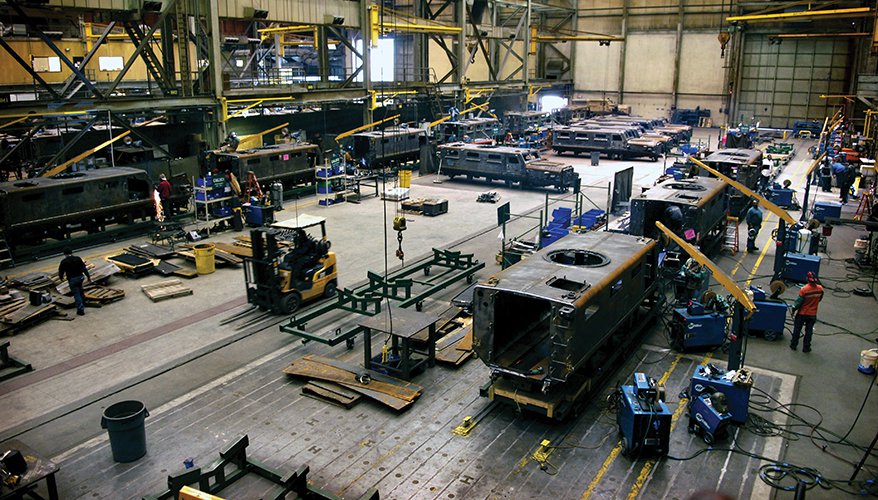
It may be more difficult than you think to introduce kaizen to manufacturing processes. The process can take time, and it takes inventory to ensure everyone is available. The amount of time needed to improve the manufacturing process depends on the level of participation, the problem area, and the firm. You must follow the right implementation procedures and acquire the required resources to ensure the success of your manufacturing process improvement program. To make this strategy work, create a culture within your company that promotes continuous improvement.
Create a company culture that is focused on improvement
Gallup polls reveal that only 32% are engaged in work in the United States. Of those, 17.2% were actively disengaged. Implementing a Kaizen culture will encourage employee engagement, which will ultimately improve processes, reduce turnover, and encourage innovation. Engagement will increase employee productivity and satisfaction. Kaizen culture offers more benefits than reducing waste, increasing productivity, and increasing customer satisfaction.
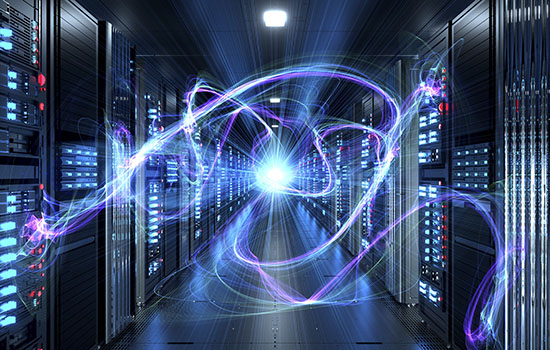
The philosophy behind Kaizen is continuous improvement in every aspect of a business. Kaizen, which is an incremental improvement method, is better than making major, drastic changes that provide little to no benefit. Kaizen processes, when done correctly, can result in lower costs, higher productivity, better quality, and increased customer satisfaction. It is also a great way to increase employee morale.
Obstacles to implementing kaizen in manufacturing
There are some downsides to kaizen implementation. First, implementing Kaizen in a business requires major changes to its management system. It can be difficult to reverse any changes made once the changes have been made. Second, many businesses find it difficult to change existing work practices, which may pose a barrier to the implementation of kaizen.
Another problem is that many manufacturers work on a "feast-or-famine" basis. When demand drops for their products and they don't have enough people to hire them, the machine shop will be in trouble. In such a scenario, they will have to layoff employees and close their doors. Implementing kaizen, which is continuous improvement, can help these machine shops steer clear of the "feast/famine" cycle. Kaizen can improve a shop's productivity and help it produce more products.
Kaizen implementation in manufacturing is a success rate
Statistics show that the success rate of Kaizen implementation in the manufacturing sector is relatively low. Only 10% percent of manufacturing companies have reported positive Kaizen outcomes. But this does not mean that the implementation process is worthless. Implementing Kaizen is an integral part of lean manufacturing. These are some ways to improve your manufacturing company's success rate.
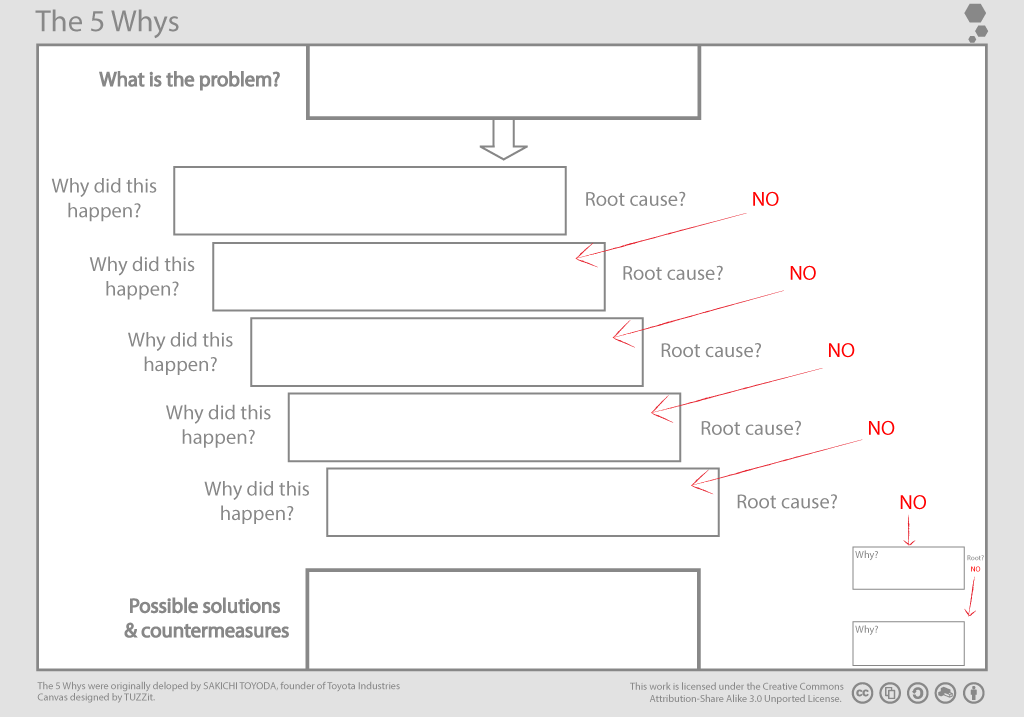
First, the process of kaizen must start with an understanding of current state processes. In the first step, data are collected and analyzed to identify high priority areas. The next step is to test and verify improvements by performing a comparison of the before-and-after. An analysis of the benefit-to-cost ratio can be used to analyze the overall impact of an improvement or the entire Kaizen process. It is vital to track the results from kaizen cycles over 60-90 days in order to assess its effectiveness.
