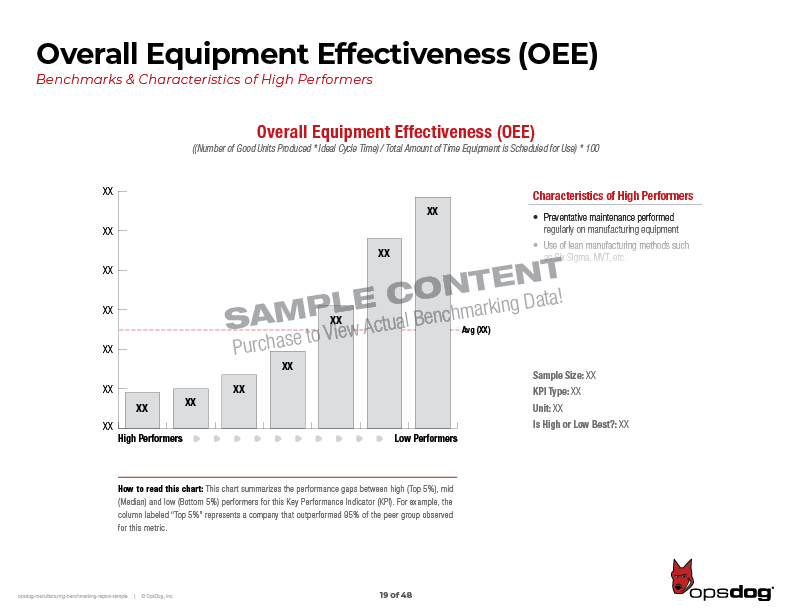
The United States is seeing a decrease in manufacturing jobs. This trend has also affected non-college educated workers. This includes Black workers, women, and minorities. These groups have been left behind by the decline in manufacturing jobs. Here is a look at how many people are left behind.
Trends in Manufacturing Employment
The impact of globalization is a major concern regarding trends in US manufacturing employment in 2019. The industry employs approximately 40 million people but is losing 3.5 million jobs each year. This decrease is due to macroeconomic variables, including government spending, taxation, Federal Reserve actions, and job losses.
The demand for entry-level labor in the manufacturing sector is growing. Since its peak in early 20th century, the share of manufacturing jobs has been declining steadily. In 1952, nearly 32% of the workforce was employed in manufacturing. That figure has dropped to 8 percent by 2019. A few economists don't consider this to be a manufacturing slump. However, it is lower than the average during a recession. The ISM Index for example is 47.2, which is more than the low 40s during a downturn.
There were eight regions in the United States that had manufacturing jobs. This was a stark contrast to the other areas. Northeast had the highest concentration of manufacturing jobs. The mid-Atlantic state had the lowest concentrations of manufacturing jobs.
Trends in manufacturing output
The manufacturing sector in the US is one of the key indicators of the economy. The recent rebound in manufacturing output suggests that the economy has experienced extended growth. Manufacturers face numerous challenges. In addition to rising costs, it is getting harder to find raw materials and components, as well as labor. Abhijit Bhide examines five trends that are impacting the US manufacturing sector. He also discusses what these changes mean for small and mid-sized businesses.
While younger people are more likely to believe that manufacturing output in the US has increased, older individuals are less likely to say that it has declined. In fact, half of the people between 50 and 64 believe that manufacturing output has increased in three years, as opposed to 39% for those between 18-29. A second factor that influences perceptions of manufacturing output is income. The perception of manufacturing output is affected by income levels. Those who earn $100,000 per year are more likely than those who earn $30,000 to 49999 to believe that manufacturing output is lower.
FAQ
What is the difference between Production Planning, Scheduling and Production Planning?
Production Planning (PP), or production planning, is the process by which you determine what products are needed at any given time. This is done through forecasting demand and identifying production capacities.
Scheduling refers the process by which tasks are assigned dates so that they can all be completed within the given timeframe.
