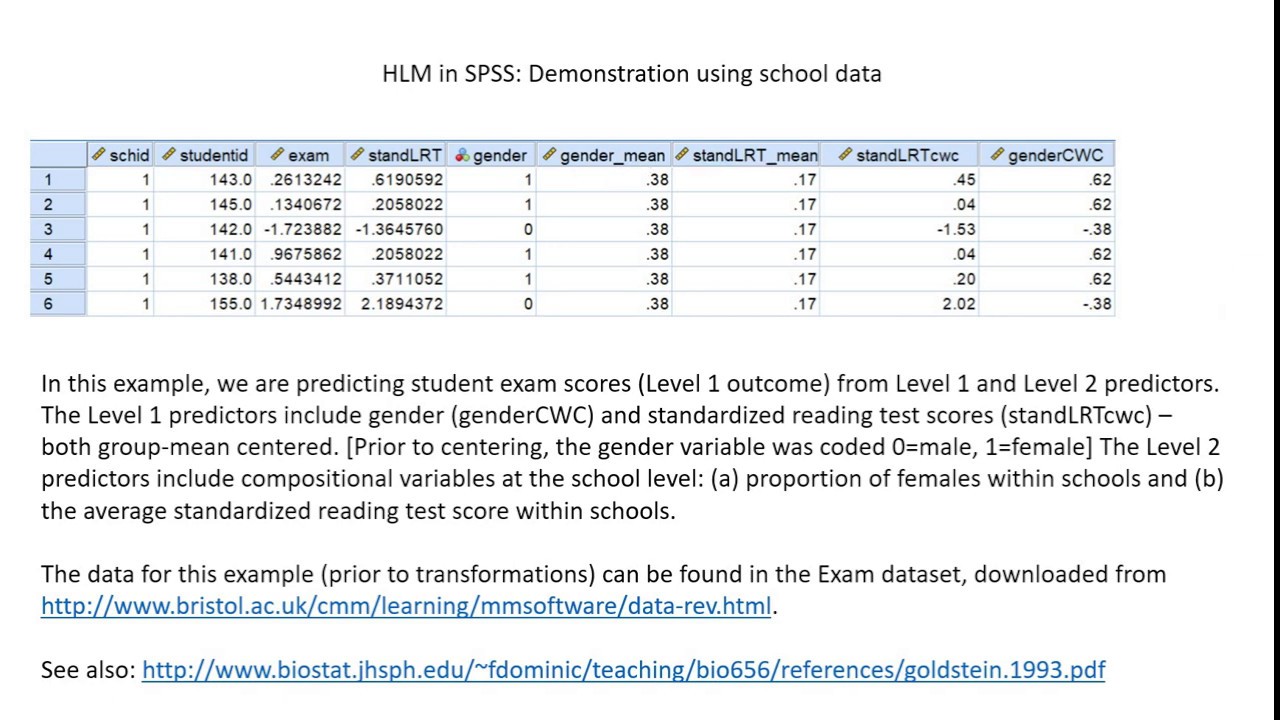
Demand management is a method that ensures that customers are satisfied. In essence, it involves bridging the gap between marketing and supply, by enabling organizations to predict demand. The process can help companies improve the speed and quality of delivery, reduce the amount of invoice disputes, and lower the cost of running the business.
Companies with a well-developed demand management system tend to be more responsive when the market changes occur. This is due to the fact that they have a system in which to identify the ideal buyer, which can be used to make marketing more effective.
Business can use demand management to help plan for the future and increase customer satisfaction. It can also help reduce the number invoice disputes and improve asset usage if done right. An effective demand management strategy can improve operational flexibility as well as operational resilience.
Project management software can be used to improve demand management. This software helps teams coordinate their work and prevents silos. A change management plan is a tool that can be used to help companies quickly fix supply chain problems.
