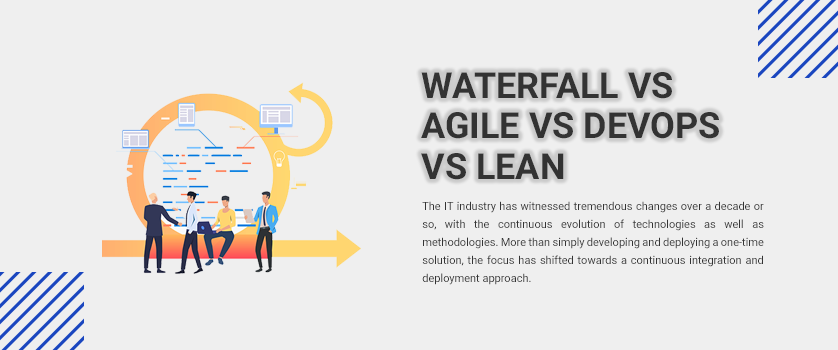
Purchasing Managers, also known as Materials Managers, are responsible for sourcing and coordinating all purchasing activities. They work with vendors, suppliers, and other purchasing agents. They need to know how to improve the company’s purchasing process. They must be able to negotiate for the best possible deals for the company.
Also, purchasing managers need to keep up-to date and accurate records of purchases. They analyze customer needs, analyze financial reports, evaluate vendor capabilities, and evaluate price trends. They also coordinate purchasing activities with other departments. They may need to work overtime when the company has urgent needs for supplies from international markets.
They coordinate and manage logistics and inventory. They make decisions about the best way to purchase products and ensure they meet company quality standards. They also manage budgets, and collaborate with their staff in order to ensure that purchases are made for the best price. They are also able to negotiate contracts and find the best suppliers.
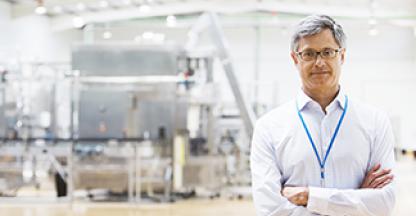
All purchasing employees must be monitored and managed by Purchasing managers. They also evaluate the quality of goods purchased, their speed of delivery and how much they cost. They also make contacts with suppliers and sellers and visit their distribution centers. They also make sure that suppliers comply with the terms of the contract. They might also need to address disciplinary issues or team building.
A Purchasing Manager should have exceptional communication skills, analytic abilities, and strategic thinking skills. They must be able to analyze the effect that various products have on the company. They must have the ability to manage suppliers, and their relationships. They should be able make business decisions, and increase sales. They also should be able to handle complicated purchases. They must be able to evaluate new vendors, analyze their capabilities, and select the best vendor for the company.
A bachelor's degree or equivalent in business is required of most purchasing managers. It's also beneficial to have experience in inventory and supply chain management. They must also have a knowledge of Microsoft Office, as well as other computer software programs.
The best purchasing managers should be able find the best deals and negotiate favorable contracts. They must be able manage inventory, coordinate purchasing activities and monitor supplier and vendor performance. They must also be able to manage a group of purchasing agents.
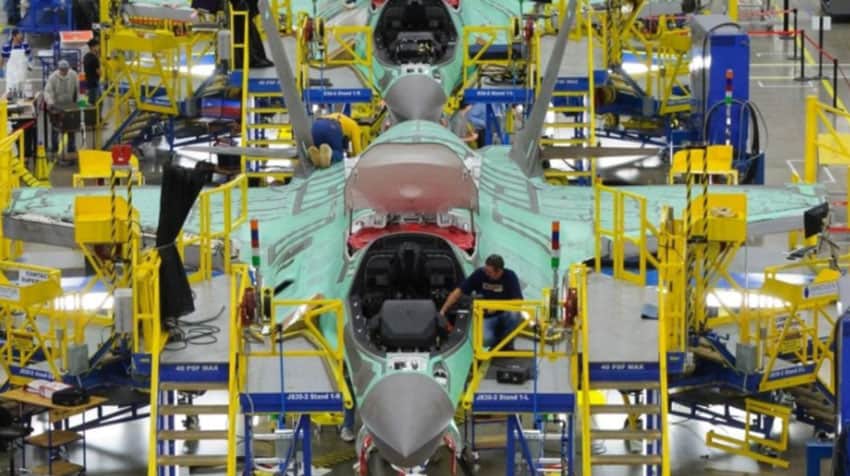
It is important that the job description for a purchase manager mentions how essential purchasing is to the company's success. It should also highlight how important it for the company's to be ahead of the game. It should also describe how the company values work-life balance. It should also include a call to action to urge applicants to apply.
