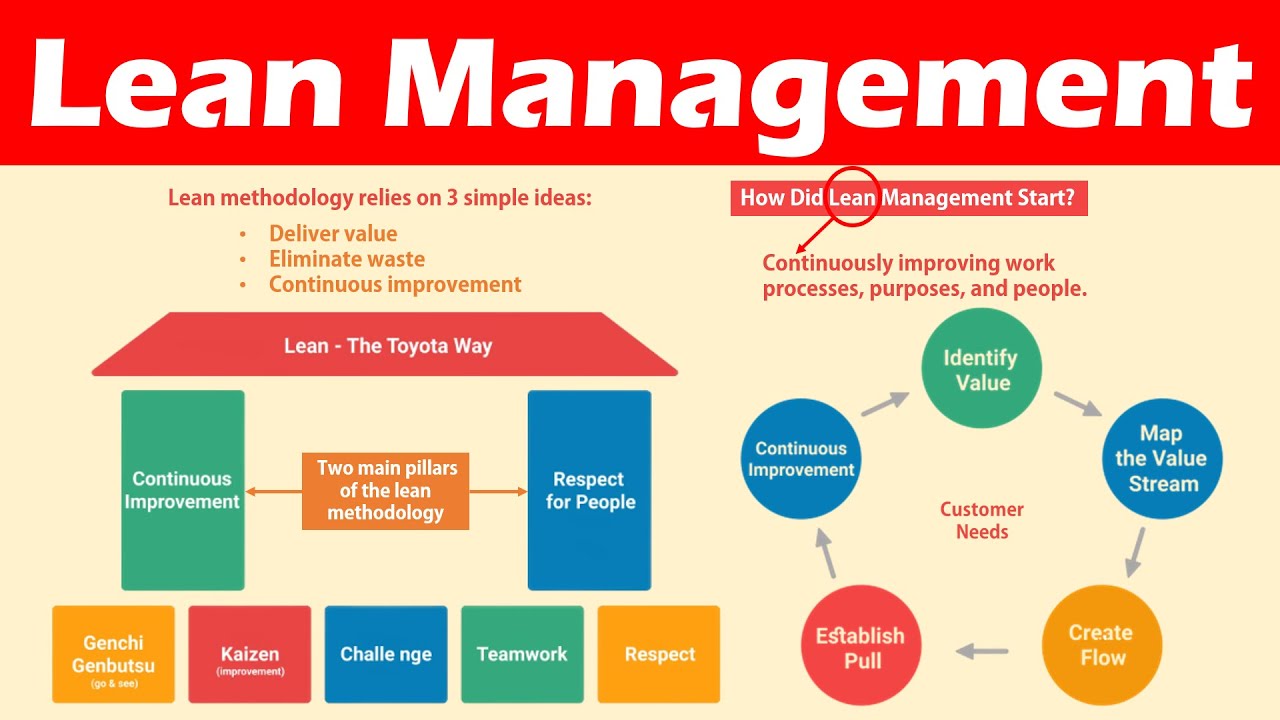
Generally, a blue collar job is a manual labor job. These jobs could be in manufacturing, agriculture, healthcare, hospitality or construction. While some jobs may require some level of skill (e.g., plumbers or electricians), others may not. Blue collar jobs often pay decent wages and offer excellent career growth.
The Fourth Industrial Revolution will transform the labor market for manual workers. This revolution encompasses artificial intelligence, robotics and machine learning. It will require a new, more skilled workforce for companies to succeed. This will require companies to move away from transactional relationships and towards more long-lasting ones.
As a result, companies are forced to hire workers from outside of the United States. These workers might be hired to make per-item payment in some cases. Other workers may be paid directly by the project. In any event, it is encouraging to see a rise in demand for blue-collar jobs.
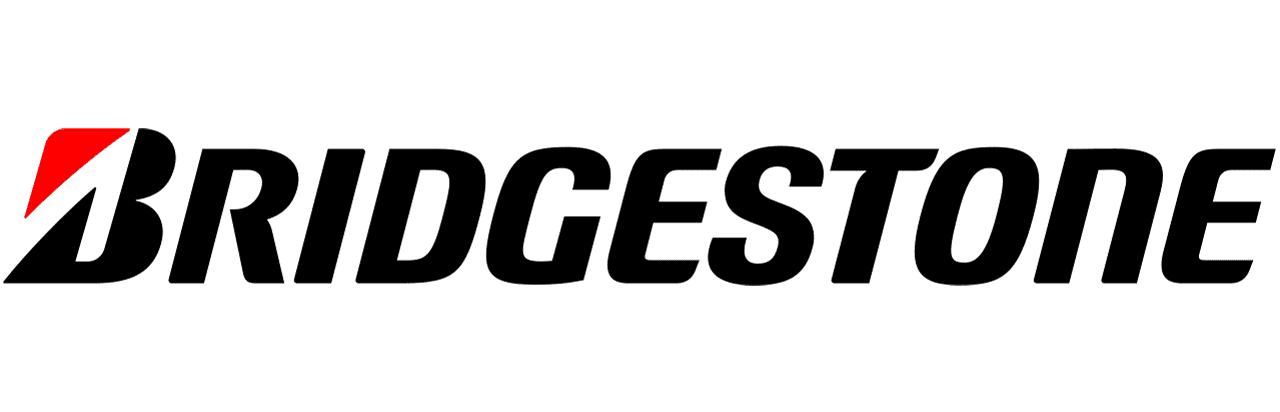
These jobs are more physically demanding than white collar jobs, but they tend to be well-paid. These jobs provide a steady income source and companies are prepared to invest in training employees. Some examples of these jobs are signal and track switching repairers, nuclear power reactor operators, and electrical and electronics repairers. Some jobs only require a high school diploma while others require training on the job.