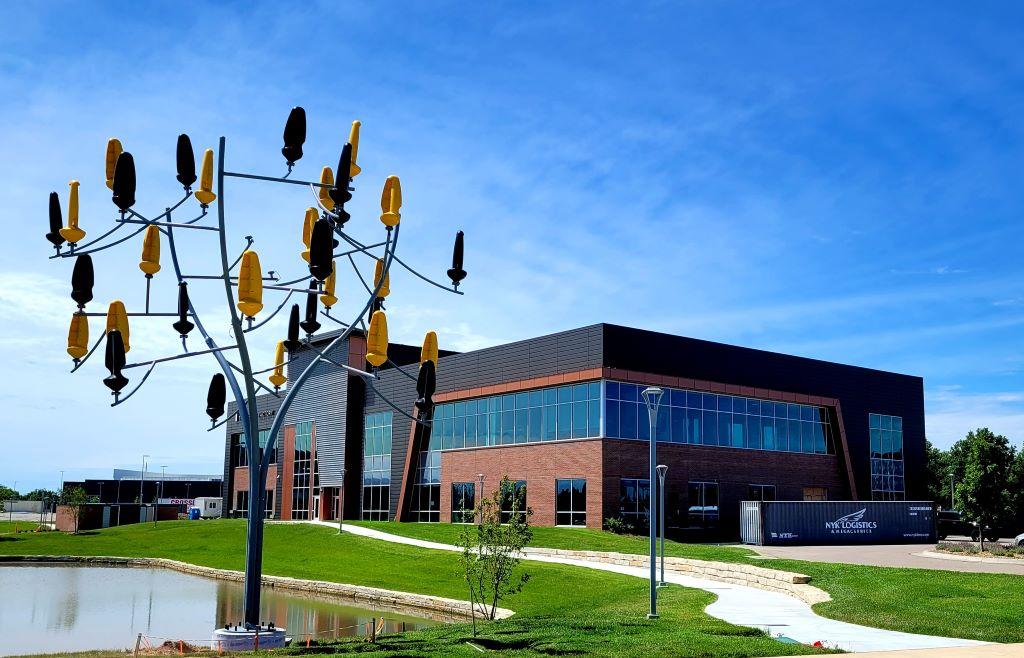
ILOG's PowerOps Suite combines manufacturing scheduling functions. Dynasys and QAD offer similar applications that enable organizations to create a supply and demand plan. These applications are useful for helping organizations see the effect of changes on their supply chains. Optiant provides ERP solutions that allow organizations to establish efficient, consistent, and effective order- and supply management processes.
Real-Time Inventory and Terra Technology offer real-time supply chain forecasting solutions. Finally, the collaborative management strategy helps companies share information and resources. It also includes performance indicators, knowledge sharing and joint planning.
However, before implementing a demand management strategy, it is important to consider a few factors. These factors can help professionals better understand the process and focus on the most important aspects.
Leadership buy in is an essential part of a demand management process. This is because demand management is a highly collaborative process that involves various levels of management. Managers and top executives are the most important players at the highest levels. They are responsible for ensuring all members are on the exact same page. The success of the initiative is also dependent on the participation of those at lower levels.
There are many applications available that can assist organizations in implementing a demand/supply planning. However, these key points should be kept in mind.
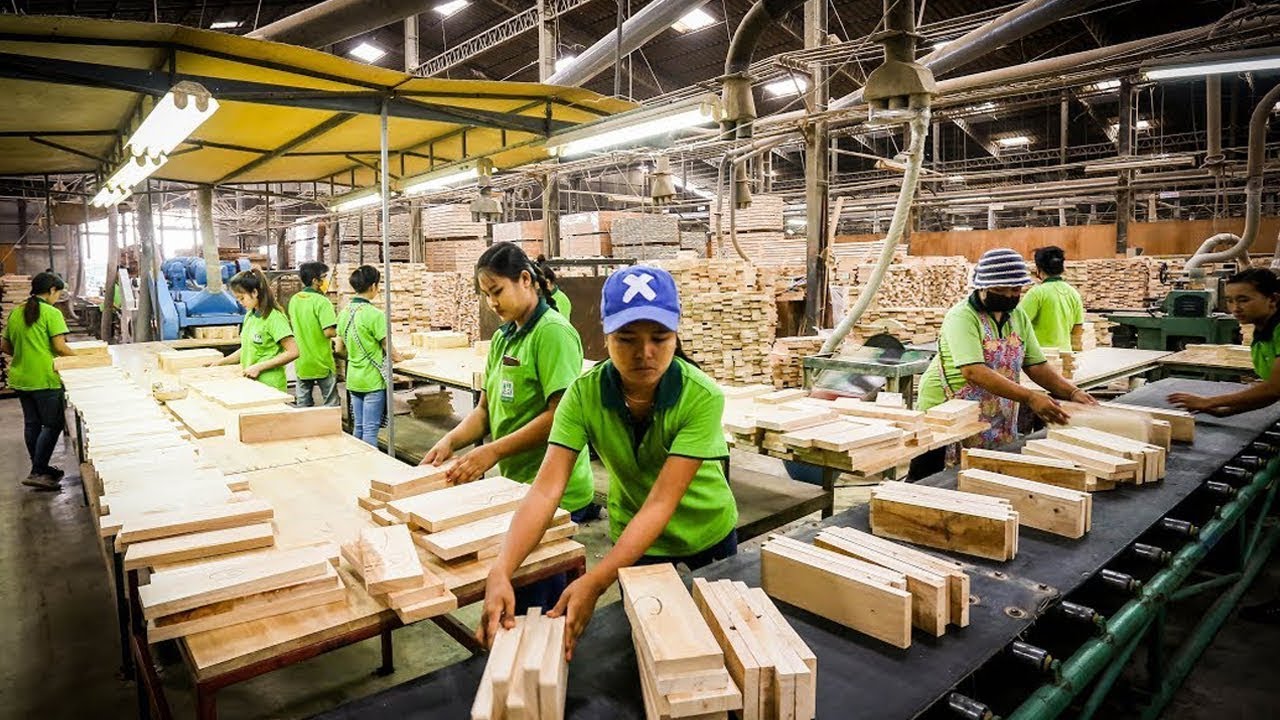
It is crucial to understand the market and identify the ideal customer. In addition to knowing who to target, the organization should be able to effectively measure and analyze the results of its efforts.
