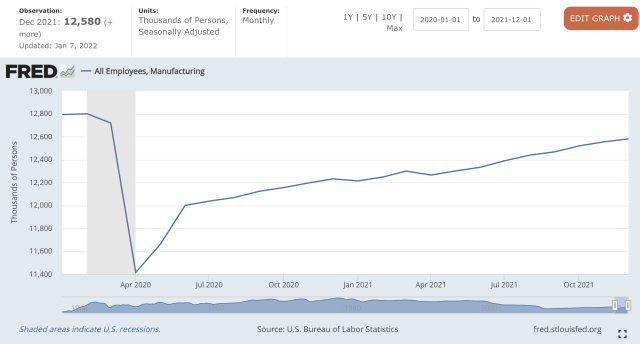
The creation of a "Smart Factory", however, is not just about installing new technology. It's more than just installing new technology. It's about changing the factory's mindset to adapt to new demands. With the right technology, you can help your customers, and help your business succeed in a new phase of manufacturing.
The first step is to determine what you want. Perhaps you want to build an intelligent factory that responds to drastic swings in demand. You may also want to create a smart factory that helps your global supply chain partners. Perhaps you want to create a factory that can respond to an industry that heavily relies on manual labor. The next step is to create an ecosystem that supports your goal, no matter what it may be.
One key obstacle to a smart factory is a lack of connectivity. This can be difficult to overcome when you have old machinery and equipment. You might also have difficulty accessing the correct information regarding your systems and machines. A study revealed that 33% said that the lack of IT infrastructure was a major impediment for a smart factory.
Technology is the second most important factor. There are many advanced manufacturing technology options available. These technologies can be used to improve your quality and productivity. These technologies can also be used to increase the value of your plant.
Another aspect to be considered is the people. You need to make investments in the right skill sets at the right times. You will need the right people as well as a talent strategy. You should ensure that there is a clear scope to work and that all parties agree on the priorities and timelines. It is important to ensure that the right people work on the right projects.
The process is the third most important thing to think about. You must ensure that your applications are able connect to a networking. This will help you to share information with other systems and processes in your factory. Lastly, you need to make sure that you have data and analytics in place. This will allow you to make data-driven decisions and to self-heal.
The fourth most important factor to consider is people. It is essential that you have a committed executive team. It can help to have a convener that can help coordinate and align efforts across multiple vendors. It is also a good idea to have a convener who can coordinate and align efforts across multiple vendors.
Security is the fifth most critical factor. There are many new technologies that can be used to decrease the likelihood of cyberattacks in manufacturing settings. You must ensure that your cybersecurity strategy is in place. Also, you need to make sure that your cybersecurity strategy is always in place.
Finally, you need to consider how you will connect your machines and equipment. Your current solutions are fine, but it might be worth exploring new options. This will allow for you to create additional data sets to support your smart manufacturing initiatives.
FAQ
What do we need to know about Manufacturing Processes in order to learn more about Logistics?
No. No. It is important to know about the manufacturing processes in order to understand how logistics works.
What are the responsibilities of a logistic manager?
Logistics managers ensure that goods arrive on time and are unharmed. This is done through his/her expertise and knowledge about the company's product range. He/she should also ensure enough stock is available to meet demand.
What does it mean to warehouse?
A warehouse is a place where goods are stored until they are sold. It can be an outdoor or indoor area. Sometimes, it can be both an indoor and outdoor space.
Why automate your warehouse?
Modern warehouses are increasingly dependent on automation. Increased demand for efficient and faster delivery has resulted in a rise in e-commerce.
Warehouses have to be flexible to meet changing requirements. Technology is essential for warehouses to be able to adapt quickly to changing needs. Automation warehouses can bring many benefits. These are some of the benefits that automation can bring to warehouses:
-
Increases throughput/productivity
-
Reduces errors
-
Improves accuracy
-
Safety enhancements
-
Eliminates bottlenecks
-
Allows companies scale more easily
-
It makes workers more efficient
-
Provides visibility into everything that happens in the warehouse
-
Enhances customer experience
-
Improves employee satisfaction
-
It reduces downtime, and increases uptime
-
Ensures quality products are delivered on time
-
Human error can be eliminated
-
It helps ensure compliance with regulations
How does a production planner differ from a project manager?
The difference between a product planner and project manager is that a planer is typically the one who organizes and plans the entire project. A production planner, however, is mostly involved in the planning stages.
Statistics
- According to a Statista study, U.S. businesses spent $1.63 trillion on logistics in 2019, moving goods from origin to end user through various supply chain network segments. (netsuite.com)
- According to the United Nations Industrial Development Organization (UNIDO), China is the top manufacturer worldwide by 2019 output, producing 28.7% of the total global manufacturing output, followed by the United States, Japan, Germany, and India.[52][53] (en.wikipedia.org)
- Job #1 is delivering the ordered product according to specifications: color, size, brand, and quantity. (netsuite.com)
- [54][55] These are the top 50 countries by the total value of manufacturing output in US dollars for its noted year according to World Bank.[56] (en.wikipedia.org)
- You can multiply the result by 100 to get the total percent of monthly overhead. (investopedia.com)
External Links
How To
Six Sigma in Manufacturing:
Six Sigma is defined as "the application of statistical process control (SPC) techniques to achieve continuous improvement." It was developed by Motorola's Quality Improvement Department at their plant in Tokyo, Japan, in 1986. Six Sigma's basic concept is to improve quality and eliminate defects through standardization. Many companies have adopted Six Sigma in recent years because they believe that there are no perfect products and services. Six Sigma's primary goal is to reduce variation from the average value of production. This means that if you take a sample of your product, then measure its performance against the average, you can find out what percentage of the time the process deviates from the norm. If there is a significant deviation from the norm, you will know that something needs to change.
Understanding the dynamics of variability within your business is the first step in Six Sigma. Once you have a good understanding of the basics, you can identify potential sources of variation. It is important to identify whether the variations are random or systemic. Random variations are caused when people make mistakes. While systematic variations are caused outside of the process, they can occur. You could consider random variations if some widgets fall off the assembly lines. You might notice that your widgets always fall apart at the same place every time you put them together.
After identifying the problem areas, you will need to devise solutions. This could mean changing your approach or redesigning the entire process. After implementing the new changes, you should test them again to see if they worked. If they don’t work, you’ll need to go back and rework the plan.