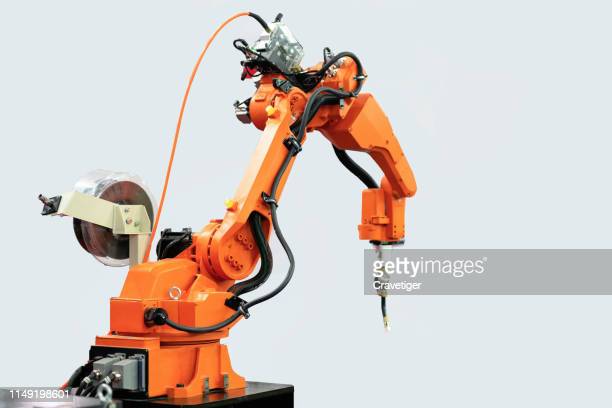
For industrial engineers, you will need strong math skills, knowledge of physical science and the ability to solve problems. These individuals may work in several sectors, including manufacturing and construction. They can be found working in offices, or on the factory floor.
Industrial engineers analyse production processes, design manufacturing techniques, improve efficiency, and make decisions about how to improve them. They may also create quality control procedures. They might also develop manufacturing standards and train employees. People who want to become industrial engineers need to be open-minded and willing work with others. They should be driven to improve efficiency and streamline their processes. They should have great communication and leadership skills.
Industrial engineers create cost analysis systems and systems that help robots perform more efficiently. They analyze data to determine if processes are efficient or not. They might also create manufacturing standards or design standards. Additionally, they are responsible for ensuring safety standards are met. They may also develop equipment control and inventory control procedures. Additionally, they will create documentation. They can also present their plans orally or in written reports.
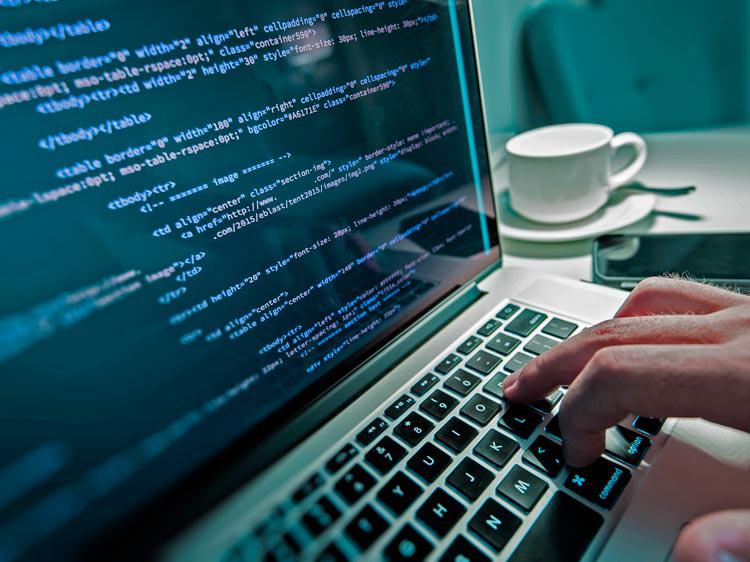
Industrial engineers may work in warehouses or manufacturing plants, but they can also travel to clients' locations. They may work in cramped or noisy environments. They may need to wear safety clothing. They might need to work extra hours in order to meet production deadlines.
The industrial engineer is responsible for the design and implementation process, assuring that it runs efficiently and producing high-quality products. They can also solve production problems. Many industrial engineers start their own manufacturing companies. They may have to train new workers and make sure that they know how to do their jobs properly. They might also need to ensure that raw materials meet high quality standards before being used in manufacturing.
Industrial engineers are part of other departments that create integrated systems to manage industrial production. They may also specialize in a particular engineering area. They may find themselves working in a noisy or cramped environment and may be required overtime to resolve unexpected manufacturing issues. They may need to travel to warehouses or construction sites to gather data, and they may have to work with other professionals to find solutions to manufacturing problems.
The education and experience of industrial engineers are a way to move up in the ranks. They could also set up their own consulting businesses or become specialists in a certain area. They may be specialists in quality control, facility planning, or other areas. They might also be responsible to design production layouts. They might also be responsible for creating wage and salary administration programs. They might also be responsible to schedule deliveries based upon production forecasts, storage and handling capabilities, and maintenance needs. They may also travel to perform administrative tasks. They can also supervise technicians.
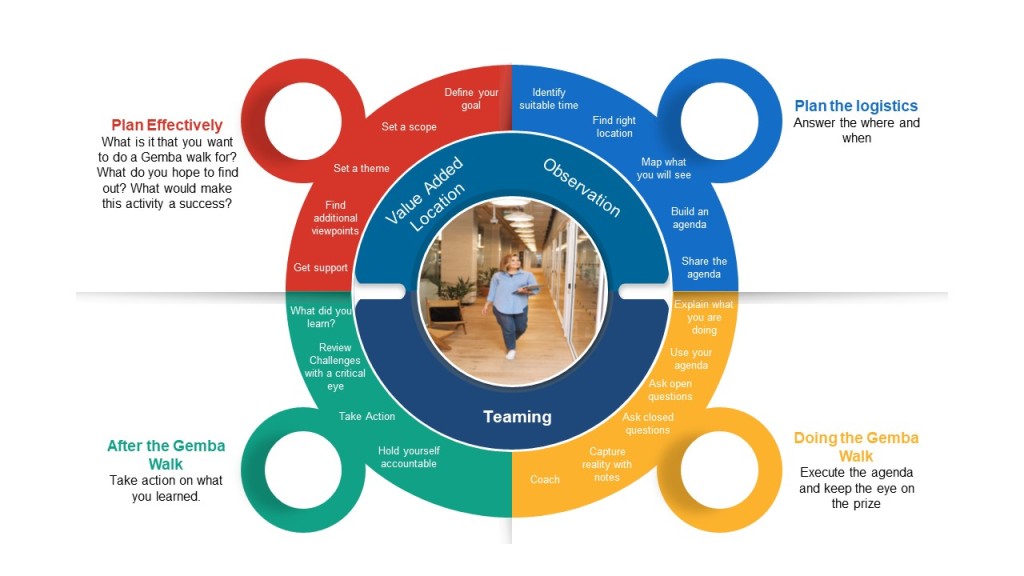
Industrial engineers can work for companies or as consultants. They can work for a company or for a consulting service, and may work up to 40 hours per week. They may also be required to work for more hours in a consultancy service, if they are providing technical assistance for a business.
