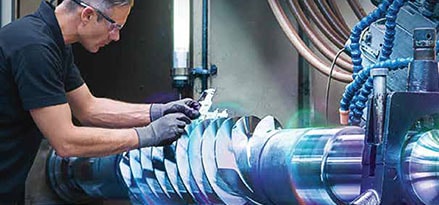
Introducing kaizen into manufacturing processes may not be as easy as some may imagine. It is slow and takes time to get inventory and make sure everyone is on the same page. This improvement process takes time depending on the company, problem area and level. Make sure you follow the proper implementation protocols and have the resources needed to make your manufacturing process improvement effort a success. In order to make this strategy successful, you need to set up a strong company culture that encourages continuous improvement.
Establishing a culture of improvement in your company
Gallup polls found that 32% of Americans are not engaged in their work. 17.2% were actively disengaged. Kaizen culture can be implemented to encourage employee engagement. This will lead to improved processes, lower turnover, and more innovation. Engaged workers are more likely to innovate and contribute ideas, which will lead to higher productivity, customer satisfaction, and better customer service. Kaizen culture is more than just reducing waste or increasing productivity.
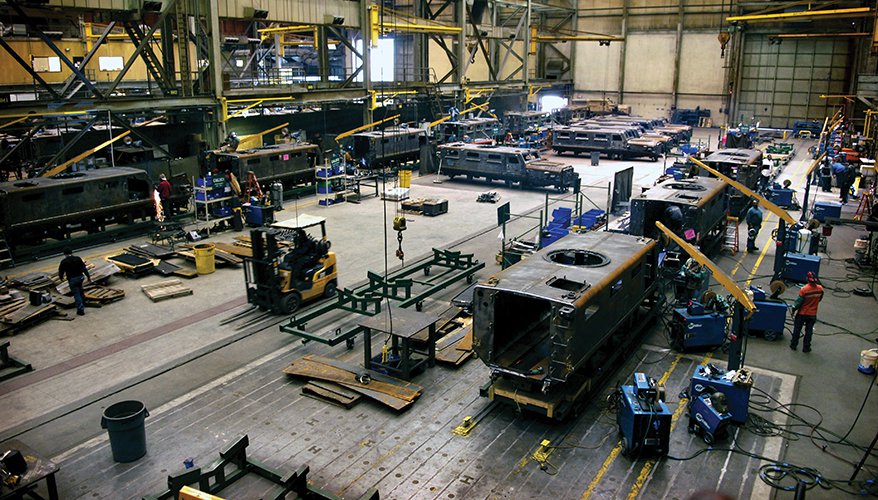
Kaizen refers to continuous improvement in all areas of a business. Kaizen, which is an incremental improvement method, is better than making major, drastic changes that provide little to no benefit. Kaizen can help reduce costs, increase productivity, improve quality, and improve customer satisfaction when implemented properly. The philosophy also helps to improve employee morale.
There are many obstacles to implementing Kaizen in manufacturing
Even though there are many benefits to kaizen, they have their drawbacks. First, implementing Kaizen in a business requires major changes to its management system. It may be difficult to reverse changes once they are made. Second, many businesses have difficulty changing their work habits, which can be a barrier in implementing kaizen.
Another common obstacle is that many manufacturers operate on a "feast or famine" cycle. Machine shops will have trouble if they are unable to find qualified workers and the demand for their product drops. They will have to fire employees and close the shop. Implementing kaizen, which is continuous improvement, can help these machine shops steer clear of the "feast/famine" cycle. Kaizen is a way to increase efficiency in a shop and produce more products.
High success rate in kaizen implementation during manufacturing
Statistics show that Kaizen implementation is not very successful in the manufacturing sector. Only 10% percent of manufacturing companies have reported positive Kaizen outcomes. This does not mean that Kaizen implementation is useless. Implementing kaizen in lean manufacturing is a crucial component. Here are some tips to increase your manufacturing business's success rate:
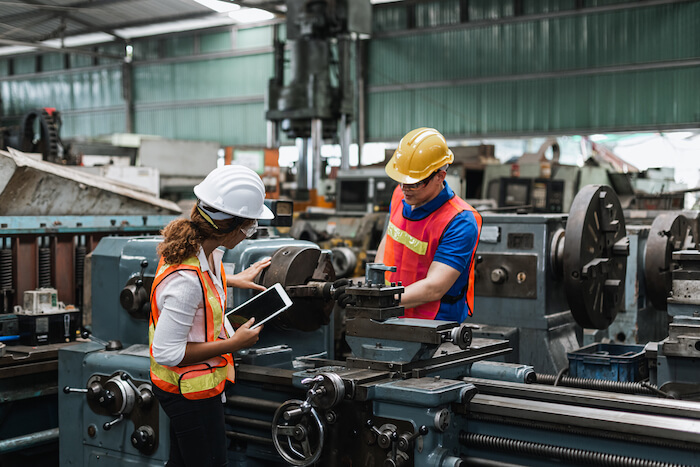
First, the process of kaizen must start with an understanding of current state processes. During the first step, data is collected and analyzed to identify the highest priorities. The next step is to test and verify improvements by performing a comparison of the before-and-after. A benefit-to-cost analysis is also a useful tool to determine the impact of specific improvements or the entire kaizen process. To assess the program's effectiveness, it is crucial to monitor the results for 60 to 90 days.
