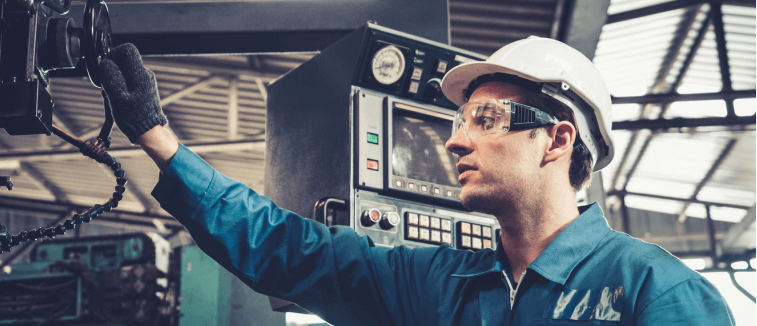
Many companies offer part-time or full-time work from home logistics jobs. They can be a great way for you to increase your earnings. Some companies are even adopting new technologies to better serve their workers. If you use the latest technology correctly, it can make your job much easier and more precise.
Work from home jobs in logistics are available in many industries. BPO jobs are the most lucrative, as India is a hub of talent. Many multinational companies are keen to recruit Indians. There are many international companies that offer opportunities to work in the logistics industry. Logistics companies offer numerous benefits, including competitive pay and flexible work schedules. It can be difficult, however, to identify the right company. It's a good idea for you to speak with multiple companies in order to find the right one.
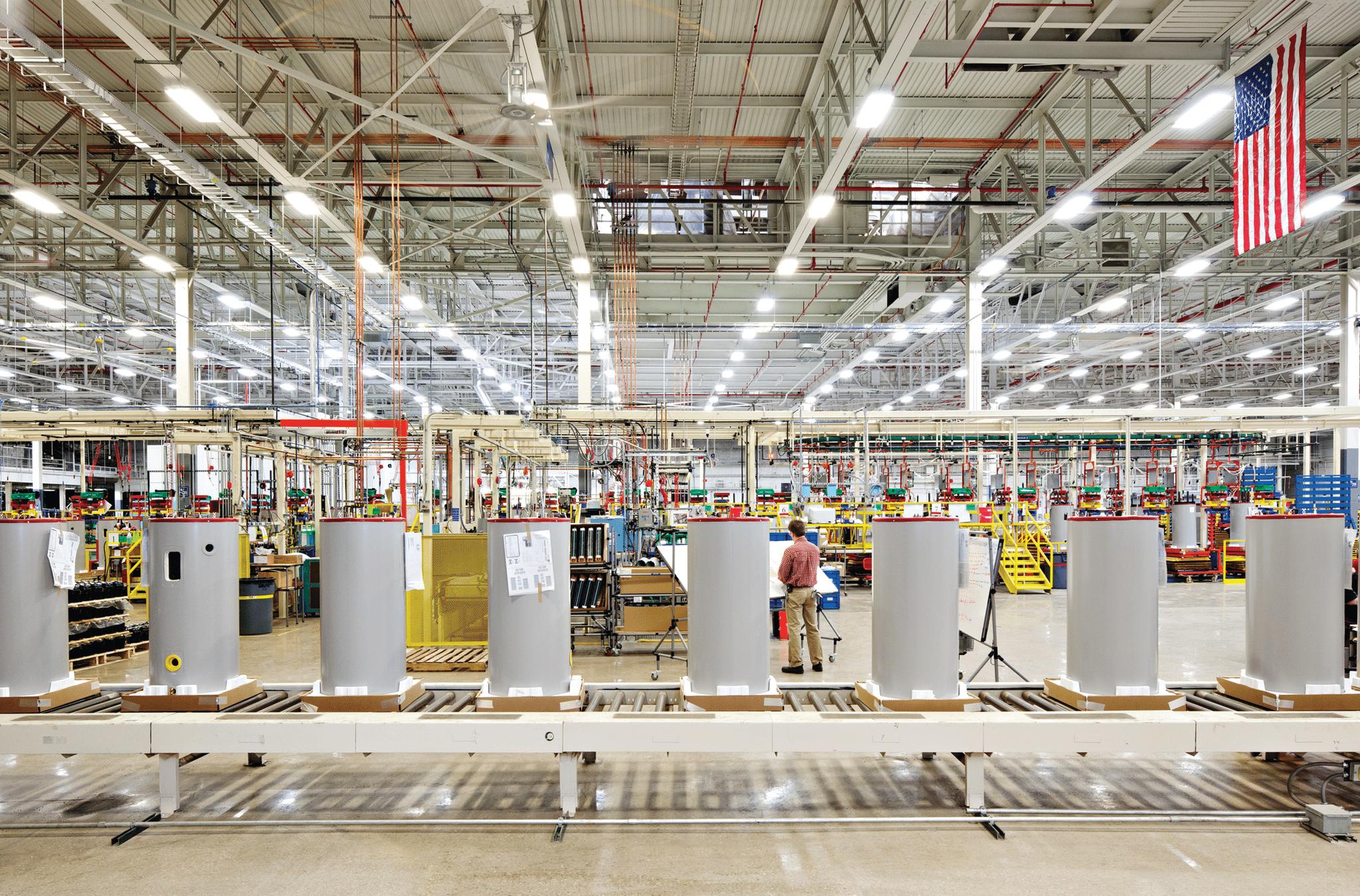
Technology is not a foreign concept in the logistics industry. The internet is a great place to begin if you are looking to join a modern, efficient logistics company. Some of the most popular examples are Uss-Express and others. They offer competitive salaries as well as many other perks like a flexible work schedule, and a fast on-boarding process. Learn the intricacies of ecommerce, from shipping to delivery. Logistics jobs are a highly-sought after profession.
