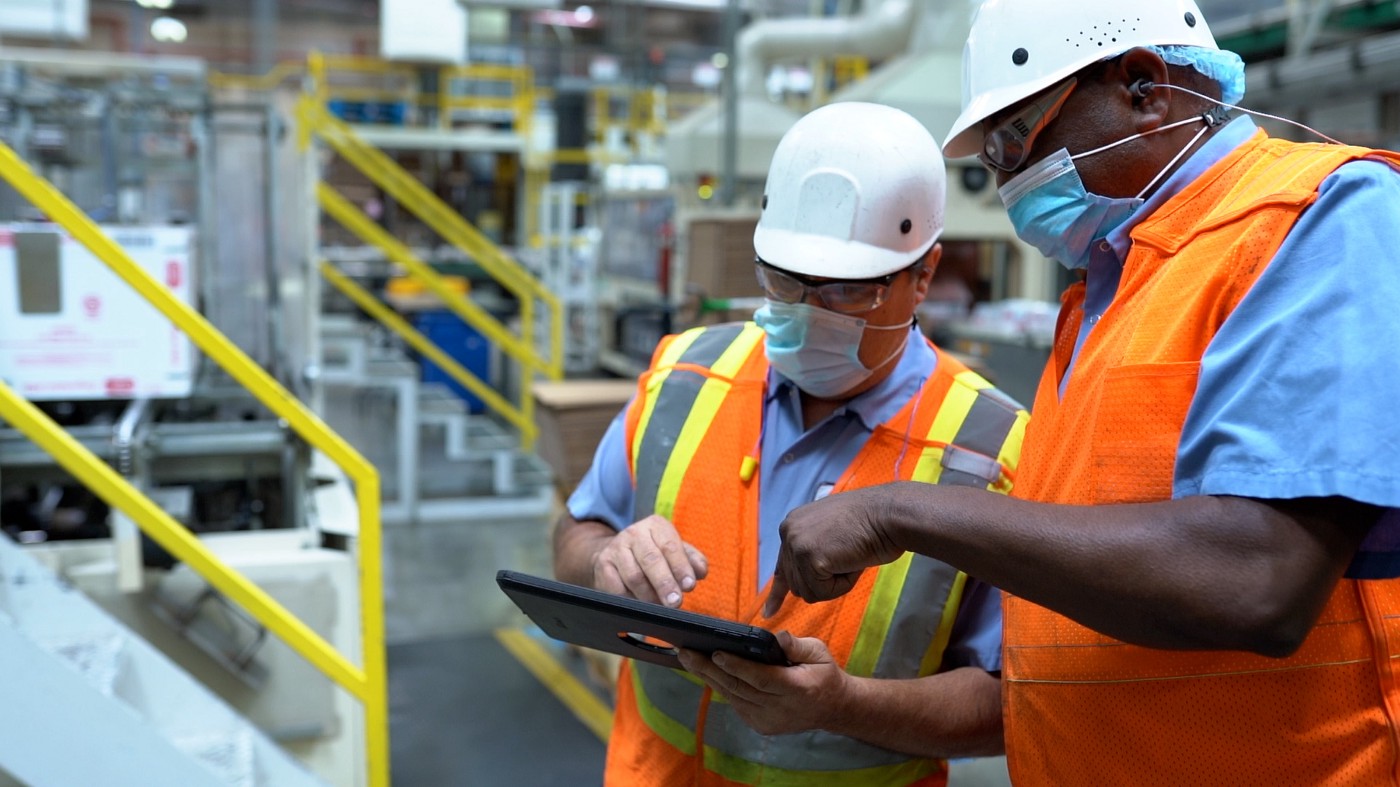
An accurate cost estimate is necessary for nearly every task a company undertakes. This task is performed by cost estimators. They assist companies in determining the cost of developing and manufacturing new products and services. They must also evaluate the costs of building a new structure. This includes the analysis of the labor and material costs.
