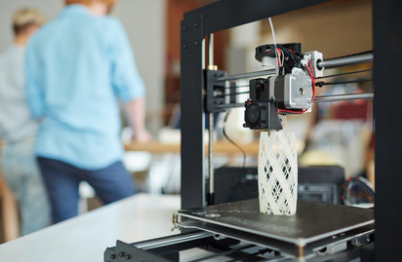
Until recently "Made in Japan", meant low quality consumer goods. Japanese products now have a reputation for being durable, precise, and reliable. Japanese manufacturers are also imposing stricter standards. This has led to increased costs and increased competition. Japanese companies are also being asked how fast they can adapt to changing market conditions.
Japanese factories are highly controlled. They control the work content, labor, and working relationships. This is possible by training their employees to make high-quality products. They also encourage feedback from their customers, quality inspectors, and vendors.
Japan's manufacturing tradition is rooted in Japan's culture of discipline and cultural conformity. It has been influenced by technology. Many Japanese companies employ artificial intelligence to supplement their non-manufacturing labor. The next wave of technology promises to further augment non-manufacturing labor. This includes robots who will work in factories, hospitals, temples, schools, and nursing homes.
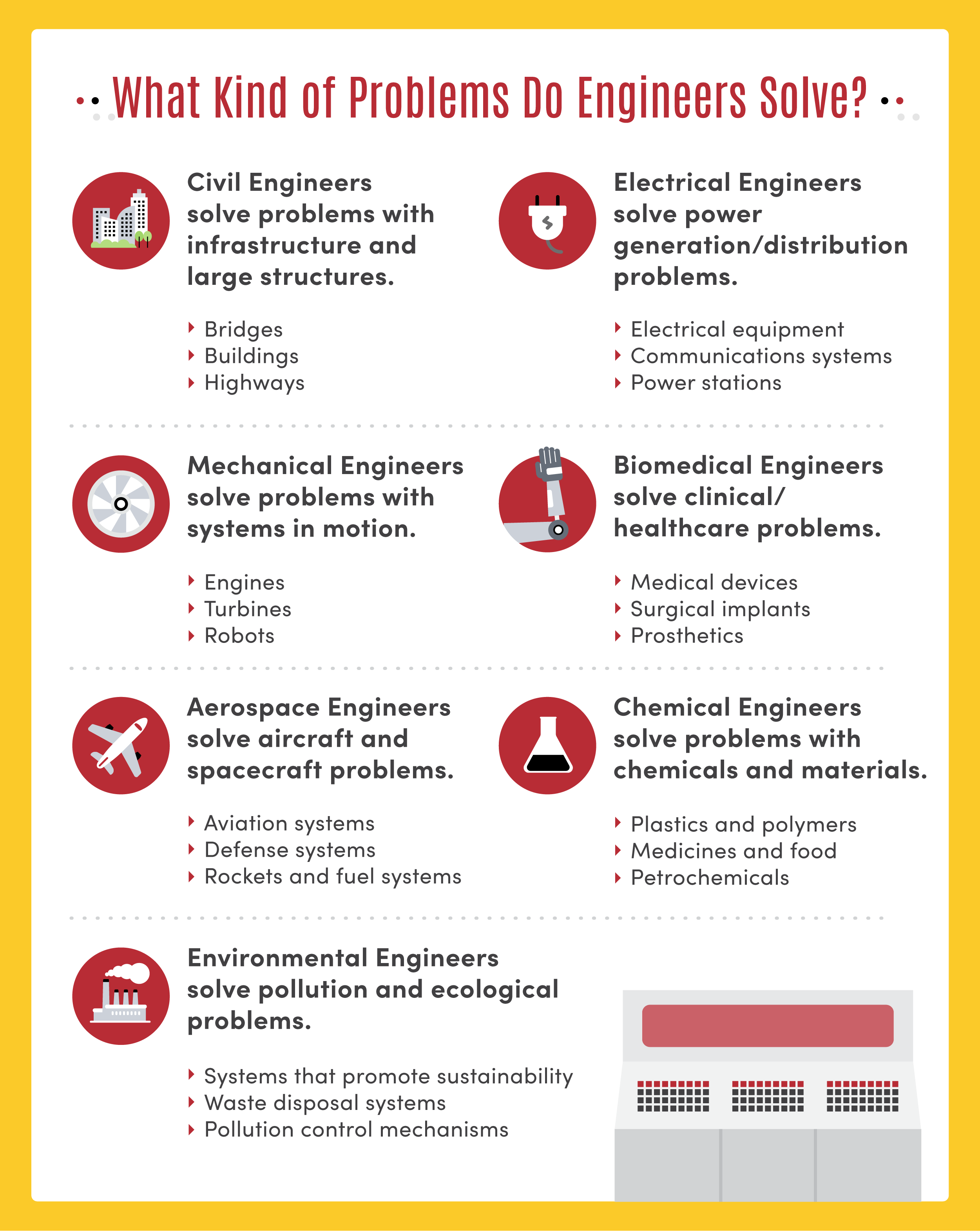
There have been many safety scandals. One was a 13-year old girl who died from complications from a factory illness. Another involved a company that admitted to improper vehicle inspection procedures. These scandals have made it difficult to inspect the Japanese factory floor. The work environment has also been affected by several strikes of workers. In response to these problems, the government has imposed new regulations, such as closed loop management, which isolates workers to prevent virus transmission.
