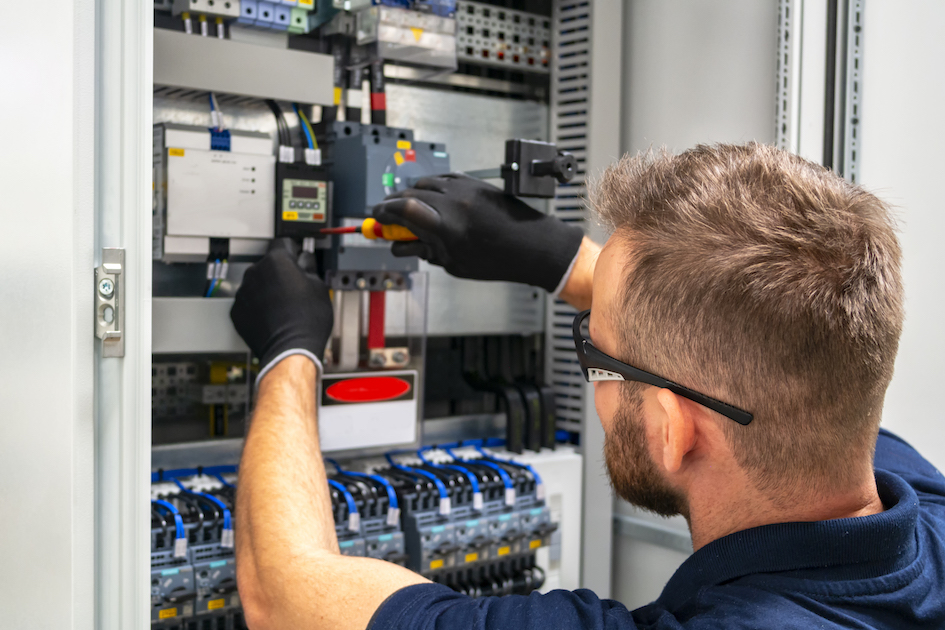
Durable goods have items that don't wear out quickly and can provide utility for a prolonged period. They are not like nondurable products, which can be used only once. They will provide greater or equal utility over time. A durable car, for example, will last many years.
Nondurable products can be consumed right away
Nondurable goods can be consumed right away, in contrast to durable goods which last a long time. In recessions, consumers are more likely to continue purchasing nondurable goods than to spend on durable goods. These items often have low prices, and can be purchased using cash. Nondurable goods can include meats, fruits and vegetables as well as dairy products and bakery items. Detergent, dish soap, cosmetics are just a few examples.
Nondurable goods last for three years or less, and they are generally the least expensive. Nondurable goods can be bought relatively frequently, which allows consumers to purchase them often without worrying about their future value. Nondurable goods, like packaged food or laundry detergent, are often disposable and can only be purchased once. However, service goods are intangible and are created in response to customer needs. The perception of a product by consumers is what drives their purchase decisions. This perception can change depending on the product's price.
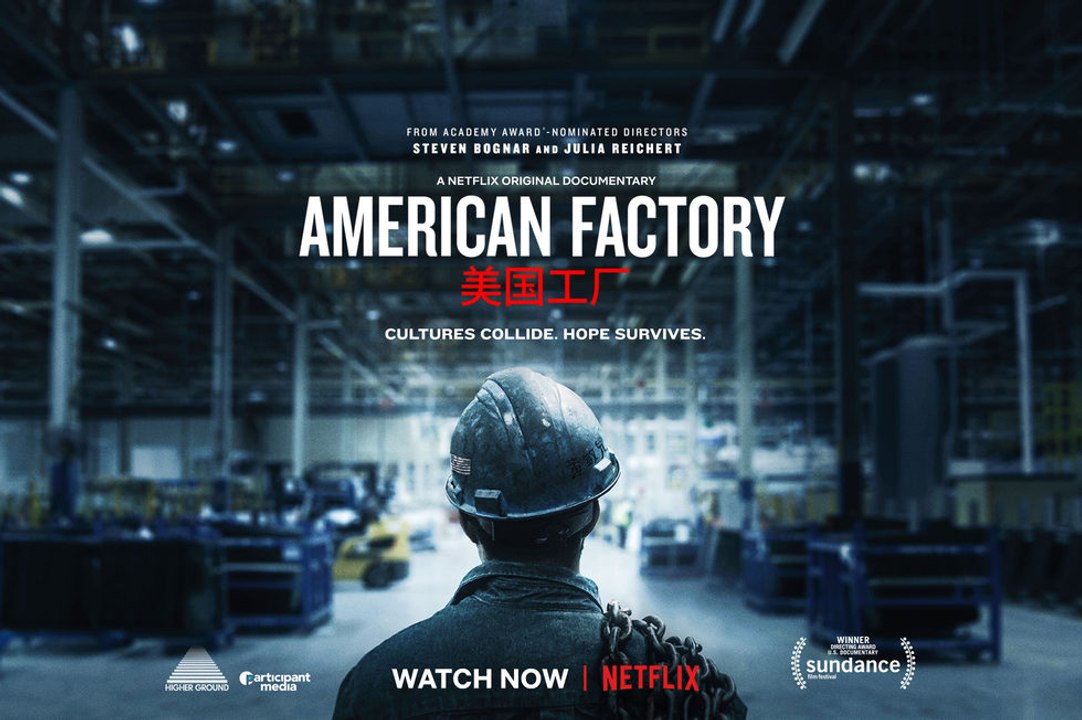
Durable goods on the other side are those products that will provide a continuous stream of utility over time. These products are also commonly known as consumer durables, and include automobiles, household furnishings, sporting goods, and jewelry. Durables are more popular during economic booms, while nondurables can be bought in periods of economic recession.