FAQ
What is the importance of logistics in manufacturing?
Logistics are essential to any business. Logistics can help you achieve amazing results by helping to manage product flow from raw materials to finished products.
Logistics are also important in reducing costs and improving efficiency.
What is the responsibility of a production planner?
Production planners make sure that every aspect of the project is delivered on-time, within budget, and within schedule. They also ensure the quality of the product and service meets the client's requirements.
What is the role of a logistics manager
Logistics managers make sure all goods are delivered on schedule and without damage. This is done using his/her knowledge of the company's products. He/she also needs to ensure adequate stock to meet demand.
Is automation important in manufacturing?
Automation is essential for both manufacturers and service providers. They can provide services more quickly and efficiently thanks to automation. It reduces human errors and improves productivity, which in turn helps them lower their costs.
What is the best way to learn about manufacturing?
Experience is the best way for you to learn about manufacturing. However, if that's not possible, you can always read books or watch educational videos.
Statistics
- In 2021, an estimated 12.1 million Americans work in the manufacturing sector.6 (investopedia.com)
- According to the United Nations Industrial Development Organization (UNIDO), China is the top manufacturer worldwide by 2019 output, producing 28.7% of the total global manufacturing output, followed by the United States, Japan, Germany, and India.[52][53] (en.wikipedia.org)
- [54][55] These are the top 50 countries by the total value of manufacturing output in US dollars for its noted year according to World Bank.[56] (en.wikipedia.org)
- Many factories witnessed a 30% increase in output due to the shift to electric motors. (en.wikipedia.org)
- It's estimated that 10.8% of the U.S. GDP in 2020 was contributed to manufacturing. (investopedia.com)
External Links
How To
How to use the Just-In Time Method in Production
Just-intime (JIT), a method used to lower costs and improve efficiency in business processes, is called just-in-time. It's the process of obtaining the right amount and timing of resources when you need them. This means that you only pay for what you actually use. Frederick Taylor, a 1900s foreman, first coined the term. He noticed that workers were often paid overtime when they had to work late. He then concluded that if he could ensure that workers had enough time to do their job before starting to work, this would improve productivity.
The idea behind JIT is that you should plan ahead and have everything ready so you don't waste money. Look at your entire project, from start to end. Make sure you have enough resources in place to deal with any unexpected problems. If you anticipate that there might be problems, you'll have enough people and equipment to fix them. This way, you won't end up paying extra money for things that weren't really necessary.
There are many JIT methods.
-
Demand-driven: This is a type of JIT where you order the parts/materials needed for your project regularly. This will allow for you to track the material that you have left after using it. This will allow to you estimate the time it will take for more to be produced.
-
Inventory-based: You stock materials in advance to make your projects easier. This allows one to predict how much they will sell.
-
Project-driven: This means that you have enough money to pay for your project. Knowing how much money you have available will help you purchase the correct amount of materials.
-
Resource-based JIT is the most widespread form. You allocate resources based on the demand. If you have many orders, you will assign more people to manage them. If there aren't many orders, you will assign fewer people.
-
Cost-based : This is similar in concept to resource-based. But here, you aren't concerned about how many people your company has but how much each individual costs.
-
Price-based: This is similar to cost-based but instead of looking at individual workers' salaries, you look at the total company price.
-
Material-based is an alternative to cost-based. Instead of looking at the total cost in the company, this method focuses on the average amount of raw materials that you consume.
-
Time-based: Another variation of resource-based JIT. Instead of focusing only on how much each employee is costing, you should focus on how long it takes to complete your project.
-
Quality-based JIT is another variant of resource-based JIT. Instead of worrying about the costs of each employee or how long it takes for something to be made, you should think about how quality your product is.
-
Value-based JIT is the newest form of JIT. You don't worry about whether the products work or if they meet customer expectations. Instead, your goal is to add value to the market.
-
Stock-based: This stock-based method focuses on the actual quantity of products being made at any given time. It is used when production goals are met while inventory is kept to a minimum.
-
Just-in time (JIT), planning: This is a combination JIT/supply chain management. It's the process of scheduling delivery of components immediately after they are ordered. This is important as it reduces lead time and increases throughput.