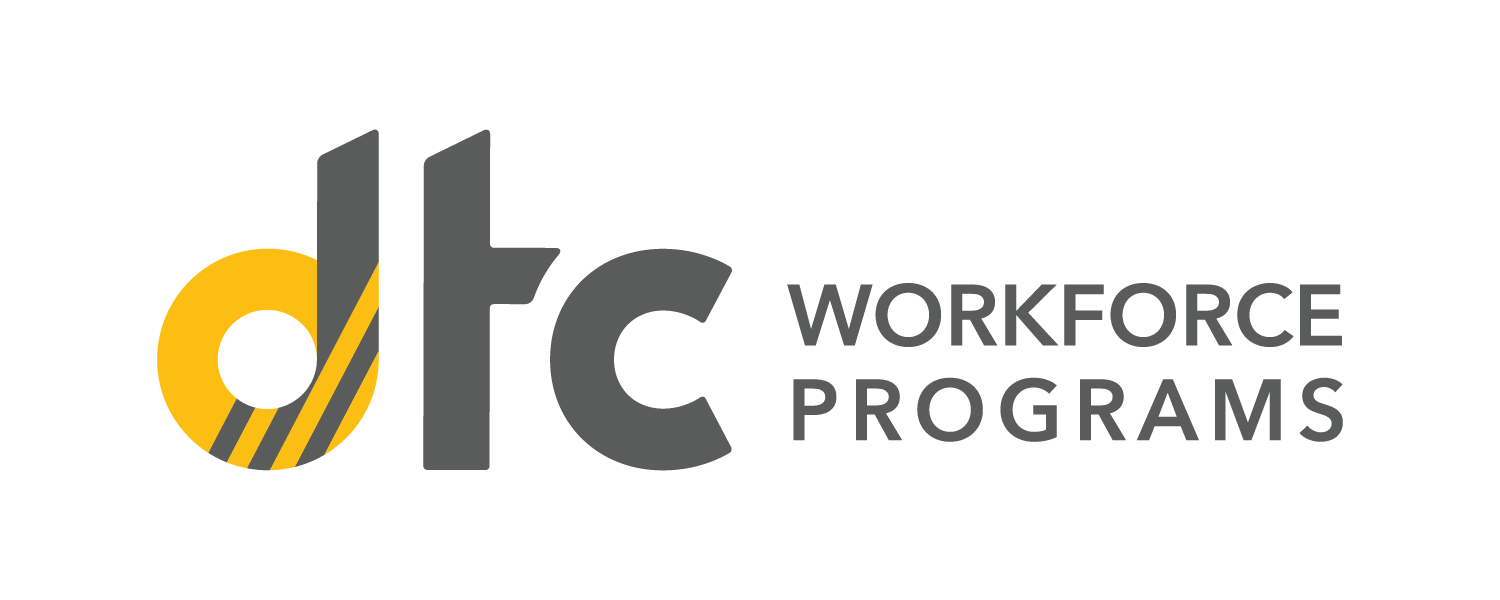
Businesses can use Just-in Time Production to produce products that meet customer demand. It relies on quality control and efficient workflows throughout manufacturing. It allows manufacturers lower inventory levels and less warehouse space. These benefits have lower costs.
JIT is a method that has helped many companies to lower their overall costs. However, it can be difficult to implement. JIT is not only dependent on operations coordination, but also the efficiency of the supply chains. This makes it susceptible to the disruptions that can occur on the global markets. There are many tools that can help you manage the JIT challenges.
JIT can be a cost-saving tool if used correctly. It also helps improve the quality of the final product. This technique can also improve the efficiency of both machine and human labor. Additionally, it helps to increase the speed and smoothness of the production cycle. It will reduce the time it takes to process unneeded output and also lower the environmental impact.
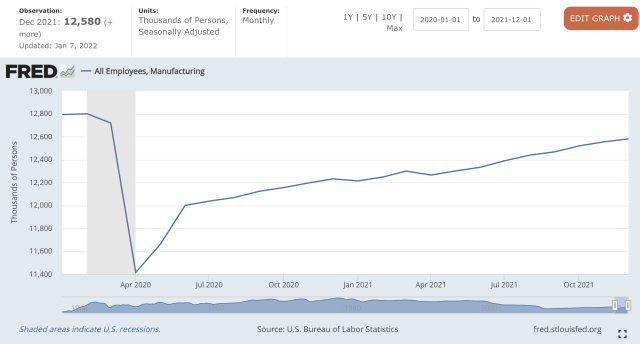
In Japan, the concept just-in-time production was initially introduced at the time of the advent of lean manufacturing. After World War II Japan was forced to rely upon limited resources. They had to streamline their manufacturing operations in order to survive. To maximize their output, they adopted JIT technologies.