Most cost estimators are employed by construction companies. They are expected to have a thorough understanding of construction processes and methods. They will also need to be familiarized with computer-aided planning (CAD). This software is used for improving the efficiency of design, and manufacturing. Additionally, cost estimators need to be capable of reading data from database. They can also use Microsoft Excel and other software.
They work closely with other professionals to produce accurate cost estimates. They evaluate the project blueprints, site conditions, and other materials to determine the costs of each component. They might also collaborate with engineers to determine the required gauges and machining operations.
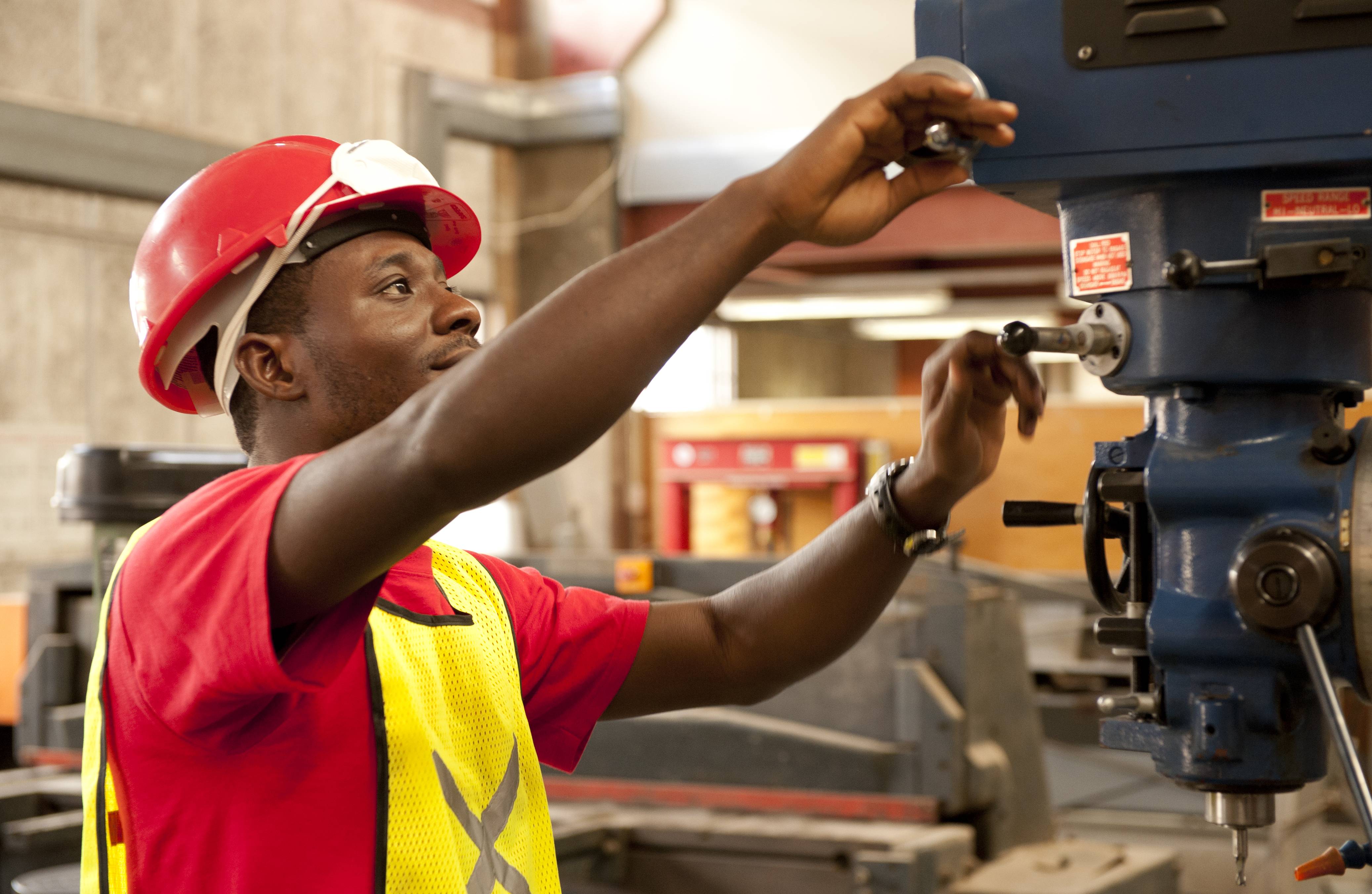
Cost estimators must be detail-oriented, assertive, and dependable. They must be able and willing to analyse difficult information. They should also be able present their findings clearly and persuasively. They must also be able and willing to collaborate with clients and professionals.