Flexibility is one advantage of working in the logistics sector. For example, you can work remotely while still being paid regular raises. You don't need to travel to work and can still do other things while at it. The best part is that you have the freedom to choose your working hours. You can work remotely, but only at the hours you prefer. This is a boon to people with young children or aging parents.
The best part about work from home logistics jobs is the opportunity to earn good money while retaining your sanity. Great benefits and incentives make the best companies to work at. A company's reputation for fairness and transparency is also a hallmark of the best. If you're careful, you can make sure that you don’t get ripped off or manipulated by your employer. There are plenty of companies to choose from, but it's important to make sure that you are doing the right thing for you and your family.
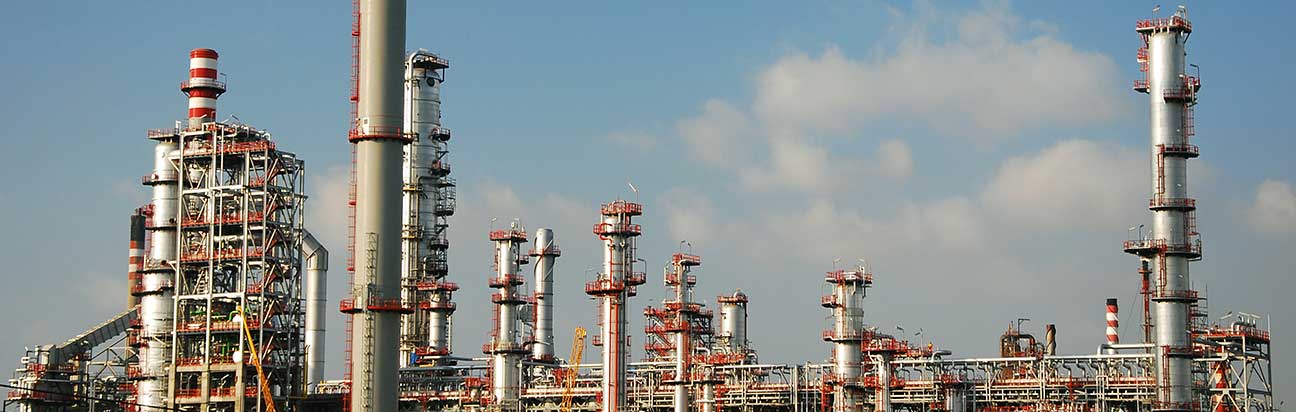
There are many other jobs available in logistics, including quality management. This role is responsible for inspecting the quality of packaging materials, and then delivering the goods. This is because they are the key to a product's success. There are many facets to the role of quality manager. Customers may have questions about the product's quality.
FAQ
What is production planning?
Production Planning includes planning for all aspects related to production. It is important to have everything ready and planned before you start shooting. This document should also include information on how to get the best result on set. It should include information about shooting locations, casting lists, crew details, equipment requirements, and shooting schedules.
The first step is to outline what you want to film. You may have already decided where you would like to shoot, or maybe there are specific locations or sets that you want to use. Once you have determined your scenes and locations, it is time to start figuring out the elements that you will need for each scene. For example, you might decide that you need a car but don't know exactly what model you want. This is where you can look up car models online and narrow down your options by choosing from different makes and models.
Once you have found the right vehicle, you can think about adding accessories. Are you looking for people to sit in the front seats? Perhaps you have someone who needs to be able to walk around the back of your car. Perhaps you would like to change the interior colour from black to white. These questions can help you decide the right look for your car. Another thing you can do is think about what type of shots are desired. Do you want to film close-ups, or wider angles? Maybe the engine or steering wheel is what you are looking to film. These things will help you to identify the car that you are looking for.
Once you've determined the above, it is time to start creating a calendar. You can create a schedule that will outline when you must start and finish your shoots. You will need to know when you have to be there, what time you have to leave and when your return home. Everyone will know what they need and when. Hire extra staff by booking them ahead of time. It is not worth hiring someone who won’t show up because you didn’t tell him.
Your schedule will also have to be adjusted to reflect the number of days required to film. Some projects only take one or two days, while others may last weeks. You should consider whether you will need more than one shot per week when creating your schedule. Shooting multiple takes over the same location will increase costs and take longer to complete. It's better to be safe than sorry and shoot less takes if you're not certain whether you need more takes.
Another important aspect of production planning is setting budgets. You will be able to manage your resources if you have a realistic budget. It is possible to reduce the budget at any time if you experience unexpected problems. It is important to not overestimate how much you will spend. You'll end up with less money after paying for other things if the cost is underestimated.