What is the best way to learn about manufacturing?
You can learn the most about manufacturing by getting involved in it. You can also read educational videos or take classes if this isn't possible.
Why is logistics important for manufacturing?
Logistics are an essential part of any business. They enable you to achieve outstanding results by helping manage product flow from raw materials through to finished goods.
Logistics play an important role in reducing costs as well as increasing efficiency.
Statistics
- According to the United Nations Industrial Development Organization (UNIDO), China is the top manufacturer worldwide by 2019 output, producing 28.7% of the total global manufacturing output, followed by the United States, Japan, Germany, and India.[52][53] (en.wikipedia.org)
- Many factories witnessed a 30% increase in output due to the shift to electric motors. (en.wikipedia.org)
- You can multiply the result by 100 to get the total percent of monthly overhead. (investopedia.com)
- It's estimated that 10.8% of the U.S. GDP in 2020 was contributed to manufacturing. (investopedia.com)
- In the United States, for example, manufacturing makes up 15% of the economic output. (twi-global.com)
External Links
How To
How to Use lean manufacturing in the Production of Goods
Lean manufacturing is a management system that aims at increasing efficiency and reducing waste. It was first developed in Japan in the 1970s/80s by Taiichi Ahno, who was awarded the Toyota Production System (TPS), award from KanjiToyoda, the founder of TPS. Michael L. Watkins published the first book on lean manufacturing in 1990.
Lean manufacturing is often defined as a set of principles used to improve the quality, speed, and cost of products and services. It emphasizes eliminating waste and defects throughout the value stream. The five-steps of Lean Manufacturing are just-in time (JIT), zero defect and total productive maintenance (TPM), as well as 5S. Lean manufacturing is about eliminating activities that do not add value, such as inspection, rework, and waiting.
Lean manufacturing improves product quality and costs. It also helps companies reach their goals quicker and decreases employee turnover. Lean Manufacturing is one of the most efficient ways to manage the entire value chains, including suppliers and customers as well distributors and retailers. Lean manufacturing is widely used in many industries. Toyota's philosophy, for example, is what has enabled it to be successful in electronics, automobiles, medical devices, healthcare and chemical engineering as well as paper and food.
Five basic principles of Lean Manufacturing are included in lean manufacturing
-
Define Value - Determine the value that your business brings to society. Also, identify what sets you apart from your competitors.
-
Reduce waste - Get rid of any activity that does not add value to the supply chain.
-
Create Flow: Ensure that the work process flows without interruptions.
-
Standardize & simplify - Make processes consistent and repeatable.
-
Build relationships - Develop and maintain personal relationships with both your internal and external stakeholders.
Lean manufacturing isn’t new, but it has seen a renewed interest since 2008 due to the global financial crisis. Many companies have adopted lean manufacturing methods to increase their marketability. Some economists even believe that lean manufacturing can be a key factor in economic recovery.
With many benefits, lean manufacturing is becoming more common in the automotive industry. These include better customer satisfaction and lower inventory levels. They also result in lower operating costs.
Any aspect of an enterprise can benefit from Lean manufacturing. Lean manufacturing is most useful in the production sector of an organisation because it ensures that each step in the value-chain is efficient and productive.
There are three types principally of lean manufacturing:
-
Just-in-Time Manufacturing: Also known as "pull systems", this type of lean manufacturing uses just-in-time manufacturing (JIT). JIT means that components are assembled at the time of use and not manufactured in advance. This approach reduces lead time, increases availability and reduces inventory.
-
Zero Defects Manufacturing (ZDM),: ZDM is a system that ensures no defective units are left the manufacturing facility. Repairing a part that is damaged during assembly should be done, not scrapping. This is true even for finished products that only require minor repairs prior to shipping.
-
Continuous Improvement (CI: Continuous improvement aims to increase the efficiency of operations by constantly identifying and making improvements to reduce or eliminate waste. It involves continuous improvement of processes, people, and tools.