FAQ
Why is logistics important in manufacturing
Logistics are an essential part of any business. They enable you to achieve outstanding results by helping manage product flow from raw materials through to finished goods.
Logistics play an important role in reducing costs as well as increasing efficiency.
What are my options for learning more about manufacturing
Hands-on experience is the best way to learn more about manufacturing. But if that is not possible you can always read books and watch educational videos.
What is production planning?
Production planning is the process of creating a plan that covers all aspects of production. This includes scheduling, budgeting and crew, location, equipment, props, and more. This document will ensure everything is in order and ready to go when you need it. It should also provide information about how best to produce the best results while on set. This information includes locations, crew details and equipment requirements.
First, you need to plan what you want to film. You might have an idea of where you want to film, or you may have specific locations or sets in mind. Once you have identified the scenes and locations, you can start to determine which elements are required for each scene. If you decide you need a car and don't know what model to choose, this could be an example. If this is the case, you might start searching online for car models and then narrow your options by selecting from different makes.
After you've found the perfect car, it's time to start thinking about adding extras. Do you need people sitting in the front seats? Or maybe you just need someone to push the car around. You may want to change the interior's color from black or white. These questions will help you determine the exact look and feel of your car. Also, think about what kind of shots you would like to capture. Will you be filming close-ups or wide angles? Maybe you want the engine or the steering wheels to be shown. All of these things will help you identify the exact style of car you want to film.
Once you have determined all of the above, you can move on to creating a schedule. You can use a schedule to determine when and where you need it to be shot. Each day will include the time when you need to arrive at the location, when you need to leave and when you need to return home. Everyone knows exactly what they should do and when. You can also make sure to book extra staff in advance if you have to hire them. It is not worth hiring someone who won’t show up because you didn’t tell him.
You will need to factor in the days that you have to film when creating your schedule. Some projects can be completed in a matter of days or weeks. Others may take several days. When you are creating your schedule, you should always keep in mind whether you need more than one shot per day or not. Multiplying takes in the same area will result both in increased costs and a longer time. If you are unsure if you need multiple takes, it is better to err on the side of caution and shoot fewer takes rather than risk wasting money.
Budget setting is an important part of production planning. As it will allow you and your team to work within your financial means, setting a realistic budget is crucial. You can always lower the budget if you encounter unexpected problems. However, it is important not to overestimate the amount that you will spend. Underestimating the cost will result in less money after you have paid for other items.
Production planning is a complicated process. But once you understand how everything works together, it becomes much easier to plan future project.
Statistics
- Job #1 is delivering the ordered product according to specifications: color, size, brand, and quantity. (netsuite.com)
- [54][55] These are the top 50 countries by the total value of manufacturing output in US dollars for its noted year according to World Bank.[56] (en.wikipedia.org)
- According to a Statista study, U.S. businesses spent $1.63 trillion on logistics in 2019, moving goods from origin to end user through various supply chain network segments. (netsuite.com)
- Many factories witnessed a 30% increase in output due to the shift to electric motors. (en.wikipedia.org)
- (2:04) MTO is a production technique wherein products are customized according to customer specifications, and production only starts after an order is received. (oracle.com)
External Links
How To
How to Use Six Sigma in Manufacturing
Six Sigma is defined by "the application SPC (statistical process control) techniques to achieve continuous improvements." Motorola's Quality Improvement Department created Six Sigma at their Tokyo plant, Japan in 1986. Six Sigma's core idea is to improve the quality of processes by standardizing and eliminating defects. In recent years, many companies have adopted this method because they believe there is no such thing as perfect products or services. The main goal of Six Sigma is to reduce variation from the mean value of production. It is possible to measure the performance of your product against an average and find the percentage of time that it differs from the norm. If you notice a large deviation, then it is time to fix it.
Understanding how your business' variability is a key step towards Six Sigma implementation is the first. Once you have this understanding, you will need to identify sources and causes of variation. Also, you will need to identify the sources of variation. Random variations happen when people make errors; systematic variations are caused externally. Random variations would include, for example, the failure of some widgets to fall from the assembly line. It would be considered a systematic problem if every widget that you build falls apart at the same location each time.
Once you identify the problem areas, it is time to create solutions. This could mean changing your approach or redesigning the entire process. Test them again once you've implemented the changes. If they don't work you need to rework them and come up a better plan.