In most cases, cost estimators work for the engineering or cost department of a company. They should have strong math and science backgrounds. They should also be familiar with computer software, including CAD, BIM, and commercial software. They may also be required to take a certification course. Some certifications include the Certified Cost Estimator/Analyst (CCEA), Professional Cost Estimator/Analyst, and Certified Professional Estimator.
Cost estimators might be experts in particular services or industries. Some specialize in construction or building costs while others concentrate on software development. Cost estimators are also able to find work in other areas, such as auto repair and maintenance, construction, and specialty trade contractors.
Individuals in this occupation communicate with engineers, clients, and suppliers. They also have a good understanding of industry terminology. Before preparing cost estimates, they also have a lot of knowledge. These individuals are skilled in cost estimations and many others conduct studies to determine the effects of different processes on prices, and then find ways to reduce them.
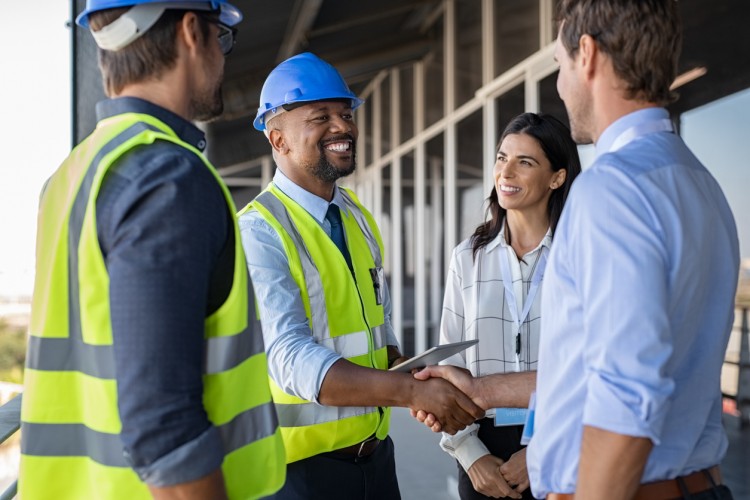
The industry may require job applicants to have a bachelor’s degree. They may also require an internship. They may also be eligible for cooperative education programs. Additionally, more construction companies are looking for people with a degree either in building construction or management.
They work in construction and other manufacturing companies. They provide accurate estimates to companies that enable them to make profitable bids. In addition, they analyze data related to the supply chain and other factors that affect costs. Government programs can also use cost estimators. They may also be asked to redesign products or services.
Cost estimators must have a strong understanding of computer-aided design (CAD) software. They can also be trained to use automatic cost estimation software.
FAQ
What is the role of a production manager?
A production planner ensures all aspects of the project are delivered on time, within budget, and within scope. They ensure that the product or service is of high quality and meets client requirements.
What is the importance of logistics in manufacturing?
Logistics are an essential component of any business. They can help you achieve great success by helping you manage product flow from raw material to finished goods.
Logistics are also important in reducing costs and improving efficiency.
Why automate your warehouse
Modern warehouses are increasingly dependent on automation. The rise of e-commerce has led to increased demand for faster delivery times and more efficient processes.