Durable goods last for longer than a calendar year
Durable goods refer to tangible commodities that can last for at most one year when used as intended. They can be classified into two main categories: producer durables as well as consumer durables. Consumer durables can include household goods like furniture, boats, and cars. Producer durables can include machinery, appliances, fine jewelry, as well as machinery.
Durable goods will last at most three years. But they may need repair or servicing. Durable goods are built so that breakage is unlikely within the first few years. Durable goods can be extended by proper care and maintenance for as long as 20 years.
When the economy is experiencing growth, the demand for durable goods is often a leading economic indicator. An increase in durable goods sales can result in higher employment and better returns on investment. On the other hand, declining sales of durable products could signal a decline economic activity. This could mean that consumers are spending their money on repairs and maintenance of their products, rather than buying new ones. As a result, a slowdown in durable goods may lead to a recession.
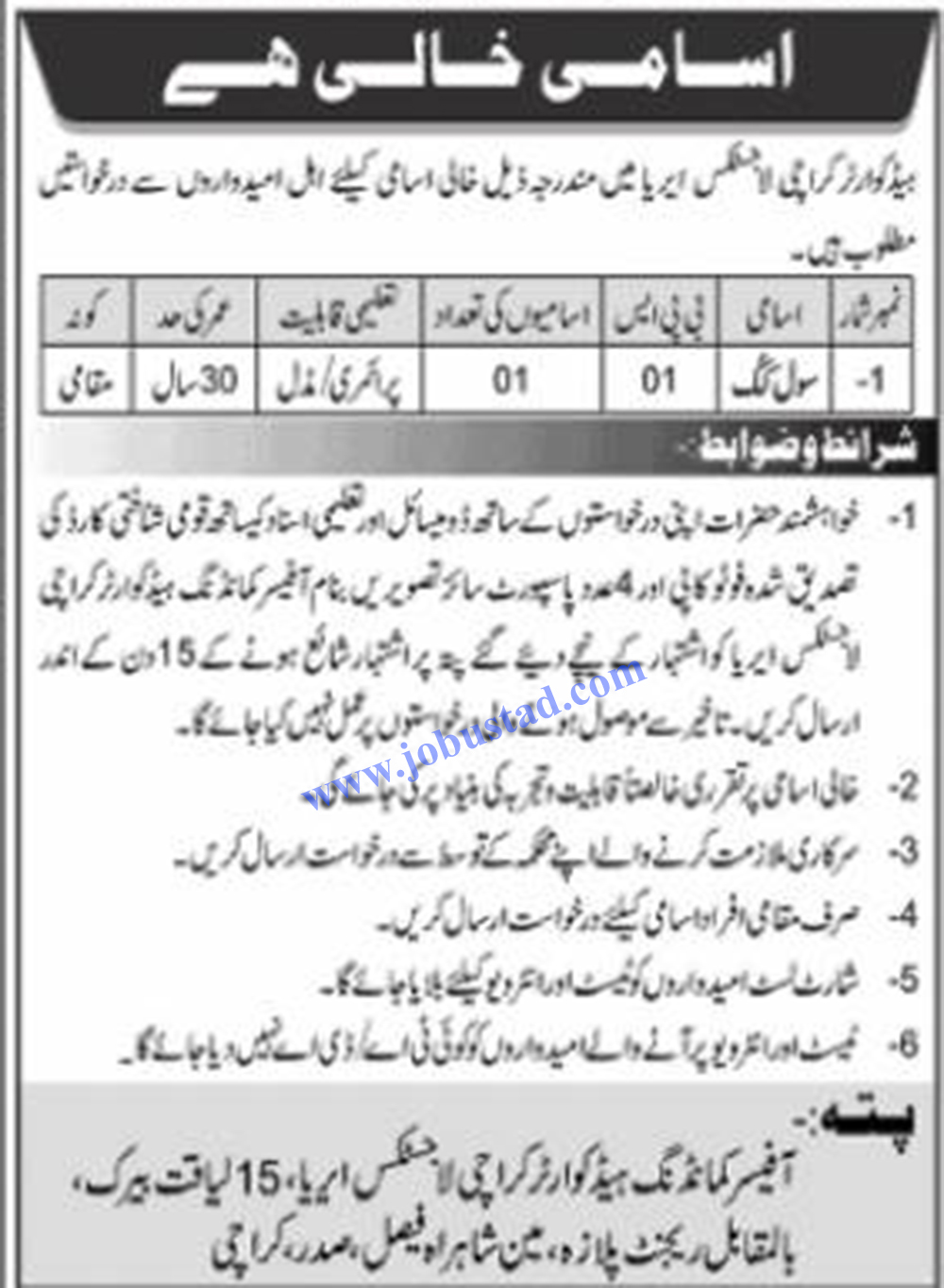
Impact of COVID-19-pandemic pandemics on durable goods
COVID-19, which was a pandemic that brought about widespread illness, has had a significant impact on consumer spending. Due to the disease, many people stopped going to gym or social events and moved into the house. People also stopped hailing taxis, which led to a decrease in consumer spending. Instead, people spent more time at their homes doing home production and leisure activities. This resulted in a decrease in consumer spending on other services and restaurants.
The US economy is seeing dramatic effects from the COVID-19 outbreak. Not only did the disease increase demand for durable products, but it also led to strong fiscal policies that increased household disposable income. This effect could be responsible for half the rise in consumer durable good spending in 2020.
The COVID-19 Pandemic has impacted individuals, communities, as well as businesses. While attention has been focused on the effect on fast-moving items, less has been done on the impact on durable goods. NielsenIQ BASES's new survey shows that almost a third (33%) of people have made durables purchases as a result of the disease. The disease has also affected consumers' purchasing habits because they spend more of their time at home caring for children.