Production planning is a very detailed process, but once you understand how everything works together, it becomes easier to plan future projects.
What is the difference between manufacturing and logistics
Manufacturing is the production of goods using raw materials. Logistics encompasses the management of all aspects associated with supply chain activities such as procurement, production planning, distribution and inventory control. It also includes customer service. Manufacturing and logistics are often considered together as a broader term that encompasses both the process of creating products and delivering them to customers.
How can manufacturing efficiency be improved?
The first step is to identify the most important factors affecting production time. We must then find ways that we can improve these factors. If you don’t know how to start, look at which factors have the greatest impact upon production time. Once you have identified the factors, then try to find solutions.
What can I do to learn more about manufacturing?
Practical experience is the best way of learning about manufacturing. You can read books, or watch instructional videos if you don't have the opportunity to do so.
What is the responsibility of a logistics manager?
Logistics managers are responsible for ensuring that all goods arrive in perfect condition and on time. This is accomplished by using the experience and knowledge gained from working with company products. He/she should make sure that enough stock is on hand to meet the demands.
What are the goods of logistics?
Logistics refers to all activities that involve moving goods from A to B.
They include all aspects of transport, including packaging, loading, transporting, unloading, storing, warehousing, inventory management, customer service, distribution, returns, and recycling.
Logisticians ensure that the right product reaches the right place at the right time and under safe conditions. Logisticians assist companies in managing their supply chains by providing information such as demand forecasts, stock levels and production schedules.
They can also track shipments in transit and monitor quality standards.
What is meant by manufacturing industries?
Manufacturing Industries are companies that manufacture products. The people who buy these products are called consumers. These companies use a variety processes such as distribution, retailing and management to accomplish their purpose. They produce goods from raw materials by using machines and other machinery. This covers all types of manufactured goods including clothing, food, building supplies and furniture, as well as electronics, tools, machinery, vehicles and pharmaceuticals.
Statistics
- In 2021, an estimated 12.1 million Americans work in the manufacturing sector.6 (investopedia.com)
- (2:04) MTO is a production technique wherein products are customized according to customer specifications, and production only starts after an order is received. (oracle.com)
- According to a Statista study, U.S. businesses spent $1.63 trillion on logistics in 2019, moving goods from origin to end user through various supply chain network segments. (netsuite.com)
- You can multiply the result by 100 to get the total percent of monthly overhead. (investopedia.com)
- It's estimated that 10.8% of the U.S. GDP in 2020 was contributed to manufacturing. (investopedia.com)
External Links
How To
How to Use the Just In Time Method in Production
Just-in-time (JIT) is a method that is used to reduce costs and maximize efficiency in business processes. It's the process of obtaining the right amount and timing of resources when you need them. This means that your only pay for the resources you actually use. The term was first coined by Frederick Taylor, who developed his theory while working as a foreman in the early 1900s. After observing how workers were paid overtime for late work, he realized that overtime was a common practice. He decided that workers would be more productive if they had enough time to complete their work before they started to work.
JIT teaches you to plan ahead and prepare everything so you don’t waste time. Also, you should look at the whole project from start-to-finish and make sure you have the resources necessary to address any issues. You'll be prepared to handle any potential problems if you know in advance. This way, you won't end up paying extra money for things that weren't really necessary.
There are many JIT methods.
-
Demand-driven: This type of JIT allows you to order the parts/materials required for your project on a regular basis. This will allow you to track how much material you have left over after using it. You'll also be able to estimate how long it will take to produce more.
-
Inventory-based: This type allows you to stock the materials needed for your projects ahead of time. This allows you to predict how much you can expect to sell.
-
Project-driven: This method allows you to set aside enough funds for your project. You will be able to purchase the right amount of materials if you know what you need.
-
Resource-based JIT: This type of JIT is most commonly used. You allocate resources based on the demand. If you have many orders, you will assign more people to manage them. You'll have fewer orders if you have fewer.
-
Cost-based: This is a similar approach to resource-based but you are not only concerned with how many people you have, but also how much each one costs.
-
Price-based: This is very similar to cost-based, except that instead of looking at how much each individual worker costs, you look at the overall price of the company.
-
Material-based: This is quite similar to cost-based, but instead of looking at the total cost of the company, you're concerned with how much raw materials you spend on average.
-
Time-based: Another variation of resource-based JIT. Instead of focusing solely on the amount each employee costs, focus on how long it takes for the project to be completed.
-
Quality-based JIT: Another variation on resource-based JIT. Instead of worrying about the costs of each employee or how long it takes for something to be made, you should think about how quality your product is.
-
Value-based: This is one of the newest forms of JIT. In this scenario, you're not concerned about how products perform or whether customers expect them to meet their expectations. Instead, your focus is on the value you bring to the market.
-
Stock-based: This is an inventory-based method that focuses on the actual number of items being produced at any given time. It is used when production goals are met while inventory is kept to a minimum.
-
Just-intime (JIT), planning is a combination JIT management and supply chain management. It is the process of scheduling components' delivery as soon as they have been ordered. It's important as it reduces leadtimes and increases throughput.