Warehouses should be able adapt quickly to new needs. They must invest heavily in technology to do this. Automating warehouses is a great way to save money. Here are some of the reasons automation is worth your investment:
-
Increases throughput/productivity
-
Reduces errors
-
Improves accuracy
-
Safety increases
-
Eliminates bottlenecks
-
Allows companies scale more easily
-
Workers are more productive
-
This gives you visibility into what happens in the warehouse
-
Enhances customer experience
-
Improves employee satisfaction
-
Reduces downtime and improves uptime
-
High quality products delivered on-time
-
Eliminates human error
-
It helps ensure compliance with regulations
What are my options for learning more about manufacturing
Practical experience is the best way of learning about manufacturing. However, if that's not possible, you can always read books or watch educational videos.
Statistics
- In 2021, an estimated 12.1 million Americans work in the manufacturing sector.6 (investopedia.com)
- According to the United Nations Industrial Development Organization (UNIDO), China is the top manufacturer worldwide by 2019 output, producing 28.7% of the total global manufacturing output, followed by the United States, Japan, Germany, and India.[52][53] (en.wikipedia.org)
- (2:04) MTO is a production technique wherein products are customized according to customer specifications, and production only starts after an order is received. (oracle.com)
- You can multiply the result by 100 to get the total percent of monthly overhead. (investopedia.com)
- It's estimated that 10.8% of the U.S. GDP in 2020 was contributed to manufacturing. (investopedia.com)
External Links
How To
How to Use lean manufacturing in the Production of Goods
Lean manufacturing refers to a method of managing that seeks to improve efficiency and decrease waste. It was developed in Japan between 1970 and 1980 by Taiichi Ohno. TPS founder Kanji Tyoda gave him the Toyota Production System, or TPS award. Michael L. Watkins published the "The Machine That Changed the World", the first book about lean manufacturing. It was published in 1990.
Lean manufacturing refers to a set of principles that improve the quality, speed and costs of products and services. It emphasizes the elimination of defects and waste throughout the value stream. Lean manufacturing can be described as just-in–time (JIT), total productive maintenance, zero defect (TPM), or even 5S. Lean manufacturing eliminates non-value-added tasks like inspection, rework, waiting.
Lean manufacturing is a way for companies to achieve their goals faster, improve product quality, and lower costs. Lean manufacturing can be used to manage all aspects of the value chain. Customers, suppliers, distributors, retailers and employees are all included. Many industries worldwide use lean manufacturing. Toyota's philosophy has been a key driver of success in many industries, including automobiles and electronics.
Five fundamental principles underlie lean manufacturing.
-
Define Value: Identify the social value of your business and what sets you apart.
-
Reduce Waste - Remove any activity which doesn't add value to your supply chain.
-
Create Flow – Ensure that work flows smoothly throughout the process.
-
Standardize & Simplify - Make processes as consistent and repeatable as possible.
-
Build Relationships- Develop personal relationships with both internal as well as external stakeholders.
Lean manufacturing, although not new, has seen renewed interest in the economic sector since 2008. Many businesses have adopted lean production techniques to make them more competitive. Many economists believe lean manufacturing will play a major role in economic recovery.
With many benefits, lean manufacturing is becoming more common in the automotive industry. These include better customer satisfaction and lower inventory levels. They also result in lower operating costs.
Any aspect of an enterprise can benefit from Lean manufacturing. This is because it ensures efficiency and effectiveness in all stages of the value chain.
There are three types of lean manufacturing.
-
Just-in Time Manufacturing: This lean manufacturing method is commonly called "pull systems." JIT is a process in which components can be assembled at the point they are needed, instead of being made ahead of time. This strategy aims to decrease lead times, increase availability of parts and reduce inventory.
-
Zero Defects Manufacturing: ZDM ensures that no defective units leave the manufacturing plant. It is better to repair a part than have it removed from the production line if it needs to be fixed. This is true even for finished products that only require minor repairs prior to shipping.
-
Continuous Improvement (CI: Continuous improvement aims to increase the efficiency of operations by constantly identifying and making improvements to reduce or eliminate waste. Continuous improvement refers to continuous improvement of processes as well people and tools.