FAQ
What kind of jobs are there in logistics?
There are many kinds of jobs available within logistics. Some examples are:
-
Warehouse workers – They load and unload pallets and trucks.
-
Transport drivers - These are people who drive trucks and trailers to transport goods or perform pick-ups.
-
Freight handlers - They sort and pack freight in warehouses.
-
Inventory managers – These people oversee inventory at warehouses.
-
Sales representatives - They sell products.
-
Logistics coordinators are responsible for organizing and planning logistics operations.
-
Purchasing agents - They purchase goods and services needed for company operations.
-
Customer service representatives - They answer calls and emails from customers.
-
Shippers clerks - They process shipping order and issue bills.
-
Order fillers - They fill orders based on what is ordered and shipped.
-
Quality control inspectors – They inspect incoming and outgoing products to ensure that there are no defects.
-
Others - There are many types of jobs in logistics such as transport supervisors and cargo specialists.
Can some manufacturing processes be automated?
Yes! Yes. Automation has been around since ancient time. The Egyptians invent the wheel thousands of year ago. We now use robots to help us with assembly lines.
There are many applications for robotics in manufacturing today. They include:
-
Automated assembly line robots
-
Robot welding
-
Robot painting
-
Robotics inspection
-
Robots that create products
Manufacturing can also be automated in many other ways. 3D printing makes it possible to produce custom products in a matter of days or weeks.
How can manufacturing avoid production bottlenecks
You can avoid bottlenecks in production by making sure that everything runs smoothly throughout the production cycle, from the moment you receive an order to the moment the product is shipped.
This includes both planning for capacity and quality control.
This can be done by using continuous improvement techniques, such as Six Sigma.
Six Sigma can be used to improve the quality and decrease waste in all areas of your company.
It seeks to eliminate variation and create consistency in your work.
What does it take to run a logistics business?
