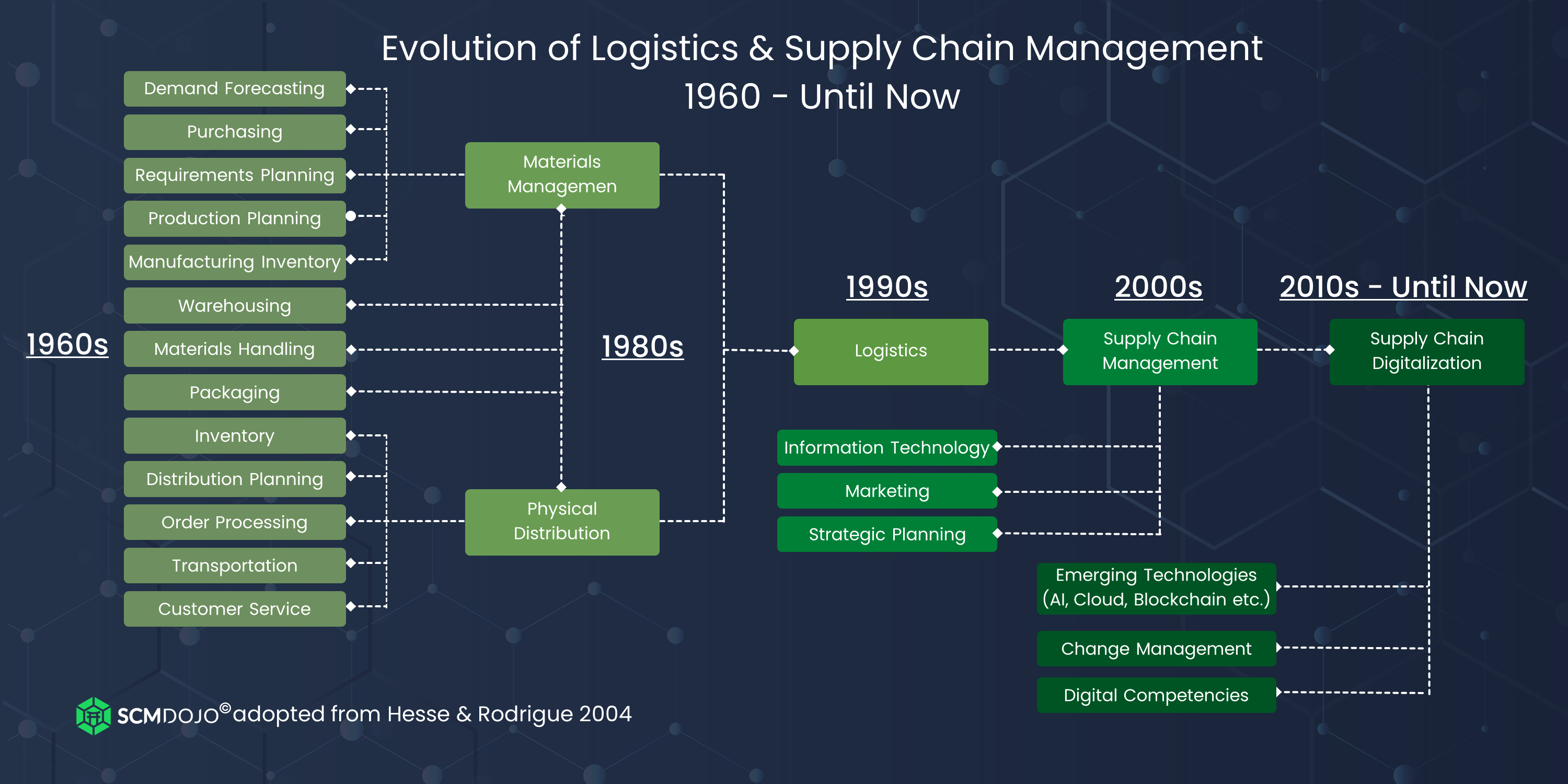
Six-Sigma, lean and Lean are complementary methods of improving processes. Both tools can be used to solve problems but each approach has its own strengths. Six-Sigma, a statistical process control technique that uses statistical processes, is used in Lean. It starts with the idea that a product must have value and not just be produced. The key to Lean is to eliminate waste and improve the quality of the product as it is being produced.
