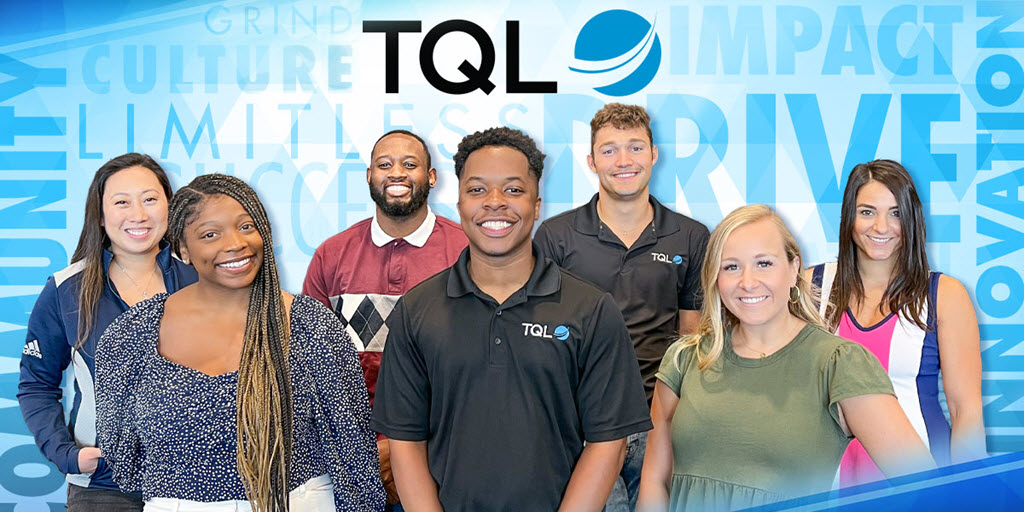
Flow is the state of being when all the steps in a production process follow each other smoothly without interruption. Every step adds value to the product, and goods meander through the production process without being impeded. In many companies, the production of a specific quantity of stock is planned out so that production orders can be fulfilled as efficiently as possible. In Lean Manufacturing, this is called "push production". Here are the key elements that make flow work:
Just-in-time manufacturing
When lean manufacturing was first introduced to the U.S. in the late 1970s, "just-in-time" manufacturing was the dominant paradigm. While the concept has its benefits, it is not the most practical way to run a company. You will need to have new mindsets and skills in order to reduce costs and increase efficiency. But it's worth trying if you want the best results.
Standardizing production processes and working in smaller batches are key aspects of just-in time manufacturing. In order to encourage a just in time mindset, it is important to plan your facility layout. Cellular manufacturing, for instance, can facilitate production flow. Workstations and parts bins can be organized in cells that ensure smoother flow of materials. Just-in-time producers should avoid lengthy changeovers.
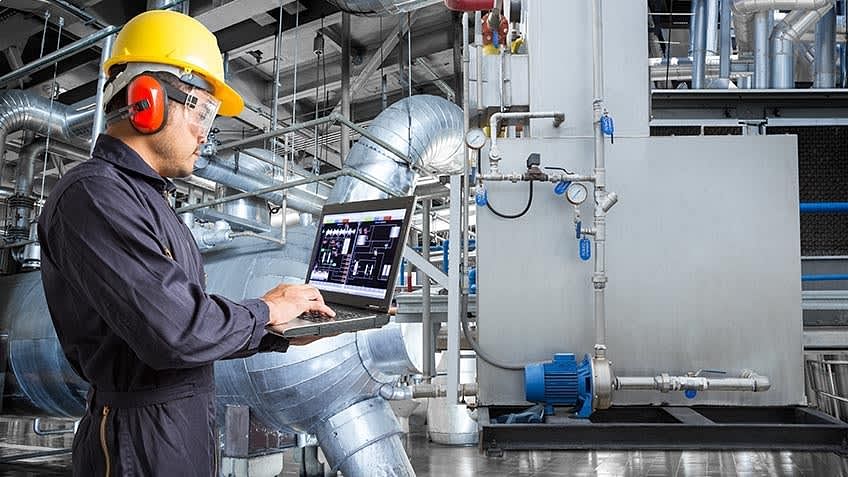
Standardized work
First, you have to create standardized work before applying lean manufacturing in manufacturing processes. This system of work places emphasis on the workers involved in the production process. It also refers to the process of continuously improving the system through kaizen. Standardized work documents are under the control of the cell leader. They are also updated whenever takt changes. Standardized documentation serves as a foundation for improvement activities.
Organizations can improve their productivity as well as service quality by having standard work processes. They can reduce the time it takes to develop products and help reduce human error. This helps organizations to resolve problems more quickly because people understand the process better. This allows organizations to make continuous improvements and improve customer satisfaction. These processes can then be implemented easily in companies once they are standardized. It is a good idea for a company to have a mission statement.