Also, blue collar jobs are more common than white collar jobs. Blue collar workers actually make up a large part of India's workforce. In India, 210 million work in the agriculture industry, while 290 million work in the non-agricultural industry. The demand for blue-collar workers is increasing at an alarming rate.
Companies are also being transformed by the Fourth Industrial Revolution in how they manage their blue-collar workers. Along with replacing manual jobs in the workplace with digital ones companies are shifting away from transactional relationships toward enduring ones. Companies can improve their productivity and build stronger relationships by prioritizing employees' needs.
The demand for blue collar workers is also high, but they are faced with competing realities. They might worry about the stability of work or their retirement. Blue collar workers, despite these worries, tend to be optimistic about the future. In fact, the percentage of blue-collar workers saving for retirement is growing. Blue collar jobs will continue to grow in popularity as the economy recovers.
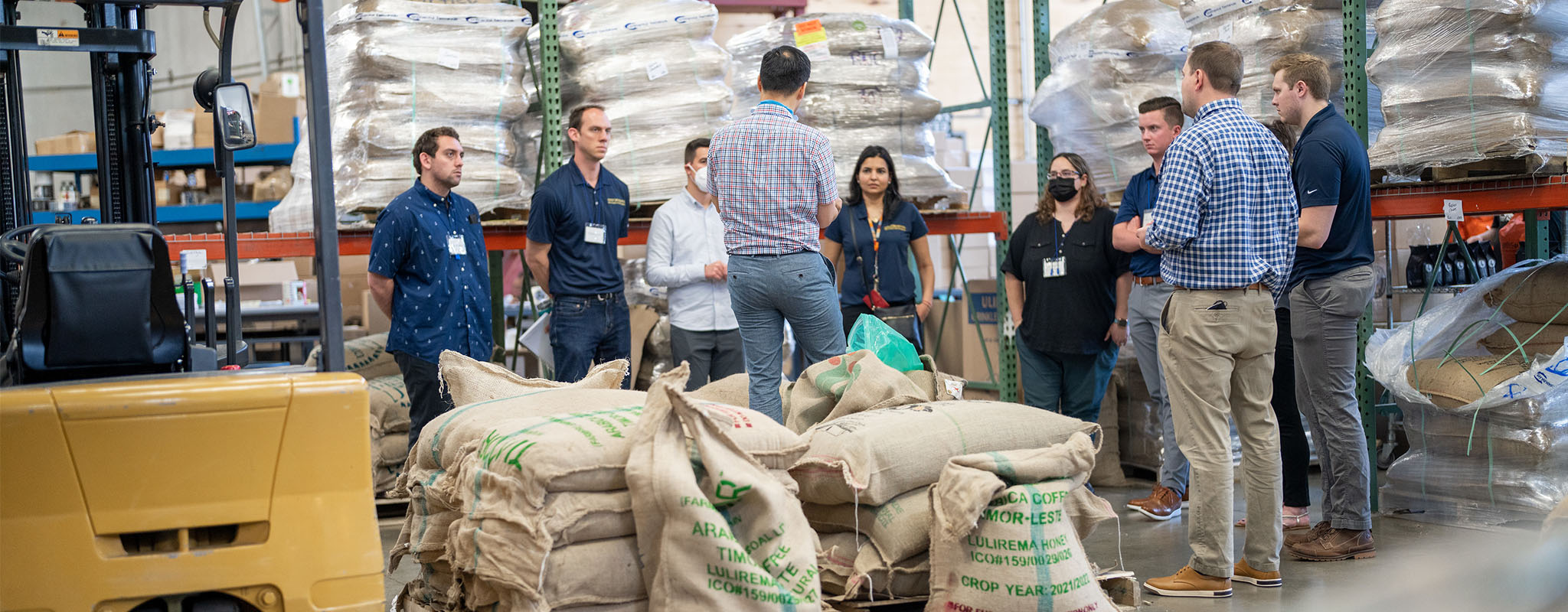
Automation is not threatening these jobs. The Association for Manufacturing Technology has found that for every job that is replaced by technology there are five new jobs. Signal and track switch technicians earned $76,210 per year, the average salary.