Problem solving for PDCA
Although there are some differences between DMAIC problem-solving and PDCA (problem solving), both are based upon the DMAIC approach. The PDCA cycle requires more planning and analysis. PDCA is not as effective as DMAIC for urgent problems. This approach requires a problem-solving leader with technical skills. Six Sigma practitioners are "green belts" certified.
In Six Sigma, problem-solving follows a cycle that was first introduced in the 1950s by W. Edwards Deming. Its creators intended to use it in conjunction with continuous improvement methods to help rebuild Japan's industries. At the P (Plan), real data must first be gathered. A clear mission statement must then be developed. After the PDCA phase, the team must agree on a solution.
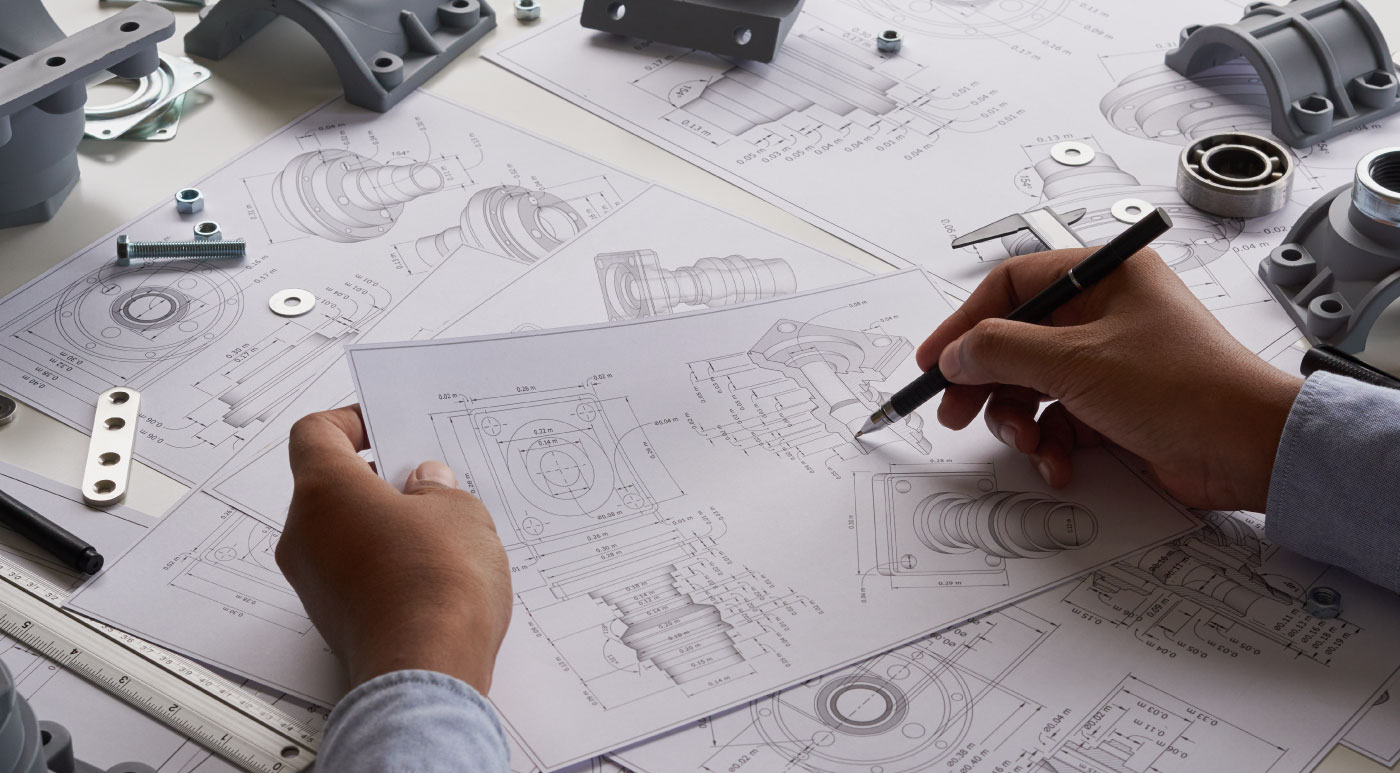
Process maps
One key difference between Six Sigma processes maps and Lean is the way each describes them. Both methods focus on defining the process in detail but each approach focuses more on different aspects. Lean is a method of mapping actual processes, not standard operating protocols. When creating process maps, consider major activities, decisions, and sources of approval. Include areas where you use multiple methods and factors that may obstruct members. Match roles carefully and examine the flow of the process.