Continuous improvement
Lean principles encourage continuous improvement and provide a variety of benefits. These benefits are often additive but there is one thread that ties them all together: greater productivity, lower cost, and shorter lead time. Continuous improvement in lean is all about increasing value creation. But how does continuous improving work? This article will give you an overview of some common benefits of continuous improvement. It's simple: it helps companies save money.
Continuous improvement is a process that focuses on incremental rather than large-scale improvements. Although individual improvements are small and seem insignificant, the total improvement is substantial. It takes small, measured steps to improve. Continuous improvement, which focuses on alignment of objectives, is key to lean manufacturing environments. It allows businesses to maximize productivity, profitability, and efficiency. Continuous improvement methods allow for a simplified production process, so that all processes work together in order to achieve a common goal.
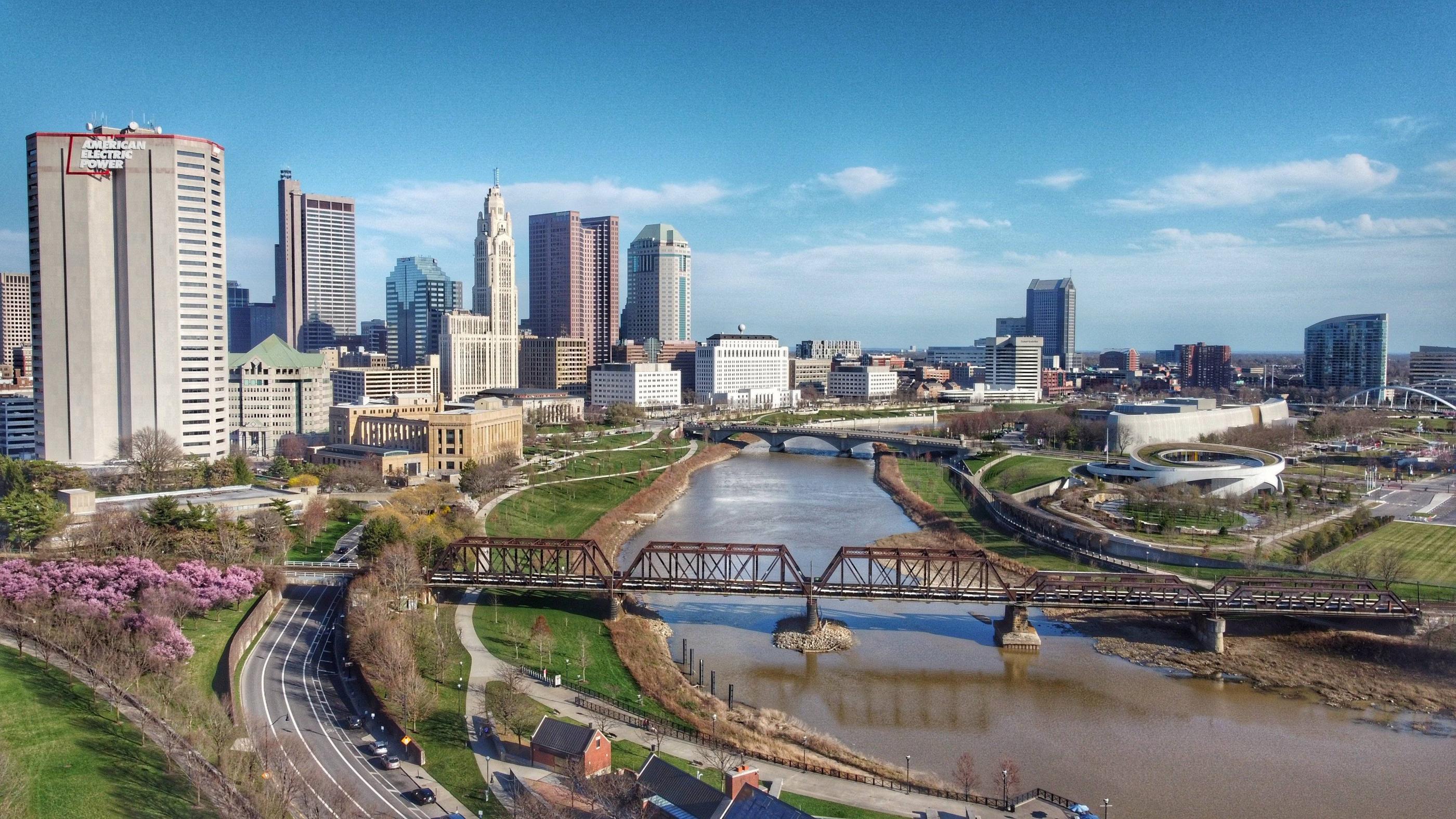
Kaizen
Kaizen is a lean manufacturing method that focuses on eliminating waste. It is sometimes used to improve production yield or reduce lead times. A team of employees is assigned a specific role to study the problem and propose solutions. The process of creating a value stream map for kaizen usually begins with the creation. Then, the team conducts time studies of relevant operations. This continues until each step can be improved and the overall process has become more efficient.
