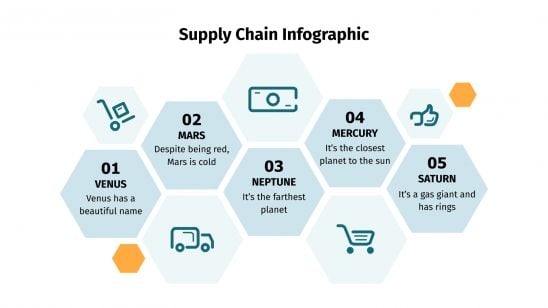
Toyota has maintained its focus on quality, despite all its successes. Toyota has become a leading automotive brand thanks to its unwavering commitment towards excellence.
Toyota's strategy rests on being true to its core values, focusing only on incremental innovations and encouraging smart growth. It emphasizes the importance in building and maintaining relationships with dealers. Toyota values its customers more than other companies who may be dependent on stock price. This is because the automobile industry is highly competitive and a company's success depends on its ability to innovate.
Toyota employees must be able to face challenges in order to continue to achieve success. Toyota encourages employees in this area to explore and create new ideas. To do this, Toyota encourages open communication and challenges employees to overcome differences and compromises. On-the-job training is a way to achieve this. Employees are also encouraged to be open about problems and mistakes.
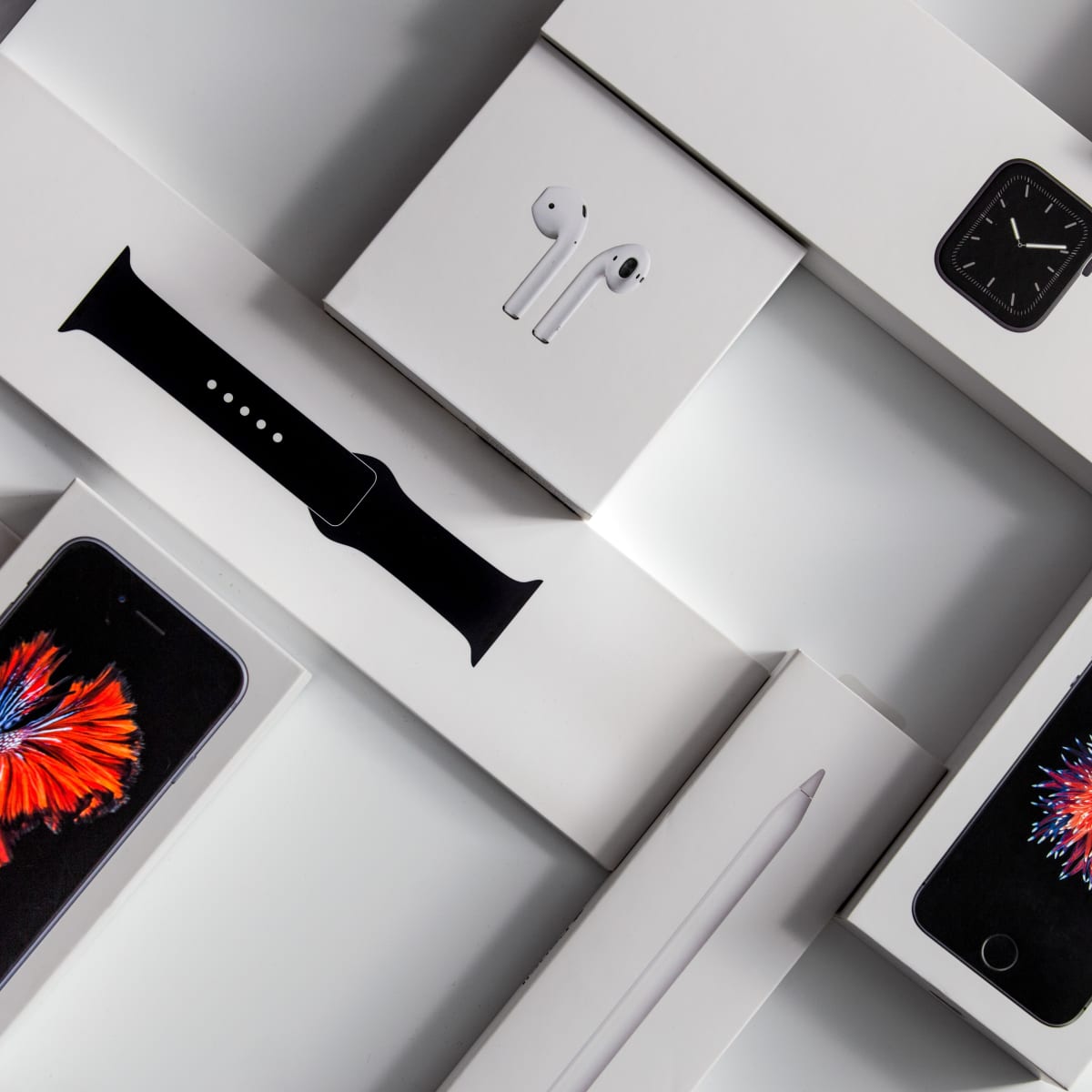
Toyota's success is also possible through continuous improvement (kaizen). The process involves streamlining processes and testing new ideas. This process, also known in Japanese as Genchi genbutsu (or "Genchi genbutsu"), helps Toyota achieve its goals. It is also an integral part Toyota's culture. It has been the foundation of Toyota's success for many decades.
