable and unbillable work. The operational excellence of an organization can then be measured on all levels. This will ensure that revenue and costs are equal.
FAQ
What is production management?
Production Planning includes planning for all aspects related to production. This document ensures that everything is prepared and available when you are ready for shooting. This document should also include information on how to get the best result on set. This includes shooting schedules, locations, cast lists, crew details, and equipment requirements.
The first step in filming is to define what you want. You may already know where you want the film to be shot, or perhaps you have specific locations and sets you wish to use. Once you have determined your scenes and locations, it is time to start figuring out the elements that you will need for each scene. Perhaps you have decided that you need to buy a car but aren't sure which model. This is where you can look up car models online and narrow down your options by choosing from different makes and models.
Once you have found the right car, you can start thinking about extras. What about additional seating? Or perhaps you need someone walking around the back of the car? Perhaps you would like to change the interior colour from black to white. These questions can help you decide the right look for your car. Also, think about what kind of shots you would like to capture. What type of shots will you choose? Maybe the engine or steering wheel is what you are looking to film. These details will help identify the exact car you wish to film.
Once you have all the information, you are ready to create a plan. You will know when you should start and when you should finish shooting. A schedule for each day will detail when you should arrive at the location and when you need leave. It will help everyone know exactly what they have to do and when. If you need to hire extra staff, you can make sure you book them in advance. You should not hire anyone who doesn't show up because of your inaction.
Also, consider how many days you will be filming your schedule. Some projects are quick and easy, while others take weeks. When you are creating your schedule, you should always keep in mind whether you need more than one shot per day or not. Multiple shots at the same location can increase costs and make it more difficult to complete. It's better to be safe than sorry and shoot less takes if you're not certain whether you need more takes.
Budget setting is an important part of production planning. You will be able to manage your resources if you have a realistic budget. Remember that you can always reduce the budget later on if you run into unforeseen problems. It is important to not overestimate how much you will spend. You will end up spending less money if you underestimate the cost of something.
Production planning is a detailed process. But, once you understand the workings of everything, it becomes easier for future projects to be planned.
What skills should a production planner have?
A production planner must be organized, flexible, and able multitask to succeed. It is also important to be able communicate with colleagues and clients.
What are the main products of logistics?
Logistics refers to all activities that involve moving goods from A to B.
They include all aspects associated with transport including packaging, loading transporting, unloading storage, warehousing inventory management customer service, distribution returns and recycling.
Logisticians ensure the product reaches its destination in the most efficient manner. Logisticians assist companies in managing their supply chains by providing information such as demand forecasts, stock levels and production schedules.
They also keep track of shipments in transit, monitor quality standards, perform inventories and order replenishment, coordinate with suppliers and vendors, and provide support services for sales and marketing.
How can manufacturing efficiency improved?
The first step is to identify the most important factors affecting production time. We then need to figure out how to improve these variables. You can start by identifying the most important factors that impact production time. Once you've identified them all, find solutions to each one.
Are there ways to automate parts of manufacturing?
Yes! Yes. Automation has been around since ancient time. The wheel was invented by the Egyptians thousands of years ago. To help us build assembly lines, we now have robots.
There are many uses of robotics today in manufacturing. These include:
-
Robots for assembly line
-
Robot welding
-
Robot painting
-
Robotics inspection
-
Robots that create products
Automation can be applied to manufacturing in many other ways. 3D printing, for example, allows us to create custom products without waiting for them to be made.
Statistics
- In the United States, for example, manufacturing makes up 15% of the economic output. (twi-global.com)
- (2:04) MTO is a production technique wherein products are customized according to customer specifications, and production only starts after an order is received. (oracle.com)
- It's estimated that 10.8% of the U.S. GDP in 2020 was contributed to manufacturing. (investopedia.com)
- According to the United Nations Industrial Development Organization (UNIDO), China is the top manufacturer worldwide by 2019 output, producing 28.7% of the total global manufacturing output, followed by the United States, Japan, Germany, and India.[52][53] (en.wikipedia.org)
- According to a Statista study, U.S. businesses spent $1.63 trillion on logistics in 2019, moving goods from origin to end user through various supply chain network segments. (netsuite.com)
External Links
How To
How to use Lean Manufacturing in the production of goods
Lean manufacturing is an approach to management that aims for efficiency and waste reduction. It was developed by Taiichi Okono in Japan, during the 1970s & 1980s. TPS founder Kanji Takoda awarded him the Toyota Production System Award (TPS). Michael L. Watkins published the "The Machine That Changed the World", the first book about lean manufacturing. It was published in 1990.
Lean manufacturing refers to a set of principles that improve the quality, speed and costs of products and services. It is about eliminating defects and waste from all stages of the value stream. Lean manufacturing is also known as just in time (JIT), zero defect total productive maintenance(TPM), and five-star (S). Lean manufacturing is about eliminating activities that do not add value, such as inspection, rework, and waiting.
Lean manufacturing can help companies improve their product quality and reduce costs. Additionally, it helps them achieve their goals more quickly and reduces employee turnover. Lean manufacturing can be used to manage all aspects of the value chain. Customers, suppliers, distributors, retailers and employees are all included. Lean manufacturing practices are widespread in many industries. Toyota's philosophy is a great example of this. It has helped to create success in automobiles as well electronics, appliances and healthcare.
Five basic principles of Lean Manufacturing are included in lean manufacturing
-
Define Value- Identify the added value your company brings to society. What makes you stand out from your competitors?
-
Reduce Waste – Eliminate all activities that don't add value throughout the supply chain.
-
Create Flow: Ensure that the work process flows without interruptions.
-
Standardize and simplify - Make your processes as consistent as possible.
-
Build Relationships- Develop personal relationships with both internal as well as external stakeholders.
Although lean manufacturing has always been around, it is gaining popularity in recent years because of a renewed interest for the economy after 2008's global financial crisis. Many companies have adopted lean manufacturing methods to increase their marketability. Some economists even believe that lean manufacturing can be a key factor in economic recovery.
Lean manufacturing is becoming a popular practice in automotive. It has many advantages. These benefits include increased customer satisfaction, reduced inventory levels and lower operating costs.
You can apply Lean Manufacturing to virtually any aspect of your organization. This is because it ensures efficiency and effectiveness in all stages of the value chain.
There are three types principally of lean manufacturing:
-
Just-in-Time Manufacturing: Also known as "pull systems", this type of lean manufacturing uses just-in-time manufacturing (JIT). JIT stands for a system where components are assembled on the spot rather than being made in advance. This method reduces lead times, increases availability, and decreases inventory.
-
Zero Defects Manufacturing: ZDM ensures that no defective units leave the manufacturing plant. Repairing a part that is damaged during assembly should be done, not scrapping. This is true even for finished products that only require minor repairs prior to shipping.
-
Continuous Improvement: Continuous Improvement aims to improve efficiency by continually identifying problems and making adjustments to eliminate or minimize waste. Continuous improvement involves continuous improvement of processes and people as well as tools.