An example is a manufacturing plant that has identified inefficiencies and may buy a new lift truck. Its operator could move inventory around to make loading/unloading more efficient. Similar to the value stream, it is a map of all processes that produce products or services. Five S's are used in the mapping process to increase employee productivity, workplace practices, and workplace efficiency. There are seven types. Each type focuses on a different aspect or part of the manufacturing process.
FAQ
What are my options for learning more about manufacturing
You can learn the most about manufacturing by getting involved in it. You can read books, or watch instructional videos if you don't have the opportunity to do so.
What is the role of a production manager?
Production planners ensure that all project aspects are completed on time, within budget and within the scope. They ensure that the product or service is of high quality and meets client requirements.
What is the difference in Production Planning and Scheduling, you ask?
Production Planning (PP), is the process of deciding what production needs to take place at any given time. This can be done by forecasting demand and identifying production capabilities.
Scheduling is the process of assigning specific dates to tasks so they can be completed within the specified timeframe.
Is automation important in manufacturing?
Not only is automation important for manufacturers, but it's also vital for service providers. They can provide services more quickly and efficiently thanks to automation. In addition, it helps them reduce costs by reducing human errors and improving productivity.
What are the responsibilities for a manufacturing manager
The manufacturing manager should ensure that every manufacturing process is efficient and effective. They should be aware of any issues within the company and respond accordingly.
They should also know how to communicate with other departments such as sales and marketing.
They should also be knowledgeable about the latest trends in the industry so they can use this information for productivity and efficiency improvements.
Is there anything we should know about Manufacturing Processes prior to learning about Logistics.
No. No. Knowing about manufacturing processes will help you understand how logistics works.
Statistics
- It's estimated that 10.8% of the U.S. GDP in 2020 was contributed to manufacturing. (investopedia.com)
- Many factories witnessed a 30% increase in output due to the shift to electric motors. (en.wikipedia.org)
- Job #1 is delivering the ordered product according to specifications: color, size, brand, and quantity. (netsuite.com)
- [54][55] These are the top 50 countries by the total value of manufacturing output in US dollars for its noted year according to World Bank.[56] (en.wikipedia.org)
- In the United States, for example, manufacturing makes up 15% of the economic output. (twi-global.com)
External Links
How To
How to Use Just-In-Time Production
Just-intime (JIT), which is a method to minimize costs and maximize efficiency in business process, is one way. It's the process of obtaining the right amount and timing of resources when you need them. This means that your only pay for the resources you actually use. Frederick Taylor, a 1900s foreman, first coined the term. Taylor observed that overtime was paid to workers if they were late in working. He then concluded that if he could ensure that workers had enough time to do their job before starting to work, this would improve productivity.
JIT is a way to plan ahead and make sure you don't waste any money. It is important to look at your entire project from beginning to end and ensure that you have enough resources to handle any issues that may arise. If you anticipate that there might be problems, you'll have enough people and equipment to fix them. This way you won't be spending more on things that aren’t really needed.
There are different types of JIT methods:
-
Demand-driven: This type of JIT allows you to order the parts/materials required for your project on a regular basis. This will let you track the amount of material left over after you've used it. You'll also be able to estimate how long it will take to produce more.
-
Inventory-based: This type allows you to stock the materials needed for your projects ahead of time. This allows you predict the amount you can expect to sell.
-
Project-driven: This method allows you to set aside enough funds for your project. You will be able to purchase the right amount of materials if you know what you need.
-
Resource-based JIT : This is probably the most popular type of JIT. You allocate resources based on the demand. For example, if there is a lot of work coming in, you will have more people assigned to them. You'll have fewer orders if you have fewer.
-
Cost-based: This approach is very similar to resource-based. However, you don't just care about the number of people you have; you also need to consider how much each person will cost.
-
Price-based: This approach is very similar to the cost-based method except that you don't look at individual workers costs but the total cost of the company.
-
Material-based is an alternative to cost-based. Instead of looking at the total cost in the company, this method focuses on the average amount of raw materials that you consume.
-
Time-based JIT: This is another variant of resource-based JIT. Instead of focusing solely on the amount each employee costs, focus on how long it takes for the project to be completed.
-
Quality-based JIT is another variant of resource-based JIT. Instead of worrying about the costs of each employee or how long it takes for something to be made, you should think about how quality your product is.
-
Value-based: This is one of the newest forms of JIT. You don't worry about whether the products work or if they meet customer expectations. Instead, your focus is on the value you bring to the market.
-
Stock-based is an inventory-based system that measures the number of items produced at any given moment. This method is useful when you want to increase production while decreasing inventory.
-
Just-in time (JIT), planning: This is a combination JIT/supply chain management. It is the process of scheduling components' delivery as soon as they have been ordered. It reduces lead times and improves throughput.