To show the flow of a process, a process map should contain steps, symbols and arrows. Every process should be reviewed several times to verify that it accurately represents the actual process. The date the process map was created should be included, along with contact information for anyone who has questions. Overall, process maps can improve a process. However, they could be too complicated.
Analysis of cause & effect
Six Sigma and lean project management techniques involve statistical analysis and stochastic optimization. The Cause and Effect Matrix (CAE) relates the steps of a process to their inputs and outputs. Customer requirements are listed in order of importance to the customer and inputs and outputs are ranked according to the impact on the outcome. The ranking and key input variables should be established.
Each technique offers a different set of benefits. Lean Six Sigma uses a process management methodology that is based around Frederick Winslow Taylor’s Principles of Scientific Management. Taylor envisioned business processes as interlocking processes and workflows. Taylor advocated reducing variation and also minimizing waste. Six-Sigma is a complement to lean in reducing waste.
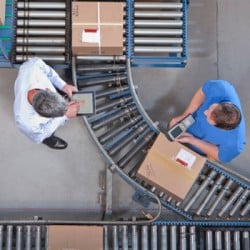
Eliminating variation
Variability is part of every manufacturing process. Uncertainty in the end result can be caused by this variability. It is important to maintain consistency in order to deliver professional results. Elimination of variation in Six Sigma and Lean manufacturing methods aims to achieve predictable output. Variation is OK. However, too much variation can lead the to repairs, rework, as well as possible out-of-business consequences. The best way to manage variation is to identify the root cause.
The decision points are the best place to search for variations. Process maps identify decision points, which are represented by diamonds. Six Sigma teams have the ability to identify decision points and start eliminating variation. This information can be obtained from the Six Sigma team or the process owner. The Six Sigma group cannot focus on a process that is not governed by a standard process if it's owner. A process map might not work if the Six Sigma team lacks the technical capability to make necessary adjustments.
FAQ
How can we reduce manufacturing overproduction?
Better inventory management is key to reducing excess production. This would reduce the time spent on unproductive activities like purchasing, storing and maintaining excess stock. We could use these resources to do other productive tasks.
Kanban systems are one way to achieve this. A Kanban board, a visual display to show the progress of work, is called a Kanban board. A Kanban system allows work items to move through several states before reaching their final destination. Each state represents an individual priority level.
If work is moving from one stage to the other, then the current task can be completed and moved on to the next. However, if a task is still at the beginning stages, it will remain so until it reaches the end of the process.
This helps to keep work moving forward while ensuring that no work is left behind. Managers can see how much work has been done and the status of each task at any time with a Kanban Board. This allows them to adjust their workflows based on real-time information.
Lean manufacturing is another way to manage inventory levels. Lean manufacturing emphasizes eliminating waste in all phases of production. Waste includes anything that does not add value to the product. Here are some examples of common types.
-
Overproduction
-
Inventory
-
Packaging not required
-
Exceed materials
These ideas will help manufacturers increase efficiency and lower costs.
What are the responsibilities of a manufacturing manager
The manufacturing manager should ensure that every manufacturing process is efficient and effective. They should be aware of any issues within the company and respond accordingly.
They should also be able and comfortable communicating with other departments like sales and marketing.
They should also be knowledgeable about the latest trends in the industry so they can use this information for productivity and efficiency improvements.
What are the four types of manufacturing?
Manufacturing is the process by which raw materials are transformed into useful products through machines and processes. It involves many different activities such as designing, building, testing, packaging, shipping, selling, servicing, etc.
What is production planning?
Production Planning involves developing a plan for all aspects of the production, including scheduling, budgeting, casting, crew, location, equipment, props, etc. It is important to have everything ready and planned before you start shooting. This document should also include information on how to get the best result on set. This includes shooting schedules, locations, cast lists, crew details, and equipment requirements.