Toyota's management team adapted the technique and transformed their production from a curious test to an exemplary success case in just a few years. This was a method that became so popular that other Japanese companies started to pay attention.
JIT is a very popular technique in Japan due to its effectiveness. The risks and benefits of JIT implementation should be understood by manufacturers before they embark on this project. It is important to establish strong relationships with suppliers in order for a JIT implementation to be successful. Suppliers can help minimize stock-keeping requirements and increase the speed of deliveries.
There are two main types of JIT methods. Pull and push. Push is the more conventional Make to Stock form of manufacturing. The push method can put pressure on other parts of the business. Retooling can also be costly. The pull method, in the same way, is based upon the actual demand for products.
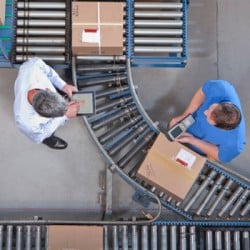
Both of these methods have been applied by many companies around the world. Implementing JIT successfully is all about empowering the workers involved to solve quality issues. JIT's effectiveness is also affected by factors such as complexity in manufacturing processes and length of time between supplier deliveries and manufacturer deliveries.
Ideally, a firm shouldn't have any stocks of raw materials or finished products. If it does have stock of finished products or raw materials, it should limit the number of reusable containers it has called kanban.
JIT strives to reduce waste while also maximising the efficiency of both machine and human labor. It is important to identify and eliminate any potential quality problems before they begin to occur.
FAQ
Why automate your factory?
Automation has become increasingly important in modern warehousing. E-commerce has brought increased demand for more efficient and quicker delivery times.
Warehouses need to adapt quickly to meet changing needs. Technology investment is necessary to enable warehouses to respond quickly to changing demands. Automation of warehouses offers many benefits. These are some of the benefits that automation can bring to warehouses:
-
Increases throughput/productivity
-
Reduces errors
-
Increases accuracy
-
Safety is boosted
-
Eliminates bottlenecks
-
This allows companies to scale easily
-
Makes workers more efficient
-
This gives you visibility into what happens in the warehouse
-
Enhances customer experience
-
Improves employee satisfaction
-
It reduces downtime, and increases uptime
-
This ensures that quality products are delivered promptly
-
Eliminates human error
-
Helps ensure compliance with regulations
What is the responsibility of a manufacturing manager?
Manufacturing managers must ensure that manufacturing processes are efficient, effective, and cost-effective. They must also be alert to any potential problems and take appropriate action.
They should also learn how to communicate effectively with other departments, including sales and marketing.
They should be informed about industry trends and be able make use of this information to improve their productivity and efficiency.
Can certain manufacturing steps be automated?
Yes! Since ancient times, automation has been in existence. The Egyptians invented the wheel thousands of years ago. Nowadays, we use robots for assembly lines.
In fact, there are several applications of robotics in manufacturing today. These include:
-
Automated assembly line robots
-
Robot welding
-
Robot painting
-
Robotics inspection
-
Robots create products
Automation can be applied to manufacturing in many other ways. 3D printing makes it possible to produce custom products in a matter of days or weeks.
Statistics
- Many factories witnessed a 30% increase in output due to the shift to electric motors. (en.wikipedia.org)
- You can multiply the result by 100 to get the total percent of monthly overhead. (investopedia.com)
- In 2021, an estimated 12.1 million Americans work in the manufacturing sector.6 (investopedia.com)
- [54][55] These are the top 50 countries by the total value of manufacturing output in US dollars for its noted year according to World Bank.[56] (en.wikipedia.org)
- It's estimated that 10.8% of the U.S. GDP in 2020 was contributed to manufacturing. (investopedia.com)
External Links
How To
Six Sigma and Manufacturing
Six Sigma is defined by "the application SPC (statistical process control) techniques to achieve continuous improvements." Motorola's Quality Improvement Department, Tokyo, Japan, developed it in 1986. Six Sigma is a method to improve quality through standardization and elimination of defects. This method has been adopted by many companies in recent years as they believe there are no perfect products or services. Six Sigma's primary goal is to reduce variation from the average value of production. This means that you can take a sample from your product and then compare its performance to the average to find out how often the process differs from the norm. If the deviation is excessive, it's likely that something needs to be fixed.
Understanding the dynamics of variability within your business is the first step in Six Sigma. Once you have a good understanding of the basics, you can identify potential sources of variation. This will allow you to decide if these variations are random and systematic. Random variations happen when people make errors; systematic variations are caused externally. For example, if you're making widgets, and some of them fall off the assembly line, those would be considered random variations. If however, you notice that each time you assemble a widget it falls apart in exactly the same spot, that is a problem.
Once you have identified the problem, you can design solutions. That solution might involve changing the way you do things or redesigning the process altogether. Test them again once you've implemented the changes. If they don’t work, you’ll need to go back and rework the plan.