It takes a lot of skills and knowledge to run a successful logistics business. To communicate effectively with clients and suppliers, you must be able to communicate well. You must be able analyze data and draw out conclusions. You must be able manage stress and pressure under pressure. You need to be innovative and creative to come up with new ways to increase efficiency. Strong leadership qualities are essential to motivate your team and help them achieve their organizational goals.
You should also be organized and efficient to meet tight deadlines.
What is the difference between Production Planning and Scheduling?
Production Planning (PP), also known as forecasting and identifying production capacities, is the process that determines what product needs to be produced at any particular time. This is done through forecasting demand and identifying production capacities.
Scheduling refers the process by which tasks are assigned dates so that they can all be completed within the given timeframe.
How can I learn about manufacturing?
The best way to learn about manufacturing is through hands-on experience. However, if that's not possible, you can always read books or watch educational videos.
What does "warehouse" mean?
A warehouse or storage facility is where goods are stored before they are sold. It can be either an indoor or outdoor space. In some cases it could be both indoors and outdoors.
Statistics
- (2:04) MTO is a production technique wherein products are customized according to customer specifications, and production only starts after an order is received. (oracle.com)
- [54][55] These are the top 50 countries by the total value of manufacturing output in US dollars for its noted year according to World Bank.[56] (en.wikipedia.org)
- You can multiply the result by 100 to get the total percent of monthly overhead. (investopedia.com)
- According to a Statista study, U.S. businesses spent $1.63 trillion on logistics in 2019, moving goods from origin to end user through various supply chain network segments. (netsuite.com)
- In 2021, an estimated 12.1 million Americans work in the manufacturing sector.6 (investopedia.com)
External Links
How To
How to use lean manufacturing in the production of goods
Lean manufacturing is a management style that aims to increase efficiency and reduce waste through continuous improvement. It was developed by Taiichi Okono in Japan, during the 1970s & 1980s. TPS founder Kanji Takoda awarded him the Toyota Production System Award (TPS). Michael L. Watkins published the original book on lean manufacturing, "The Machine That Changed the World," in 1990.
Lean manufacturing refers to a set of principles that improve the quality, speed and costs of products and services. It is about eliminating defects and waste from all stages of the value stream. Lean manufacturing can be described as just-in–time (JIT), total productive maintenance, zero defect (TPM), or even 5S. Lean manufacturing eliminates non-value-added tasks like inspection, rework, waiting.
In addition to improving product quality and reducing costs, lean manufacturing helps companies achieve their goals faster and reduces employee turnover. Lean manufacturing has been deemed one of the best ways to manage the entire value-chain, including customers, distributors as well retailers and employees. Lean manufacturing can be found in many industries. Toyota's philosophy is the foundation of its success in automotives, electronics and appliances, healthcare, chemical engineers, aerospace, paper and food, among other industries.
Lean manufacturing includes five basic principles:
-
Define Value - Identify the value your business adds to society and what makes you different from competitors.
-
Reduce Waste – Eliminate all activities that don't add value throughout the supply chain.
-
Create Flow – Ensure that work flows smoothly throughout the process.
-
Standardize & simplify - Make processes consistent and repeatable.
-
Build Relationships - Establish personal relationships with both internal and external stakeholders.
Lean manufacturing, although not new, has seen renewed interest in the economic sector since 2008. Many businesses have adopted lean manufacturing techniques to help them become more competitive. In fact, some economists believe that lean manufacturing will be an important factor in economic recovery.
Lean manufacturing, which has many benefits, is now a standard practice in the automotive industry. These include higher customer satisfaction, lower inventory levels, lower operating expenses, greater productivity, and improved overall safety.
You can apply Lean Manufacturing to virtually any aspect of your organization. Lean manufacturing is most useful in the production sector of an organisation because it ensures that each step in the value-chain is efficient and productive.
There are three types principally of lean manufacturing:
-
Just-in Time Manufacturing, (JIT): This kind of lean manufacturing is also commonly known as "pull-systems." JIT is a method in which components are assembled right at the moment of use, rather than being manufactured ahead of time. This strategy aims to decrease lead times, increase availability of parts and reduce inventory.
-
Zero Defects Manufacturing, (ZDM): ZDM is focused on ensuring that no defective products leave the manufacturing facility. If a part is required to be repaired on the assembly line, it should not be scrapped. This applies to finished products, which may need minor repairs before they are shipped.
-
Continuous Improvement (CI: Continuous improvement aims to increase the efficiency of operations by constantly identifying and making improvements to reduce or eliminate waste. Continuous Improvement (CI) involves continuous improvement in processes, people, tools, and infrastructure.