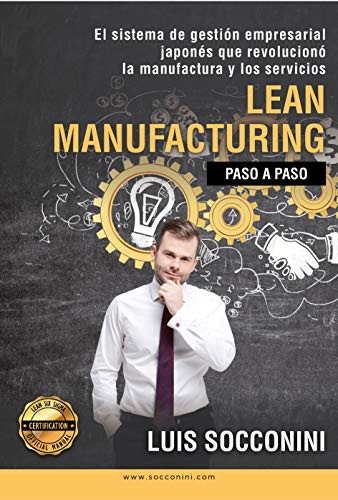
Lean manufacturing is a great way to reduce costs, improve lead times and minimize set-up and turnaround times. The benefits of lean manufacturing can be seen immediately. They cut down on lead time and cost while improving customer experience. These improvements make Lean Manufacturing the best way for your business to grow. If you're still skeptical, let's take a look at three reasons that lean manufacturing is the best method to make products and lower costs.
Lowers costs
Lean manufacturing can bring significant savings. Through reducing defects, rework and direct labor costs, manufacturers can make savings. In this way, labor costs are less motivating for decision-making. Hazardous waste can also be eliminated. In many industries, the cost of direct labor is below 15%, making it harder to justify outsourcing manufacturing to low-cost locations. This can help lower manufacturing costs, and provide better customer service.
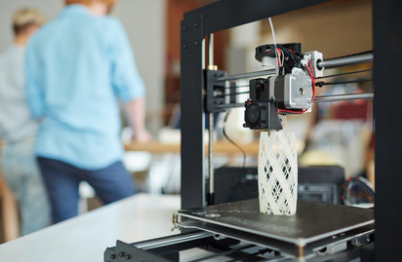
This improves lead times
There are many benefits to using lean manufacturing. These include the ability to reduce waste, improve lead times and lower costs. It is a philosophy that promotes continuous improvement, or "kaizen". It combines the talents of employees and encourages collaboration and accountability. It can increase lead times up to 20% Lean manufacturing allows you to make small changes often to improve product quality and efficiency.
Shortens set-up times
It is possible to reduce the time taken to create a product by reducing setup times. The time it takes for a product to be switched from its last item to the new one is called setup time. The setup time includes preparation, replacement, as well as location activities. These activities can either be internal, or external. While some activities such as the moving of a machine or placing an item requires an inactive process to be completed, others can be carried out while the process continues to operate.
Reduces time it takes to get to market
Lean manufacturing, also known as continuous improvement, was first developed in Japan in the period of rebuilding after World War II. It sought to improve competitiveness and reduce lead times. Companies can be more responsive to customers and increase profits by reducing the time it takes a product reach the market. This method of production not only increases efficiency but also makes the facility more productive.
Improves product quality
Lean manufacturing's success depends on the ability to reduce waste, improve product quality, and minimize costs. It has been used by many companies, large and small. It can lower lead times, costs, labor, and other expenses. Learn more about how lean production can help improve your business. Here are some areas that you need to be focused on. Lean principles are a way to reduce lead times and improve product quality while lowering costs.
