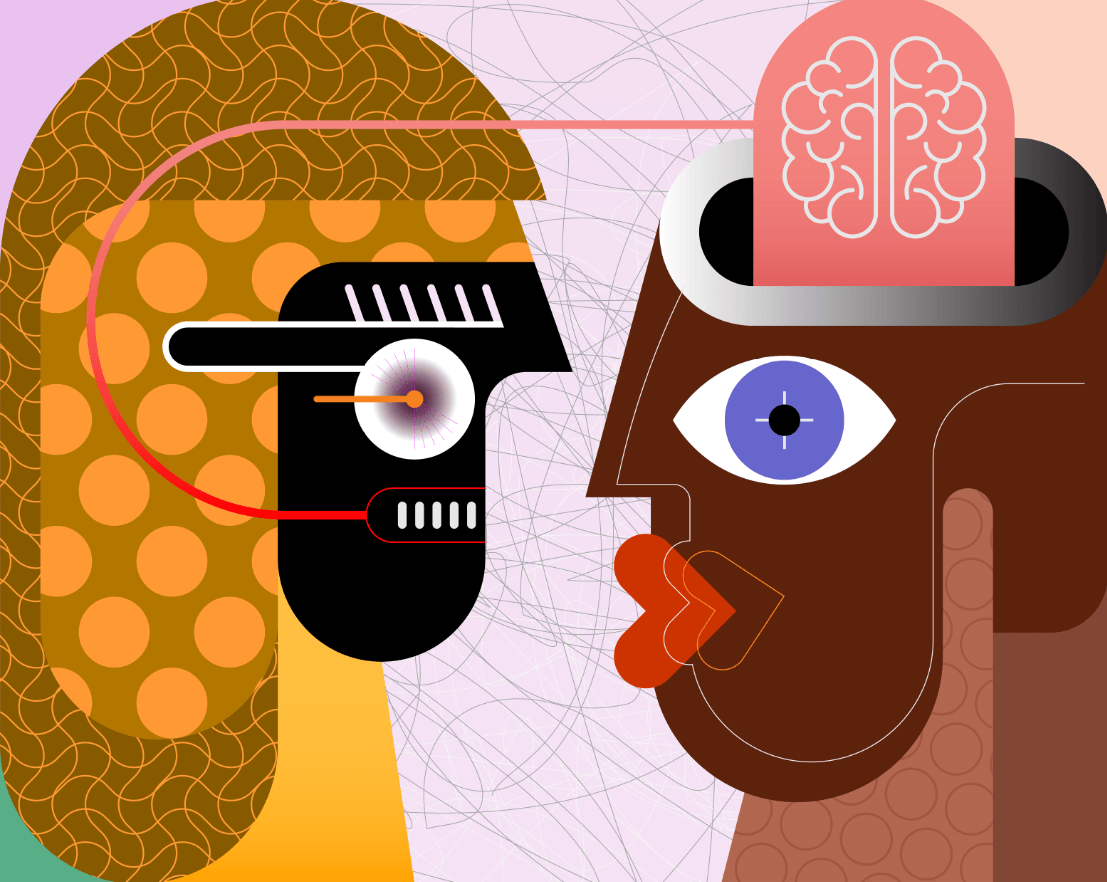
Classic economics has three basic sectors. These three basic sectors can be divided into manufacturing, financial activities, and services. The classification of businesses is based on characteristics and risks. You will find out more about each sector below. Below is a summary of the businesses that each sector has. This information can be further explored if you are curious. These categories do not have to be mutually exclusive.
Economic activity
Factors such as production, inputs, outputs are key to determining the economic activity of any nation or country. The demand for a certain good or service often determines a region's economy. There are two types, primary and secondary, of economic activity. Primary economic activities offer goods and services that meet human needs. Secondary economic activities add value to raw materials to create a more valuable product. Manufacturing and processing industries are examples of secondary economic activity.