Toyota established a research center as one of its first major decisions. Its founder, Kiichiro Toyoda, believed that if the automobile industry was to remain competitive, it would need to develop new technologies from scratch. In the late 1930s, he set up a research facility. He dreamed of a Japan that could produce automobiles and other technology independently.
Toyota made many strategic moves during the 1950s. It started diversifying its product line and exporting cars all over the globe. It also set up a separate sales firm and established a network dealers. It began to understand the international automotive market. It was able to see that American and European automakers would overtake Toyota if Toyota attempted to compete in the global market.
Another major move that Toyota made in the '50s was to launch its own American division. The move was made because the American workforce is nine times more productive that Japanese workers. It realized that fuel-efficient cars were in demand. It was required to convince the American public that Japanese cars were an excellent investment. It also had to overcome a major strike that crippled the company in the 1950s. It had to obtain loans and trim staff.
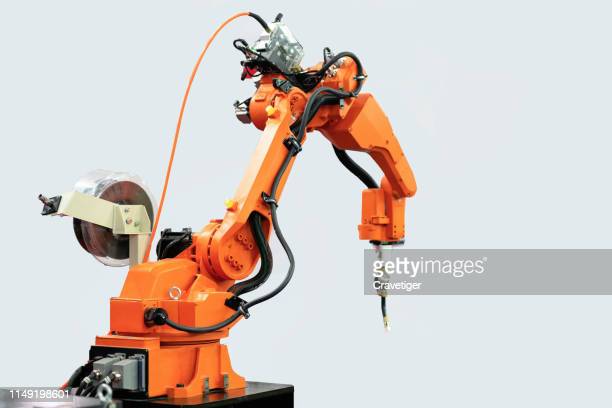
Finally, Toyota created a "driving school" to help citizens obtain drivers' licenses. Toyota also developed a special line of cars for the U.S. market. These initiatives helped the company attract more customers to its dealerships.
Toyota's success is dependent upon its ability to innovate and create value. It is also dependent upon its ability build relationships with suppliers.
FAQ
What does manufacturing industry mean?
Manufacturing Industries is a group of businesses that produce goods for sale. These products are sold to consumers. To accomplish this goal, these companies employ a range of processes including distribution, sales, management, and production. They create goods from raw materials, using machines and various other equipment. This includes all types of manufactured goods, including food items, clothing, building supplies, furniture, toys, electronics, tools, machinery, vehicles, pharmaceuticals, medical devices, chemicals, and many others.
How can manufacturing efficiency improved?
The first step is to identify the most important factors affecting production time. Next, we must find ways to improve those factors. If you don't know where to start, then think about which factor(s) have the biggest impact on production time. Once you have identified the factors, then try to find solutions.
How can manufacturing avoid production bottlenecks
The key to avoiding bottlenecks in production is to keep all processes running smoothly throughout the entire production cycle, from the time you receive an order until the time when the product ships.
This includes both planning for capacity and quality control.
This can be done by using continuous improvement techniques, such as Six Sigma.
Six Sigma is a management system used to improve quality and reduce waste in every aspect of your organization.
It emphasizes consistency and eliminating variance in your work.
Statistics
- You can multiply the result by 100 to get the total percent of monthly overhead. (investopedia.com)
- It's estimated that 10.8% of the U.S. GDP in 2020 was contributed to manufacturing. (investopedia.com)
- In 2021, an estimated 12.1 million Americans work in the manufacturing sector.6 (investopedia.com)
- In the United States, for example, manufacturing makes up 15% of the economic output. (twi-global.com)
- (2:04) MTO is a production technique wherein products are customized according to customer specifications, and production only starts after an order is received. (oracle.com)
External Links
How To
How to Use the 5S to Increase Productivity In Manufacturing
5S stands for "Sort", "Set In Order", "Standardize", "Separate" and "Store". Toyota Motor Corporation was the first to develop the 5S approach in 1954. This methodology helps companies improve their work environment to increase efficiency.
The basic idea behind this method is to standardize production processes, so they become repeatable, measurable, and predictable. This means that tasks such as cleaning, sorting, storing, packing, and labeling are performed daily. These actions allow workers to perform their job more efficiently, knowing what to expect.
Five steps are required to implement 5S: Sort, Set In Order, Standardize. Separate. Each step requires a different action to increase efficiency. You can make it easy for people to find things later by sorting them. When items are ordered, they are put together. Then, after you separate your inventory into groups, you store those groups in containers that are easy to access. Finally, when you label your containers, you ensure everything is labeled correctly.
Employees must be able to critically examine their work practices. Employees should understand why they do the tasks they do, and then decide if there are better ways to accomplish them. They will need to develop new skills and techniques in order for the 5S system to be implemented.
In addition to improving efficiency, the 5S system also increases morale and teamwork among employees. As they begin to see improvements, they feel motivated to continue working towards the goal of achieving higher levels of efficiency.