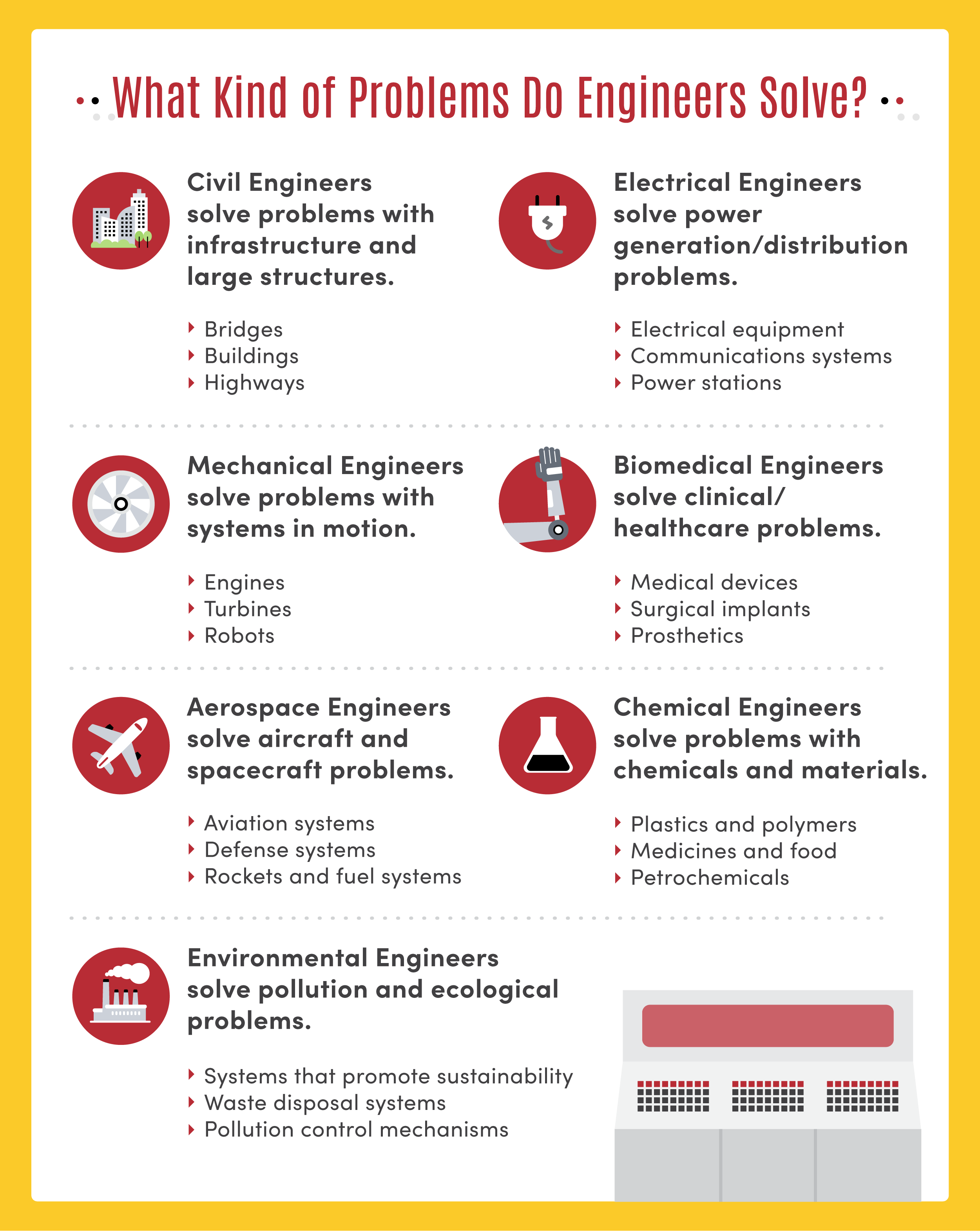
Direct labor costs can be reduced
In lean manufacturing, the low hanging fruit is reducing indirect labor costs. True lean companies are not concerned with direct labor efficiency but rather look at ways to cut indirect labor cost. This means eliminating material handling and inspection jobs. This is the same method used by Toyota and other lean manufacturing firms. In this article, we'll examine how lean production can lower indirect labor expenses.
FAQ
What is the difference between a production planner and a project manager?
The main difference between a production planner and a project manager is that a project manager is usually the person who plans and organizes the entire project, whereas a production planner is mainly involved in the planning stage of the project.
What are my options for learning more about manufacturing
Hands-on experience is the best way to learn more about manufacturing. If that is not possible, you could always read books or view educational videos.
What are the goods of logistics?
Logistics is the process of moving goods from one point to another.
They cover all aspects of transportation, such as packing, loading, transporting and unloading.