It is important to first outline the type of film you would like to make. You may have already decided where you would like to shoot, or maybe there are specific locations or sets that you want to use. Once you have determined your scenes and locations, it is time to start figuring out the elements that you will need for each scene. For example, you might decide that you need a car but don't know exactly what model you want. You could look online for cars to see what options are available, and then narrow down your choices by selecting between different makes or models.
After you've found the perfect car, it's time to start thinking about adding extras. Do you need people sitting in the front seats? You might also need someone to help you get around the back. Perhaps you would like to change the interior colour from black to white. These questions will help you determine the exact look and feel of your car. The type of shots that you are looking for is another thing to consider. Will you be filming close-ups or wide angles? Perhaps you want to show the engine or the steering wheel? These factors will help you determine which car style you want to film.
Once you have all the information, you are ready to create a plan. You will know when you should start and when you should finish shooting. Every day will have a time for you to arrive at the location, leave when you are leaving and return home when you are done. So everyone is clear about what they need to do. Hire extra staff by booking them ahead of time. It's not worth paying someone to show up if you haven't told him.
It is important to calculate the amount of filming days when you are creating your schedule. Some projects only take one or two days, while others may last weeks. While creating your schedule, it is important to remember whether you will require more than one shot per day. Multiple takes at the same place will result in higher costs and longer completion times. It's better to be safe than sorry and shoot less takes if you're not certain whether you need more takes.
Budgeting is another important aspect of production planning. It is important to set a realistic budget so you can work within your budget. It is possible to reduce the budget at any time if you experience unexpected problems. It is important to not overestimate how much you will spend. Underestimating the cost will result in less money after you have paid for other items.
Production planning is a very detailed process, but once you understand how everything works together, it becomes easier to plan future projects.
What are the main products of logistics?
Logistics is the process of moving goods from one point to another.
They include all aspects of transport, including packaging, loading, transporting, unloading, storing, warehousing, inventory management, customer service, distribution, returns, and recycling.
Logisticians ensure that the product is delivered to the correct place, at the right time, and under safe conditions. Logisticians help companies improve their supply chain efficiency by providing information about demand forecasts and stock levels, production schedules, as well as availability of raw materials.
They can also track shipments in transit and monitor quality standards.
What are my options for learning more about manufacturing
Experience is the best way for you to learn about manufacturing. If that is not possible, you could always read books or view educational videos.
Statistics
- Job #1 is delivering the ordered product according to specifications: color, size, brand, and quantity. (netsuite.com)
- According to the United Nations Industrial Development Organization (UNIDO), China is the top manufacturer worldwide by 2019 output, producing 28.7% of the total global manufacturing output, followed by the United States, Japan, Germany, and India.[52][53] (en.wikipedia.org)
- [54][55] These are the top 50 countries by the total value of manufacturing output in US dollars for its noted year according to World Bank.[56] (en.wikipedia.org)
- Many factories witnessed a 30% increase in output due to the shift to electric motors. (en.wikipedia.org)
- It's estimated that 10.8% of the U.S. GDP in 2020 was contributed to manufacturing. (investopedia.com)
External Links
How To
How to use 5S in Manufacturing to Increase Productivity
5S stands for "Sort", 'Set In Order", 'Standardize', & Separate>. Toyota Motor Corporation created the 5S methodology in 1954. It improves the work environment and helps companies to achieve greater efficiency.
The idea behind standardizing production processes is to make them repeatable and measurable. It means tasks like cleaning, sorting or packing, labeling, and storing are done every day. These actions allow workers to perform their job more efficiently, knowing what to expect.
Five steps are required to implement 5S: Sort, Set In Order, Standardize. Separate. Each step requires a different action, which increases efficiency. You can make it easy for people to find things later by sorting them. When items are ordered, they are put together. After you have divided your inventory into groups you can store them in easy-to-reach containers. You can also label your containers to ensure everything is properly labeled.
Employees must be able to critically examine their work practices. Employees need to understand the reasons they do certain jobs and determine if there is a better way. They must learn new skills and techniques in order to implement the 5S system.
In addition to increasing efficiency, the 5S method also improves morale and teamwork among employees. As they begin to see improvements, they feel motivated to continue working towards the goal of achieving higher levels of efficiency.