Japan's ageing population is another major factor that impacts the country's manufacturing industry. The Japanese birth rate is decreasing, which means there is a shortage of labor. This demand is not being met by enough labor in Japan. Japanese manufacturing requires foreign workers to grow. But many factories are unable to source supplies. This is causing problems in their supply chain.
Japanese manufacturers work closely with their suppliers in order to solve problems. Japanese companies often hold seminars for suppliers to help them better meet customer needs. They also screen incoming parts to make sure that they meet specifications. They also employ advanced technology, such an automatic checker, to identify defects before they happen.
Many of their products showcase the best of Japanese manufacture. Japanese automobiles, for example, are known for their fuel economy, durability, and excellent quality. Japan's automobile industry is one of the most important in the world. Six out of the top ten automotive manufacturers, including Toyota, Honda and Suzuki, are located in Japan. They are known for producing vehicles with higher quality features at a cheaper price.
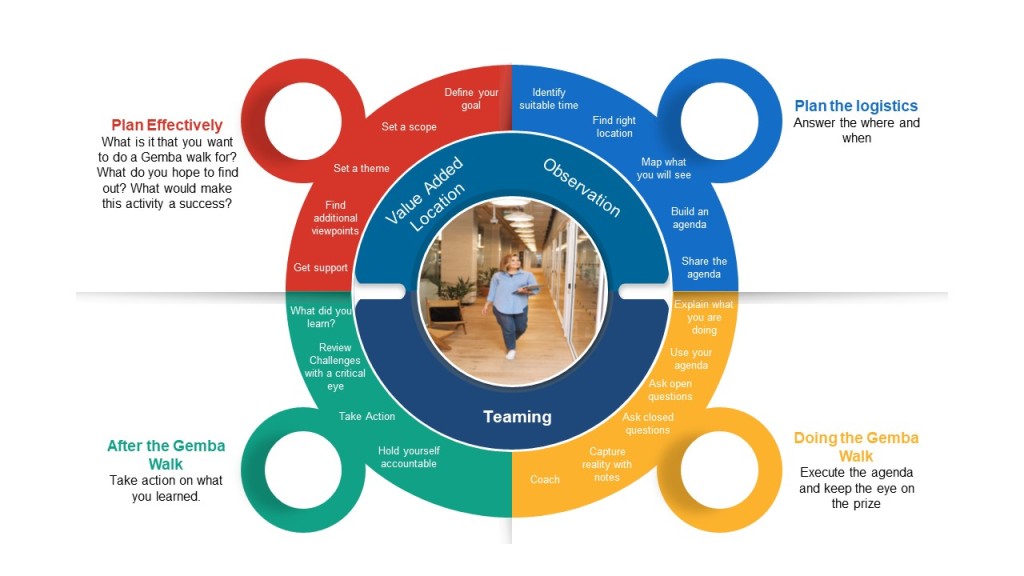
The industry will also be impacted by the next wave of technology, especially in terms wages. Robots are already replacing human workers in field service organizations. These workers report directly back to either sales managers or manufacturing executives. The future of automation will extend beyond Japanese factories. Robots will even work in hospitals and train stations.