Logisticians ensure the product reaches its destination in the most efficient manner. They help companies manage their supply chain efficiency by providing information on demand forecasts, stock levels, production schedules, and availability of raw materials.
They also keep track of shipments in transit, monitor quality standards, perform inventories and order replenishment, coordinate with suppliers and vendors, and provide support services for sales and marketing.
Statistics
- It's estimated that 10.8% of the U.S. GDP in 2020 was contributed to manufacturing. (investopedia.com)
- According to a Statista study, U.S. businesses spent $1.63 trillion on logistics in 2019, moving goods from origin to end user through various supply chain network segments. (netsuite.com)
- (2:04) MTO is a production technique wherein products are customized according to customer specifications, and production only starts after an order is received. (oracle.com)
- According to the United Nations Industrial Development Organization (UNIDO), China is the top manufacturer worldwide by 2019 output, producing 28.7% of the total global manufacturing output, followed by the United States, Japan, Germany, and India.[52][53] (en.wikipedia.org)
- In 2021, an estimated 12.1 million Americans work in the manufacturing sector.6 (investopedia.com)
External Links
How To
How to Use lean manufacturing in the Production of Goods
Lean manufacturing refers to a method of managing that seeks to improve efficiency and decrease waste. It was developed in Japan between 1970 and 1980 by Taiichi Ohno. TPS founder Kanji Tyoda gave him the Toyota Production System, or TPS award. Michael L. Watkins published the "The Machine That Changed the World", the first book about lean manufacturing. It was published in 1990.
Lean manufacturing is often described as a set if principles that help improve the quality and speed of products and services. It emphasizes the elimination and minimization of waste in the value stream. Just-in-time (JIT), zero defect (TPM), and 5S are all examples of lean manufacturing. Lean manufacturing is about eliminating activities that do not add value, such as inspection, rework, and waiting.
Lean manufacturing not only improves product quality but also reduces costs. Companies can also achieve their goals faster by reducing employee turnover. Lean Manufacturing is one of the most efficient ways to manage the entire value chains, including suppliers and customers as well distributors and retailers. Lean manufacturing is widely practiced in many industries around the world. Toyota's philosophy, for example, is what has enabled it to be successful in electronics, automobiles, medical devices, healthcare and chemical engineering as well as paper and food.
Lean manufacturing is based on five principles:
-
Define Value: Identify the social value of your business and what sets you apart.
-
Reduce Waste - Eliminate any activity that doesn't add value along the supply chain.
-
Create Flow – Ensure that work flows smoothly throughout the process.
-
Standardize & Simplify - Make processes as consistent and repeatable as possible.
-
Develop Relationships: Establish personal relationships both with internal and external stakeholders.
Although lean manufacturing has always been around, it is gaining popularity in recent years because of a renewed interest for the economy after 2008's global financial crisis. To increase their competitiveness, many businesses have turned to lean manufacturing. According to some economists, lean manufacturing could be a significant factor in the economic recovery.
Lean manufacturing has many benefits in the automotive sector. These benefits include increased customer satisfaction, reduced inventory levels and lower operating costs.
Any aspect of an enterprise can benefit from Lean manufacturing. Lean manufacturing is most useful in the production sector of an organisation because it ensures that each step in the value-chain is efficient and productive.
There are three main types of lean manufacturing:
-
Just-in Time Manufacturing (JIT), also known as "pull system": This form of lean manufacturing is often referred to simply as "pull". JIT is a process in which components can be assembled at the point they are needed, instead of being made ahead of time. This approach reduces lead time, increases availability and reduces inventory.
-
Zero Defects Manufacturing (ZDM),: ZDM is a system that ensures no defective units are left the manufacturing facility. It is better to repair a part than have it removed from the production line if it needs to be fixed. This applies to finished products, which may need minor repairs before they are shipped.
-
Continuous Improvement: Continuous Improvement aims to improve efficiency by continually identifying problems and making adjustments to eliminate or minimize waste. It involves continuous improvement of processes, people, and tools.