As businesses look to become more nimble, they must develop a demand management strategy that can be easily altered to accommodate change. An effective plan can decrease supply chain disruptions, tactical forecast error, and supply chain disruptions. Lastly, demand management is a valuable tool to help develop and implement portfolio and strategic plans.
FAQ
What is the difference between a production planner and a project manager?
A production planner is more involved in the planning phase of the project than a project manger.
How can excess manufacturing production be reduced?
In order to reduce excess production, you need to develop better inventory management methods. This would reduce the time needed to manage inventory. This could help us free up our time for other productive tasks.
A Kanban system is one way to achieve this. A Kanban board is a visual display used to track work in progress. Kanban systems allow work items to move through different states until they reach their final destination. Each state has a different priority level.
To illustrate, work can move from one stage or another when it is complete enough for it to be moved to a new stage. If a task is still in its beginning stages, it will continue to be so until it reaches the end.
This allows for work to continue moving forward, while also ensuring that there is no work left behind. Managers can monitor the work being done by Kanban boards to see what is happening at any given time. This allows them to adjust their workflows based on real-time information.
Lean manufacturing can also be used to reduce inventory levels. Lean manufacturing seeks to eliminate waste from every step of the production cycle. Any product that isn't adding value can be considered waste. Here are some examples of common types.
-
Overproduction
-
Inventory
-
Packaging not required
-
Exceed materials
By implementing these ideas, manufacturers can improve efficiency and cut costs.
How important is automation in manufacturing?
Automating is not just important for manufacturers, but also for service providers. Automation allows them to deliver services quicker and more efficiently. In addition, it helps them reduce costs by reducing human errors and improving productivity.
What are the responsibilities of a manufacturing manager
A manufacturing manager has to ensure that all manufacturing processes work efficiently and effectively. They should be aware of any issues within the company and respond accordingly.
They should also know how to communicate with other departments such as sales and marketing.
They should also be aware of the latest trends in their industry and be able to use this information to help improve productivity and efficiency.
Statistics
- In 2021, an estimated 12.1 million Americans work in the manufacturing sector.6 (investopedia.com)
- You can multiply the result by 100 to get the total percent of monthly overhead. (investopedia.com)
- In the United States, for example, manufacturing makes up 15% of the economic output. (twi-global.com)
- [54][55] These are the top 50 countries by the total value of manufacturing output in US dollars for its noted year according to World Bank.[56] (en.wikipedia.org)
- (2:04) MTO is a production technique wherein products are customized according to customer specifications, and production only starts after an order is received. (oracle.com)
External Links
How To
How to Use the 5S to Increase Productivity In Manufacturing
5S stands for "Sort", 'Set In Order", 'Standardize', & Separate>. The 5S methodology was developed at Toyota Motor Corporation in 1954. This methodology helps companies improve their work environment to increase efficiency.
The basic idea behind this method is to standardize production processes, so they become repeatable, measurable, and predictable. This means that daily tasks such as cleaning and sorting, storage, packing, labeling, and packaging are possible. Through these actions, workers can perform their jobs more efficiently because they know what to expect from them.
Five steps are required to implement 5S: Sort, Set In Order, Standardize. Separate. Each step is a different action that leads to greater efficiency. If you sort items, it makes them easier to find later. When you set items in an order, you put items together. Then, after you separate your inventory into groups, you store those groups in containers that are easy to access. You can also label your containers to ensure everything is properly labeled.
Employees must be able to critically examine their work practices. Employees need to be able understand their motivations and discover alternative ways to do them. To implement the 5S system, employees must acquire new skills and techniques.
In addition to increasing efficiency, the 5S method also improves morale and teamwork among employees. They are more motivated to achieve higher efficiency levels as they start to see improvement.