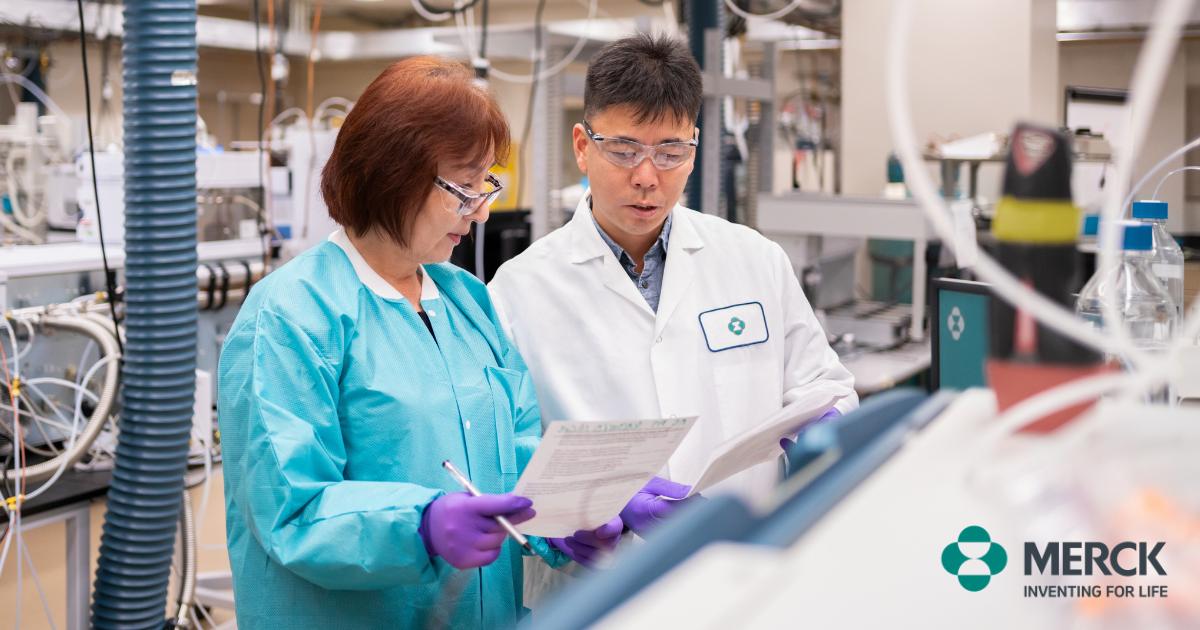
XPO logistics offers 145 jobs in Atlanta. Check out their site if you are interested in a new job. They are currently hiring. It is a great place to work, and you will be rewarded. They also have offices throughout the United States, including in Atlanta, San Antonio, Phoenix and Tucson, AZ. They offer the best benefits and bonuses in the business, and have the best culture and safety programs in the business. You can work when you want. You can even take advantage of our medical benefits program. XPO's health benefits program provides a variety plan options, discounts, as well as benefits that will assist you in your work life.
Georgia is a great location to do business if it's willing to work hard. Georgia is known for its high-quality workforce and business friendly policies. In fact, the state ranks fourth in the nation for jobs and training. The state also has one of the lowest tax rates in the country. XPO logistics has the perfect job for you, whether you are looking to get a new job or want to start a company. You can rest assured that you will have a fulfilling and rewarding experience if you are committed to your success.
FAQ
Do we need to know about Manufacturing Processes before learning about Logistics?
No. No. It is important to know about the manufacturing processes in order to understand how logistics works.
What is the distinction between Production Planning or Scheduling?
Production Planning (PP), or production planning, is the process by which you determine what products are needed at any given time. This can be done by forecasting demand and identifying production capabilities.
Scheduling refers to the process of allocating specific dates to tasks in order that they can be completed within a specified timeframe.
How important is automation in manufacturing?
Automation is important not only for manufacturers but also for service providers. Automation allows them to deliver services quicker and more efficiently. In addition, it helps them reduce costs by reducing human errors and improving productivity.
What are the 7 Rs of logistics.
The acronym 7R's of Logistic is an acronym that stands for seven fundamental principles of logistics management. It was published in 2004 by the International Association of Business Logisticians as part of their "Seven Principles of Logistics Management" series.
