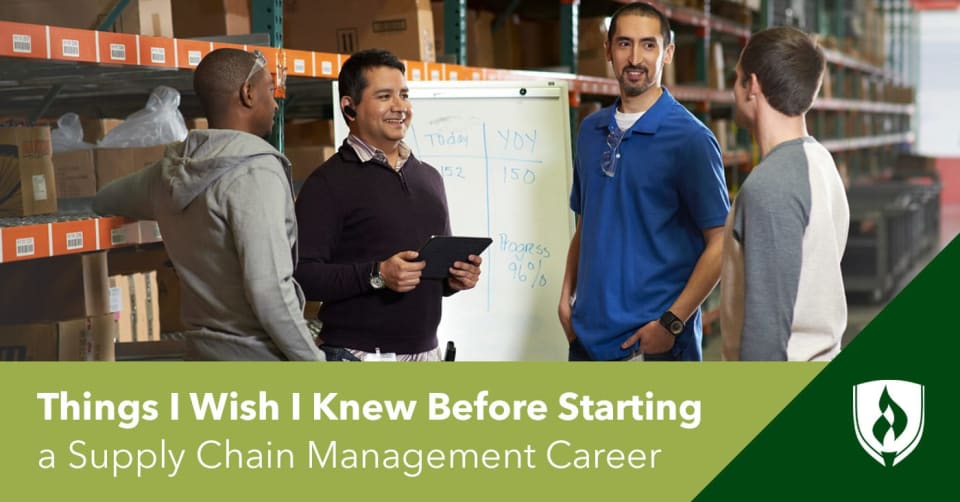
A blue collar job, in general, is one that requires manual labor. These jobs might be in the fields of agriculture, manufacturing, healthcare or hospitality. Some require some level or skill, such a plumber, electrician, etc. While others are less skilled. Blue collar jobs pay good salaries and provide great career growth.
The Fourth Industrial Revolution will transform the labor market for manual workers. This revolution encompasses artificial intelligence, robotics and machine learning. Companies will need a more skilled workforce to be successful. This will require companies to move away from transactional relationships and towards more long-lasting ones.
Companies are often forced to hire workers from abroad. These workers may be hired in exchange for per-item wages. Others might be paid by the project. It is encouraging to see the demand for blue collar work rising.
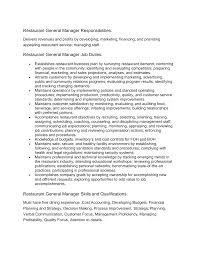
These jobs are more physically demanding than white collar jobs, but they tend to be well-paid. Because these jobs are a good source of income, companies are willing to invest in training their employees. These jobs include signal and track switch operators, electrical and electronic repairers and nuclear power reactor operator. These jobs do not require a highschool diploma. However, some require on-thejob training.
There are also more blue collar jobs than there are white collar ones. In fact, blue collar workers make up a substantial part of the Indian workforce. India's agricultural industry employs 210 million people, while the non-agricultural industries employ 290 million. The demand for blue-collar workers is increasing at an alarming rate.
Companies' management of their blue-collar workforce is changing as well with the Fourth Industrial Revolution. Firms are not only replacing manual jobs with digital jobs, but they also shift away from transactional relationships towards lasting ones. Firms can create stronger relationships and better productivity by prioritizing their employees.
Blue collar workers are also in demand, but they face competing realities. They might be concerned about their jobs' stability, or about retirement. Regardless of these concerns, blue collar workers tend to be optimistic about their futures. Blue-collar workers are actually saving more for retirement. Blue collar jobs will continue to grow in popularity as the economy recovers.
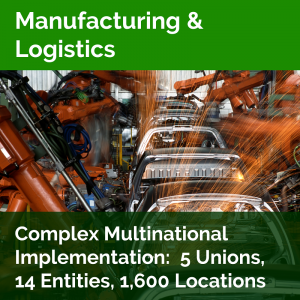
These jobs are also not threatened by automation. The Association for Manufacturing Technology has found that for every job that is replaced by technology there are five new jobs. Signal and track switching repairers saw the biggest increase in their average annual salary of $76,210.
Additionally, blue collar jobs have a rising number of better-paying positions. Many blue collar jobs earn much more than the national average. This makes them an attractive option for anyone looking for a high-paying job. A lot of blue collar jobs require high levels of problem-solving skills. This will increase your career prospects.
FAQ
How can I learn about manufacturing?
The best way to learn about manufacturing is through hands-on experience. But if that is not possible you can always read books and watch educational videos.
How does manufacturing avoid bottlenecks in production?
Production bottlenecks can be avoided by ensuring that processes are running smoothly during the entire production process, starting with the receipt of an order and ending when the product ships.
This includes planning for capacity requirements as well as quality control measures.
The best way to do this is to use continuous improvement techniques such as Six Sigma.
Six Sigma management is a system that improves quality and reduces waste within your organization.
It is focused on creating consistency and eliminating variation in your work.
Do we need to know about Manufacturing Processes before learning about Logistics?
No. It doesn't matter if you don't know anything about manufacturing before you learn about logistics. Knowing about manufacturing processes will help you understand how logistics works.
Statistics
- It's estimated that 10.8% of the U.S. GDP in 2020 was contributed to manufacturing. (investopedia.com)
- According to a Statista study, U.S. businesses spent $1.63 trillion on logistics in 2019, moving goods from origin to end user through various supply chain network segments. (netsuite.com)
- According to the United Nations Industrial Development Organization (UNIDO), China is the top manufacturer worldwide by 2019 output, producing 28.7% of the total global manufacturing output, followed by the United States, Japan, Germany, and India.[52][53] (en.wikipedia.org)
- Job #1 is delivering the ordered product according to specifications: color, size, brand, and quantity. (netsuite.com)
- In 2021, an estimated 12.1 million Americans work in the manufacturing sector.6 (investopedia.com)
External Links
How To
How to use 5S in Manufacturing to Increase Productivity
5S stands in for "Sort", the "Set In Order", "Standardize", or "Separate". Toyota Motor Corporation developed the 5S method in 1954. It assists companies in improving their work environments and achieving higher efficiency.
This method aims to standardize production processes so that they are repeatable, measurable and predictable. Cleaning, sorting and packing are all done daily. Workers can be more productive by knowing what to expect.
Implementing 5S involves five steps: Sort, Set in Order, Standardize Separate, Store, and Each step involves a different action which leads to increased efficiency. If you sort items, it makes them easier to find later. You arrange items by placing them in an order. You then organize your inventory in groups. You can also label your containers to ensure everything is properly labeled.
Employees will need to be more critical about their work. Employees need to understand the reasons they do certain jobs and determine if there is a better way. In order to use the 5S system effectively, they must be able to learn new skills.
The 5S method increases efficiency and morale among employees. Once they start to notice improvements, they are motivated to keep working towards their goal of increasing efficiency.