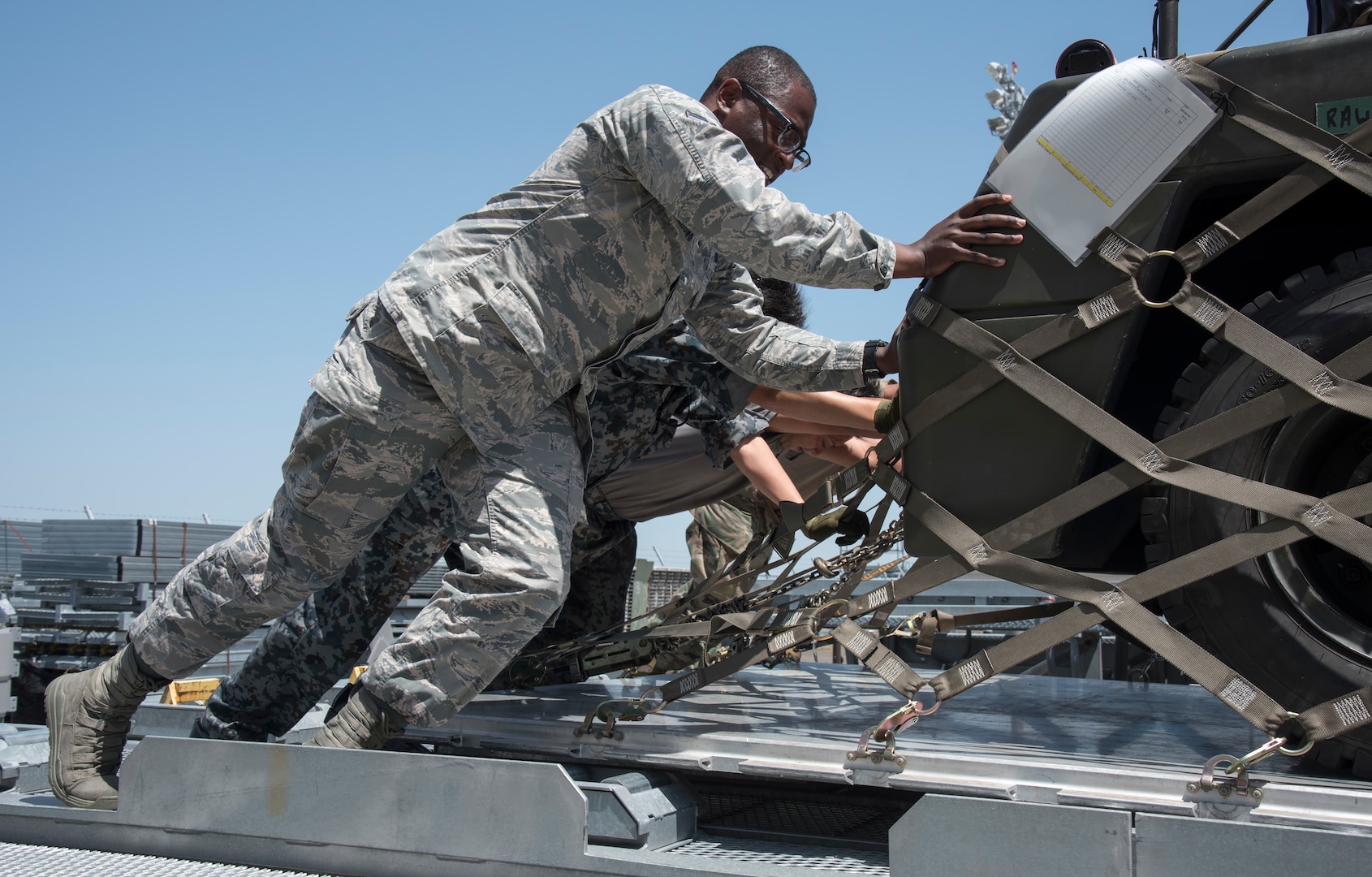
Classification of businesses
Business classification is the process by which businesses are divided into groups based upon the activities they engage in. There are two main categories: primary and secondary. Primary businesses are those which extract or exchange natural resources. The second type of business processes and transforms raw materials into products that are ready for consumption. There are many differences between the two types. These are just a few of the differences between the two types. This article can help you choose the right type of business for your company.
Characteristics
The following discussion discusses the differences between the primary and secondary sectors. It also focuses on the impact each sector has on the economy. First, let's define sectors. Sectors are distinct economic entities that react differently to different factors. These conditions may occur repeatedly, like business cycles. Or they could be unique events, like technological advancements. These characteristics can be useful for identifying the most promising sectors and determining their relative importance in an economic economy.
There are risks
Industry risk is the variation in performance across industries and their companies. It can be measured using the variance in ROE and profitability. This may be influenced by the performance of stock market stocks, depending on the industry. A company that makes steel is high-risk because of the possibility for major earthquakes in the area. An analysis of these risks can help investors identify volatile sectors.

Investments
While some investors may invest in specific companies or sectors, others might choose to invest in broader areas. Sectors are more risk-free and can be found within mutual funds and exchange traded funds. In addition, sector investing is becoming a popular investment strategy today. This article will help you identify the best investments. For more information, please read on. And don't forget to check out our free resource section for more information.
FAQ
What are the requirements to start a logistics business?
You need to have a lot of knowledge and skills to manage a successful logistic business. Good communication skills are essential to effectively communicate with your suppliers and clients. You must be able analyze data and draw out conclusions. You must be able to work well under pressure and handle stressful situations. In order to innovate and create new ways to improve efficiency, creativity is essential. Strong leadership qualities are essential to motivate your team and help them achieve their organizational goals.
You must be organized to meet tight deadlines.
Why is logistics important for manufacturing?
Logistics are an essential part of any business. They are essential to any business's success.
Logistics are also important in reducing costs and improving efficiency.
What is the responsibility of a manufacturing manager?
A manufacturing manager must make sure that all manufacturing processes run smoothly and effectively. They should also be aware of any problems within the company and act accordingly.