FAQ
What do we need to know about Manufacturing Processes in order to learn more about Logistics?
No. No. Knowing about manufacturing processes will help you understand how logistics works.
What's the difference between Production Planning & Scheduling?
Production Planning (PP), is the process of deciding what production needs to take place at any given time. This is accomplished by forecasting the demand and identifying production resources.
Scheduling refers the process by which tasks are assigned dates so that they can all be completed within the given timeframe.
What are manufacturing & logistics?
Manufacturing is the process of creating goods from raw materials by using machines and processes. Logistics is the management of all aspects of supply chain activities, including procurement, production planning, distribution, warehousing, inventory control, transportation, and customer service. Sometimes manufacturing and logistics are combined to refer to a wider term that includes both the process of creating products as well as their delivery to customers.
How can we improve manufacturing efficiency?
First, determine which factors have the greatest impact on production time. The next step is to identify the most important factors that affect production time. You can start by identifying the most important factors that impact production time. Once you've identified them all, find solutions to each one.
What is the job of a production plan?
A production planner ensures all aspects of the project are delivered on time, within budget, and within scope. They ensure that the product or service is of high quality and meets client requirements.
What are the four types in manufacturing?
Manufacturing is the process of transforming raw materials into useful products using machines and processes. It involves many different activities such as designing, building, testing, packaging, shipping, selling, servicing, etc.
What are the main products of logistics?
Logistics is the process of moving goods from one point to another.
These include all aspects related to transport such as packaging, loading and transporting, storing, transporting, unloading and warehousing inventory management, customer service. Distribution, returns, recycling are some of the options.
Logisticians ensure that the product is delivered to the correct place, at the right time, and under safe conditions. Logisticians assist companies in managing their supply chains by providing information such as demand forecasts, stock levels and production schedules.
They coordinate with vendors and suppliers, keep track of shipments, monitor quality standards and perform inventory and order replenishment.
Statistics
- It's estimated that 10.8% of the U.S. GDP in 2020 was contributed to manufacturing. (investopedia.com)
- [54][55] These are the top 50 countries by the total value of manufacturing output in US dollars for its noted year according to World Bank.[56] (en.wikipedia.org)
- In the United States, for example, manufacturing makes up 15% of the economic output. (twi-global.com)
- In 2021, an estimated 12.1 million Americans work in the manufacturing sector.6 (investopedia.com)
- Job #1 is delivering the ordered product according to specifications: color, size, brand, and quantity. (netsuite.com)
External Links
How To
How to Use Just-In-Time Production
Just-intime (JIT), a method used to lower costs and improve efficiency in business processes, is called just-in-time. It's the process of obtaining the right amount and timing of resources when you need them. This means that only what you use is charged to your account. Frederick Taylor first coined this term while working in the early 1900s as a foreman. He saw how overtime was paid to workers for work that was delayed. He then concluded that if he could ensure that workers had enough time to do their job before starting to work, this would improve productivity.
JIT is an acronym that means you need to plan ahead so you don’t waste your money. Also, you should look at the whole project from start-to-finish and make sure you have the resources necessary to address any issues. If you expect problems to arise, you will be able to provide the necessary equipment and personnel to address them. This way, you won't end up paying extra money for things that weren't really necessary.
There are different types of JIT methods:
-
Demand-driven: This type of JIT allows you to order the parts/materials required for your project on a regular basis. This will let you track the amount of material left over after you've used it. This will allow you to calculate how long it will take to make more.
-
Inventory-based : You can stock the materials you need in advance. This allows you to forecast how much you will sell.
-
Project-driven : This is a method where you make sure that enough money is set aside to pay the project's cost. When you know how much you need, you'll purchase the appropriate amount of materials.
-
Resource-based JIT: This type of JIT is most commonly used. Here, you allocate certain resources based on demand. For example, if there is a lot of work coming in, you will have more people assigned to them. If there aren't many orders, you will assign fewer people.
-
Cost-based: This is similar to resource-based, except that here you're not just concerned about how many people you have but how much each person costs.
-
Price-based pricing: This is similar in concept to cost-based but instead you look at how much each worker costs, it looks at the overall company's price.
-
Material-based - This is a variant of cost-based. But instead of looking at the total company cost, you focus on how much raw material you spend per year.
-
Time-based: This is another variation of resource-based JIT. Instead of worrying about how much each worker costs, you can focus on how long the project takes.
-
Quality-based JIT is another variant of resource-based JIT. Instead of thinking about the cost of each employee or the time it takes to produce something, you focus on how good your product quality.
-
Value-based JIT: This is the latest form of JIT. In this case, you're not concerned with how well the products perform or whether they meet customer expectations. Instead, your focus is on the value you bring to the market.
-
Stock-based. This method is inventory-based and focuses only on the actual production at any given point. This method is useful when you want to increase production while decreasing inventory.
-
Just-in time (JIT), planning: This is a combination JIT/supply chain management. It refers to the process of scheduling the delivery of components as soon as they are ordered. It's important because it reduces lead times and increases throughput.