In addition to being more lucrative, blue collar positions are also becoming more popular. The earnings of many blue collar jobs are well above the national average, making it an ideal option for those looking for a job with good pay. In addition, many blue collar jobs require a high degree of problem-solving skills, and are more than likely to provide good career growth.
FAQ
How can overproduction in manufacturing be reduced?
In order to reduce excess production, you need to develop better inventory management methods. This would reduce the amount of time spent on unnecessary activities such as purchasing, storing, and maintaining excess stock. This would allow us to use our resources for more productive tasks.
You can do this by adopting a Kanban method. A Kanban Board is a visual display that tracks work progress. Kanban systems are where work items travel through a series of states until reaching their final destination. Each state has a different priority level.
To illustrate, work can move from one stage or another when it is complete enough for it to be moved to a new stage. However, if a task is still at the beginning stages, it will remain so until it reaches the end of the process.
This allows work to move forward and ensures that no work is missed. A Kanban board allows managers to monitor how much work is being completed at any given moment. This data allows them adjust their workflow based upon real-time data.
Lean manufacturing is another option to control inventory levels. Lean manufacturing seeks to eliminate waste from every step of the production cycle. Anything that doesn't add value to the product is considered waste. There are several types of waste that you might encounter:
-
Overproduction
-
Inventory
-
Unnecessary packaging
-
Excess materials
Manufacturers can increase efficiency and decrease costs by implementing these ideas.
What is the difference between a production planner and a project manager?
The primary difference between a producer planner and a manager of a project is that the manager usually plans and organizes the whole project, while a production planner is only involved in the planning stage.
How can we increase manufacturing efficiency?
First, identify the factors that affect production time. We must then find ways that we can improve these factors. If you don’t know where to begin, consider which factors have the largest impact on production times. Once you have identified the factors, then try to find solutions.
What is the responsibility of a manufacturing manager?
A manufacturing manager has to ensure that all manufacturing processes work efficiently and effectively. They should also be aware and responsive to any company problems.
They should also be able and comfortable communicating with other departments like sales and marketing.
They should also be aware of the latest trends in their industry and be able to use this information to help improve productivity and efficiency.
What are the differences between these four types?
Manufacturing is the process that transforms raw materials into useful products. Manufacturing can include many activities such as designing and building, testing, packaging shipping, selling, servicing, and other related activities.
What is the importance of logistics in manufacturing?
Logistics is an integral part of every business. They are essential to any business's success.
Logistics are also important in reducing costs and improving efficiency.
What does warehouse refer to?
A warehouse is an area where goods are stored before being sold. It can be either an indoor or outdoor space. In some cases, it may be a combination of both.
Statistics
- According to the United Nations Industrial Development Organization (UNIDO), China is the top manufacturer worldwide by 2019 output, producing 28.7% of the total global manufacturing output, followed by the United States, Japan, Germany, and India.[52][53] (en.wikipedia.org)
- Job #1 is delivering the ordered product according to specifications: color, size, brand, and quantity. (netsuite.com)
- You can multiply the result by 100 to get the total percent of monthly overhead. (investopedia.com)
- [54][55] These are the top 50 countries by the total value of manufacturing output in US dollars for its noted year according to World Bank.[56] (en.wikipedia.org)
- According to a Statista study, U.S. businesses spent $1.63 trillion on logistics in 2019, moving goods from origin to end user through various supply chain network segments. (netsuite.com)
External Links
How To
Six Sigma and Manufacturing
Six Sigma is "the application statistical process control (SPC), techniques for continuous improvement." Motorola's Quality Improvement Department created Six Sigma at their Tokyo plant, Japan in 1986. Six Sigma's core idea is to improve the quality of processes by standardizing and eliminating defects. Since there are no perfect products, or services, this approach has been adopted by many companies over the years. Six Sigma's primary goal is to reduce variation from the average value of production. This means that if you take a sample of your product, then measure its performance against the average, you can find out what percentage of the time the process deviates from the norm. If there is a significant deviation from the norm, you will know that something needs to change.
Understanding the dynamics of variability within your business is the first step in Six Sigma. Once you have a good understanding of the basics, you can identify potential sources of variation. These variations can also be classified as random or systematic. Random variations are caused by human errors. Systematic variations can be caused by outside factors. If you make widgets and some of them end up on the assembly line, then those are considered random variations. However, if you notice that every time you assemble a widget, it always falls apart at exactly the same place, then that would be a systematic problem.
Once you've identified the problem areas you need to find solutions. You might need to change the way you work or completely redesign the process. You should then test the changes again after they have been implemented. If they don't work you need to rework them and come up a better plan.