They should also know how to communicate with other departments such as sales and marketing.
They should also be knowledgeable about the latest trends in the industry so they can use this information for productivity and efficiency improvements.
How is a production manager different from a producer planner?
The difference between a product planner and project manager is that a planer is typically the one who organizes and plans the entire project. A production planner, however, is mostly involved in the planning stages.
How can manufacturing reduce production bottlenecks?
Avoiding production bottlenecks is as simple as keeping all processes running smoothly, from the time an order is received until the product ships.
This includes planning for capacity requirements as well as quality control measures.
The best way to do this is to use continuous improvement techniques such as Six Sigma.
Six Sigma can be used to improve the quality and decrease waste in all areas of your company.
It is focused on creating consistency and eliminating variation in your work.
How can overproduction in manufacturing be reduced?
Better inventory management is key to reducing excess production. This would reduce the amount of time spent on unnecessary activities such as purchasing, storing, and maintaining excess stock. This will allow us to free up resources for more productive tasks.
One way to do this is to adopt a Kanban system. A Kanban board, a visual display to show the progress of work, is called a Kanban board. Kanban systems allow work items to move through different states until they reach their final destination. Each state has a different priority level.
To illustrate, work can move from one stage or another when it is complete enough for it to be moved to a new stage. It is possible to keep a task in the beginning stages until it gets to the end.
This keeps work moving and ensures no work is lost. With a Kanban board, managers can see exactly how much work is being done at any given moment. This data allows them adjust their workflow based upon real-time data.
Lean manufacturing can also be used to reduce inventory levels. Lean manufacturing focuses on eliminating waste throughout the entire production chain. Any product that isn't adding value can be considered waste. Some common types of waste include:
-
Overproduction
-
Inventory
-
Packaging not required
-
Materials in excess
These ideas will help manufacturers increase efficiency and lower costs.
Statistics
- In the United States, for example, manufacturing makes up 15% of the economic output. (twi-global.com)
- According to a Statista study, U.S. businesses spent $1.63 trillion on logistics in 2019, moving goods from origin to end user through various supply chain network segments. (netsuite.com)
- [54][55] These are the top 50 countries by the total value of manufacturing output in US dollars for its noted year according to World Bank.[56] (en.wikipedia.org)
- Job #1 is delivering the ordered product according to specifications: color, size, brand, and quantity. (netsuite.com)
- Many factories witnessed a 30% increase in output due to the shift to electric motors. (en.wikipedia.org)
External Links
How To
How to Use Just-In-Time Production
Just-intime (JIT), which is a method to minimize costs and maximize efficiency in business process, is one way. It's a way to ensure that you get the right resources at just the right time. This means that you only pay the amount you actually use. Frederick Taylor first coined this term while working in the early 1900s as a foreman. He saw how overtime was paid to workers for work that was delayed. He then concluded that if he could ensure that workers had enough time to do their job before starting to work, this would improve productivity.
JIT is about planning ahead. You should have all the necessary resources ready to go so that you don’t waste money. Also, you should look at the whole project from start-to-finish and make sure you have the resources necessary to address any issues. You'll be prepared to handle any potential problems if you know in advance. You won't have to pay more for unnecessary items.
There are different types of JIT methods:
-
Demand-driven: This type of JIT allows you to order the parts/materials required for your project on a regular basis. This will let you track the amount of material left over after you've used it. It will also allow you to predict how long it takes to produce more.
-
Inventory-based: You stock materials in advance to make your projects easier. This allows you to forecast how much you will sell.
-
Project-driven: This approach involves setting aside sufficient funds to cover your project's costs. You will be able to purchase the right amount of materials if you know what you need.
-
Resource-based JIT is the most widespread form. This is where you assign resources based upon demand. For instance, if you have a lot of orders coming in, you'll assign more people to handle them. If there aren't many orders, you will assign fewer people.
-
Cost-based : This is similar in concept to resource-based. But here, you aren't concerned about how many people your company has but how much each individual costs.
-
Price-based: This is a variant of cost-based. However, instead of focusing on the individual workers' costs, this looks at the total price of the company.
-
Material-based is an alternative to cost-based. Instead of looking at the total cost in the company, this method focuses on the average amount of raw materials that you consume.
-
Time-based JIT is another form of resource-based JIT. Instead of focusing on how much each employee costs, you focus on how long it takes to complete the project.
-
Quality-based JIT is another variant of resource-based JIT. Instead of looking at the labor costs and time it takes to make a product, think about its quality.
-
Value-based JIT is the newest form of JIT. In this scenario, you're not concerned about how products perform or whether customers expect them to meet their expectations. Instead, your goal is to add value to the market.
-
Stock-based: This is an inventory-based method that focuses on the actual number of items being produced at any given time. This is used to increase production and minimize inventory.
-
Just-in-time planning (JIT): This is a combination JIT and supply-chain management. It's the process of scheduling delivery of components immediately after they are ordered. It reduces lead times and improves throughput.