If the company must purchase material or equipment for an overseas market, Purchasing managers might also be required to work overtime. They may also have to deal with vendors and sellers and attend trade shows.
FAQ
What is the role of a logistics manager
Logistics managers are responsible for ensuring that all goods arrive in perfect condition and on time. This is done using his/her knowledge of the company's products. He/she should ensure that sufficient stock is available in order to meet customer demand.
What skills is required for a production planner?
Being a production planner is not easy. You need to be organized and flexible. Also, you must be able and willing to communicate with clients and coworkers.
What does it mean to warehouse?
A warehouse is an area where goods are stored before being sold. It can be either an indoor or outdoor space. It could be one or both.
Is automation important for manufacturing?
Not only is automation important for manufacturers, but it's also vital for service providers. They can provide services more quickly and efficiently thanks to automation. In addition, it helps them reduce costs by reducing human errors and improving productivity.
What are the products of logistics?
Logistics refers to the movement of goods from one place to another.
These include all aspects related to transport such as packaging, loading and transporting, storing, transporting, unloading and warehousing inventory management, customer service. Distribution, returns, recycling are some of the options.
Logisticians ensure that the right product reaches the right place at the right time and under safe conditions. They assist companies with their supply chain efficiency through information on demand forecasts. Stock levels, production times, and availability.
They also keep track of shipments in transit, monitor quality standards, perform inventories and order replenishment, coordinate with suppliers and vendors, and provide support services for sales and marketing.
Statistics
- In 2021, an estimated 12.1 million Americans work in the manufacturing sector.6 (investopedia.com)
- Many factories witnessed a 30% increase in output due to the shift to electric motors. (en.wikipedia.org)
- Job #1 is delivering the ordered product according to specifications: color, size, brand, and quantity. (netsuite.com)
- According to the United Nations Industrial Development Organization (UNIDO), China is the top manufacturer worldwide by 2019 output, producing 28.7% of the total global manufacturing output, followed by the United States, Japan, Germany, and India.[52][53] (en.wikipedia.org)
- It's estimated that 10.8% of the U.S. GDP in 2020 was contributed to manufacturing. (investopedia.com)
External Links
How To
How to Use 5S for Increasing Productivity in Manufacturing
5S stands in for "Sort", the "Set In Order", "Standardize", or "Separate". The 5S methodology was developed at Toyota Motor Corporation in 1954. This methodology helps companies improve their work environment to increase efficiency.
The basic idea behind this method is to standardize production processes, so they become repeatable, measurable, and predictable. This means that tasks such as cleaning, sorting, storing, packing, and labeling are performed daily. This knowledge allows workers to be more efficient in their work because they are aware of what to expect.
There are five steps that you need to follow in order to implement 5S. Each step requires a different action to increase efficiency. By sorting, for example, you make it easy to find the items later. When items are ordered, they are put together. Once you have separated your inventory into groups and organized them, you will store these groups in easily accessible containers. Make sure everything is correctly labeled when you label your containers.
Employees must be able to critically examine their work practices. Employees need to understand the reasons they do certain jobs and determine if there is a better way. They must learn new skills and techniques in order to implement the 5S system.
In addition to increasing efficiency, the 5S method also improves morale and teamwork among employees. Once they start to notice improvements, they are motivated to keep working towards their goal of increasing efficiency.