Japan is also having problems with its supply chain. This has led to a slowdown in exports as well as clogging of the port. Another problem is the increase in non-regular labor, which has led to lower standards and reduced costs.
FAQ
Is there anything we should know about Manufacturing Processes prior to learning about Logistics.
No. No. It is important to know about the manufacturing processes in order to understand how logistics works.
What is the difference in Production Planning and Scheduling, you ask?
Production Planning (PP) refers to the process of determining how much production is needed at any given moment. Forecasting and identifying production capacity are two key elements to this process.
Scheduling is the process of assigning specific dates to tasks so they can be completed within the specified timeframe.
What makes a production planner different from a project manger?
The primary difference between a producer planner and a manager of a project is that the manager usually plans and organizes the whole project, while a production planner is only involved in the planning stage.
What are the 7 Rs of logistics?
The 7R's of Logistics is an acronym for the seven basic principles of logistics management. It was developed and published by the International Association of Business Logisticians in 2004 as part of the "Seven Principles of Logistics Management".
The acronym is composed of the following letters.
-
Responsible – ensure that all actions are legal and don't cause harm to anyone else.
-
Reliable - You can have confidence that you will fulfill your promises.
-
Reasonable - make sure you use your resources well and don't waste them.
-
Realistic – consider all aspects of operations, from cost-effectiveness to environmental impact.
-
Respectful: Treat others with fairness and equity
-
Resourceful - look for opportunities to save money and increase productivity.
-
Recognizable - Provide value-added services to customers
How can manufacturing efficiency improved?
The first step is to identify the most important factors affecting production time. Then we need to find ways to improve these factors. You can start by identifying the most important factors that impact production time. Once you have identified the factors, then try to find solutions.
What is the importance of automation in manufacturing?
Automation is important not only for manufacturers but also for service providers. Automation allows them to deliver services quicker and more efficiently. It reduces human errors and improves productivity, which in turn helps them lower their costs.
Statistics
- (2:04) MTO is a production technique wherein products are customized according to customer specifications, and production only starts after an order is received. (oracle.com)
- It's estimated that 10.8% of the U.S. GDP in 2020 was contributed to manufacturing. (investopedia.com)
- According to a Statista study, U.S. businesses spent $1.63 trillion on logistics in 2019, moving goods from origin to end user through various supply chain network segments. (netsuite.com)
- Many factories witnessed a 30% increase in output due to the shift to electric motors. (en.wikipedia.org)
- Job #1 is delivering the ordered product according to specifications: color, size, brand, and quantity. (netsuite.com)
External Links
How To
Six Sigma: How to Use it in Manufacturing
Six Sigma is defined as "the application of statistical process control (SPC) techniques to achieve continuous improvement." Motorola's Quality Improvement Department created Six Sigma at their Tokyo plant, Japan in 1986. The basic idea behind Six Sigma is to improve quality by improving processes through standardization and eliminating defects. Since there are no perfect products, or services, this approach has been adopted by many companies over the years. Six Sigma's primary goal is to reduce variation from the average value of production. It is possible to measure the performance of your product against an average and find the percentage of time that it differs from the norm. If there is a significant deviation from the norm, you will know that something needs to change.
Understanding the dynamics of variability within your business is the first step in Six Sigma. Once you have this understanding, you will need to identify sources and causes of variation. These variations can also be classified as random or systematic. Random variations happen when people make errors; systematic variations are caused externally. You could consider random variations if some widgets fall off the assembly lines. If however, you notice that each time you assemble a widget it falls apart in exactly the same spot, that is a problem.
Once you've identified where the problems lie, you'll want to design solutions to eliminate those problems. You might need to change the way you work or completely redesign the process. To verify that the changes have worked, you need to test them again. If they don’t work, you’ll need to go back and rework the plan.