The following letters make up the acronym:
-
Responsible - ensure that actions are in compliance with legal requirements and do not cause harm to others.
-
Reliable - Have confidence in your ability to fulfill all of your commitments.
-
Reasonable - use resources efficiently and don't waste them.
-
Realistic – consider all aspects of operations, from cost-effectiveness to environmental impact.
-
Respectful - treat people fairly and equitably.
-
Be resourceful: Look for opportunities to save money or increase productivity.
-
Recognizable provides value-added products and services to customers
Statistics
- [54][55] These are the top 50 countries by the total value of manufacturing output in US dollars for its noted year according to World Bank.[56] (en.wikipedia.org)
- (2:04) MTO is a production technique wherein products are customized according to customer specifications, and production only starts after an order is received. (oracle.com)
- It's estimated that 10.8% of the U.S. GDP in 2020 was contributed to manufacturing. (investopedia.com)
- In the United States, for example, manufacturing makes up 15% of the economic output. (twi-global.com)
- According to the United Nations Industrial Development Organization (UNIDO), China is the top manufacturer worldwide by 2019 output, producing 28.7% of the total global manufacturing output, followed by the United States, Japan, Germany, and India.[52][53] (en.wikipedia.org)
External Links
How To
How to use Lean Manufacturing in the production of goods
Lean manufacturing is a management style that aims to increase efficiency and reduce waste through continuous improvement. It was developed in Japan between 1970 and 1980 by Taiichi Ohno. TPS founder Kanji Tyoda gave him the Toyota Production System, or TPS award. Michael L. Watkins published the "The Machine That Changed the World", the first book about lean manufacturing. It was published in 1990.
Lean manufacturing refers to a set of principles that improve the quality, speed and costs of products and services. It is about eliminating defects and waste from all stages of the value stream. Lean manufacturing is also known as just in time (JIT), zero defect total productive maintenance(TPM), and five-star (S). Lean manufacturing eliminates non-value-added tasks like inspection, rework, waiting.
Lean manufacturing can help companies improve their product quality and reduce costs. Additionally, it helps them achieve their goals more quickly and reduces employee turnover. Lean Manufacturing is one of the most efficient ways to manage the entire value chains, including suppliers and customers as well distributors and retailers. Lean manufacturing is widely used in many industries. Toyota's philosophy is the foundation of its success in automotives, electronics and appliances, healthcare, chemical engineers, aerospace, paper and food, among other industries.
Five basic principles of Lean Manufacturing are included in lean manufacturing
-
Define Value - Identify the value your business adds to society and what makes you different from competitors.
-
Reduce Waste - Eliminate any activity that doesn't add value along the supply chain.
-
Create Flow - Ensure work moves smoothly through the process without interruption.
-
Standardize and simplify - Make your processes as consistent as possible.
-
Develop Relationships: Establish personal relationships both with internal and external stakeholders.
Although lean manufacturing has always been around, it is gaining popularity in recent years because of a renewed interest for the economy after 2008's global financial crisis. Many companies have adopted lean manufacturing methods to increase their marketability. Economists think that lean manufacturing is a crucial factor in economic recovery.
Lean manufacturing is now becoming a common practice in the automotive industry, with many benefits. These benefits include increased customer satisfaction, reduced inventory levels and lower operating costs.
It can be applied to any aspect of an organisation. It is especially useful for the production aspect of an organization, as it ensures that every step in the value chain is efficient and effective.
There are three main types in lean manufacturing
-
Just-in Time Manufacturing: This lean manufacturing method is commonly called "pull systems." JIT stands for a system where components are assembled on the spot rather than being made in advance. This approach reduces lead time, increases availability and reduces inventory.
-
Zero Defects Manufacturing - ZDM: ZDM focuses its efforts on making sure that no defective units leave a manufacturing facility. It is better to repair a part than have it removed from the production line if it needs to be fixed. This also applies to finished products that need minor repairs before being shipped.
-
Continuous Improvement: Continuous Improvement aims to improve efficiency by continually identifying problems and making adjustments to eliminate or minimize waste. Continuous improvement refers to continuous improvement of processes as well people and tools.